Inadequate lighting can be a real headache for dentists, so Swiss orthodontic solutions company Mikrona developed the LX Master Mirror, which both shines a light on their work and gives them a clearer view
Few people enjoy having to sit back in a dentist’s chair. Even fewer want their visits to drag on any longer than necessary. For dentists dealing with back-to-back appointments, getting clear visibility on a patient’s dental issues as quickly as possible can help avoid uncertainty, errors and eye fatigue. Mikrona knows these challenges well. The company has been developing dental tools and other equipment for over 50 years. With lighting challenges in mind, it set out to design the ultimate tool for precise and accurate visibility within the oral cavity with its light-enhanced LX Master Mirror.
Adding lights to the mirrors that enable dentists to inspect hard-to-reach areas of the mouth and make fixes where needed is nothing new. But in this case, Mikrona’s designers looked to address other user requirements, too: simpler sterilisation, specific light temperatures and reusability.
Development of the LX Master Mirror began with the team building up a booklet of sketches, working on the ideation of features and proposed best forms for the handheld tool to take.
The first challenge was finding a shape that everybody liked. “We found that dental professionals have very unique tastes as to how their tools work within their hands,” explains Mikrona industrial design lead Luke Guttery.
“We had to work very hard on the length of the handle, the balance point and the indexing (hexagon) shape. We also had to take into consideration the many different sizes of hands, if gloves are worn and if the surface gets slippery.”
Guttery explains that this required the team to undertake in-depth research into material finishes and industry standards, not to mention patient mouths. “These come in all shapes and sizes, and to work out the size of the mirror and distance to the fibre optic to get the right reflection was an interesting challenge for the team,” he says.
Tools of the trade
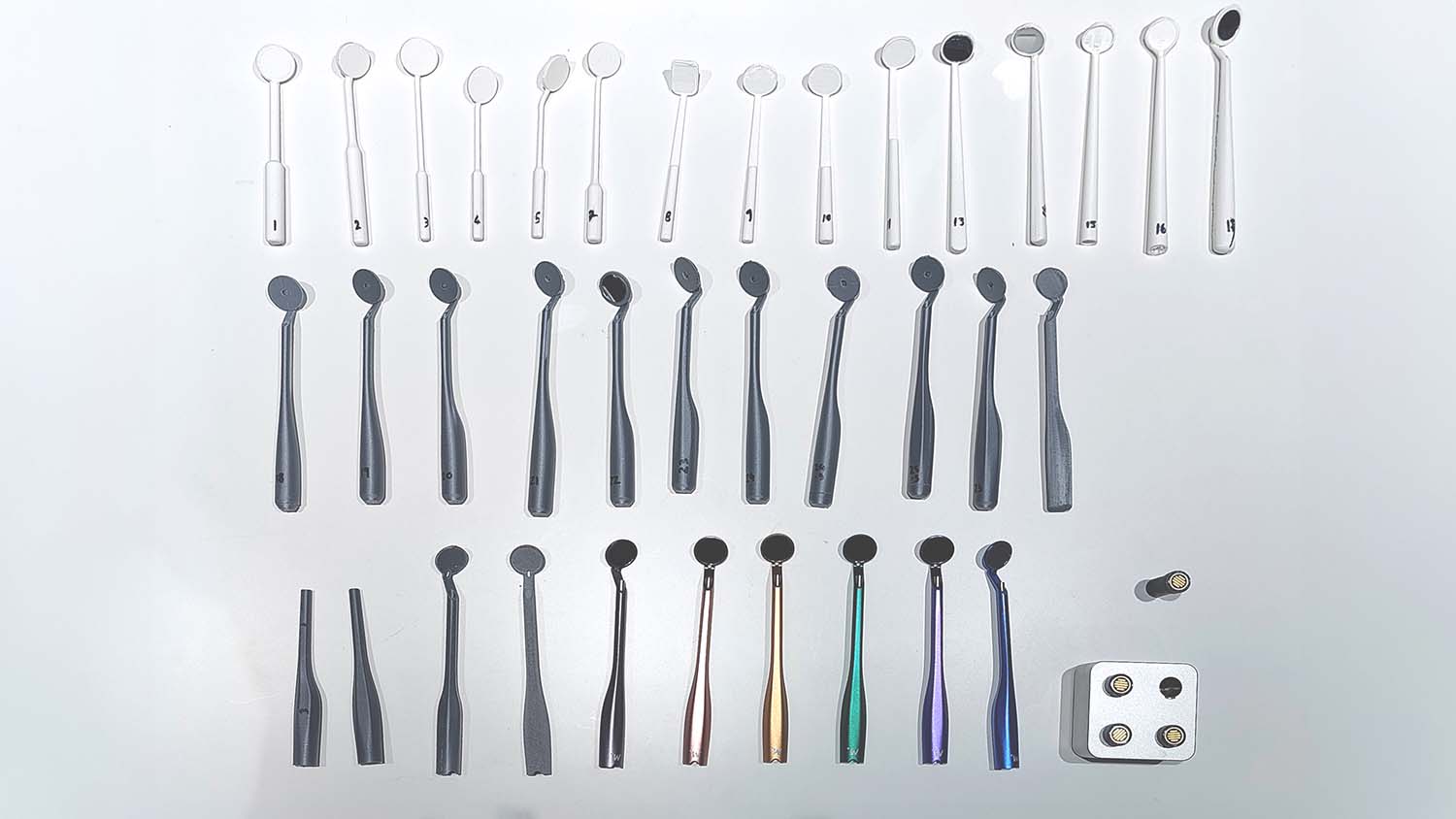
The project was engineered using Solidworks from the ground up, translating sketched shapes into surface models. These then allowed rendered concepts to be quickly produced in Luxion Keyshot, in order to help narrow down design intent before moving into physical prototypes.
