The engineering team at OX Delivers has hit the bullseye with an electric vehicle designed for use in developing nations. A ‘fail fast’, iterative prototyping approach to design has kept its mission to build the ‘Uber for potatoes’ charging forwards, as Stephen Holmes reports
Getting crops to market in Rwanda can be a real struggle for the nation’s farmers. The terrain may be fertile in this small, landlocked country in the Great Rift Valley of Central Africa, but it’s not known as the ‘land of a thousand hills’ for no reason. To add to the transportation challenges associated with steep gradients, fewer than 20% of the country’s roads are paved, and severe flooding and landslides during the country’s biannual rainy seasons frequently join the list of obstacles that motorised transport must navigate.
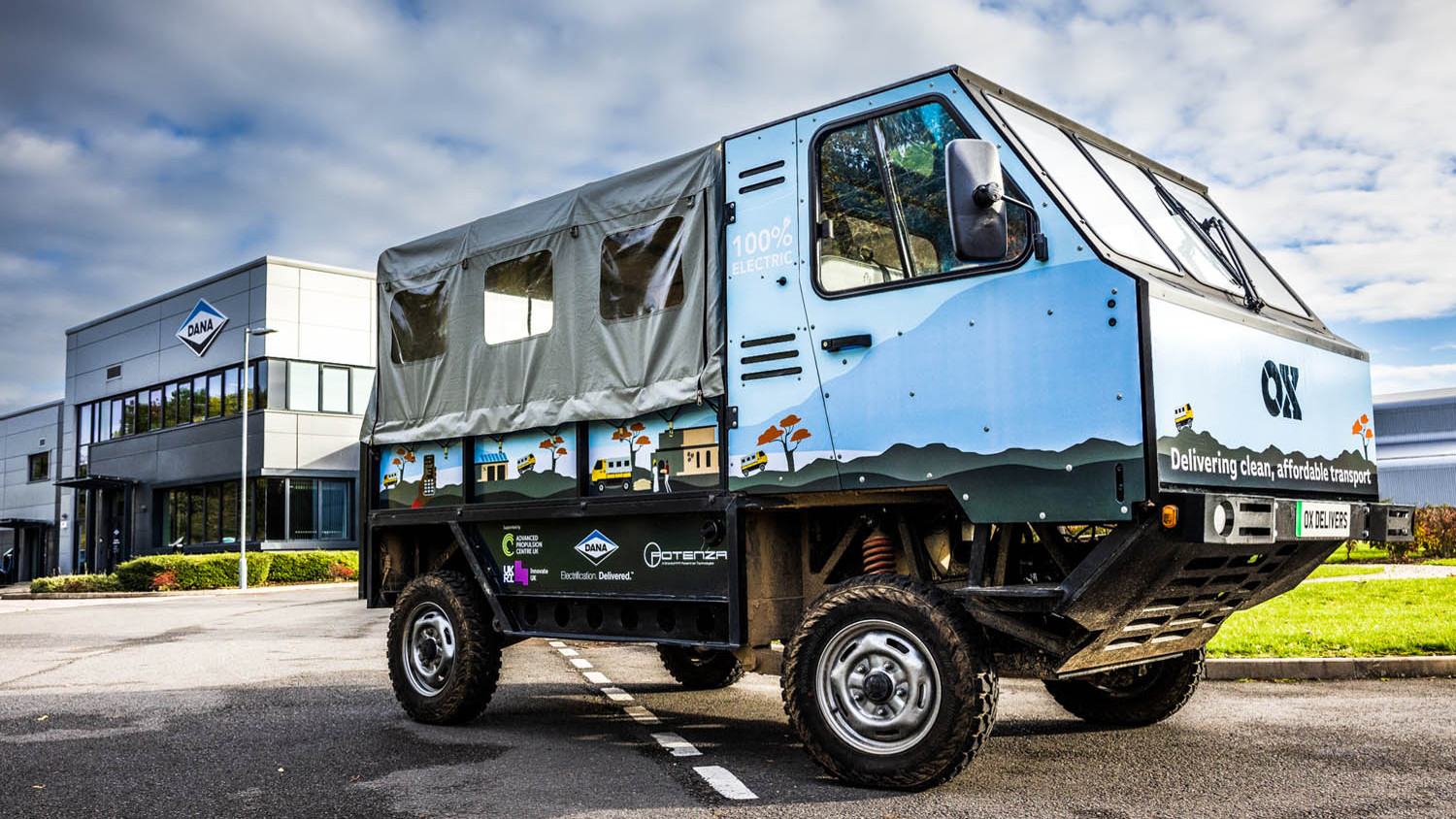
As Kristiana Hamilton, a member of the 14-strong design and engineering team at OX Delivers cheerfully puts it: “The Rwandan roads are considerably worse than I think was originally anticipated!”
