Dassault Systèmes is betting big on its 3DExperience Platform. With AI and other new technologies only being developed for the platform, could this mean traditional desktop Solidworks users are about to get left behind? Greg Corke reports
Like its competitors, the long-term strategy for Dassault Systèmes Solidworks is to move its customers to the cloud – the multi-app 3DExperience Platform.
Launched 12 years ago to provide Dassault users with easy access to a variety of branded applications and services needed for their different workflows, its offering for core Solidworks users has continued to struggle. Browser-based Solidworks xApps have been less than inspirational in enticing users away from their existing, much-loved, desktop software.
However, as Dassault presented at its 3DExperience World user event last month, new AI-enabled features might prove the incentive for designers to move to the cloud.
Over the next few years, if your data isn’t on the 3DExperience Platform you won’t get access to new AI powered capabilities. All of the Solidworks AI developments will be on the platform, including modelling productivity tools, automated drawings, enhanced data management and design assistants that offer real time feedback on performance (simulation) and manufacturability.
The word ‘data’ is key. Customers will still be able to use Solidworks on the desktop for years to come, but to access new AI-powered capabilities, their data can’t be there too.
As Solidworks CEO Manish Kumar explained during his 3DExperience World keynote, Solidworks now has two flavours: ‘with the platform’, referring to the traditional desktop version with data stored in the cloud, or ‘on the platform’ with the browser-based version.
AI: past, present, and future
Dassault Systèmes Solidworks is riding the current wave of excitement around AI, but the company is by no means starting out on its AI journey, having tools that date back several years.
Design Assistant uses AI and machine learning to learn how users work, offering suggestions based on their individual workflows. Tools including ‘Selection Helper’, ‘Mate Helper’, ‘Sketch Helper’ and ‘Smart Mate’ are currently available for the platform-native Solidworks xDesign tool, but will soon make their way into desktop Solidworks, as Kumar told DEVELOP3D.
“We are starting to use the same algorithms that were developed for [xApps] in order to put it back into Solidworks with the platform, so now Mate [Helper] is almost there, Selection [Helper] we’ll do the same, Sketch [Helper] we’ll do the same, but unless your data is on the platform, we can’t do anything.
“Think of it this way: All these AI models that we build, it takes some input in order to learn, or you provide some data in order for it to learn. The output can be given to anyone, whether it’s our xApps, our Solidworks, or even Catia for that matter,” he said.
During his keynote, Kumar showed an AI ‘self-driving’ mode for both desktop Solidworks and xDesign that predicts which commands a designer may want to use next. “Our intention is to make it irresistible and a very smooth design experience for you,” he said. “You are always in full control, by the way, and you can use your regular commands anytime you like.”
He followed with a new AI driven ‘image to sketch’ capability that can automatically trace a sketch on top of a picture to use as the basis for a new 3D model.
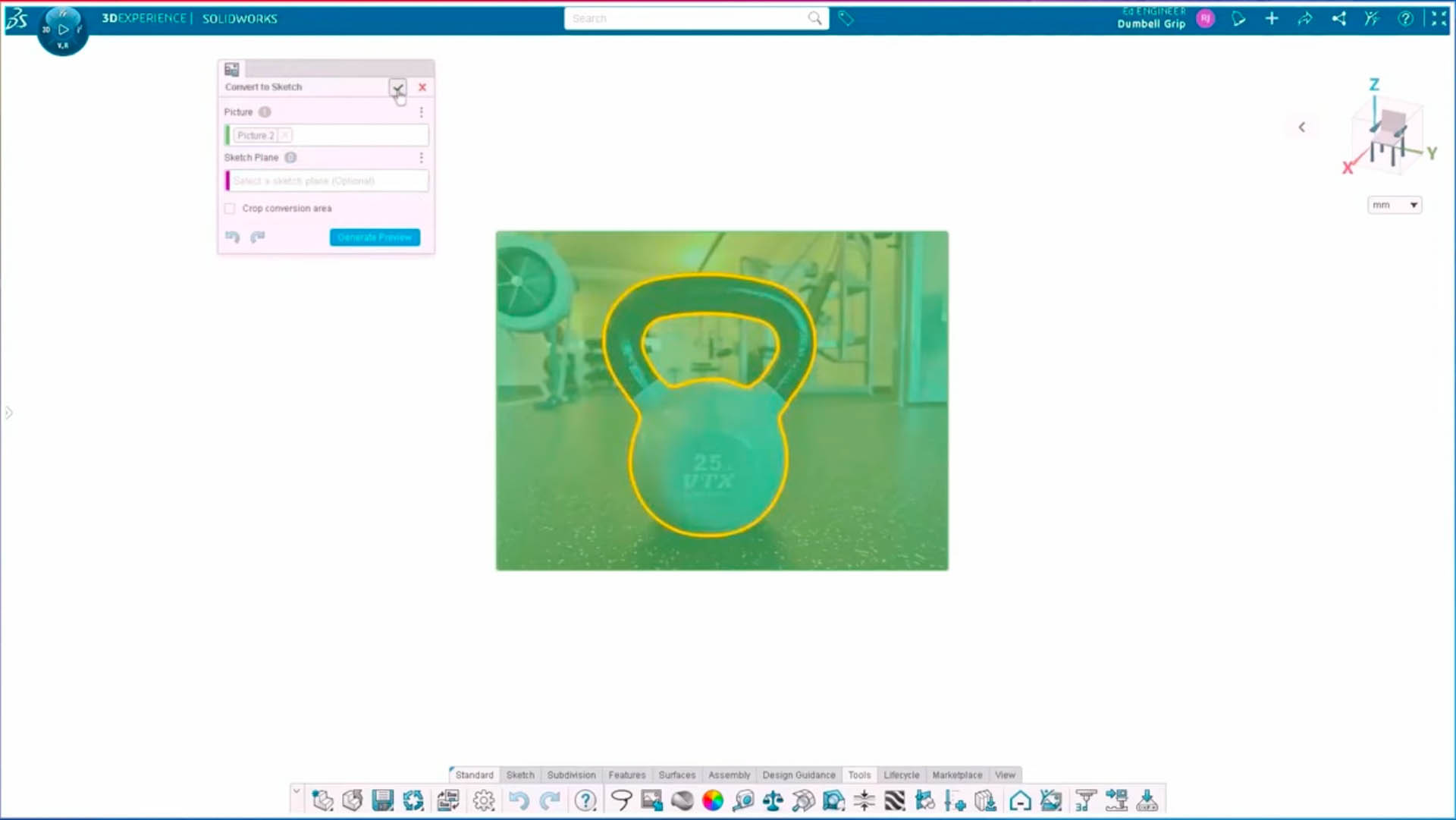
Solidworks is also working on a new tool designed to turn third party data into parametric models. “You give me a model from any system, whether it is a point cloud, whether it is solid geometry coming from some other CAD system or neutral file format, we want to give the parametric feature for that particular model using AI,” Kumar told DEVELOP3D. “Why is it important? Because once it is parametric, you will be able to make modifications there.”
AI is also being used to accelerate more mundane processes. While it’s easy to generate 2D views from 3D models, creating final drawings takes a huge amount of time. As a result, the company is looking to introduce automated drawings to Solidworks by the end of the year.