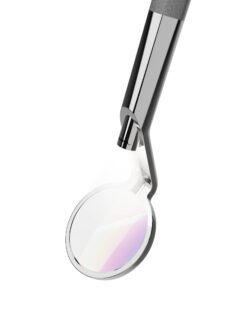
“From here we move to the 3D printer within the same day, sometimes within 30 minutes of concept generation,” says Guttery. The first stages of ideation, he adds, saw the team print over 40 different models using an in-house UltiMaker S5 3D printer.
“These prints were then reviewed and tested with clinicians to determine which design provided the best ergonomics for use in dental procedures. The chosen design was then refined to meet the specific requirements of the users, including high clarity mirror and specific light temperatures,” Guttery explains.
“The S5 can pump up very rough prototypes at 0.2 tolerance that are great for gauging size in the hand and overall shape,” he continues. “It can also in its finer setting produce really nice prototypes for more detailed fittings and connections.”
For larger scale prototyping, the Mikrona team turned to UK-based service bureau Printing Portal, which is equipped with HP MultiJet Fusion 3D printing for faster turnarounds at volume. Key challenges were settling on a design that was biocompatible and could be easily sterilised. These were addressed through materials and manufacturing choices.
Mikrona selected as its material Stainless-steel 316, which can withstand high temperatures and pressures and offers appropriate biocompatibility features. When the project reached the stage of creating working prototypes for testing and validation, a local CNC prototype producer machined several batches of fully working tools to allow for in-house testing. The handle can be autoclaved after each use, ensuring it remains hygienic and suitable for use in clinical settings. The Microbeam lighting module can be hand disinfected and reused in the next procedure.
Open wide
The MicroBeam LED light is attached to an ultra-reflective Rhodium mirror, giving bright and focused illumination. This allows dentists a clear view of the patient’s mouth, while ensuring that light remains consistent throughout the procedure.
Capable of running for 120 minutes, the module is offered in either day light, cure safe light and UV light versions.
The day light module is perfect for everyday procedures and check-ups, providing a bright, clear light. The MicroBeam CureSafe option provides an orangetinted light designed specifically for procedures that involve UV glue, which can prematurely cure under certain types of light. The UV light version allows for check-ups of composite fillings and retainer anchor points and searching for residual glue left over from previous procedures.
