The goal of a loudspeaker is to replicate sound exactly as recorded – so who better to achieve this than experts taking their knowledge of studio monitors and applying it to home speakers? Stephen Holmes speaks to the team at PMC Audio to hear more
PMC Audio founder Peter Thomas has the perfect metaphor to explain the process of audio engineering to the uninitiated. Audio, he says, “is like shining a light through seven plates of glass that are slightly opaque, and the light just about reaches the end. If you clean one of the plates, then the light still doesn’t all reach the end, because the other opaque plates stop it. So, what you’ve got to do is clean each opaque plate to gain some improvement to get the light better at the end – and that is what audio is about.”
In other words, there’s no magic solution based on fixing one particular component or element, he says. “You have to raise the game in all of them.”
After more than three decades dedicated to recreating flawless audio, PMC Audio has got closer than most. The company got started in 1991, when it delivered its first-ever products to the BBC’s Maida Vale studios. Britain was going through a recession at the time, but former BBC Radio engineer Thomas and his business partner Adrian Bauch were able to kickstart the Professional Monitor Company (PMC) with one product and a single customer.
Guerilla marketing played its part. PMC speakers were lugged around various music labels and Hollywood studios in the back of a van. Today, the company’s products are used by an impressive number of leading recording studios and some three-quarters of all film scores are mastered using PMC kit, according to Thomas.
The goal has always been to replicate sound as close to how it was intended to be heard by its producers – and that applies equally to mixing desks and homes.
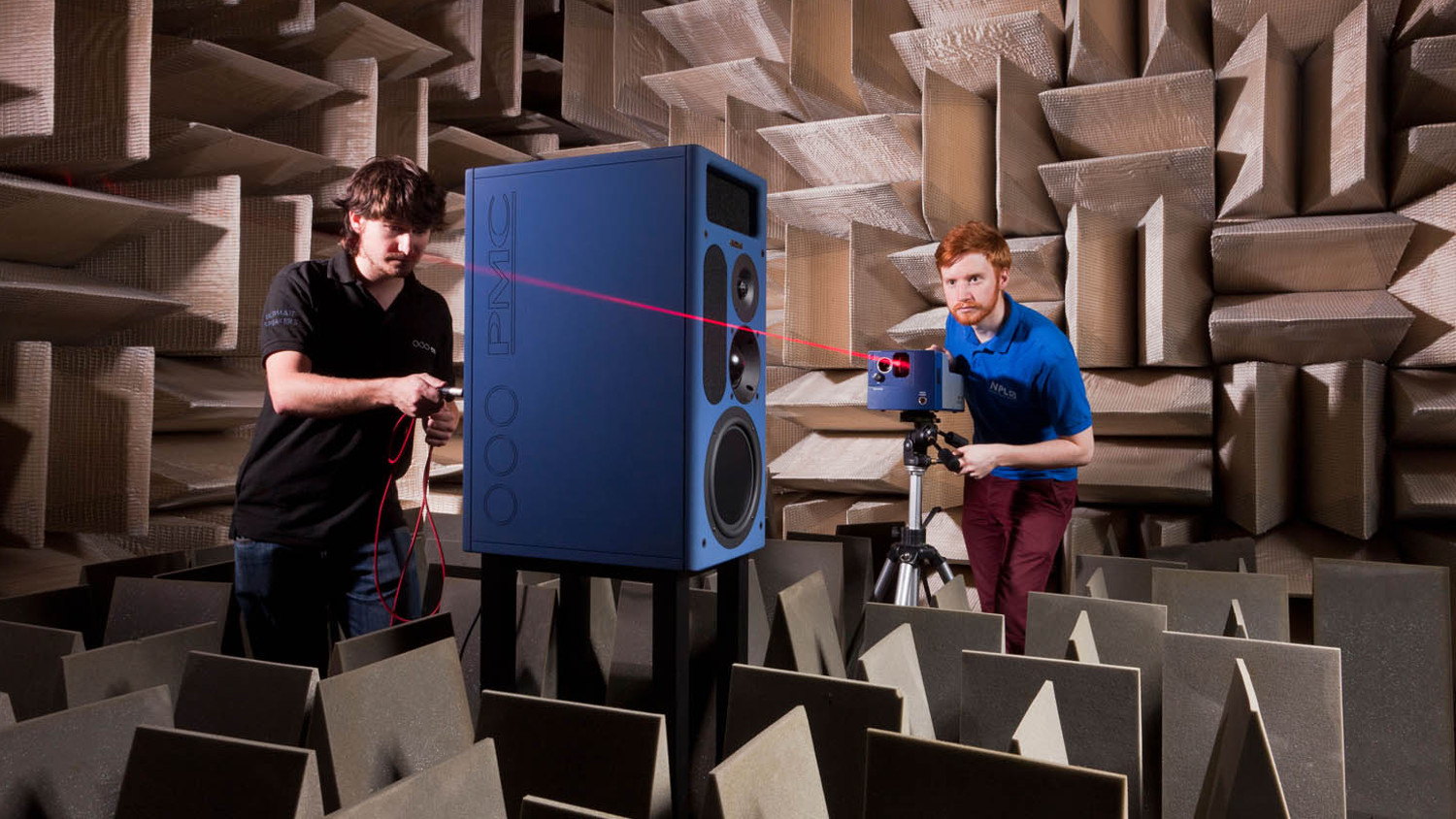
PMC Audio – Low notes
PMC’s flagship studio model, the QB-1, is a beast. It’s designed to be mounted in studio walls, where it is able to produce the full frequency range as loudly and as clearly as possible. Key to this is a technique from the 1960s called Transmission Line, a method of producing more bass from a smaller cabinet.