During his keynote, Kumar showed the technology working on both desktop Solidworks and xApps, via the platform. “Drawings are driven by standards and well understood manufacturing needs,” he said. “Using this open available information, we are working to provide you with AI-driven generative drawings. But of course you can go back to this drawing and make any manual modifications that you may want. It will help you save precious time, but you will still be the final authority.”
All the technologies mentioned above could have a positive impact on the day-to-day productivity of all designers and engineers. However, Kumar admits that Solidworks can sometimes be too focused on design, or drawings, or selection etc. Moving forward, there’s huge potential to harness AI to make simulation and manufacturing a much more integrated part of the design process.
Kumar described a common iterative workflow, where simulation and manufacturing are typically used at the tail end of design and any identified issues often result in a lengthy cycle of design changes.
“It is a no brainer that if a problem is identified at the design time, it’s the cheapest for the manufacturer. If it is identified here, it is also the most environmentally friendly because you are trying to reduce the waste,” he said.
He referenced ‘left shift’, where companies want to capture all the problems as soon as possible. “If you’re trying to shift left, AI is not just about design,” he said. “Rather, when I design something, if it is going to cause a problem in downstream operation, can I also predict that? We can if these sequences of things are happening on the platform.
“We are not just looking at AI from a design centric [point of view] in a confined space. We are looking at it from a holistic point of view that how can we help our clients become more business centric, be more profitable, reduce time to market, be more sustainable for that matter?”
In other words, design becomes less about design-test-iterate loops, and more about giving real time feedback on performance and manufacturability from the very early stages.
Of course, Solidworks CAD is just the beginning. Once data is in the platform it can also link into downstream manufacturing processes, as Kumar explained. “You can create manufacturing bill of materials, you can link it to ERP Delmiaworks, where every single step of how this manufacturing BOM was converted into what series of manufacturing steps operations were performed on it.
“If we know all that, we have a lot of data for a given company that when you get something like ‘this’, ‘these’ are the operations you perform. We should be able to tell you that when you come up with something new, maybe there is an alternative design. Or certainly there is an alternative series of processes that you can perform.
“At times it might also happen that it suggests a longer manufacturing process to reduce the overall time to market or to make it more efficient, which a normal human being will not think about.”
According to Kumar all of this is achievable in the next five years. Longer term, he sees an increased role for virtual twins as part of a broader Dassault Systèmes play where the company helps its clients build virtual twins of real objects covering everything from design and manufacturing all the way to shipping.
“We also want to go in the users’ aspects of it, in the sense if you try to use these things in real life, what is the data being produced and can we use that data in order to improve it further?” he said. “The next step is can these virtual twins live without any context?”
Kumar gave the simple example of a loudspeaker. “It needs to have a context, because how is that speaker going to operate in a room like this, versus outside?” he said.
On a larger scale, he referenced a building, pointing out that a single virtual twin is never enough. You need to put it in the context of a city. What will its relationship be with other buildings in terms of shadows cast and air flow? What impact will it have on transport, on water supply etc? The answer, he believes, is multiple virtual twins connected through some kind of relationship.
