With luxury car manufacturers keen on spoiling passengers with the highest sound quality and refinement, it’s of no surprise to hear the lengths to which how marques like Bentley are working to reduce aeroacoustics annoyances in their plush cabins.
The electrification of the automotive industry has altered the acoustic environment – no combustion engine means that other sounds come to the fore, typically aeroacoustic sources – even glazing panels make noise. With conventional cars and engine noise, it’s hardly audible, but the sound from glazing panels can be rather irritating when driving a quiet, electric vehicle.
Acoustic engineers work hard to predict all potential noise contributions; they study a multitude of source types and locations and the paths on which noise is transmitted to vehicle occupants. To quantify these sources and paths early enough in the development process to remove or mitigate their contribution without costly late design changes, acoustic engineers at Bentley have been relying on computational methods to predict whole vehicle aeroacoustic interior noise of new designs.
In a joint study with ESI, Bentley has looked to develop a cost-effective approach to predicting whole vehicle aeroacoustic interior noise early in the development process by reducing the reliance on expensive physical prototype vehicles.
A typical vehicle’s body structure can produce as many as 100,000 modes (up to 8000Hz) and 250,000 modes for the interior cavities, which would require many millions of degrees of freedom to be able to map the small wavelengths associated with these high frequencies.
The team, on deciding that deterministic methods would not able to handle such amounts of data in order to reach the higher frequencies of the audible range, so instead took a statistical approach. As high-frequency amplitude variations are influential in the perception of automotive aeroacoustics, the research team concluded that a CFD and a statistical energy analysis (SEA) combined approach should be used.
SEA is an established methodology to perform interior noise and vibration prediction and sound and damping pack development. Using the SEA module of acoustic simulation software VA One – an evolution of the industry-standard AutoSEA2 – the model was defined to provide the best understanding of the energy flow around and within the vehicle, enabling a large variety of analyses.
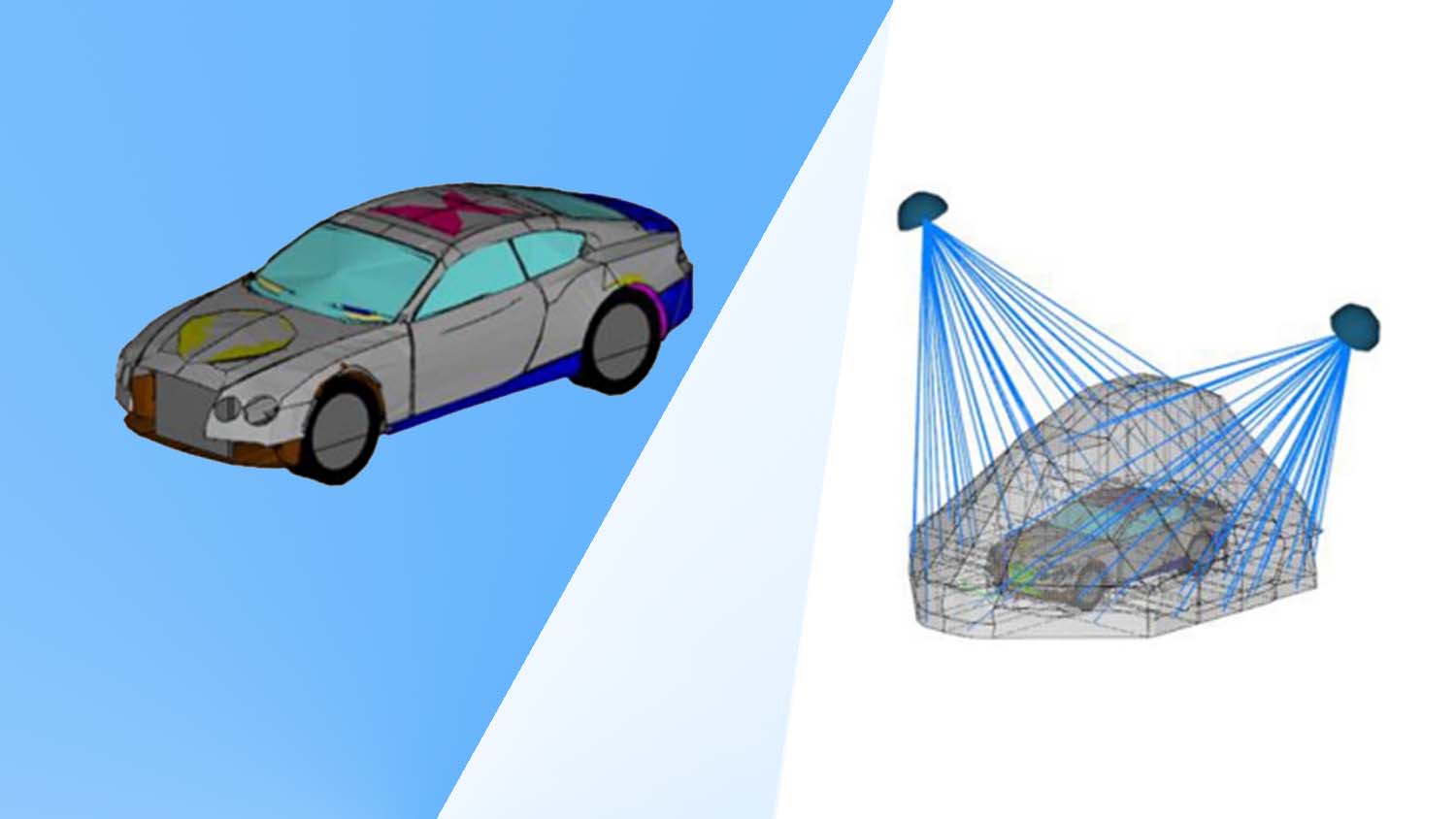
The exterior sound field was comprised of near-field and midfield cavities, which were discretised to allow diffraction effects to be considered. The midfield cavities were also connected to a semi-infinite fluid to represent an unbounded exterior acoustic space.
After two CFD simulations the team exported the panel excitations into acoustic simulation software VA One. Following wavenumber frequency, spectra calculations for each panel were applied to a whole vehicle SEA model.
The results from the simulation process were compared to the measurement data performed in the FKFS full-scale aeroacoustic wind tunnel, based in Stuttgart, Germany, using a luxury Bentley coupé comparable to that modelled for the simulation activities.
The wind tunnel moving belt system and vehicle wheels were both stationary, reflecting the CFD simulation. The test vehicle’s seals and ‘shutlines’ were taped to remove the contribution from potential aeroacoustic leakages caused by gaps in the vehicle sealing system.
According to the test team, the total interior noise predicted via the CFD and SEA method correlated very well with the wind tunnel measurements, creating an option for future easy stage testing and development.