Tour-de-Force Power Engineering (TDF) is bringing the F1 experience to enthusiasts desperate to understand what a fast lap in a modern day racer is like.
Every car produced as part of the TDF-1 program is built at TDF by ex F1 engineers and mechanics who have previously worked for teams such as Williams, Mercedes, Marussia and Renault, but getting the data to build a car is hard to come by.
In many cases the original design documentation for these unique vehicles is simply not available.
For TDF, the first step was to generate accurate dimensional data for reverse engineering the vehicles and key components – creating a digital twin of the car that could be referred to throughout.
This was essential not only to facilitate the design and engineering work, to modify the cars to make them safer to drive by my more novice pilots on private circuits, but also for all on-going maintenance (should a bang with a barrier occur).
Design engineering company, ES Products and Design, was tasked with project managing the design work for virtual assembly of the vehicles and with the reverse engineering of key components.
To produce the dimensional data needed to underpin this work, the company chose 3D scanning experts T3DMC to perform precision 3D scans on the original ex-F1 cars ready for TDF cars to be built.
Data from these scans, augmented as necessary by manual measurements made on components, was transferred into Siemens NX to build and verify the full CAD model.
“We were asked to scan the Formula 1 cars for reverse-engineering purposes and also to create a digital twin of the vehicles,” explained T3DMC product sales manager Scott Robinson.
“The digital twin means that design engineers can ‘virtually assemble’ the modified vehicles so that they can easily see and correct problems before work starts on the real vehicles.”
“By using our handheld KSCAN 3D scanner we were able to make extremely accurate scans of the panels and of the ‘tub’ that houses the cockpit.
“We scanned the whole of the A surfaces of the vehicles, then took the panels off and repeated the process to provide a surface B scan.
“The whole job took just a few hours, compared with the days of tedious work it would have needed to make manual measurements.”
Portable and relatively simple to use, the KSCAN handheld scanner is ideal for use in speedy reverse engineering projects due to its blue laser technology, which captures details with 10 μm resolution, complemented by a red laser mode that provides a large 600 mm scanning window.
Thanks to its portable probe, with has a capability of 0.03 mm, it proved well suited to inspection applications such as determining the dimensional accuracy of drilled holes, trim, edges and cylindrical components.
With built-in photogrammetry features, this portable scanner boasts volumetric accuracy of up to 0.035 mm/m and according to T3DMC, makes easy work of scanning large objects such as car panels or dashboards.
“The CAD drawings we produce from the scan data will be used for manufacturing components and spares so even if a car is badly damaged on the track it can be rebuilt to exactly the same specification, which gives extra peace of mind to the owners of these spectacular vehicles,” concludes Edward Smith, director at ES Products and Designs.
Hopefully TDF won’t need to rebuild too many, as with millions of F1 fans around the world – many willing to give almost anything to step into the cockpit of the sport’s high-performance cars – this looks like a fast track adventure everyone will want to experience.
New to taking your 3D Scanning in house, or just taking your first steps with entry-level 3D Scanners? Then read our quick guide to upgrading your 3D scan results with a few secrets from the experts.
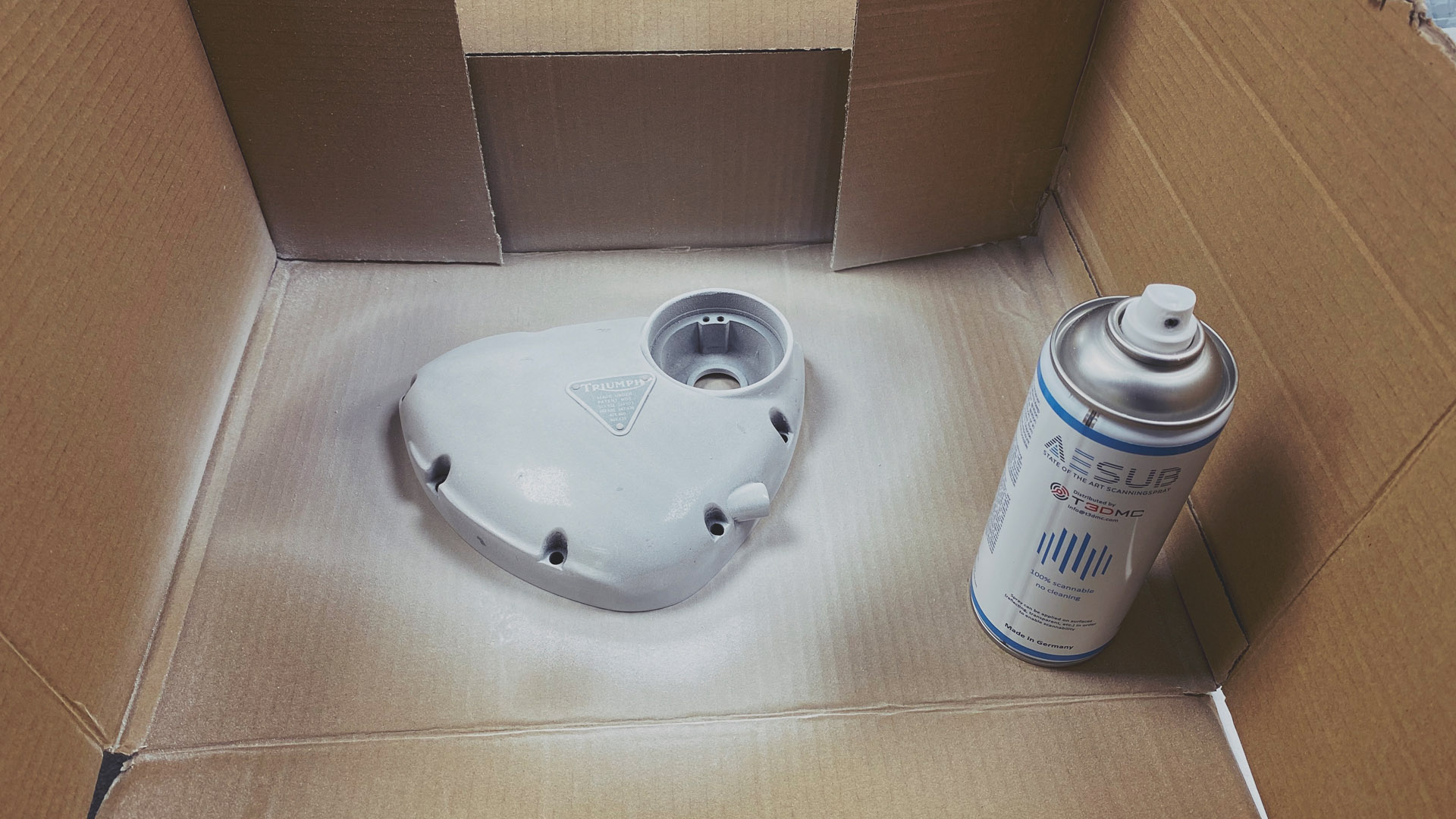