“Then you need to simulate on a much larger scale, in order to come up with solutions that you will never be able to do based on just a study of one virtual twin.
“This is where we want to go, where we want to think in a holistic way. And if you want to think in that holistic way, no way anyone will be able to do anything if they are just bound to a desktop kind of environment. Embrace the platform, because we want to go there. Big Data, consolidated, that’s the way to go.”
Protecting IP
With industry wide concerns about the impact of AI on Intellectual Property (IP), Solidworks has been very clear that customers’ IP will be protected. “We will never give the IP of one company, by extracting the knowledge and know-how, to someone else,” said Kumar.
“We have a very clear barrier between IP and knowledge,” said Gian Paulo Bassi, executive vice president, 3DExperience Works. “We want to create models that represent knowledge in the field of manufacturing, but what is important is the technology behind the creation of those models. But how these models are then built, then populated, so to speak, that is on your own data.”
Bassi sees that AI could present an opportunity for manufacturing firms to share IP, in a similar way to how big pharmaceutical companies are working together. He gave an example in the aerospace industry, “What if Company A has a specific knowledge on a certain type of composites, and they want to expand into another type of composites?” he said. “So, maybe Company B has knowledge on aluminium fabrication, and in exchange they get knowledge and know how on composite fabrication. There is a mutual advantage.”
Breaking down barriers to simulation
Simulation forms a critical part of many product development processes, but it remains massively underutilised by designers. Kumar said that he wants to bring simulation to every Solidworks user, but there are two major barriers to adoption.
The first is fear, he said, a sense that simulation is something which is only done by analysts. Solidworks Simulation has done a good job of addressing the needs of designers, by putting easy to use tools inside the Solidworks environment, but he admitted that simulation still needs to be taken one level further down. “We want to make it approachable to an extent where even kids should be able to use it, without thinking about it, without getting scared of it,” he said.
According to Kumar, the key to this is making simulation studies much easier to define. “We need to convert simulation speak into something which is a layman speak,” he said.
“Rather than saying ‘how many newtons do you want to apply?’, you change the language to something like ‘are you trying to press it with a thumb, are you trying to press it with a palm, are you trying to stand on it, or is there an elephant standing on it?’. If you try to speak in those terms, anyone can get it. Even a kid will get it.”
The second barrier is a lack of available hardware. Kumar said that while an iPad can be used for design, using xApps, it is not powerful enough to run simulation. Today, you still need a high-end laptop or high-end computer. But that is changing, he said.
Kumar described having a simple simulation environment on the iPad, where all the processing is done in the cloud using a credit system. “If it is so cheap [and simple to use] that anyone can start to leverage it, I think we will break those two barriers.”
MCAD meets ECAD
For electromechanical design, mechanical engineers using Solidworks have historically collaborated with electrical engineers by transferring files to tools like Altium Designer, or any other electrical or PCB design software that supports the IDX file format.
Last month Dassault Systèmes and Cadence announced a partnership designed to provide a much tighter integration between MCAD (Solidworks) and ECAD (Cadence OrCAD-X or Cadence Allegro-X).
The big difference with this new approach is that it’s a platform-to-platform integration, between the 3DExperience platform and the Cadence Allegro platform.
Push a button in Solidworks and all the data gets passed through the 3DExperience Platform, automatically notifying the designer using OrCAD or Allegro. They then get to approve or reject any changes, and this works bi-directionally.
According to Kumar, this approach provides a single source of truth, with full traceability of what was changed, why it was changed, who changed it and more.
