5 trends from Formnext
Where is 3D printing heading? At DEVELOP3D, we talk a lot about this technology in product design: first, for its use in prototyping, but increasingly, as a way to build end-use parts.
Perhaps the best place in the world to get an overarching sense of the current state of play in the sector is Formnext, where four huge spaces in Frankfurt’s Messe Halle are packed with polymer and metal systems capable of delivering miraculous results.
With just a handful of days to cover the event, it’s entirely possible we missed some aspects of the action. But some clear patterns certainly emerged. Here, Stephen Holmes identifies five key trends from the event and what they could mean for design and engineering
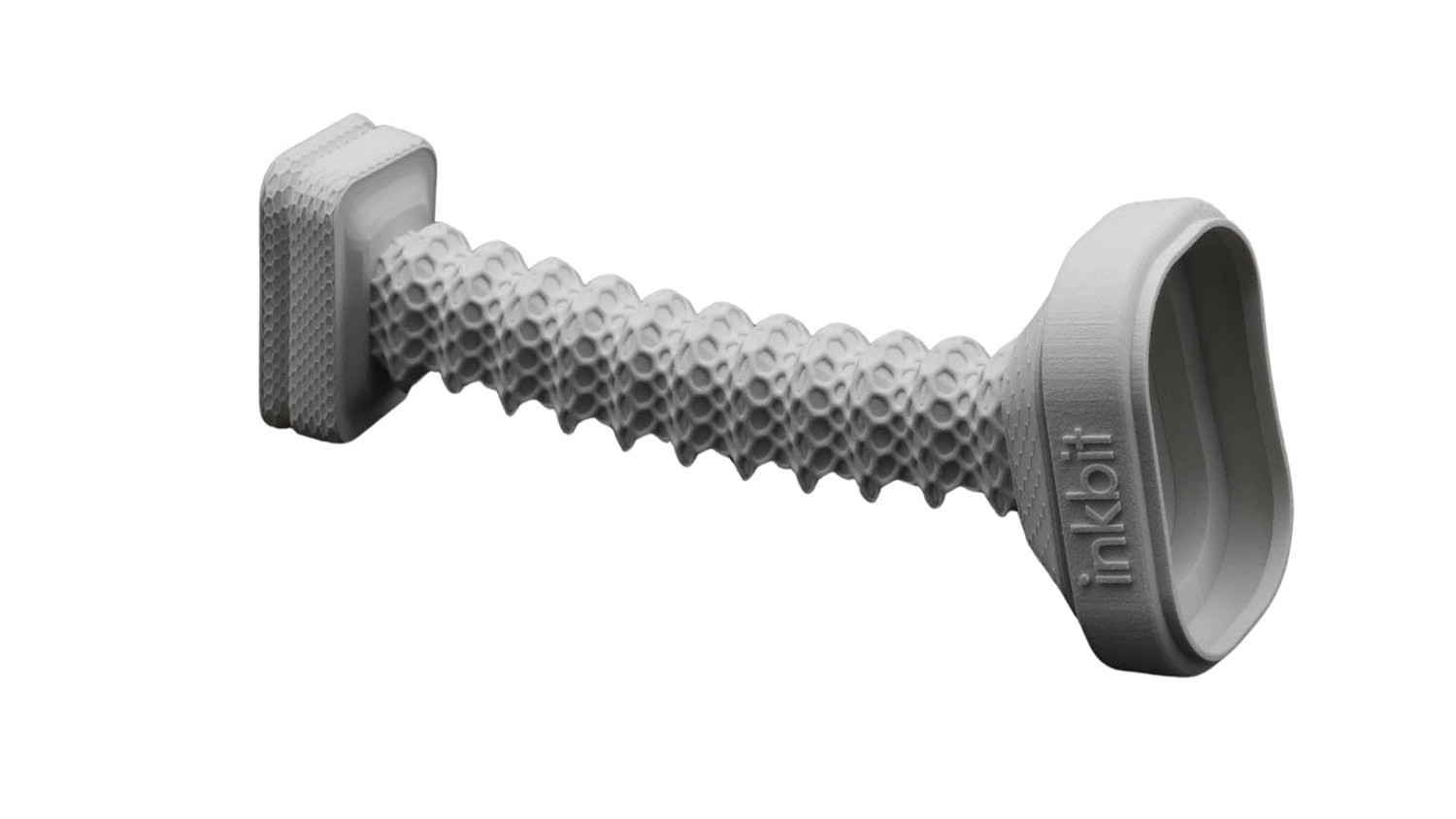
Finding a niche
While hardly on its arse, there is a sense that this maturing industry is fast running out of gimmicks. Throwing more lasers at a problem, wittering on about sustainability, or selling a machine built from someone else’s expired patents can only go so far.