The thinking behind OX Delivers dates back to 2013, when philanthropist Sir Torquil Norman and the Global Vehicle Trust (GVT) charity got together to focus on building reliable goods transportation specifically designed for the African continent.
End-of-life trucks from other regions of the world are frequently imported to Africa, but with age-related wear and the rough terrain they are forced to negotiate, these quickly become too expensive for users in local markets to fuel and maintain. Alternatives include using bicycles, people or animals to move goods – all too slow and restricted in the loads they can manage to build prosperous businesses. And thus the problems of low incomes, inefficient value chains and food waste continue.
GVT’s response was to commission acclaimed South African-British automotive designer Sir Gordon Murray to create the original OX truck, and four diesel prototypes were built as innovative flat-pack products made of engineered laminated panels bonded to steel frames.
Later, in 2020, OX Delivers was established to create a scalable business model that would support the transition of the OX truck into an electric vehicle (EV) for emerging markets. This design overhaul was backed by funding from US AID, Innovate UK, and the Advanced Propulsion Centre among others.
The idea here is that farmers should be able to rent space on an OX truck to take their goods to market – or as the OX Delivers team like to refer to it: ‘an Uber for potatoes’.
A pilot scheme is now running in Rwanda, chosen for its centrality and its abundance of small businesses, as well its credentials as a forward-thinking country that appreciates technology. It also has a relatively good electricity network fed by renewables (mostly hydropower and solar) – a necessity for any EV company.
OX Delivers // Challenging terrain
Just as roads to Rwandan farms are seldom paved, the path to market for the OX design hasn’t been the smoothest journey, either. Far from a straightforward swap-out to an electric powertrain, much of Murray’s original design had to be redeveloped.
OX 1, a full EV conversion from one of the original diesel trucks, was shipped to Rwanda for in-market testing and feedback, only to find on arrival that the central driving position that Gordon Murray is known for in his supercar designs isn’t permitted on the country’s roads.
“It had to be converted at the port from central drive to left-hand drive, so that we could actually have the vehicle in the market to test,” says Hamilton, running through a list of changes that the team has had to assess, redesign and move forward on. The original bench seat gave drivers no support on the rough roads, and its lack of adjustment made the ride deeply uncomfortable. “The Rwandan population overall is relatively short in stature, so if you can’t move that forward, you’ve got no support on your back and you’re sitting right at the step. So all of that changed,” she says.
For a vehicle destined to be carrying heavy loads in challenging conditions, there was a lot to consider when overhauling the original design. Despite this, the transformation has happened quickly, with the OX team set up to ‘fail fast’. In other words, it has worked iteratively, identifying what won’t work, analysing what might work better, and then testing and repeating until the design is perfected.
Hamilton explains that at the start of 2022, the team combined to look at the main issues, feedbacks and to define what needed to be core to the OX Truck. “We laid all that out – predominantly stuff like progress on the roads, a decent set of suspension, all these things – and we could filter [the team] out into different sections.”
Having split into pairs of engineers and brainstormed ideas, the team then reunited to plot the best path forward for each section and for the vehicle as a whole.
We know it’s going to be durable and it’s made of materials that are available in the market, which is one of the big issues Kristiana Hamilton, Engineer
The original chassis was relatively robust, but after running tests on the ground in Rwanda, the engineering team quickly spotted some issues, particularly with cracks. The chassis, notes Hamilton, was also not made in a way that makes it easy to repair. This has big implications for the OX Delivers business model, since it will be running the trucks itself, rather than selling them to third parties. Truck uptime is critical.
“We’re currently going through an iteration of the chassis and we’re gradually redesigning the whole thing so it fits better for our market and can be easily repaired,” she says. “We know it’s going to be durable and it’s made of materials that are available in this market, which is one of the big issues.”
Meanwhile, the original steel box section design works well – until you need to make repairs in a market where you can only buy bent sheets, which makes it difficult to make a full box section and have it be as strong as it needs to be.
“We work in an agile environment, where we work in two-week sprints. And, if we find something during that sprint, then we can go, ‘Actually, this isn’t going to work out’ and it makes it really easy for us to change direction,” she says. “We try to be as fluid as possible.”