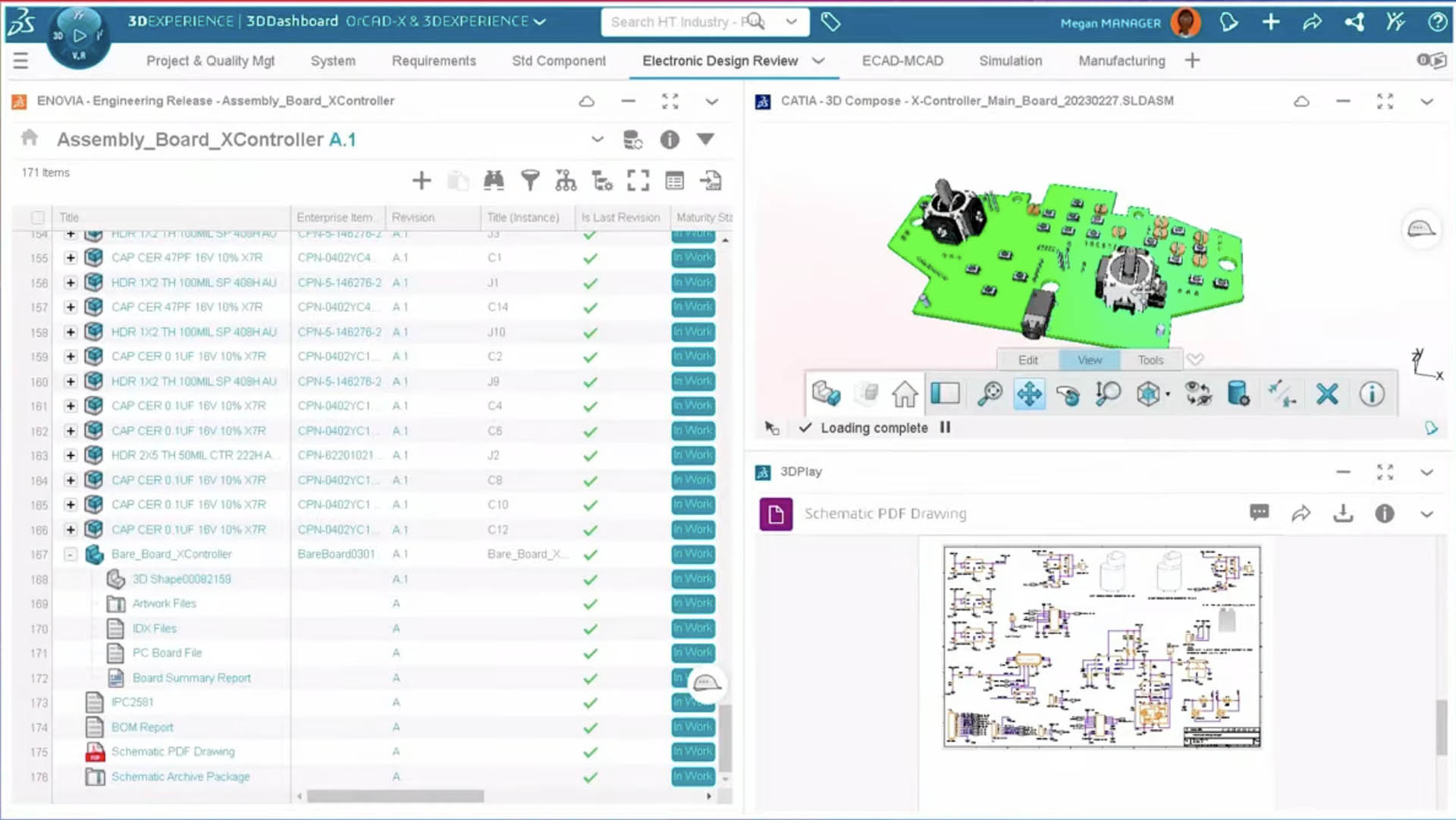
The cloud carrot
With Solidworks 2024 every new seat purchased comes with cloud services, which is essentially a collection of 3DExperience platform workflows ranging from simple share and markup to full on data management.
Users can dip their toes in as-and-when they are ready. “Nothing’s being thrust on our customers, they can do anything they want with our tools,” emphasised Mark Peterson, senior industry process consultant at Dassault Systèmes.
There are three levels of engagement with cloud services, which Dassault defines as ‘Share and Markup’, ‘Store and Revise’, and ‘Manage and Control’.
Share and Markup allows you to share a file internally or with a manufacturing partner for markup. From within Solidworks, users click the share button, punch in an email, and the file is then stored in a secure share location on the 3DExperience Platform for the third party to access, view and markup. Once done, feedback is seen directly inside Solidworks through the task pane.
“One of the things I really love about share markup is that you still maintain control of that intellectual property, which is something that has always been challenging for a lot of our clients, because if you email somebody a Solidworks file, they have your data, they have your feature tree, they have your exact dimensions,” said Peterson.
‘Store and revise’ allows customers to store their data on the 3DExperience platform. This can then be accessed from anywhere, on any device, and augmented with simple data management tools like Revision Management.
‘Manage and control’ offers much more comprehensive data management on the platform, although this requires some handholding. “We have tools that we use to migrate our users from any PDM system to 3DExperience Solidworks or platform,” said Peterson.
The platform future
It appears that Dassault Systèmes Solidworks will be channelling most of its development resources into its 3DExperience platform over the next few years. And if you don’t get on board, you won’t get access to the most advanced new features, potentially optimising everything from modelling and drawings, to simulation, manufacturing, and electromechanical design.
The challenge for the company is how to encourage customers to make the move. One thing seems clear: it’s not going to force them. Desktop Solidworks with local data is going nowhere fast.
Instead, Solidworks looks set to dangle a series of increasingly large carrots – if ‘Share and Markup’ is your snack-sized Chantenay, AI could be your farmer’s prize-winning goliath.
Of course, it’s still very early days for AI at Solidworks and MCAD in general, and it remains to be seen how new features will appeal to the average Solidworks user. While upfront simulation and manufacturing might not be for everyone, it’s hard to imagine that even the least progressive firms won’t perceive real value in automating drawings.
There’s also the question of cost, both in terms of software licensing and cloud processing. Solidworks appears to be taking a similar token-based approach to Autodesk, where Fusion customers pay for computational services including generative design, simulation and rendering.
Perhaps the most interesting point about Solidworks and AI is that all of this could be happening in the next five years. Solidworks is one of the most loved CAD tools out there, but it could be about to experience its biggest change in its quarter-century history. The question is: who will come along for the ride?
