Electric cars are now a common sight on UK roads, but a goods vehicle powered by electricity is a far rarer beast. Stephen Holmes visits Tevva, a start-up looking to extend the capabilities of electrified trucks with the help of hydrogen
There are over half a million goods vehicles on the road in the UK. The vast majority of them (some 98.8%) rely on diesel to make deliveries, collect household waste, transport fuel and so on. So it’s pretty shocking to consider that in the transportation sector, freight trucks emit more carbon dioxide than aviation and maritime combined.
And despite the uptake in electric passenger vehicles, trucks and lorries have so far proved immune to the trend. As of 2021, only 520 battery-electric trucks and lorries were registered in the UK.
That’s a big problem. On a worldwide basis, a passenger car is driven, on average, just one to two hours per day.
In the case of electric vehicles (EVs), that leaves many of them with a store of power left over in their batteries and a 22-hour window of opportunity to recharge.
But trucks are a different proposition entirely, according to Tevva CEO Asher Bennett. For a start, a truck typically heads out on each shift with around eight or more hours of work ahead of it. At the same time, there is no specific range for a fully charged battery. So much depends on the workload ahead. Variables are far more diverse than those for a passenger car.
They include the distances involved, the terrain to be navigated, the individual operator’s driving style and the loads to be carried. These all vary hugely from delivery truck to delivery truck, and from day to day. And that’s before you even consider any additional energy needs, such as refrigeration for chilled goods in transit or garbage compacting capabilities.
No fleet manager will send out a truck in the morning if it’s not guaranteed to complete its day, whatever that day is,” says Bennett.
While EVs are often used on shorter routes, the issue of variability overrides one of the biggest advantages of an electric truck, which is that miles using cheap grid electricity are dramatically less costly than miles using diesel. Tevva’s company mission, explains Bennett, is to replace diesel trucks – and not just those working shorter, repetitive routes and carrying predictable loads.
At the heart of this mission is hydrogen. By adding a hydrogen fuel cell system to its battery-electric HGV design, Tevva can deliver zero-emission vehicles from its Tilbury, Essex facility that will work for most fleet operators across various sectors. The fuel cell system tops up the battery, extending the vehicle’s range and allowing it to carry heavier loads over longer distances.
According to Bennett, the current battery technology on a Tevva truck would cover 80% and 90% of users’ needs. “Most days, you won’t need anything more than that. But getting back to base ‘on average’ is not good enough!” he says. “So we back it up with the hydrogen fuel system.”

Call for back-up
The idea first came to Bennett beneath the ocean waves. A stint in the Israeli Navy means that his first EV was a submarine, powered by an electric motor, with a huge bank of batteries that could be recharged by onboard diesel generators.
In the case of Tevva, it’s the hydrogen system that acts as back-up, performing as a range extender or REX.
“Because it’s there, [companies] can send this truck out without worry,” says Bennett. Most days, they won’t need to use the hydrogen, but any day on which they do – like a trip to the maintenance depot, or relocating trucks for busy Christmas deliveries – then hydrogen will be the enabler of all those cheap miles already provided by the battery. “It really gets the economics going!”
A key advantage of hydrogen is its energy density over a lithium-ion battery. A 100 kg tank has the effective energy of 600 kg of battery. “And that’s about the battery [weight] we put on this truck. So, by adding one cylinder, we’ve doubled the amount of energy in this truck; two cylinders, tripled. We go for three – quadrupled.”
To manage this to its highest efficiency, Tevva has designed and built its own software, electronic management systems and batteries.
Its Predictive Range Extender Management System (PREMS) software is used to make a prediction of the energy needs of a truck on a given day. All the variables that normally count against an EV truck are fed into the first part of the equation to determine how much additional energy from the hydrogen will be needed to augment the battery power.
“The second part of the algorithm is, now that I know that we need to augment 60 kilowatt hours, let’s decide where it’s most beneficial and optimised to do so, not just wait till 3pm, end of day,” explains Bennett. The algorithm might opt to turn the hydrogen fuel cell on earlier in the day, but at half power, which gives 22% more efficiency than running at full power.
Such measures can lengthen the life of the fuel cell stack, or it can be used tactically; for example, when the battery is under stress from climbing a steep hill at high speed when fully loaded.
All of this is handled over the cloud, not by the driver, and as more Tevva trucks take to the road and feed back more data, the better the optimisation will become.