Additive manufacturing is tightening its belt as investors lose interest and patience, and start to direct their lustful glances at artificial intelligence (AI) instead.
The need to generate real money from 3D printer sales is biting hard.
For many companies – those ones that are not still flogging the 2014 playbook of a ‘machine for all seasons’ – pinpointing some truly niche applications may be the best way to keep money flowing in and raising awareness of what their technology offers potential buyers.
Frankly, this is a massive relief. In the right hands, some additive technologies are capable of pure witchcraft, offering huge time and cost savings, unleashing designers and engineers from the shackles of old workflows, and allowing them to get stuck in to new and exciting projects.
Today, there shouldn’t be a single factory that doesn’t boast at least a few 3D printers of its own. They might be using them to produce custom end effectors, grippers, suction pads, new tooling or simply to replace dumb parts on demand when they wear out. Sexy? No. Dollar signs? Yes.
Food processing, rail spares, everyday electrical infrastructure: multiple industries have quietly fallen in love with specific types of 3D printing. And that means there’s money to be made in them there niches.
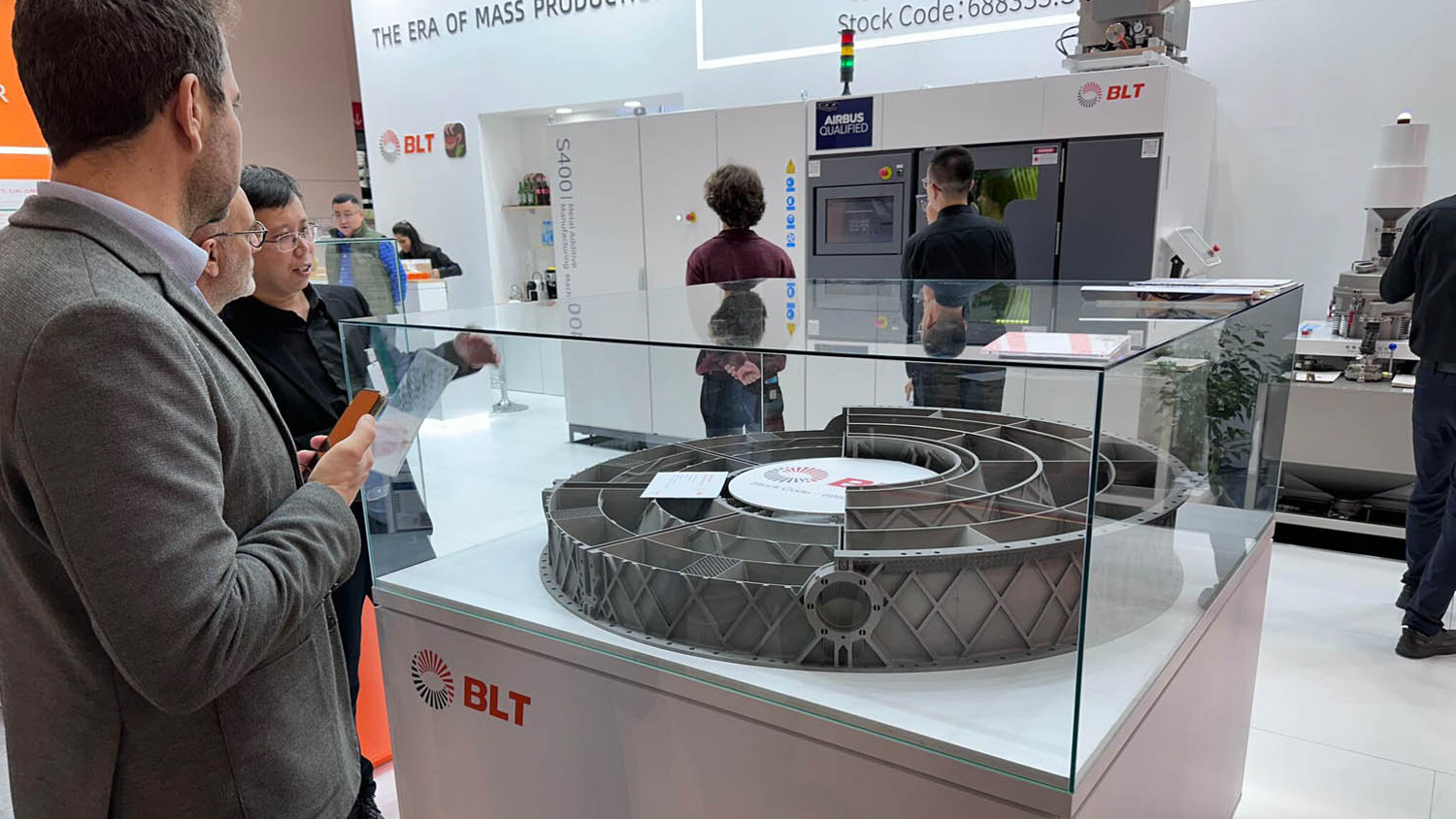
Asia’s impact
It should come as no surprise that the rest of the world’s factories haven’t been hanging around, waiting for Europeans and Yanks to build machines. The specimens on show at Formnext with origins in the Far East proved to be some of its biggest jaw droppers.
Need a 26-laser SLS machine with a 1,500 x 1,500 x 1,200mm build platform? No problem. The BrightLaser Technologies BLT-S1500 may be right up your street.
A sub-$1,500, 800 x 800 x 1,000mm FDM printer, capable of knocking out parts at 300mm/s? Yup, Elegoo has got it covered.
An open platform, 298 x 165 x 320 mm, DLP benchtop 3D printer that undercuts everyone and their mother? Have a look at Uniontech’s Martrix range.
An SLA 3D printer capable of producing full-scale prototype car body panels? Lincsolution over in Korea will sell you a 2,300 x 850 x 1,000mm unit, no worries.
To paraphrase Daft Punk, everything is bigger, cheaper, faster, stronger, and less tied to legacy materials and software infrastructure.
Sure, you might have some concerns about support, security and supply – but user stories for the large format machines in particular show their proven track record.
It’s no longer a case of the legacy brands looking over their shoulders. The Asian brands are here and in their faces.