With this design approach being guided by data fed back from the OX team running vehicles in Rwanda, the unloved original cab has been redesigned. An electronic drive unit (EDU) has been developed with EV experts Dana and the vehicle architecture has switched from ineffective front-wheel drive to more powerful rear-wheel drive with the option to adapt to all-wheel drive to deal with the harsh terrain.
The powertrain team has devised new brackets to hold the revised EDU, quickly working through ideas in Onshape, testing them through Onshape Simulation and iterating them several times before having physical prototypes made.
“We’re trying to move as quickly as possible, and our agile framework allows for that,” says Hamilton.
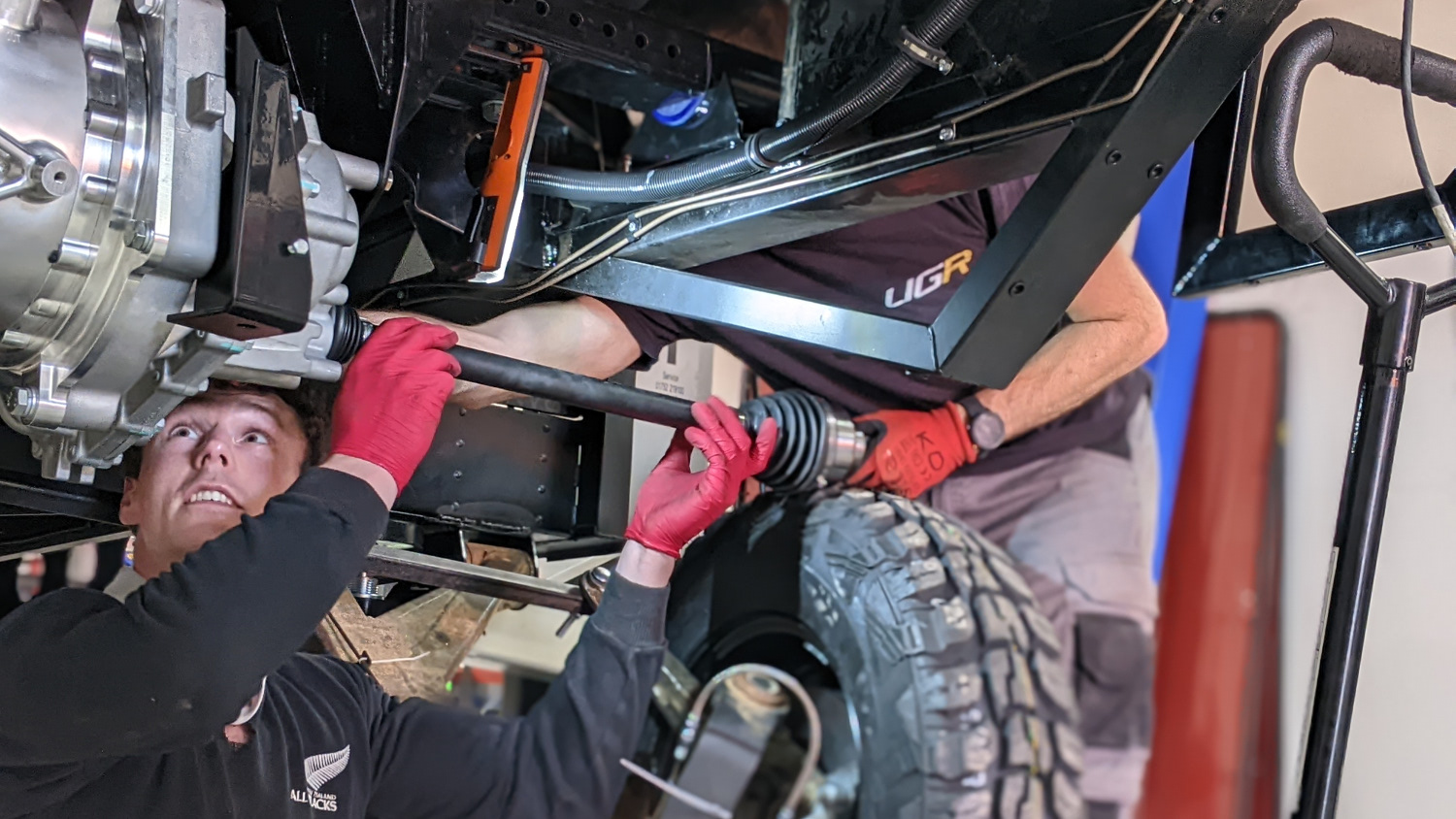
OX Delivers // Always moving
The fluidity of the team within OX Delivers means that the design team is constantly lending its expertise across multiple sections of the truck development. Hamilton explains that she’s recently worked on suspension, steering and chassis, and will be moving into cab improvement at some point in the near future.
