For many tech-literate designers and engineers, 3D scanning is a process they understand in theory, but may never experience first-hand.
Maybe it never came up in their own workflows, or maybe it’s subcontracted to other folk more knowledgeable and better equipped than themselves.
Either way, it’s always fun to get hands-on with a new device.
While core concepts remain much the same with each scanner, there are subtle differences in workflow from device to device.
Every time, you learn something new. For instance, the Peel 3D device that we’ve been working with this month is interesting on a number of accounts.
First, it comes from the Creaform family, so there’s a decent bit of prior knowledge behind it – and that shows both in how the device is built and how the accompanying software works.
It’s also obvious that the product represents Creaform trying to compete with newer, perhaps lower cost entrants in the scanning market and using what might be considered to be a lower end set of technologies to do that.
Structured white-light scanners may be an older technology, but these devices are still highly usable if the resolutions they offer meet your needs. And what might those needs be?
A more coarse scan would be useful for quick measurement, as long as you can pull the information you need from the results.
Or, you might just want a partial scan, in order to build mating components. Or, you might simply need to capture a rough design space.
The Peel 2 CAD scanner that we’ve tested this week encounters age-old issues when dealing with very dark, matt surfaces, as well as highly reflective ones.
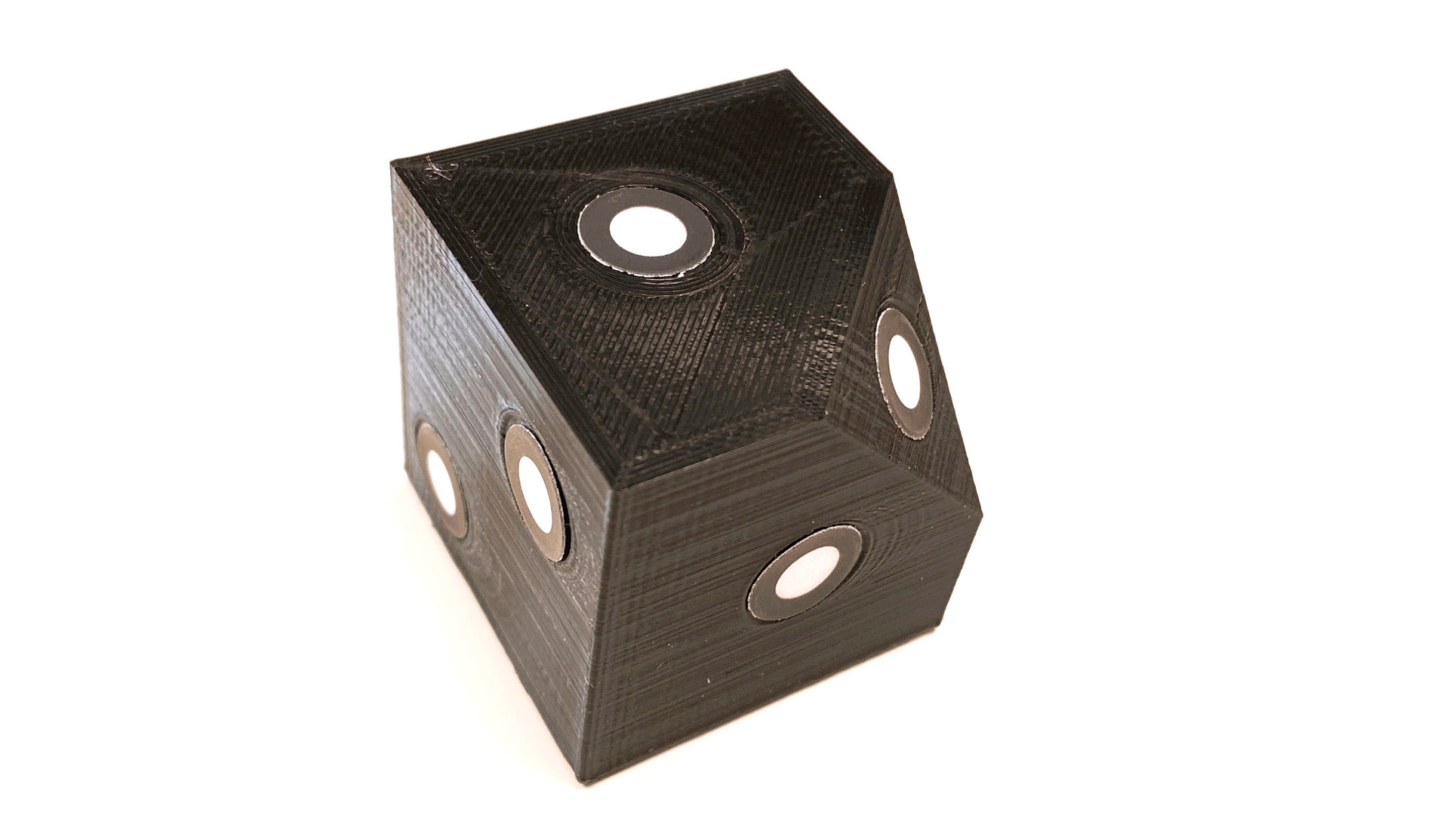
Both cause issues for white-light scanners, which is why blue-light systems have superceded them in many cases.
To get around these issues, it’s common to use registration targets (those small, reflective stickers) in combination with spraying or coating the surface of your part.
That led us to experiment with some new ideas we’ve come across.
Registration targets, after all, are useful for tracking handheld scanner movements, but you’re not always able to stick them to your object.
To get around this, I quickly modelled up a cube with a one-corner chamfer and a number of recesses on each face for a varying number of targets.
I then 3D printed them in black. This really helped with scanner tracking, particularly once I had two registration cubes in place.
Another thing I came across recently is mentioned in the review: AESUB spray.
There are all manner of methods of making reflective surface more matt in finish for scanning purposes – from foot powder and talc to fault-finding sprays and primers.
The issue is that these aren’t ideal and are often a pain the arse to clean off your product, prototype or competitor’s kit.
I was given a couple of cans of AESUB from the folks at The 3D Measurement Company who, as it turns out, have an office in Shropshire, just down the road from where I live.
This stuff is a revelation. It’s a spray with no nano particles, which gives you a very thin and consistent coating at a thickness that’ll have little effect on your scan accuracy.
Most impressively, it completely disappears after a couple of hours.
I conducted some experiments on our test parts, combining the registration cubes with the AESUB spray, and got dramatically improved results.
They say that every day is a school day – and it looks like we might have a little more time for learning in the coming months.