Toyota has been shedding light on how its Prototype Division works in virtual reality to assess the user friendliness of vehicle designs far earlier than usual in the development process.
While it’s now common for automotive companies to harness real-time technology on the showroom floor for interactive configurators, Toyota has been leveraging Unreal Engine technology to identify areas for improvement.
In recent years, virtual ergonomics technology has transformed the traditional processes of physical models, with designers and engineers able to simulate human interaction with a vehicle far more realistically by testing the reactions of real people in VR.
The process starts with the import of a 3D mockup into a virtual environment built in Unreal Engine.
A person wearing a VR headset sits in a real car seat and experiences a series of simulated scenarios to test out the design and usability of the vehicle.
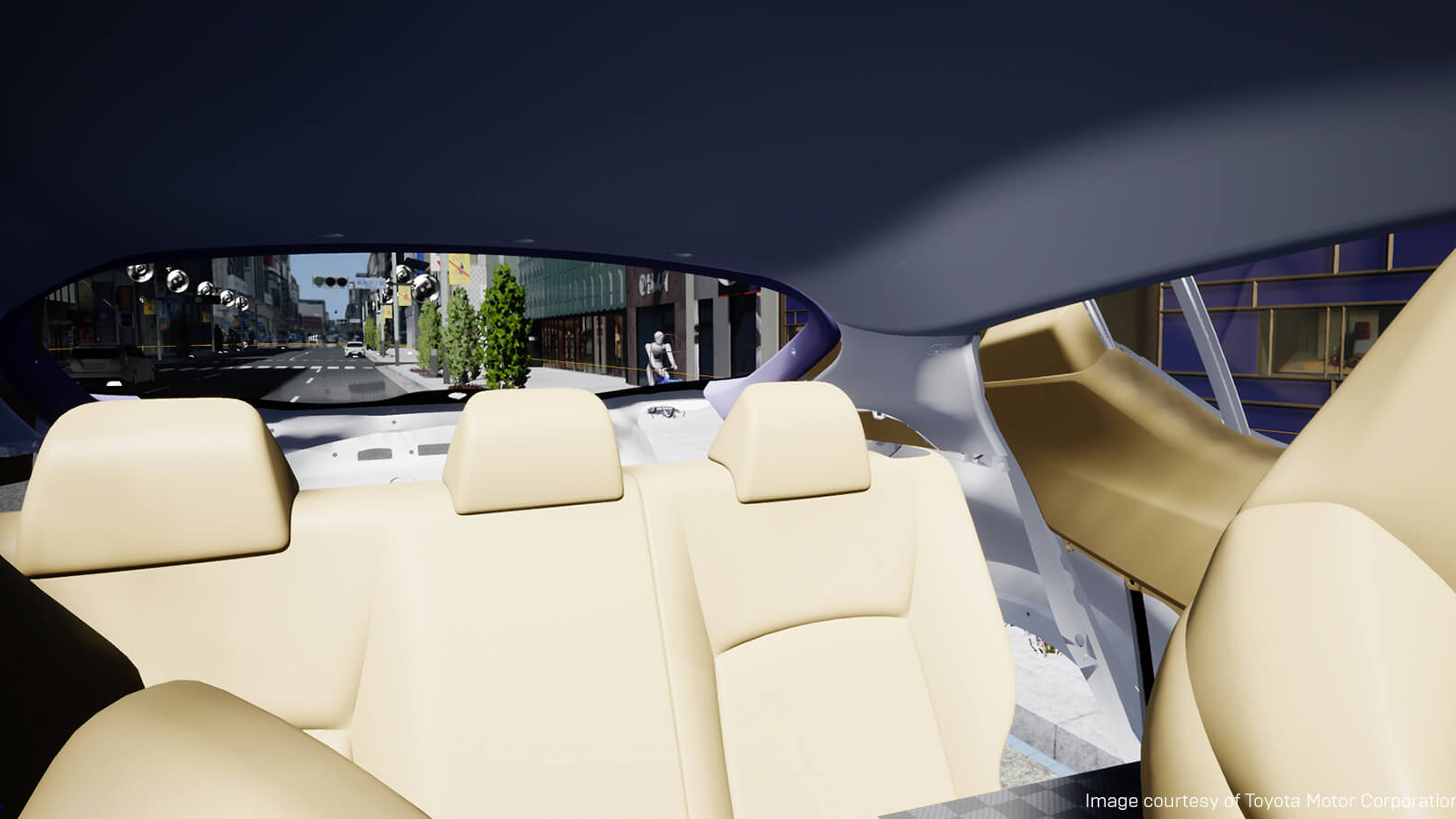
One such validation scenario developed by the Toyota team involves testing the visibility of other road users out of the rear quarter window of a new-generation car.
“We prepared several pedestrians and bikers in a virtual city environment,” says Mikiya Matsumoto, GM of the Prototype Division, digital engineering department at Toyota.
