From feeding ingredients into a sandwich, to testing the tenderness of fresh peas, Dodman Ltd design and manufacture food handling, processing and packaging factory equipment for some of the UK’s favourite brands.
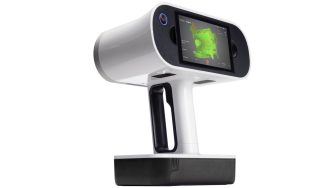
Designed for efficiency, with important considerations for accessibility and cleaning hygiene, products can often be bespoke solutions – from a stand-alone conveyor to fully automated processing lines.
A move by its design team to incorporate the latest reverse engineering technology into its process has allowed its customers to upgrade or find new uses for existing machinery, a cost saving and sustainable move.
Through experience, the Dodman team understand that 3D scanning is just the beginning of this process. Having mastered using its Artec Leo 3D scanner, the team adopted KVS Mesh2Surface to process the scan data and allow them to use it in Solidworks.
Here is where the real engineering work lies – transforming the scanned data into manufacturable designs. While Mesh2Surface’s tools make this process fast for the team, it still requires an engineering mindset and an understanding of sheet metal fabrication, ensuring that designs are practical and can be built with the available plant and materials.
From a manufacturing perspective, the end result needs accurate parts and a full bill of materials. “It’s not enough to draw simple tubes to represent pipework or hollow sections, it has to be drawn to a pipework standard, or, for example, using standard pieces of box section that can be sourced and manufactured,” explains Dodman design engineer Andrew Chase, adding that a key benefit of reverse engineering using Mesh2Surface is that it can run directly inside Solidworks, eliminating the need to switch between different software environments.
With projects around older equipment with no CAD data available, capturing the part data in a 3D scan over a few hours on-site, the team are able to reverse engineer a full CAD model within in a couple of days.
The accuracy and speed of this process, says Chase, allows the Dodman team to capture every detail, allowing for later design changes without the need for additional site visits. The process also minimises the risk of errors.
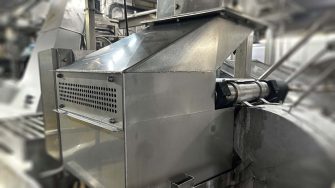
With support from its Artec and KVS reseller, Patrick Thorn, the team have been able to approach complex projects that would have previously been unfeasible. A recent example is a potato dicer that needed to be fitted onto a new machine within tight tolerances that would ensure operator safety.
In a trip to the customer factory, the team quickly captured the dicer using the Artec Leo 3D scanner while it was still being used on the outgoing machinery. With the data captured, the Dodman team could clean-up the scan and remove the old machinery in Mesh2Surface, before transferring it to Solidworks where it could be accurately be reconstructed.
With the precise dimensions of the 3D CAD model, fixtures corresponding to the new machinery could be developed and the elements – old and new – could be mated together digitally.
The process allowed the team to achieve a millimetre-perfect fit in real life, the dicer slotting precisely into place on the new machinery with minimal downtime for the customer.