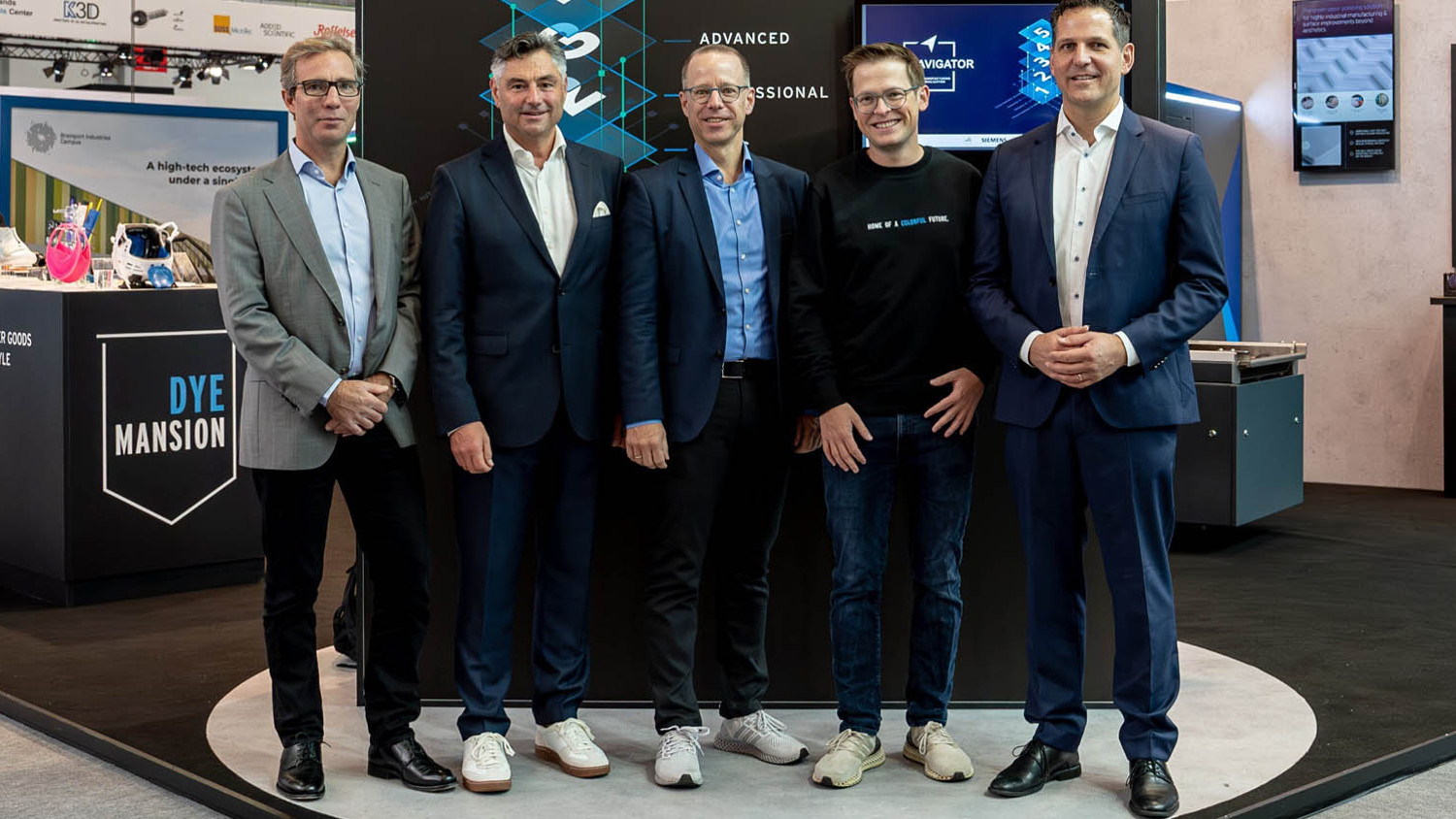
Come together
The above point on our list clearly signals a ‘shots fired’ moment in additive manufacturing. So it’s no surprise that a number of key European and American brands announced partnerships and collaborations at Formnext 2023.
Partly this is to create more fluid, brand-aligned ecosystems, but there’s also a real sense of circling the wagons at play here.
Siemens chose the event to shout about its new ‘holistic maturity’ model for industrialising 3D printing – the AM I Navigator Initiative. This takes that tried-and-tested Siemens knack for building parts, systems, factories and production lines that work, and applies it to additive manufacturing, with a little help from partners DyeMansion, HP, BASF Forward AM and EOS. Elsewhere, Siemens’ partnership with Ricoh around aluminium 3D printing is one of the most intriguing, purely for its focus on this specific material process.
HP was also busy bundling Autodesk Fusion with HP Multi Jet Fusion and Metal Jet printers, and lining up partners for metals materials (GKN, Sandvik and Elnik), alongside a developing relationship with metal injection moulding giant Indo-MIM.