Tech from the show floor – 3DExperience World
Some of the tech highlights from the show floor at the recent Solidworks conference, 3DExperience World.
Driveworks
Driveworks was showing its latest online configurators that can be embedded in a website, so customers can configure and order personalised products.
The customer gets an instant quote and essentially does all the work for a process that, when done manually in the traditional way, can be error prone and take hours.
The company highlighted a new configurator aimed at the Australian market, for companies that customise utility vehicles (utes, for short). Customers can choose different canopies, trays, sideboards and more. If a folding ladder is selected, mounting brackets are automatically added.
Customers get real time pricing and a nicely rendered interactive 3D model of their specific configuration. The system then automatically generates quote documents, and all the manufacturing data.
Designs can also be viewed in AR in any environment using an iPad. The system generates a QR code, which you simply snap with the camera.
Seeing a ‘ute’ in the context of the exhibition show floor might not be the best use of this technology, but picture a conveyor system in a factory or a consumer product in the environment in which it will be used, and you start to imagine the potential.
Driveworks has built a tonne of sample configurators for various products including agricultural trailers, scissor lifts, industrial emergency showers, and folding doors.
The UK firm also offers DriveWorks Pro to build your own Solidworks automation and online 3D product configurator solutions and DirectWorks Solo for part, assembly, and drawing automation inside Solidworks.
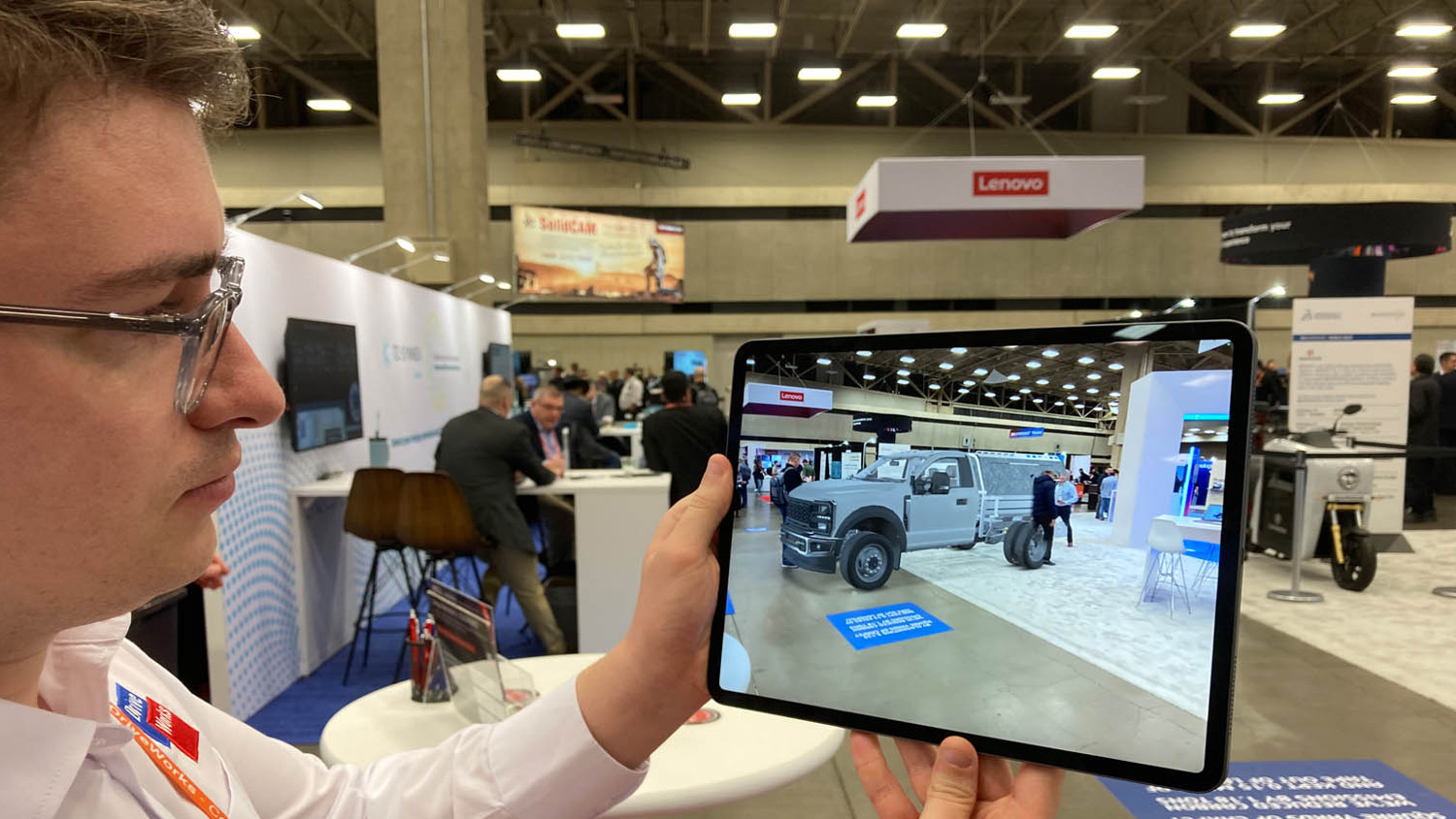
Elysium
Elysium, a specialist in 3D data interoperability, showcased two main products: 3DxSuite and CADfeature.
