Precision production has been essential at Manufactura Moderna de Metales since it first started supplying the transport industry in last century. Today, its additive manufacturing capability is an invaluable tool for developing new products for the future of automotive
A key supplier to the transport industry since its foundation in 1944, each generation of management at Manufactura Moderna de Metales (MMM) has looked to progress the company’s production capabilities in order to keep pace with the very latest developments in automotive systems.
Headquartered in Barcelona, Spain, with facilities in Romania and Mexico, MMM has built a reputation for designing and manufacturing advanced fluid conducting products. Currently, it provides cooling, air recirculation, vacuum, fuel and brake systems in steel, stainless steel, aluminium and its alloys for brands like Audi, BMW and Toyota.
In 2019, the company added 3D printing technology to its production processes, initially with the aim of producing fixtures and shims to mount precision tubing.
“These tubes have different diameters and are expensive, so when you can print the tube and validate the shims, and get the right diameters and fixtures to simulate assembly and mounting during production, then you have a fantastic advantage to offer your customers,” says MMM’s Borja Batlle, business development manager of the company’s 3D printing division, Addival.
“We have managed to design and produce fixtures that are 100% printed in three weeks and ready to validate the whole process.”
The team realised it could create precision metal tube bending tools for the development stage as well as new shims and other control tools for use in both production and development stages with deviations of 0.05 mm.
“Over the last five years, we have cut down component delivery time from an average of 58 days to just two to three weeks, even taking as little as three days in some cases. A complete success story!” says Batlle.
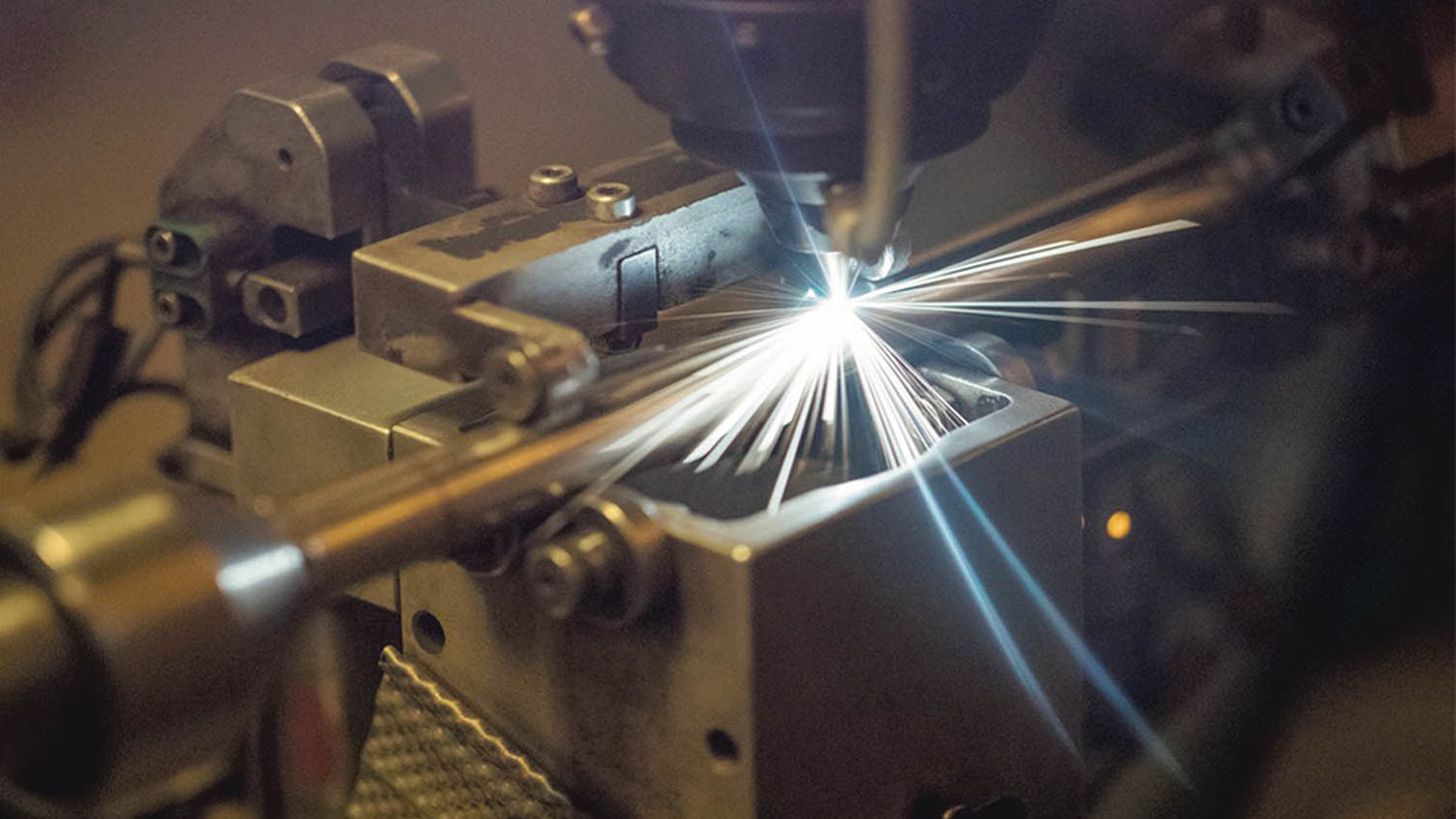
Production flows
At its Romanian factory, MMM has designed a fixture for checking rubber sleeves, creating an internal mechanism inside the fixture with a worm gear. “Thanks to the highprecision build, the fixture could be used to check the maximum deviation of 1.0 mm at the tube ends,” says Batlle.
“This play, which determines the precision for finding a part’s tolerance, has saved 60% of the total time for the cycle. These sorts of mechanisms cannot be incorporated using traditional methods, so it’s only with composite fixtures that we can create solutions like this.”
To complement its machining processes, MMM acquired a Markforged X7 3D Printer, primarily for its ability to print parts reinforced with continuous fibreglass and carbon fibre composites.
Initially used for prototypes, the X7 is now used to design and produce final components directly in the factory, thanks to its balance of ease of use, precision and versatility, says Batlle.
Buoyed by this success, the next step saw MMM introduce a Markforged Metal X 3D printer, allowing the company to combine its output with the polymers from the X7 to create high-strength, light-weight hybrid fixtures.
“We have used 17-4PH stainless steel and H13 tool steel in the Metal printer, although we specialise in pure copper components for high-conductivity parts,” continues Batlle, explaining that some printed copper parts are used as welding electrodes.
In a sector demanding specialised parts, it’s the precision that MMM is achieving with 3D printing that is driving results and the next generation of the company’s evolution.