Materialise, meanwhile, is no stranger to a partnership. (In fact, it’s one of the company’s key strengths.) At Formnext, it announced sensible partnerships with HP, to integrate its MJF and Metal Jet technology into the Materialise CO-AM software platform; with Ansys, for simulation; and with DigiFabster, for quoting automation and white-label e-commerce AM.
The new kids on the block aren’t missing a trick when it comes to getting involved with bigger, more established players. Hyperganic updated its fast-to-lattice software to include BASF materials data and metrics from top-tier Chinese 3D printer company Farsoon. Meanwhile Lincsolution signed an agreement with Xaar to provide its printheads.
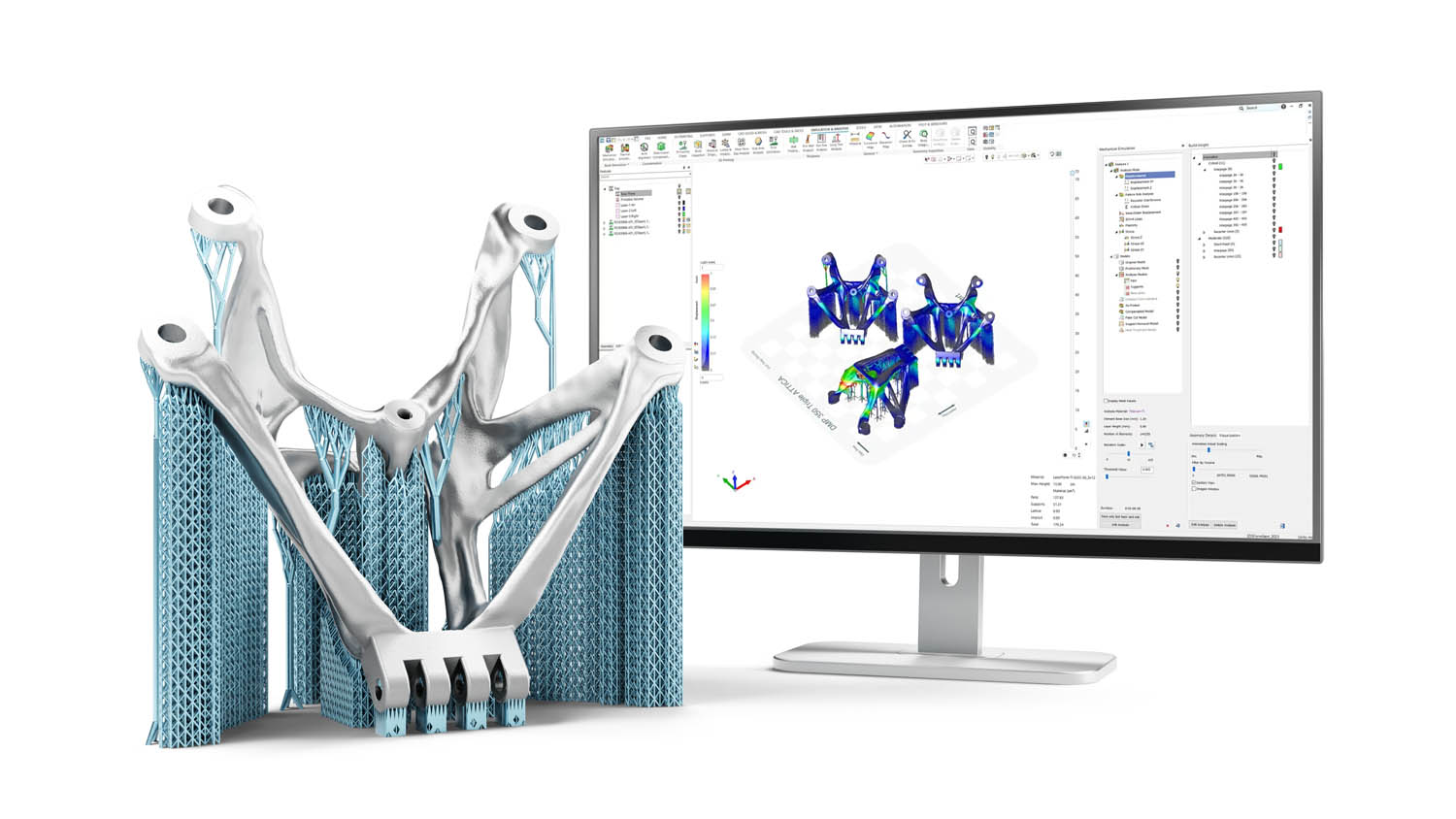
Problem-solving software
Formnext is no longer just a showcase for radical new technology, giving attendees the chance to coo about it in the bar after the show. It’s about solutions. And these days, solutions mostly come in digital form.