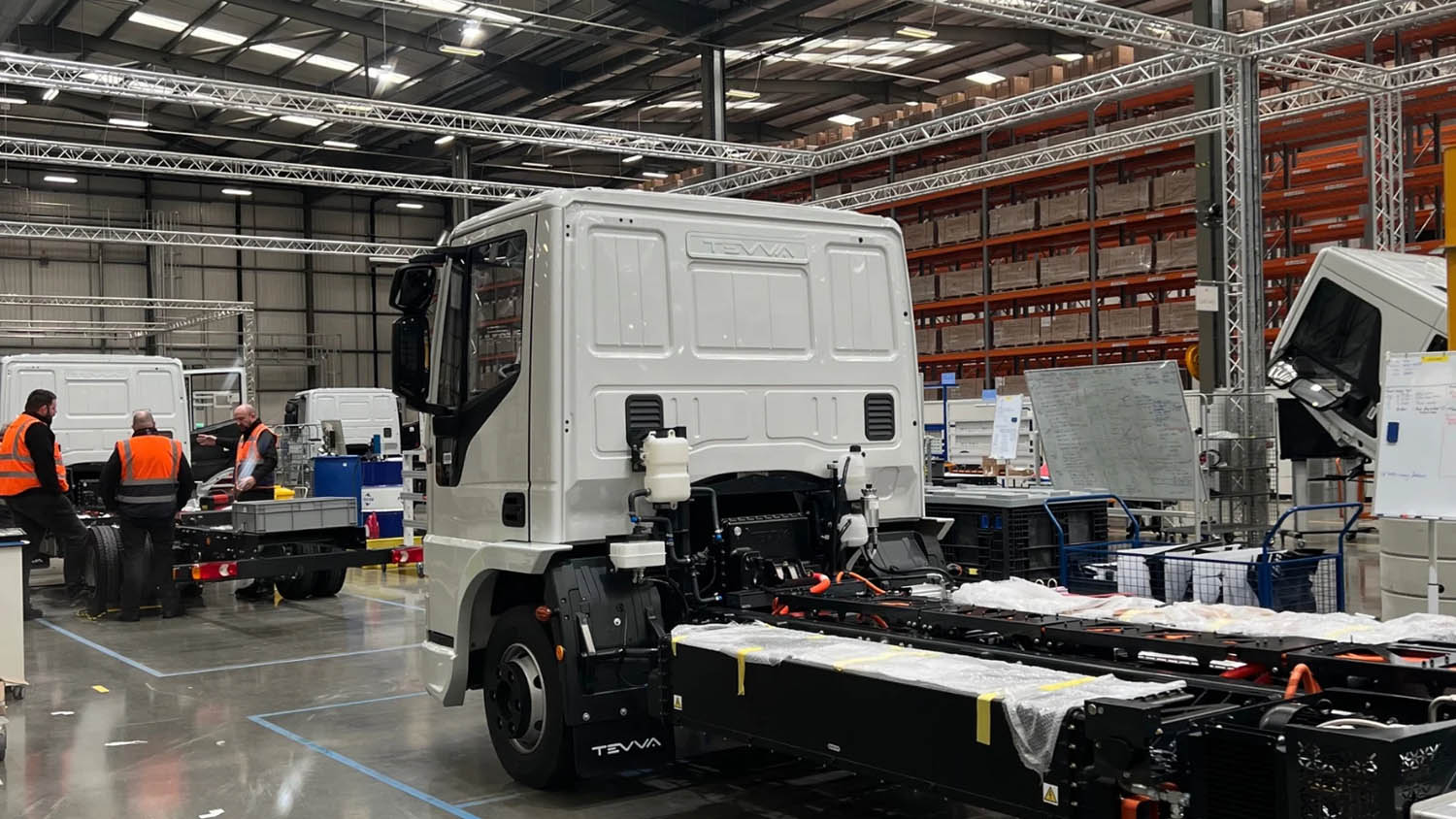
Hydrogen in, water out
The development of Tevva’s hydrogen-electric 7.5-ton model continues. A road-going prototype fitted with three hydrogen tanks recently covered more than 1,000km (approximately 620 miles) on a test run, in which it was driven from Tevva’s headquarters in Essex to the Scottish border on a single charge.
Under development for two years, much of the work involved testing and developing systems for the fuel cell technologies. Tevva REX engineer, Ryan Clark, explains that the team opted for supplier Loop Energy, a Canadian company. “They were best in terms not only of the engineering factors, like the efficiency and ease it took to integrate and fit the cabin, but also the commercial factors. They’ve been really good at supporting us, helping us with the design.”
Currently, there are three hydrogen storage tanks mounted behind the cabin, although this has been designed to be versatile, to accommodate future developments and provide modularity. “I think there is scope to reduce it to two in the future, because we might be getting batteries with more rounded capacity. And that’s all up in the air at the minute,” says Clark.