As a startup, we can’t really afford to have servers that hold all of our data, and Onshape was super easy to access for us. It’s incredibly intuitive and that’s been one of the biggest wins
Since everyone needs access to the latest versions of CAD data, using cloud-based Onshape made perfect sense. “As a start-up, we can’t really afford to have servers that hold all of our data,” says Hamilton, “and Onshape was super easy to access for us.”
She also praises Onshape for its ease of use. “It’s incredibly intuitive and I think that’s been one of the biggest wins for us. We have a variety of engineers, with a variety of different skill sets, but a lot of people are expected to use CAD.”
Take, for example, one team member in particular, a suspension expert who works in kinematics. “He worked out how to do that in Onshape, which was fabulous and it looks great. It really helped us not just with understanding our suspension, but also understanding our packages, how we need to design things. He was never fully confident in CAD, in terms of modelling, but he’s been able [to work in Onshape] because it’s so easy to just pick it up and do it,” says Hamilton.
The customer service offered by Onshape is “incredible”, she adds. “If there’s anything that’s a problem with the software or that we’re struggling to do, they’re really supportive. We have direct contact with them.”
Also proving its worth in Onshape are its custom features. These are created by the wider Onshape community in the native Onshape code, giving the OX team a way to easily find feature scripts and tools to tackle challenges for which the software might not have an immediate answer.
“We’ve started to use this a lot more recently,” she says. “Even if Onshape doesn’t have the [desired] functionality within the base software, you can find it elsewhere. It’s been really interesting lately, working out how best to utilise that software and the different tools that we can find.”
Ox works closely with partners, including transport OEMs Dana, Penso and Potenza. These organisations help iterate on the truck design with the latest CAD data and even test some prototype units and systems on the physical OX test units.
Both sides want to work with the latest CAD data as much as possible, although the major OEMs tend to work in Catia or NX, for which typically the OX team rely on importing STEP files into Onshape.
Penso has gone a step further: such is the cost and accessibility of Onshape that it has assigned two of its engineers to model files from their native Catia format directly into Onshape. The Penso team is trained not only in Onshape, but also on how OX manages its CAD structure, making it faster to integrate models regardless of complexity.
The existing truck CAD model is split into cab, base and powertrain, leading off into different subsections within that. However, more recently the team has been looking to alter this to cab, front section, middle section and rear, with powertrain in the middle.
“That allows it to be modular and lets us do that individual testing, because it’s not like a traditional vehicle, where the whole chassis is integrated. You have these split sections that all connect to one another and allow you to do these individual tests on specific areas, rather than having to have a full truck design to be able to do that.”
The team outsources some simulation work to partners and specialists in specific scenarios such as crash testing, but by splitting up the design, it allows these trusted third parties to work quickly on the design.
Online delivery
Working using a cloud-based system means that team members in Rwanda can also access and update the latest data, remaining connected to the process.
One of the UK team members is now based in Rwanda, where he is gathering a lot of design data from the field, from real-time feedback from testing different duty cycles to information on issues spotted during maintenance. He also has access to the full CAD model.
Another key member of the Rwanda team is a designer focused on the goods storage section at the back of the truck. Here, a lot of work is going into ensuring that the rear canopy is the right size and equipped with the right tools for the job, including scales to ensure customers don’t overload the truck.
Designers and engineers from the UK regularly head out to Rwanda in order to get a first-hand feel for the market, conditions and customers, while mechanics from the Rwandan team travel to the UK to undergo the necessary high voltage training needed to maintain EV systems. This back and forth greatly assists both digital and in-person knowledge-sharing.
Once the team has the production model ready, the plan is that regular shipments from the UK will form the basis for flat-pack delivery. So the trucks will be built in the UK and then assembled by the OX team in Rwanda, where thought is already going into sharing assembly training guides that leverage the existing CAD data.