Most producers of additive parts are still using Materialise Magics as their production software of choice, and with good reason. In this area, Materialise knows much better than most what it’s talking about – but it’s no surprise to see big names trying to muscle in on the act.
We’ve already mentioned Siemens wading into the production-level fray, but another point to note is that its Xcelerator Marketplace has added three partner solutions specifically focused on additive manufacturing. Among them, the addition of Castor is probably the most exciting. Castor’s software looks at a database of parts and identifies which of these could be 3D printed (profitably) from the equipment you already have, and the ability to use it via the existing Siemens ecosystem is very cool indeed.
Xcelerator is quickly developing into a platform with a lot of options, and any expansion into AM is one to watch.
Hexagon is similarly moving to connect all of its production powers around AM. The HxGN Additive Manufacturing suite is machine-independent and CADagnostic, allowing it to connect multiple complex software and hardware across the workflow, while throwing in some lovely additions like Simufact Additive for process verification, Esprit Edge for post-process machining, and Digimat for materials qualification.
Oqton remains as impressive as ever, with 3D Systems continuing to let the team off the leash and do its thing. New addition Oqton BuildQuality monitors and traces the quality of 3D printed parts and evaluates build performance.
Some really impressive features help in detecting and correcting anomalies early on in the process, to either ensure the success of each part, or at least salvage the rest of the build. While other software suppliers chat about who beta-tested their kit, Oqton went straight to Baker Hughes (a firm that knows quite a lot about 3D printing critical parts) and developed the tool alongside it.
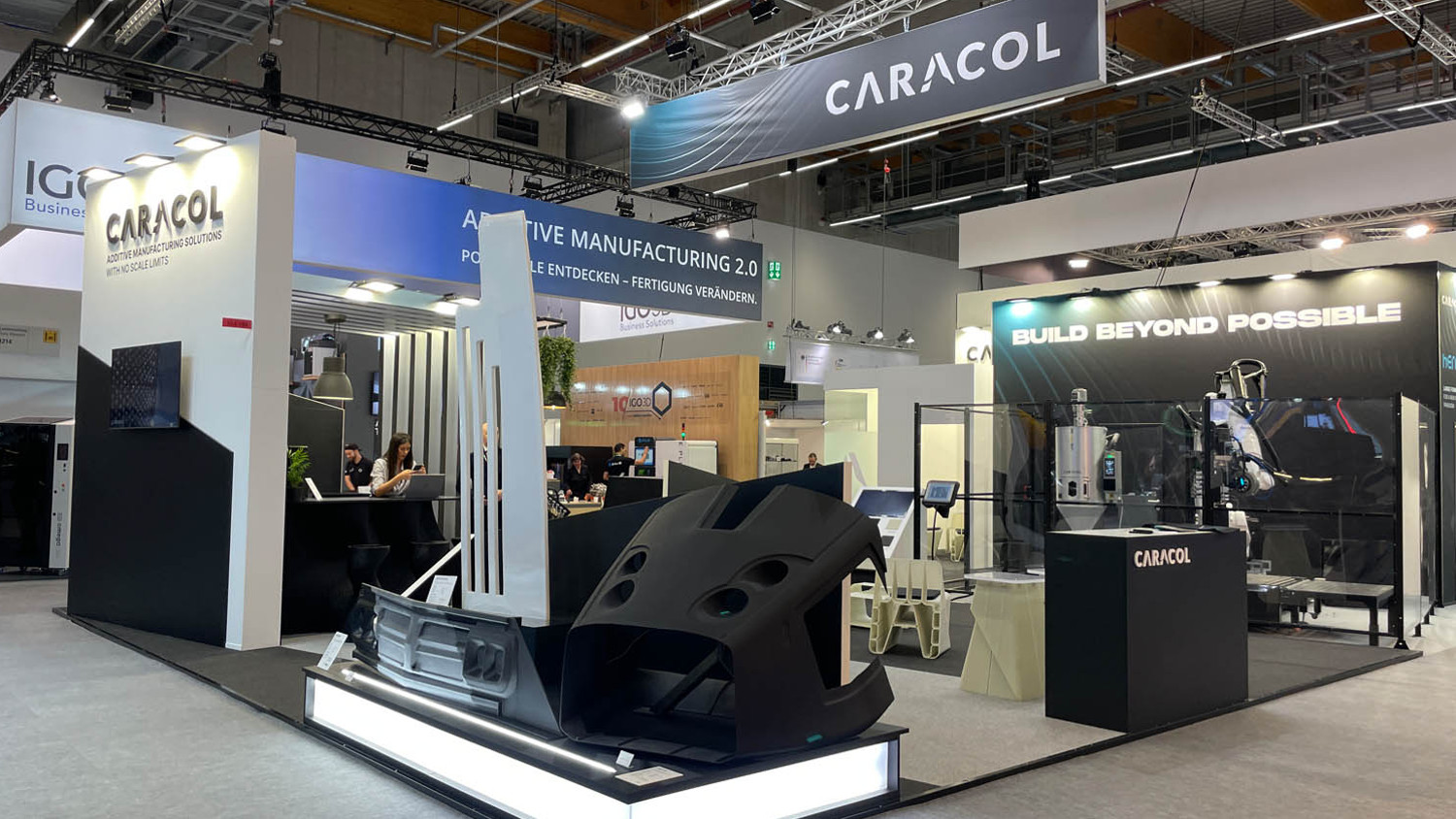
Formnext sees the rise of industrial heavyweights