PMC’s highly tuned version of the technology is known as Advanced Transmission Line (ATL). After snaking through a cabinet lined with a proprietary acoustic foam that absorbs all but the very lowest frequencies, the bass exits from a front-panel vent, extending the low-frequency response, and creating the impression of a far larger speaker.
The calculations required to perfect this are complex. These frequencies need to exit the speaker in phase with the output from the drivers. Yet the results are worth the effort, with ATL producing clean and clear bass that doesn’t mask the rest of the music.
Oliver Thomas, Peter’s son and company CTO heads up PMC’s team of five engineers. “The speakers are tools for mixing audio in the studio world. That is always the core, fundamental part: the performance, how it measures, how it sounds,” he says.
“The very first step of the product development cycle is looking at the speaker enclosure, because that’s the biggest variable in many ways to try and nail down. We then develop the acoustics within that, and then move from that towards other aspects, like the electronics, and finally a bit more of the aesthetic design to pull it all together.”
Speed of iteration is important here. Simulation tools play an important role, but building a physical product to test is essential. Using Solidworks, the team builds the initial 3D CAD model around its ideas for how the acoustics will work inside the speaker enclosure.
From here, the engineers assess the design using a ‘rudimentary’ proprietary simulation tool, and then use Comsol to run an FEA analysis focused inside the enclosure. Additional simulation software like the niche Physical Lab LEAP may also direct the design, with its analysis of crossover electronics. Once developed in CAD, prototypes can be physically built, and further analysis undertaken.
PMC Audio – Testing times
With the mechanicals and the acoustics nailed down, Oliver Thomas and team then start to take a look at electronics.
“It’s typically the crossover: we have multiple different drive units in an enclosure that produce different frequencies better, and so we need to filter the frequencies from the audio signal to be sent to the right driver,” he explains.
Listening tests are synonymous with this part of the process. These tend to take place in the later stages of development, with engineers using their ears to make sure that the measuring done to this point is accurate.
When PMC Audio moved into its new facility in Bedfordshire, UK, the team built a hemi-anechoic chamber, used for taking measurements and analysing performance, giving it the chance to compare real-life results against simulations.
“It’s quite a balancing act between the listening tests and the actual measurements,” says Thomas, “But as we get more sophisticated measurements, that gap starts to close a bit further.”
An R&D project in partnership with the National Physical Laboratory (NPL) helped further close the gap. PMC co-developed a new acoustic measurement technique using a laser-based technology to measure tiny changes in the refractive index of the air in front of the speaker that were caused by the sound, allowing them to measure the sound pressure.
This took analysis to the next level. “Rapidly, we could measure at each different point in a sort of threedimensional space in front of the speakers,” says Thomas. “We could literally build up a 3D image of a soundwave being transmitted from the speaker, in a way that is only possible with some simulation software.”