Should an owner have access to an abundance of cheap hydrogen, the truck is capable of running entirely on that fuel. It’s not the most effective way to run a Tevva Truck, according to the team, but it highlights the versatility that could give these trucks wider appeal as energy and fuel markets continue to be volatile.
Tevva’s current line of all-electric trucks, meanwhile, is already hard at work at companies such as parcel delivery giant UPS, a Tevva customer for around three years now.
The powertrain and systems of these vehicles have been developed in-house, including the batteries and the electronic ‘brains’ behind the management technology that is already feeding back valuable information to R&D.
Designing its own battery has been a key challenge for Tevva. While the team could buy batteries from a supplier, that would leave the company hostage to changes in price, battery technology and electronics specifications. Instead, they are assembled in-house on the company’s own assembly line, giving it full control.
The single-geared motor is actually two units mounted on a single shaft. Co-developed with a sister company based in Newcastle, it offers a redundancy safety advantage, as well as providing swift yet silent acceleration. Should one motor fail, the driver can continue a few miles further on the second motor, until they find a safe place to stop.
Each truck features five major control units, all developed by Tevva to manage vehicle control, the battery management system, power distribution, telematics, and on the hydrogen version, an additional unit for the fuel cell system.
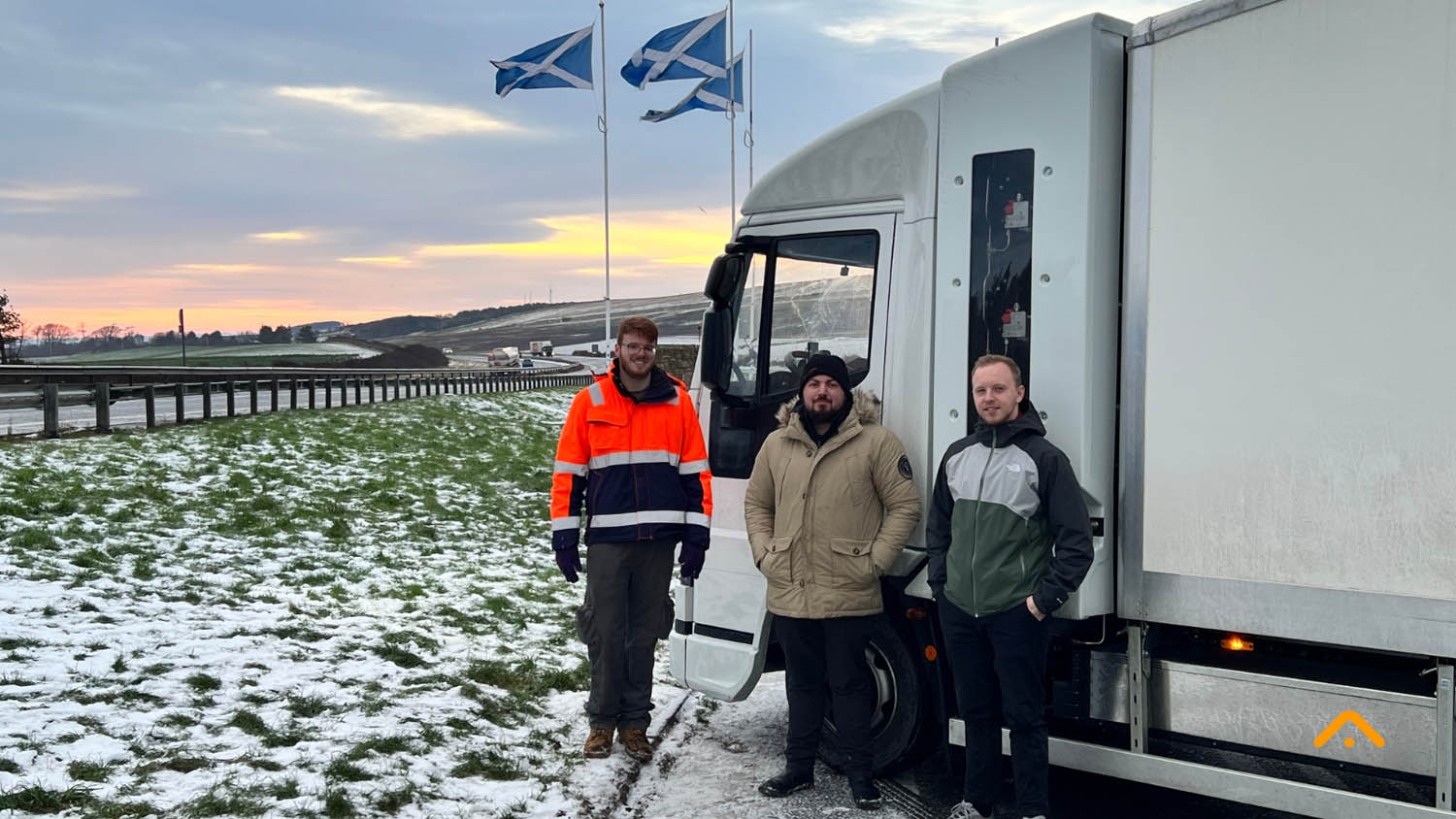
Joining the dots
All of this technology needs to be fitted together and positioned on a donor chassis and cab that is known as a ‘Glider’. This comes from a supplier that also produces the same parts for a widely used diesel-powered variant.