“The evaluator could see the simulated pedestrians and bikers passing near to the vehicle through the rear quarter window from the driver seat position via a VR headset.
“The test enabled us to improve visibility and we were able to complete it very quickly at a low cost compared to conventional methods.”
The team also leverages the setup to perform accessibility checks, using tracking gloves to evaluate how easy it is to reach various buttons and controls.
It uses a HTC Vive headset, CarSim for vehicle dynamics, Leap Motion controllers for hand tracking, and a combination of different physical prototype parts and VR simulation, depending on the evaluation performed.
Car model data is imported into Unreal Engine via Datasmith, a collection of tools and plugins for bringing CAD data into the VR engine.
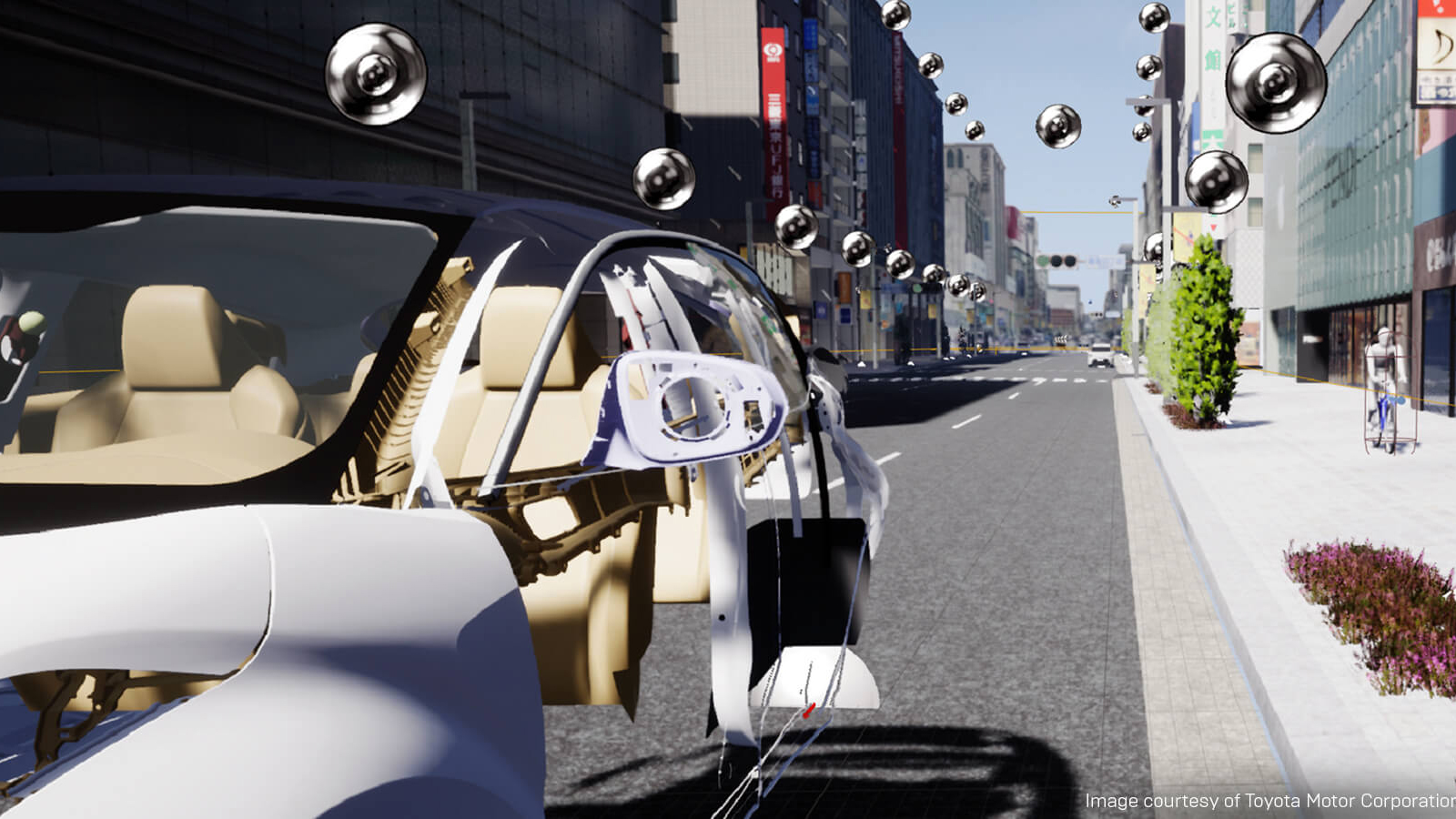
Datasmith enables the team at Toyota to go straight from CAD to Unreal Engine in a couple of clicks without using any third-party software in between.
With the ability to create complex scenarios that include virtual vehicles and human characters, game engine toolsets have some advantages for performing real-time ergonomics testing.
