As designers and engineers continue to explore additive manufacturing, achieving the perfect finish is becoming a big focus and requires attention, as Steve Alviti president of Bel Air Finishing explains what factors prove the best finishing processes for 3D Printing
Additive manufacturing, or 3D printing, is becoming a widely popular form of production, but it comes with its own set of challenges. One of these is the finishing process, otherwise known as post-processing.
In the medical, automotive, aerospace and firearms industries, many companies struggle to develop and improve finishing processes for their parts. At Bel Air Finishing, we’ve created a set of steps to help them.
We believe that, in order to get the most out of finishing, it’s important to understand both how the process should work and how best to measure results.
Optimising Form For Finish
First, a 3D model of the part should be made available, in order to provide valuable information on how the part’s structure and size will affect post-processing.
This will help narrow down the machines, compounds and media that should be used.
Consider, for example, a large part with a complex geometry sent to Bel Air; since there are many aspects associated with this geometry, it’s best for us to hold a conference call with the customer to acquire background information about the part and its function.
This helps decide which specific technologies to consider and provides vital information for creating a feedback loop that can improve post-processing.
The part may not be fully optimised for post-processing. By suggesting alternative print layouts, we can make post- processing faster and more effective.
This step also aims to preserve and/or improve the cosmetic and functional aspects of the part.
Once suggestions have been taken and the design of the part agreed, it’s then time to consider its finishing needs.
The purpose of your parts is an important thing to consider, since it directly affects the details of the finishing process.
Deciding whether or not a part’s finish should fulfill cosmetic and/or functional purposes is important.
Parts can be made to be shiny, matte or coarse, among other surface qualities. The part can be processed to a certain Ra value – a measure of the surface’s roughness.
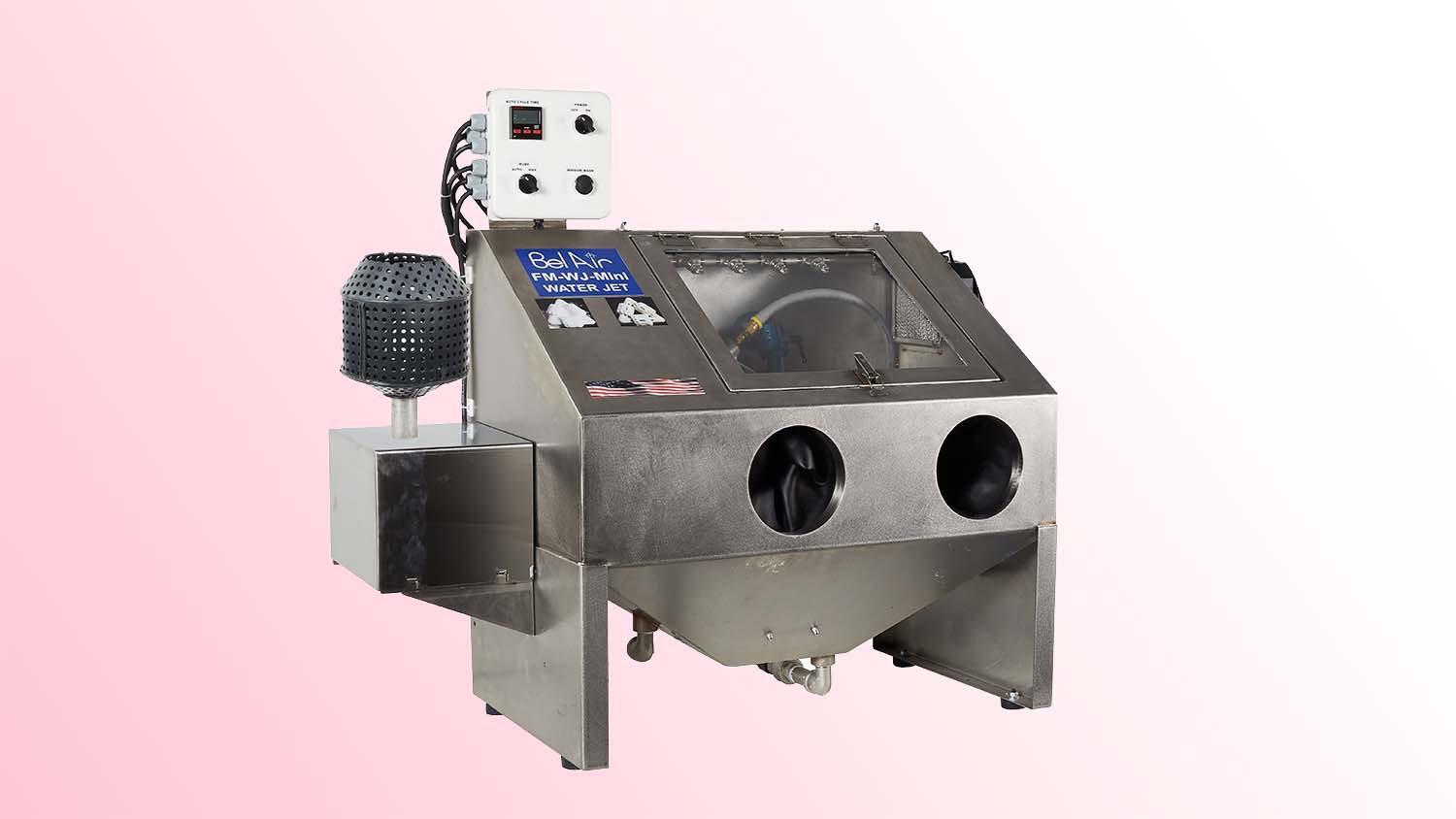
Measurable Goals For Finishing Processes
Manufacturers also need to know how many parts they want to process a day and how consistent they want that process to be.