These XYZ-axis boxes are all well and good, but if you want to remove constraints from 3D printing, then the best way is to print from the end of a 6-axis robot, using the cheap, verified, real-world polymers most commonly seen in injection moulding.
There’s more to solving this problem than strapping a hot end to a robot, but Formnext featured several companies making big leaps forward, enabling giant tooling to be built and even building end-use products on demand.
Companies including AI Build and Adaxis impressed with programming software that can work for polymers, metals and even concrete. Both technologies are hardware-agnostic, so you can use what you like. You simply import your CAD file for its geometry to be optimised and for toolpaths to be simulated, while sensors on robots means builds are monitored for quality assurance.
Turnkey solutions for largeformat, robot-based systems are on the rise, with brands like Caracol and Cead working with customers on building end-toend solutions that encompass printheads, printbeds and postprocess milling.
Both companies offer set-ups that can be found in aerospace and automotive autoclave tooling, as well as at rail and marine parts suppliers, and Caracol even offers its own software.
Pellet-extrusion was also on show, not only with Arburg’s longstanding entry into additive, its Freeformer, but with a new entry into the market from Bosch, and on the 3D Systems stand with the development of the EXT Titan Pellet 3D printer. Capable of 1270mm x 1270mm x 1829mm build volumes, and printing with pellets enables hundreds of thermoplastic materials to be 3D-printed, including high-performance materials not available in filament form, the EXT Titan was a popular machine for attendees.
If 3D printing is realistic about being part of the bigger manufacturing picture, then expect the trend for industrial robotics and feedstocks to grow fast.
This article first appeared in DEVELOP3D Magazine
DEVELOP3D is a publication dedicated to product design + development, from concept to manufacture and the technologies behind it all.
To receive the physical publication or digital issue free, as well as exclusive news and offers, subscribe to DEVELOP3D Magazine here