The Toyota team leverages Blueprint – a visual gameplay scripting system in Unreal Engine – to create custom virtual scenarios for each test and very specific requirements, without the need for masses of coding experience.
The workflow developed by Matsumoto’s team saves masses of time compared to traditional methods of having to build physical mock-ups, and also provides the team with a more flexible development path.
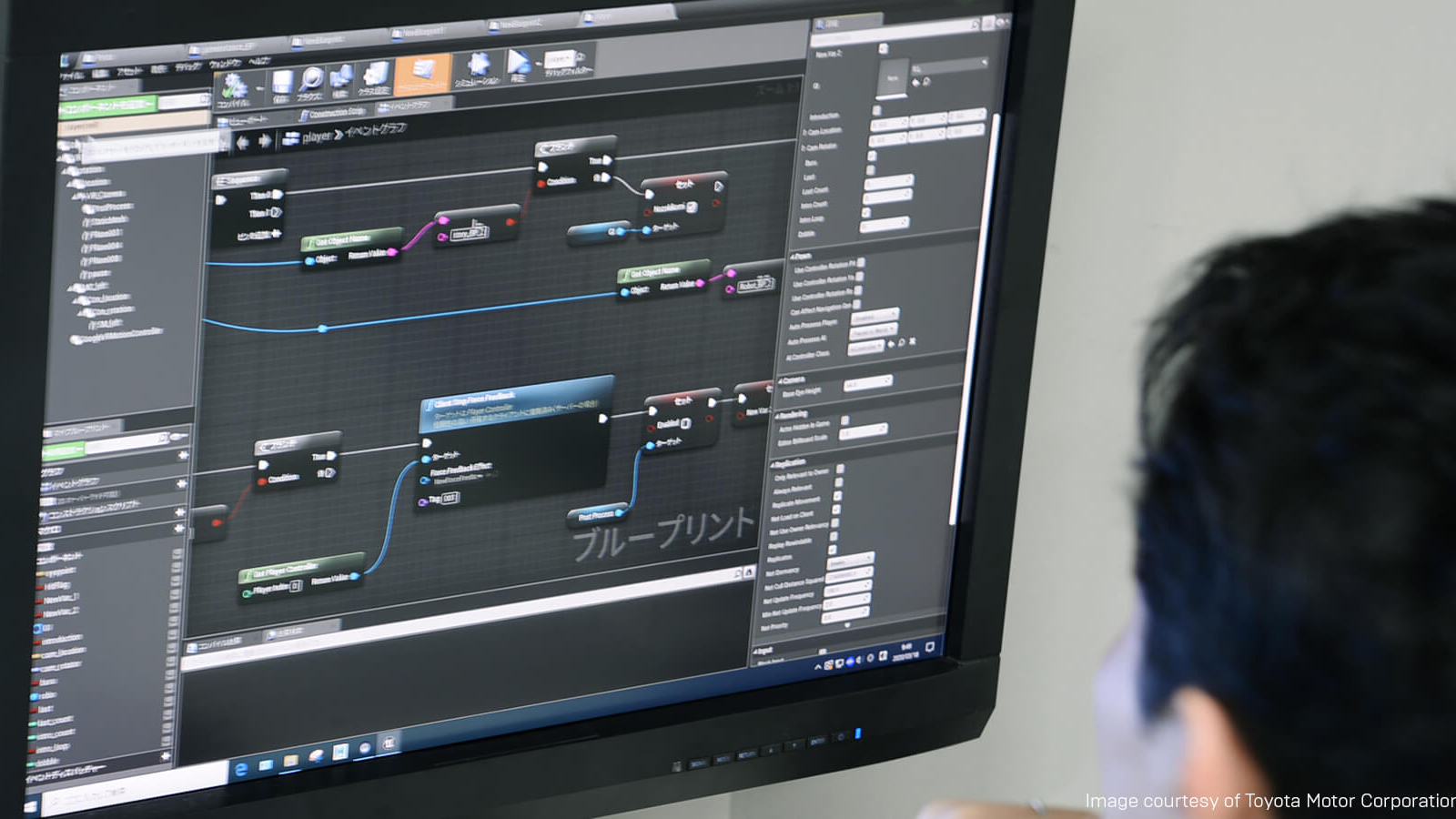
“Real-time technology allows us to perform virtual user experience testing,” explains Matsumoto. “This reduces the cost of and time taken for proof-of-concepting, leading to a more agile way of development.”
What’s more, Matsumoto believes real-time technology will be pivotal in proving the concepts of the vehicles of the future.
“Future vehicles might not have a traditional steering wheel—they might have something totally different to control the direction of movement.
“By using real-time technology and VR, we can evaluate any type of human-machine interface (HMI) and user experience.”
With a typical development process lasting just three years to get a car from concept design to showroom floor, the ability to test out more ergonomic concepts and ideas faster and early on makes for a more comfortable situation for all.