North Manchester General Hospital (NMGH) has been putting the iReal 2S entry-level 3D scanner through its paces for its maxilo-facial reconstruction devices and prostheses for trauma patients.
Traditionally this involves taking a physical impression of the patient’s face, a procedure which could take up to an hour while the patient has to remain very still until the impression sets. Once the mould has been created, it takes further time to pour gypsum stone solution into the mould, letting it set so that a facial prosthesis can be built around it.
The process of taking an impression is not always reliable and can be extremely uncomfortable for some patients, especially for burns and severe trauma patients.
“In the last few years we have tried to move from traditional methods of mould making to using 3D scanners, which has enabled this process to become quicker, cleaner and more convenient for the patient,” explained Oliver Burley, reconstructive scientist and lab manager at NMGH.
The team already had access to 3D scanning technology for some applications – such as burn splint manufacture – however the level of detail captured left a lot to be desired.
“[The] ability to capture the intricate detail of patient’s face was not as precise as we’d want it to be,” explained Burley. “A high level of accuracy is essential for creating maxillofacial devices and facial prostheses that are aesthetically pleasing, fit well, and blend seamlessly with the patient’s own features.”
New trials for entry-level 3D scanners, supplied by metrology experts The 3D Measurement Company, were recently introduced at NMGH, where the handheld iReal 2S 3D Scanner became a favourite of the prosthesis team.
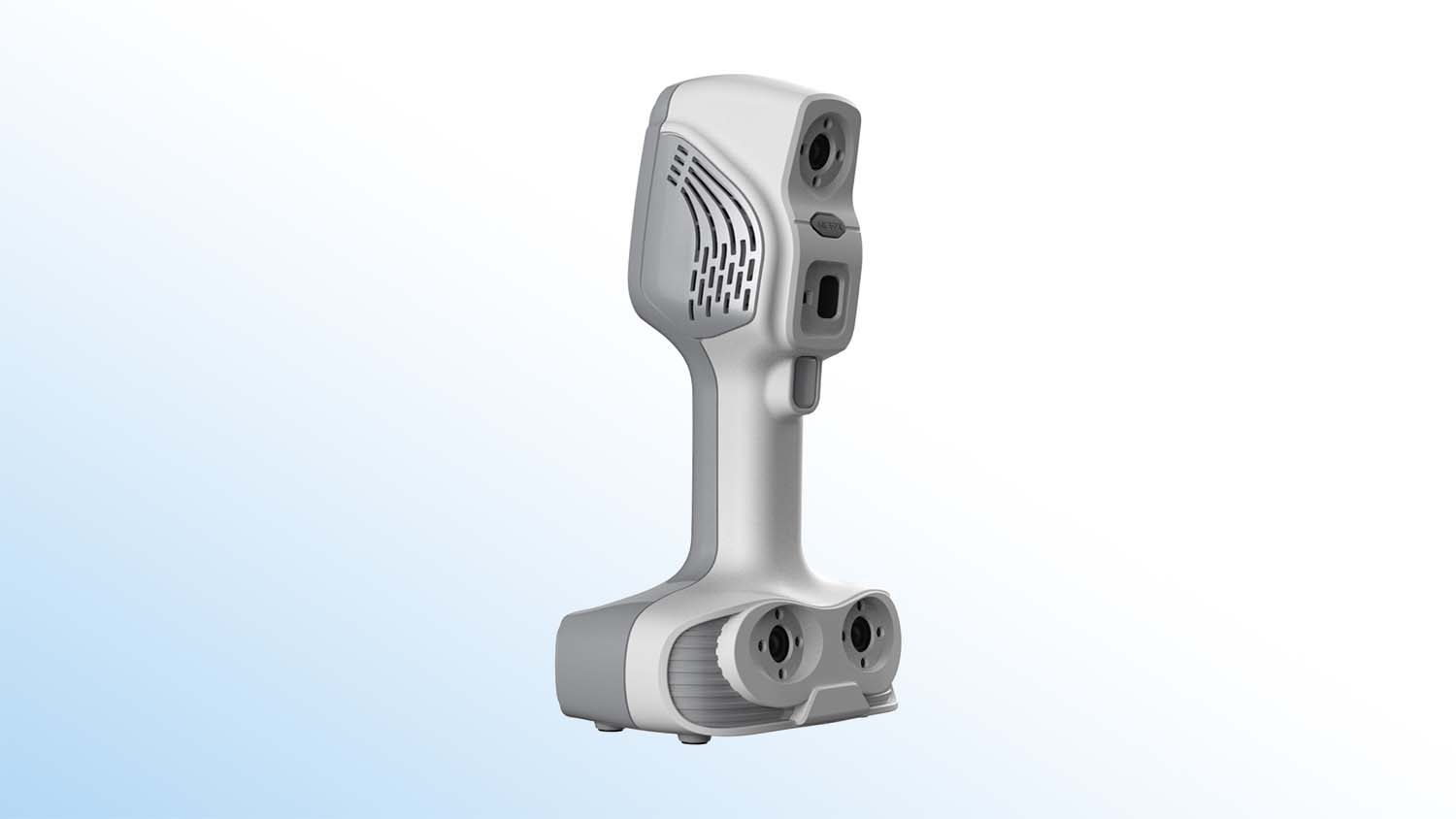
During the trial they found that the scanner was capturing detailed features such as eyebrows, skin folds, wrinkles and eye position, alongside the pigments and colours for each of them.
The blue and the infrared light settings of the iReal 2S, as well as the HD allow the user to produce high quality scan of a patient’s head in around thirty seconds, with minimal post processing required, resulting STL and OBJ files that can be used depending on the need, such as for printing the 3D models.
The portability of the 3D scanner is means it can be easily transported between different hospital sites, with its set-up taking only a few minutes.
“Compared to other systems we have tried, we found that the iReal met all requirements and applications within the hospital settings,” enthused Burley. “We are now looking at using it as a volume measurement tool for tissue reconstruction on other areas of the body.”