3DxSuite handles data conversion and model-based definition, such as creating technical data packages or derivatives that need Product Manufacturing Information (PMI) within them.
At 3DExperience World the company demonstrated several new features including an HTML Exporter for Technical Data Packages, so TDPs can be created and published in HTML as well as 3D PDF. The company also showed a prototype of a new PMI Checker designed to prevent the publication of incomplete PMI through ‘comprehensive verification’.
CADfeature is a migration platform for companies that are looking to consolidate CAD systems or to move off a legacy system. Elysium told DEVELOP3D that in recent years there has been an increase in demand for migrating to Solidworks.
Importantly, the software allows firms to preserve the feature history tree, assembly relationships, and associative drawings, as well as nongraphic model properties such as attributes and metadata. Of course, no two CAD system are identical, and Elysium admits that while some CAD models may come over 100% feature-based, others may not, such as those with certain surfaces. In such cases, the company explains that the software has a fallback method where geometry is preserved but some of the features may be supressed.
CADfeature can also be set up for automated batch processing, where jobs can be scheduled to periodically perform a variety of different translation types.
The software supports a wide range of CAD tools including Siemens Solid Edge, Siemens NX, Autodesk Inventor, PTC Creo, and DS Catia – and of course DS Solidworks and the 3D Experience Platform.
Eagle Point Software
Eagle Point is well known to DEVELOP3D’s sister publication, AEC Magazine, for its architectural, engineering and construction focused learning tools, but we didn’t know that the company also has a focus on product design and manufacturing. Over the last couple of years, the company has been developing a range of Solidworks content for its ‘Pinnacle Series’, focusing on everything from basic modelling to more complex workflows such as simulation (which launched at 3DExperience World).
The Pinnacle Series has both e-learning and learning management system (LMS) components for tracking workforce, identifying skills gaps, collaborating and sharing organisational information.
HCL CAMworks
HCL CAMworks develops a range of Solidworks-integrated CAM software, covering everything from 2D, 2.5-axis, 3-axis and 5-axis to mill turn, wire EDM and others. It includes Solidworks CAM, which comes with a Solidworks subscription, plus a range of CAMworks modules for more advanced features.
According to the company, one of the foundations to its software is the Technology Database (TechDB). This provides ‘intelligence’ for ‘knowledge-based’ machining strategies, allowing companies to ‘automatically generate’ toolpaths. In essence, once a part has been programmed, those algorithms and information can be saved to a company’s TechDB, so they can be used again – a huge time saver.
At 3DExperience World the company launched CAMWorks 2024, and was demonstrating several new features. One of the highlights is Machine Aware Programming which allows users to include a ‘digital twin’ of a CNC machine directly inside Solidworks. According to the company, this ensures the digital model mirrors the physical machine’s capabilities for more precise and dependable programming.
CAMWorks 2024 also includes a new UI enhancement – hover a mouse cursor over a feature in the model, and the operations that are being used to machine that feature will pop up.
The new release also introduces an array of multi-axis toolpaths for both rough milling and finishing. 5-axis machining was supported in previous versions of the software, but the roughing and finishing routines are now more automated.
SolidCAM
SolidCAM offers a huge range of Solidworks-integrated CAM software but the company used 3D Experience World to primarily showcase its advanced mill turn and Swiss turning capabilities. These have been ‘significantly enhanced’ in the last couple of versions with what SolidCAM describes as ‘drag and drop’, ‘plug and play’ functionality, plus improvements to make the software more visual and easier to use.
The company also gave a live demonstration of a tool cutting precipitation hardening stainless steel using its patented iMachining high speed milling technology.
iMachining is designed to create faster and safer CNC programs to machine mechanical parts, while maximising tool life. The amazing thing about the demonstration is that the steel and the tool didn’t even get hot. According to SolidCAM, this is all down to iMachining’s algorithms which help maintain an extremely constant chip size, resulting in a constant load on the part, the tool and the machine. A SolidCAM spokesperson explained that there’s no linear force against the tool, only rotary force, and all the heat comes out with the chip.