Working on another company’s platform comes with some frustrations, says Stephan Engelbrecht, Tevva principal engineering manager for concepts. But, he adds, it makes it easier to avoid the many pitfalls of developing a product of this complexity and scale.
“What we’ve done makes sense. Too many companies fail at the first hurdle of trying to produce their first ground-up vehicle. And you’ll fail on something trivial, which has nothing to do with the EV side of it.”
While the Glider has its limitations, these are issues that the design and engineering teams have found smart ways to work around.
A lot of that effort has been managed in CAD. Tevva’s initial designs were built in Solidworks, but with the scale of the project and team growing in size, the decision was made to move to Dassault Systèmes’ Catia.
The benefits were instantaneous, says Engelbrecht, giving the team at Tevva the ability to load up a model of the entire vehicle quickly and work in context without encountering problems.
“To me, that’s very important, because there’s so much effort downstream, trying to get everything to fit together. Because if a designer hasn’t looked at these systems when he was designing whatever he’s doing, it can become fairly problematic in big organisations,” he says.
“So the fact that it is so good at handling big chunks of data means collaborative design just [happens]. It’s not just a word. Everyone can work on live data without falling over each other.”
Previously, the team had issues taking the supplier’s Catia models of the Glider and then having to translate them into Solidworks. Along the way, they would sometimes lose some details.
Now that they have moved to native Catia imports, Engelbrecht says, it’s easier to perform high-level investigations of changes to future Glider designs, or changes to systems, and explore what the design team can do going forward in terms of maintaining fast development times.
There is still a large element of physical prototyping, mostly to quality-assure OEM parts against CAD models and to ensure that all the necessary systems and components fit into place.
“Our first step usually is to 3D print a bracket to mount something in place,” says Engelbrecht. “I think something that’s really helped us in our industry, being able to turn things around quickly using onsite 3D printers and not having to wait for a supplier.” Five small desktop units have been replaced with a Stratasys F170 FDM system, or “one big, proper printer to do the job”, laughs Engelbrecht.
His advice to other companies? “Get something proper that works every time. You can’t have something that requires someone to re-engineer the thing every five minutes.”