In the mass finishing world, no two parts share the same exact finish – there are always slight variations.
There are also likely to be small defects in the processing of parts, whether they come from printing or accidental wear-and- tear during post-processing. Therefore, you need to consider the margin for error: What is acceptable here?
Furthermore, additional processes might be considered. Dyeing, coating and electroplating can all improve the look and feel of finished parts. Once the criteria have been set, the parts are ready to be processed.
Sending a sample of acceptably finished parts is an important step in creating a more effective post-process. At Bel Air, we are able to take sample parts and analyse them to determine the exact cosmetic and metric details of the part using Zygo optical metrology equipment.
This means that surface data is recorded using a contactless method and a 3D image of the surface is created. These provide an in-depth look into how surfaces might be improved.
Once a part has been analysed thoroughly, it is time to decide what technologies to incorporate into the sample process.
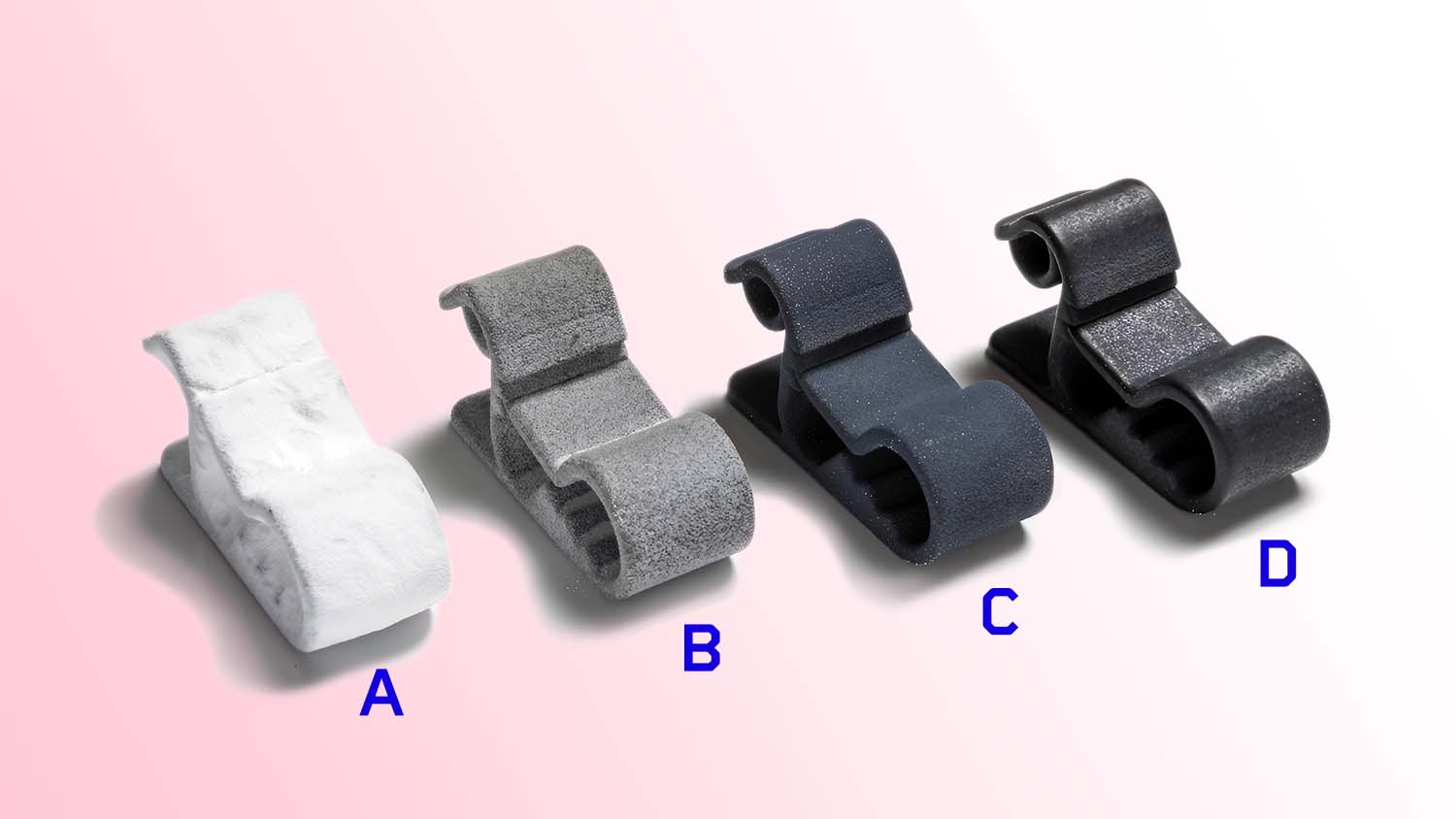
(A) Raw part, (B) Water-blasted, (C) Low-energy finished and dyed, (D) High-energy finished and dyed
A sample process is determined based on the manufacturer’s needs; these might include finish quality, price and/or pure throughput.
Machines, media and compounds are recommended and then selected for the sample processes. Then, the processes are performed and metrology is taken to determine the exact effects and results of each one.
Once that’s complete, it’s time to discuss those results and determine how best to move forward. Additional equipment might be considered, in order to preserve the life of machinery and media and to lower maintenance costs.
More sample processes can be created and manufacturer specifications changed, in order to further improve a finish or create a more realistic one.
We have developed these steps for in order to provide manufacturers with everything that they need to create the best finishing processes for 3D printing, while also providing them with solutions for their coating, electroplating, dyeing and surface analysis needs.