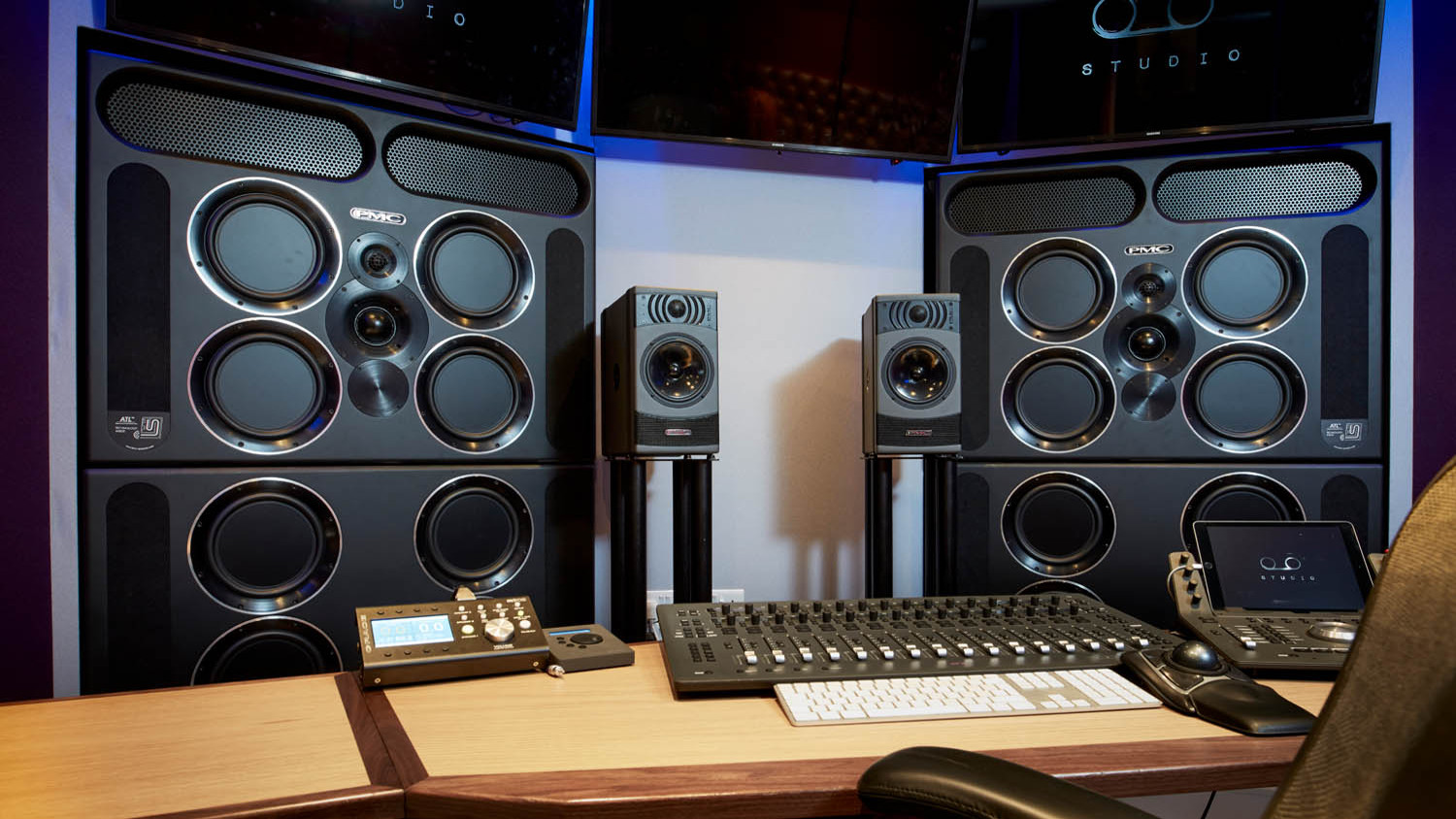
Sounding clear
However perfect speakers might be on paper, explains Peter Thomas, there is always a level of ‘unknown’ in how audio works and how to get the very best results.
“It’s still a 50/50 between actual engineering measurements and using these two things on your head, because none of the measurements really tell you how it’s going to sound as a whole,” he explains.
“It’ll tell you how individual elements sound, and how accurate they are, but you can produce a speaker that measures wonderfully well, but sonically has something wrong with it.”
To attain the best possible results, most elements of the speakers are produced in-house, or made to specification by a small number of trusted specialists. The faultless veneered cabinets, meanwhile, are still CNC-machined and hand-assembled in Britain, with both old and new skills mixing to achieve the right balance of craftsmanship and minute tolerances.
PMC Audio is now in the first stages of using 3D-printed production parts. It has already used some small SLS components in initial production runs, before tooling was created for injection moulding.
With its products fitting the low-volume/highvalue mould, there’s every chance that more additive manufacturing will figure in future designs, as market demands mean shorter development times.
In the early days of the company, Peter Thomas used modelling clay to sculpt the front of the speaker, which could take weeks. Now, with 3D modelling, parts can be 3D-printed, tested and iterated in a matter of hours until, sound-wise, they’re perfected.
“As a company, that’s what keeps you alive – developing new techniques – and that’s where Oliver and his team come in, with new techniques to explore areas that I just didn’t have time to do,” he says.
“He’s measuring vibrations now on cabinets down to infinitesimal levels. I knew they were there, and I could measure them, but I didn’t have the time to develop a better cabinet.”
Little by little, he adds, PMC Audio is gradually nibbling away at unwanted vibrations in ways that make the final product sound much better for customers. So while it might be true that light will never shine at full strength through those seven glass plates, for PMC Audio, the future is looking much clearer.