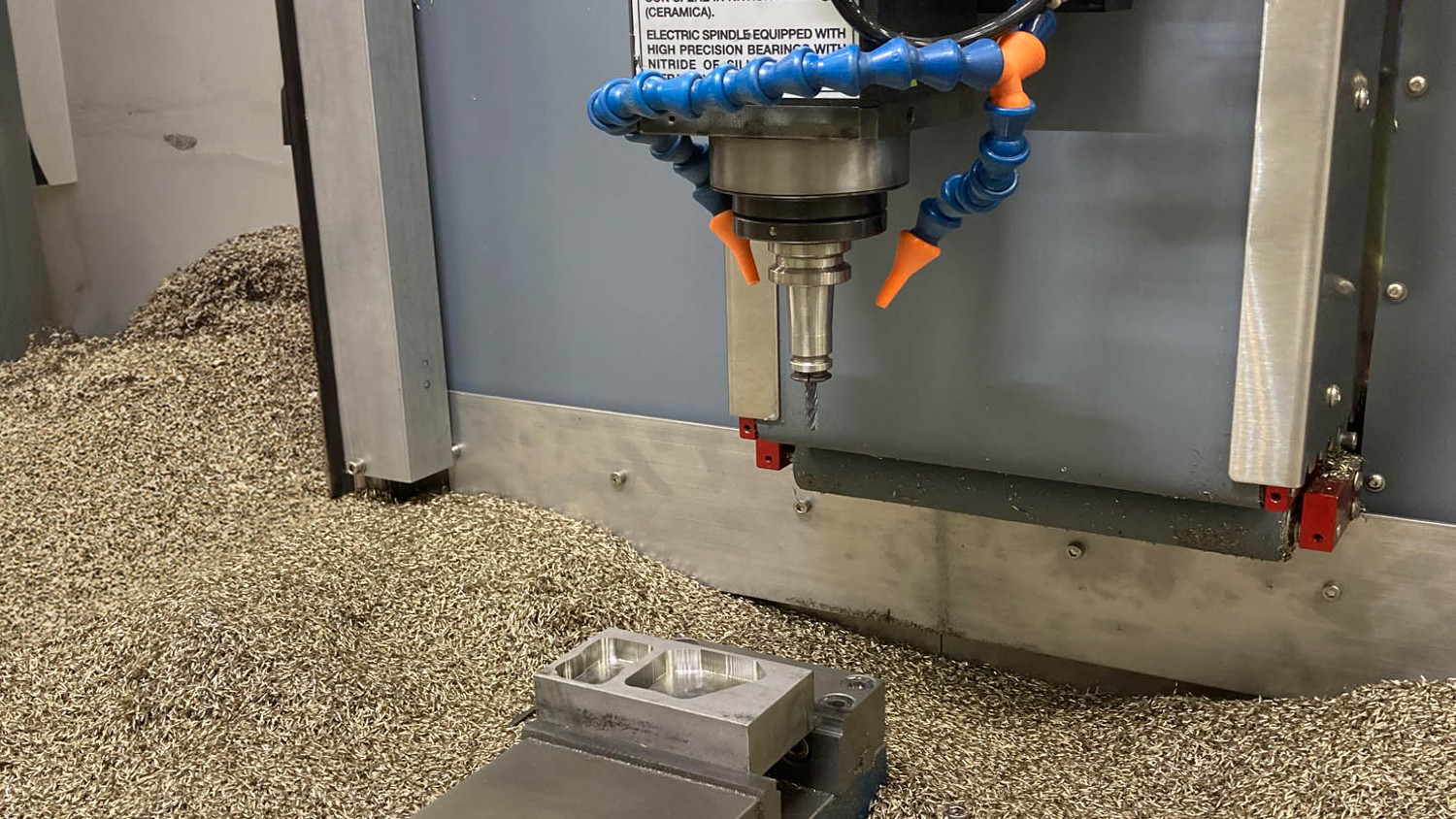
Workstation technology
3DExperience World was a natural hotbed for workstation tech, with plenty of standout products for Solidworks users.
HP, Dell and Lenovo had a tonne of mobile workstations on show, but it was the HP ZBook Firefly G10 A and Lenovo ThinkPad P14s mobile workstation that stood out for us. Both pro laptops have a compact 14-inch form factor, so are highly portable and energy efficient, but also deliver plenty of performance for most Solidworks workflows. The interesting thing about these machines is that, instead of having an Intel processor and separate Nvidia GPU, they are powered by an AMD Ryzen processor with a GPU built in.
Nvidia used 3DExperience World to launch the Nvidia RTX 2000 Ada Generation, a low-profile graphics card designed for small form factor desktop workstations, such as the HP Z2 SFF/Mini and Lenovo ThinkStation P3 Ultra.
It’s an important release for Solidworks users as it hits the price / performance sweet spot for those who want to take their design workflows beyond Solidworks and into the realms of visualisation with tools like Solidworks Visualize and Luxion KeyShot.
