BMW has built a new automated factory line that allows the company to take full advantage of 3D-printed sand casting for cores, producing thousands every week and benefiting designers, manufacturers and end customers
From origins that date back thousands of years, through the industrial age and now with the addition of 3D printing and inorganic forms, sand casting has been through several periods of radical transformation in its long history.
At BMW Group’s largest component plant in Landshut, Germany, the world’s first fully automated additive serial 3D production line for sand cores has been built. Developed with the knowhow of experts at BMW, Loramendi and Voxeljet, the Industrialisation of Core Printing (ICP) cooperation project looks set to inject this ancient art with added speed, sustainability and design freedom and set a new industry standard at the same time.
As a company, Loramendi has a long history in developing solutions that keep foundries at the cutting edge of production, with expertise in inorganic casting methods. Joined by Voxeljet’s 3D-printed sand casting technology, the two companies have developed a system for the automatic large-scale production of sand cores used in casting cylinder heads for high-efficiency engines.
The ICP line is currently producing thousands of 3D-printed cores each week to support the mass production of the latest generation of BMW Group engines at Landshut, which supplies all of BMW’s vehicle and engine plants worldwide. These areused for almost all BMW, MINI and Rolls-Royce vehicles, as well as for motorcycles from the company’s BMW Motorrad brand.
One-piece sand cores
The production of inorganic 3D-printed cores has enabled BMW Group to advance the design of its engine components.
For example, the cylinder head for BMW’s B48 engine has been significantly improved by using 3D printing to produce water jacket outlet combi cores. Additionally, 3D printing allows BMW to produce sand cores in one piece, reducing the complex design of engine components while optimising engine efficiency and fuel consumption.
The custom, low-emissions production line significantly reduces foundry emissions, as only water steam is produced during the casting process.
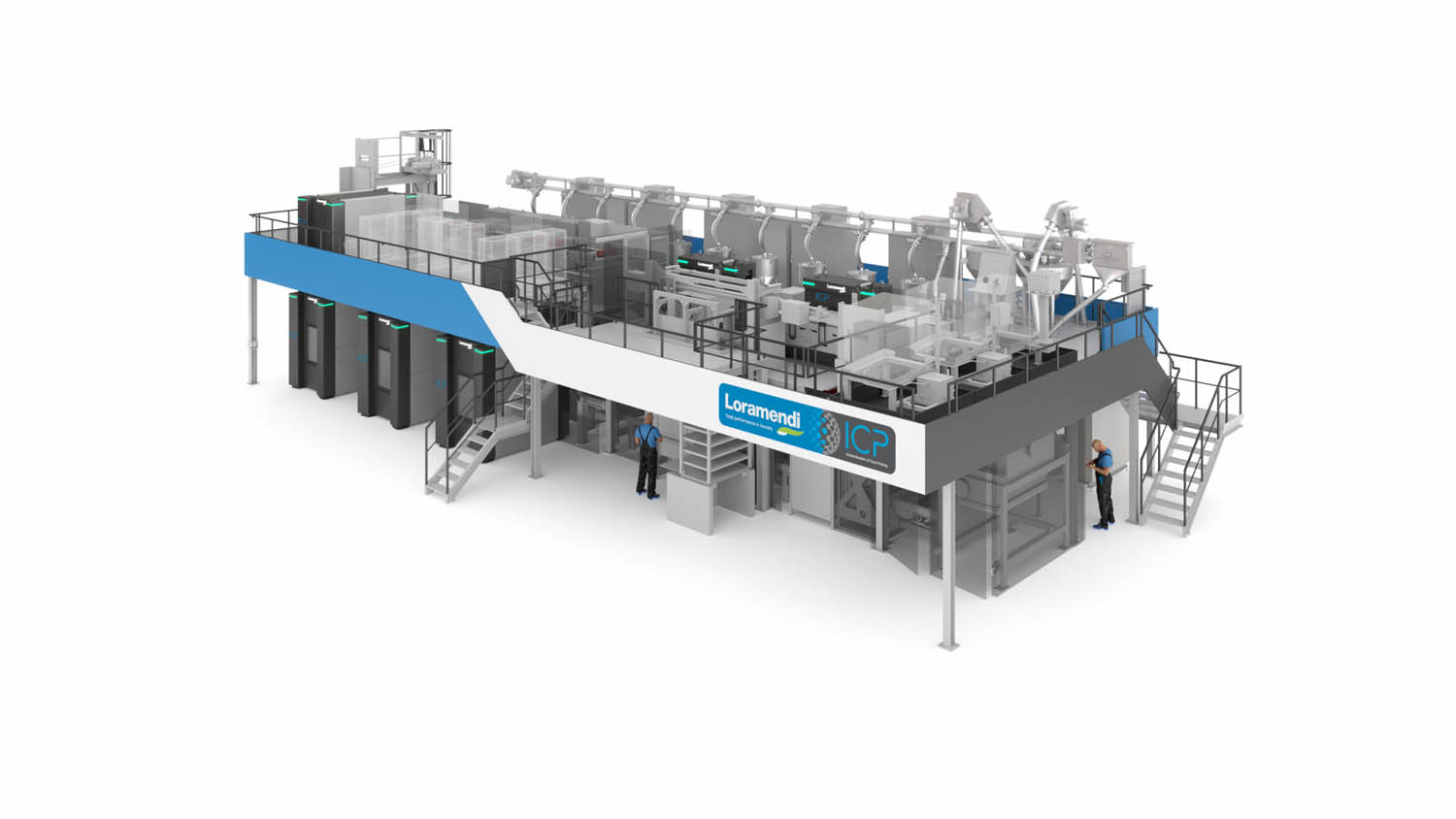
The automated line integrates Voxeljet’s latest highspeed VJET-X 3D printers into a fully automated preand post-processing workflow, which also includes Loramendi’s industrial microwave curing units.
A print head selectively bonds layers of sand to create the cores, which are then unpacked, microwave-cured, cleaned and inspected before being fed into BMW’s established casting process.
The printing rates of the Voxeljet VX1300-X have been increased by a factor of ten over previous models, and the toolless design of the sand cores allows BMW to make variant changes at unprecedented speed without time-consuming tool changes and production downtime. Unused material from 3D printers is recycled and reused in the production process.