Soon, it is hoped, an entire network of OX Trucks will be successfully transporting produce across the hills of Rwanda, before the company expands its reach across borders into neighbouring countries. At the same time, OX will be raising the prosperity of its users through a fit-for-purpose design that puts EV technology at the heart of improving economies. Not even Rwanda’s two rainy seasons can dampen the exciting promise of a better future for its farmers.
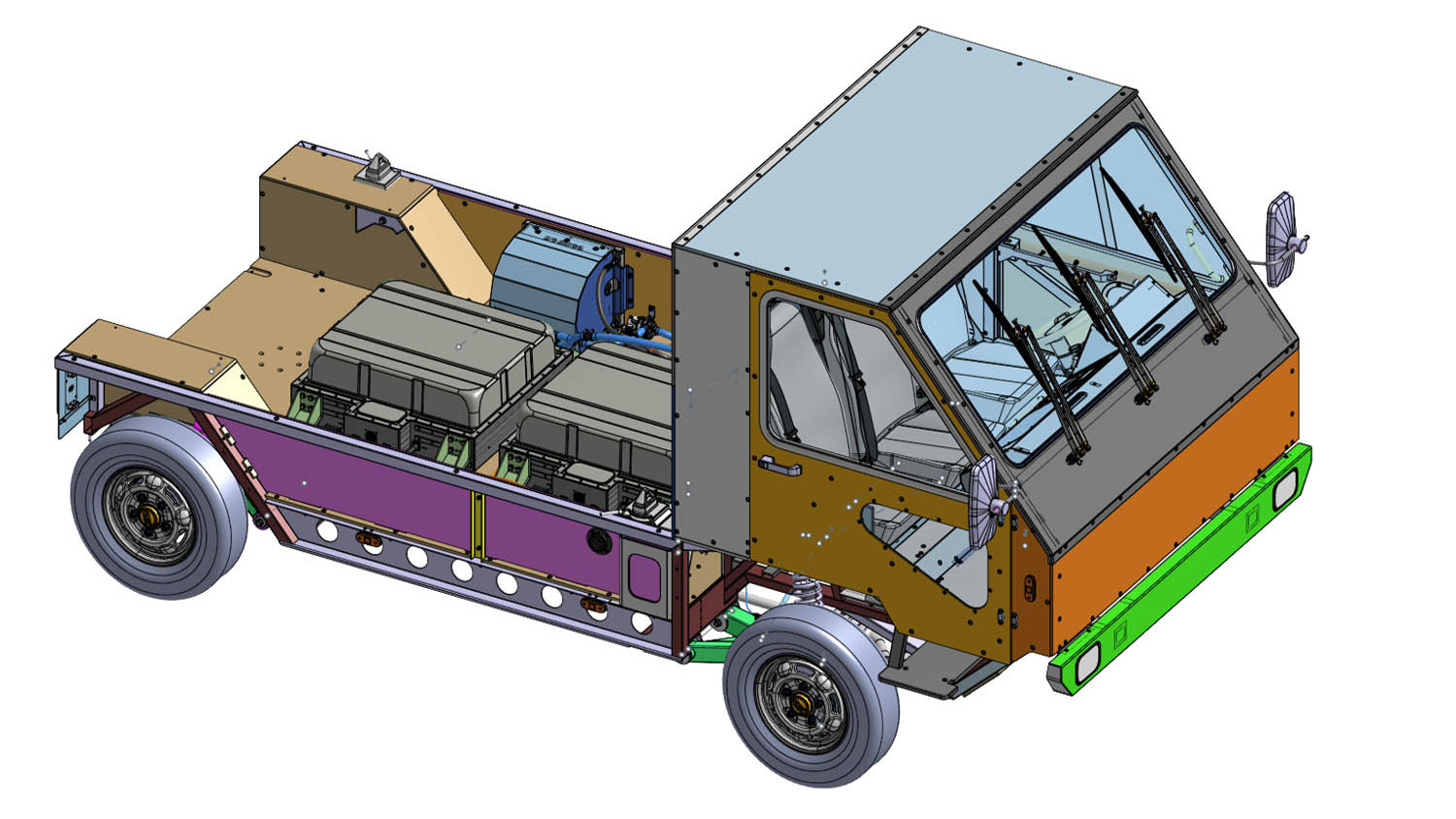
This article first appeared in DEVELOP3D Magazine
DEVELOP3D is a publication dedicated to product design + development, from concept to manufacture and the technologies behind it all.
To receive the physical publication or digital issue free, as well as exclusive news and offers, subscribe to DEVELOP3D Magazine here