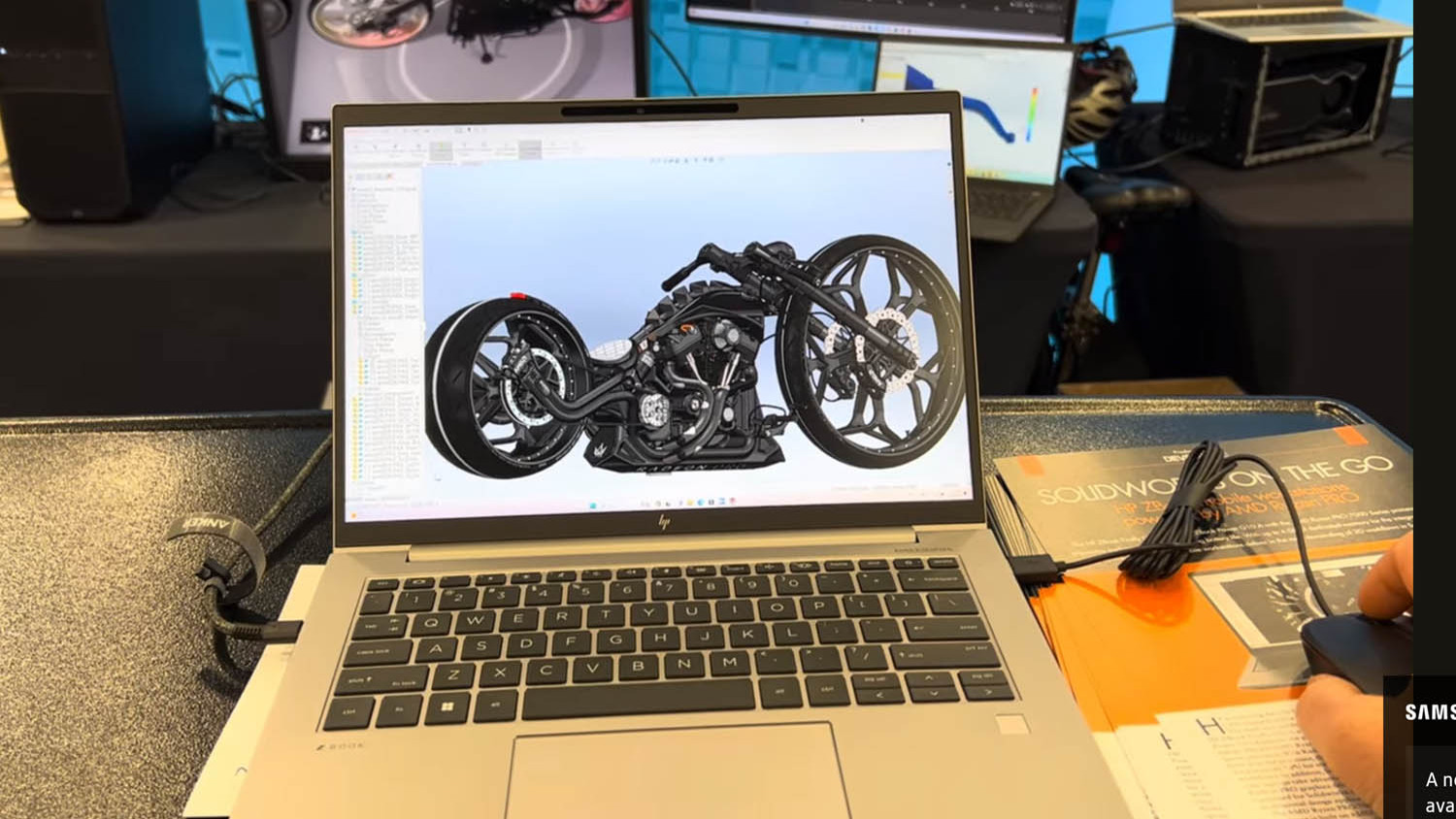
AMD was showcasing its range of AMD Radeon Pro GPUs, along with Dell, HP and Lenovo workstations with AMD Threadripper Pro CPUs with up to 96-cores. Mechanical engineer and product designer Adi Pandzic unveiled his latest creation – a complex motorbike design, modelled in Solidworks and rendered in Solidworks Visualize using an HP Z6 G5 A workstation with AMD Ryzen Threadripper Pro CPU and AMD Radeon Pro W7900 GPU.
Dell gave a soft launch to its new CAD-focused entry-level desktop workstations, the Dell Precision 3280 CFF and Precision 3680 Tower. We refer to this as a soft launch because both machines feature 14th Gen Intel Core processors, which at the time had not been announced. Since then Dell and Intel have released full details, which can be found here.
The show floor also brought up some interesting options for remote workstations. Lenovo showed how it can pack up to seven ThinkStation P3 Ultra workstations in a 5U rack, while HP showed off the latest advancements in its HP Anyware remoting software, demonstrating how a powerful desktop workstation can be accessed remotely from a standard laptop.
Sony offered a visual attraction, showcasing its Sony ELF-SR1 Spatial Reality Display which gives the illusion of viewing a model in true 3D without the need for glasses. The device consists of a 15.6” 4K LCD panel which shows independent left- and right-eye images, which are directed to each eye via micro-optical lens. With built in eye tracking, the display adjusts the view as you move your head, so you can explore the 3D model from any angle. The results are very impressive.
The initial focus for Sony was on DCC and game developers, with SDKs for Unity and Unreal Engine, plug-ins for ZBrush, 3ds Max and Maya, but the company is now turning its attention to CAD.
The idea is that you’d use a 2D display for modelling and the 3D display to get inside your design. Considering Sony was exhibiting at 3DExperience World, it wouldn’t take a genius to work out that it has something in the pipeline for Solidworks users. Beyond direct support, the monitor should work with any tool that supports openXR. There’s also a file viewer for OBJ, STL and glTF.
Finally, 3DConnexion was showing how its range of 3D mice can be used to improve model navigation in Solidworks, from the portable SpaceMouse Compact to the cable free SpaceMouse Pro Wireless Bluetooth Edition with plenty of configurable buttons.