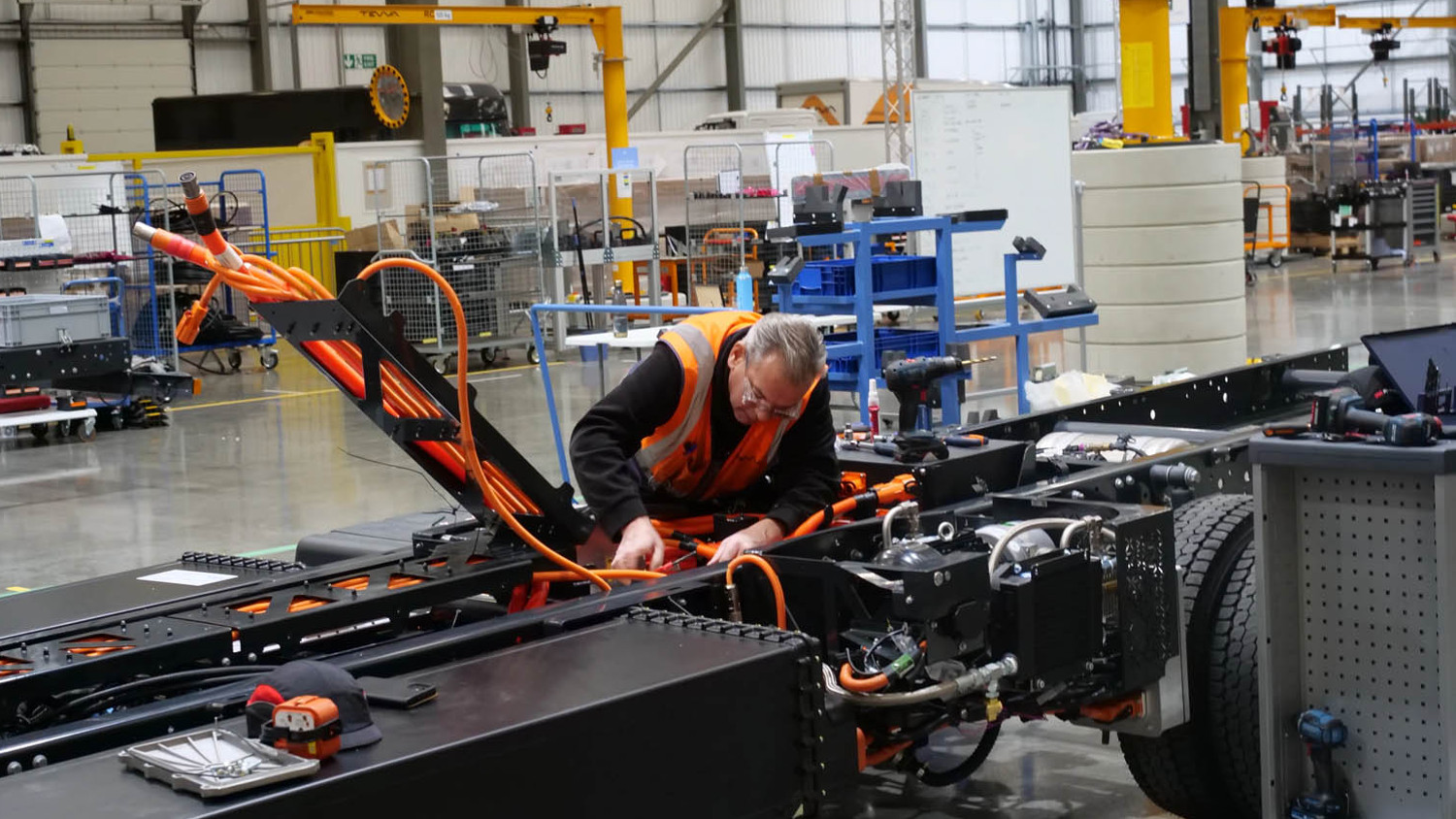
Like the wind
Upgrading the Glider for EV meant the need for further aerodynamic surfaces, where these could be added. Engelbrecht explains that the elements that the team have changed do make a difference, but the team’s members also had to be careful not to make more work for themselves and create downstream maintenance headaches.
It’s a case of not changing anything that could make life difficult further down the road, according Engelbrecht. “Door handles are difficult, so don’t go messing with doors and closures! Exterior mirrors are extremely difficult, unless you’re going to replace them with a lowdrag camera,” he says. “But there are things we can do. We can improve how the air wraps around the front. We can improve what happens at the rear.”
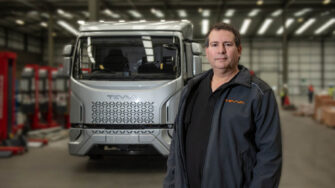
Compared to the passenger vehicles that some members of the team had previously worked on, where floors are nearly always sealed and aerodynamic, freight vehicles have some large surfaces and underside scoops that create drag. “It should have been obvious. It took us sending a few guys to a wind tunnel to go and work out that all we needed to do was add some porosity and a way for the air to get out,” says Engelbrecht.
“It’s a different game to designing for a passenger car,” he adds. “Also, for a passenger car, there’s so much of it that doesn’t actually need to be a good product. You just need to tell a good story and sell it to some customer. It’s more of an emotional purchase than a practical purchase. When it comes to a truck, it needs to do the job on paper, it needs to be good. It’s not an emotional decision.”
Production at Tevva’s headquarters is conservatively ramping up, with staff getting to grips with installing miles of wiring looms, coolant tubes and black-boxed battery housings. Tevva is targeting production of 3,500 trucks each year. With the majority set for UK customers, it will greatly increase the number of EV goods vehicles on the road.
From there, production will continue to scale, the company hopes. And it will optimise both its product and its manufacturing process as it goes, with manufacturing sites set to open closer to other target markets. It’s an exciting time for EVs overall. As more of Tevva’s vehicles take to the road, there’s every chance that trucks running on renewables will deliver the biggest impact of all.
This article first appeared in DEVELOP3D Magazine
DEVELOP3D is a publication dedicated to product design + development, from concept to manufacture and the technologies behind it all.
To receive the physical publication or digital issue free, as well as exclusive news and offers, subscribe to DEVELOP3D Magazine here