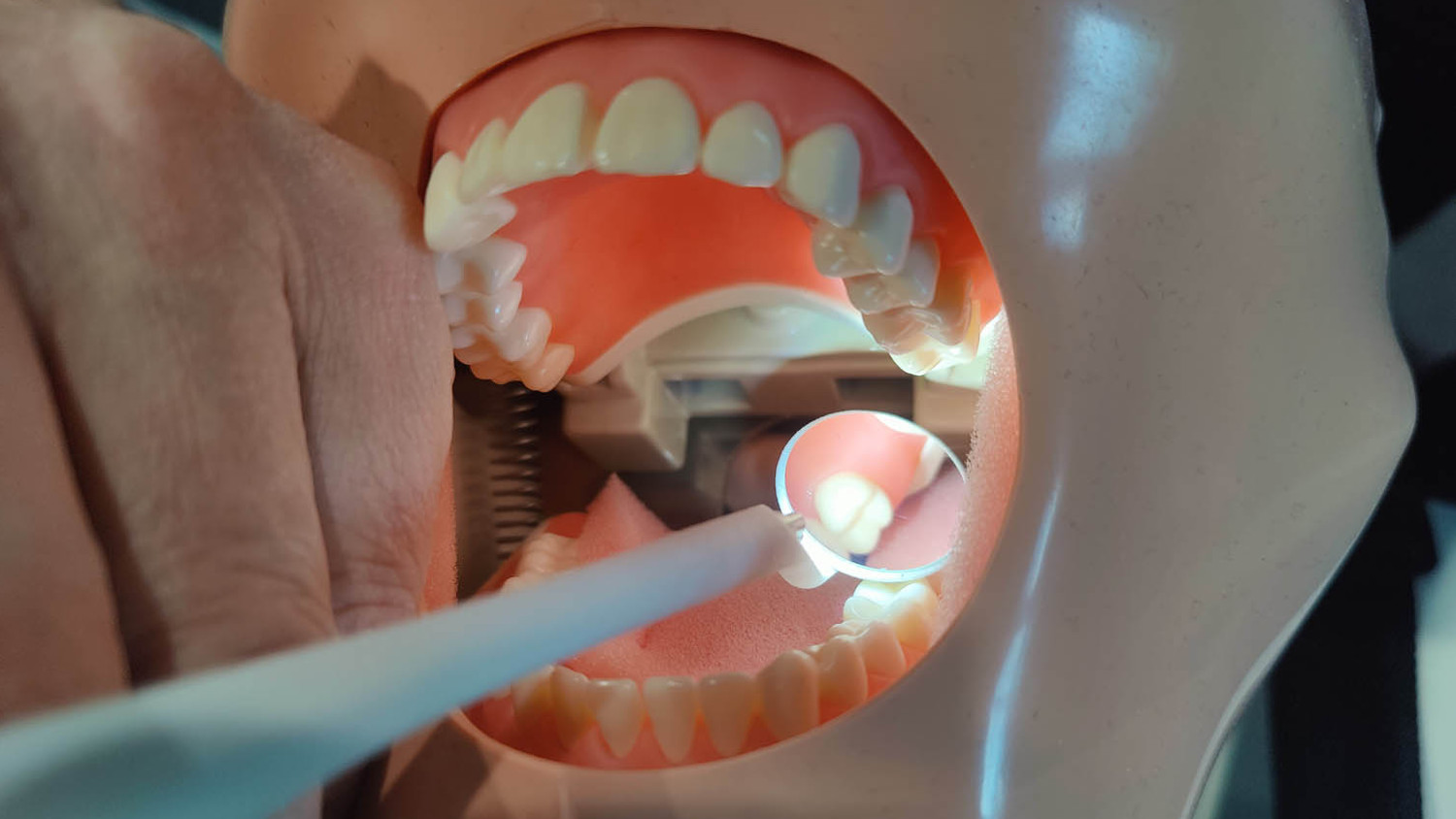
To achieve the best light, fibre optic technology was used, forming a critical step in the development process. The team worked with a Swiss fibre optic specialist FiberOptics to develop the correct optic dimensions and light reflection angles for the optimal performance.
The result is a light junction shaped to match that of the fibre optics’ reflective angles, which ensures all light is directed onto the mirror surface. Sensor specialist Dynaforce was enlisted to calibrate and perfect the feel of the on/ off switch in a multitude of environments. “Since this HMI input solution is based on force touch, we are able to use it in all environments, such as with thick gloves, with wet or dry hands, even under water! The system can even be adjusted in force pressure, depending on customer need,” explains Guttery.
The LX Master Mirror uses a 7x2mm sensor soldered onto a PCB board. Assembled to a polycarbonate cover, it acts as the user interface. On the PCB board is a preprogrammed microcontroller that measures the force applied on the user interface.
“It’s not easy to pack the LED tech and a very high-end touch sensor into a tiny housing that must be sealed from the elements, cleaned with hard chemicals regularly, recharged and complies with medical standards!” laughs Guttery. “Luckily we have fantastic internal and external experts who assisted us in the development.”
Following comprehensive testing, the product is now proving its worth in clinics.
This article first appeared in DEVELOP3D Magazine
DEVELOP3D is a publication dedicated to product design + development, from concept to manufacture and the technologies behind it all.
To receive the physical publication or digital issue free, as well as exclusive news and offers, subscribe to DEVELOP3D Magazine here