Looking to put its Theta camera to work on monitoring its own factory production lines, Ricoh used nTop to redesign its casing and enable it to let off some heat
The Ricoh Theta is a pocket-sized, 360-degree camera, capable of capturing high-definition (HD) environments at the click of a button. Users say they love its simplicity, which frees them from having to worry about the angle of view, tilt or settings. It’s a popular tool in real estate and auto sales for creating virtual tours. Visualisation artists use it for making HDR backdrops.
Meanwhile, Ricoh was keen to put the camera to work internally, providing 24-hour monitoring of factory production lines. To provide this kind of streaming, the camera would clearly need to operate continuously in environments as hot as 32C. However, as a safeguard to prolong the life of its components, the Theta camera is designed to shut down automatically when the main circuit board senses it might overheat.
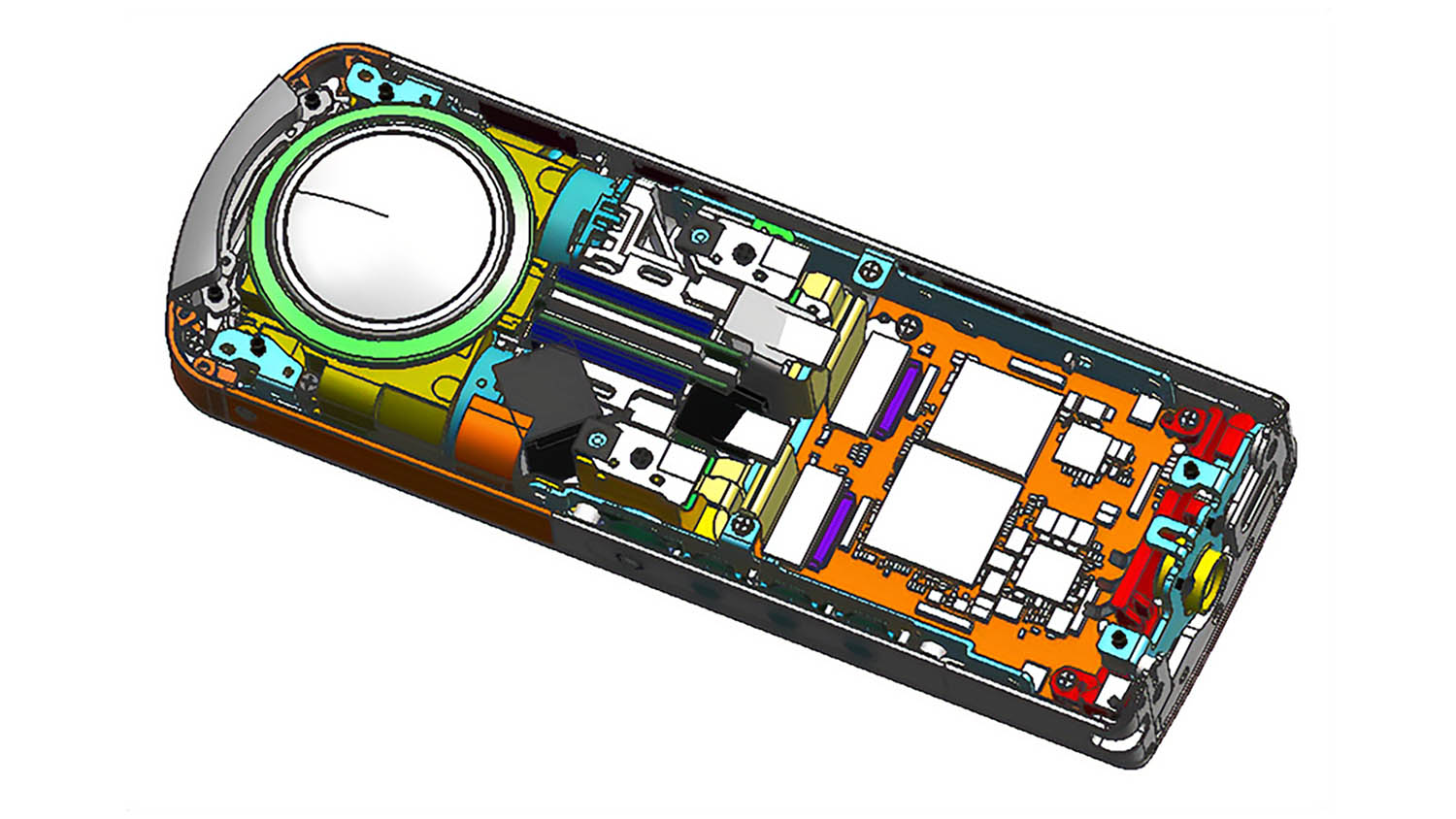
To get round this, the design team set out to remodel the camera’s casing, to improve the performance of heat exchangers and dissipate sufficient excess heat to keep the camera running 24/7, regardless of its environment.
Keep it in the family
Determined to keep the project in-house, executives at Ricoh chose the company’s own aluminium binder jetting capabilities to manufacture the redesigned casing, in what would be an excellent test of its own metals 3D printers.
In part, that’s because aluminium is notoriously difficult to use in combination with binder jetting, due to oxidation in the sintering process. However, Ricoh’s technology uses a specialised binder and a unique sintering process that delivers parts reliably. This was perfect for producing the small, complex features of the camera cover.
A gyroid structure was chosen for the design, driven by the need to improve heat dissipation and also take full advantage of 3D printing. Using nTop’s implicit modelling software, this gyroid structure could be tuned for the best heat transfer performance, since it creates a lightweight, self-supporting structure with a high surface area to volume ratio.
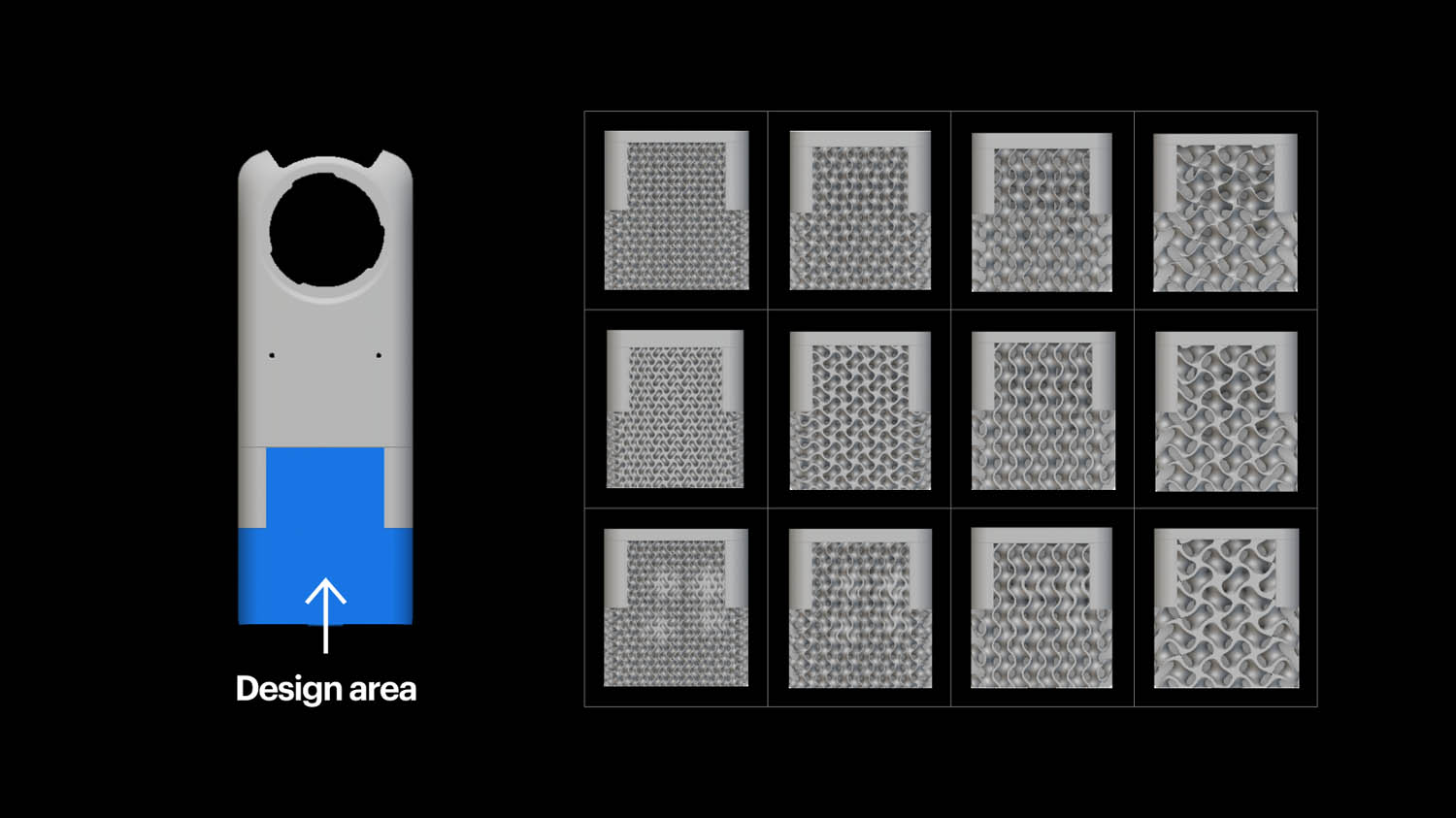
Ricoh created several models of the camera cover gyroid in nTop using as its parameters XYZ cell size and wall thickness. These models, created almost instantly in nTop, would have taken hours to build as traditional CAD models. Because of the time savings achieved, the design team was able to iterate and test multiple options to find the best solution for its thermal management goals.
“NTop is great for solving thermal issues, because it allows us to model and test the geometry needed for heat dissipation easily and quickly,” says Tsuji Masato, mechanical designer in the development for mechatronic and software section at Ricoh.
“With conventional CAD software, it is practically impossible to evaluate multiple complex shapes such as gyroids. With nTop, creating and testing these shapes was easy.”
By creating a gyroid structure in nTop, the Ricoh team was able to redesign the heat transfer paths, allowing heat to faster dissipate through the front cover of the camera housing and keeping internal electronics 24% cooler than was seen in the previous design.
With the new elements of its housing in place, a Theta camera could easily run for over 24 hours in continuous use without coming anywhere close to overheating. As a result, it can be put to a cool new use, thanks to a simple section redesign.
This article first appeared in DEVELOP3D Magazine
DEVELOP3D is a publication dedicated to product design + development, from concept to manufacture and the technologies behind it all.
To receive the physical publication or digital issue free, as well as exclusive news and offers, subscribe to DEVELOP3D Magazine here