At Liniar, a new uPVC product suite can easily cost well into six-figures for tooling, particularly for extrusion, so having the confidence that a physical model gives the designers helps when going forward and cutting steel.
Liniar, whose plastics mixing plant in Denby, UK, is the largest in Europe, employs 500 people and works around the clock to produce 32,000 tonnes of material annually, using it to create and supply windows, doors, conservatories, decking and fencing to specialist fabricators and installers.
With more than 50 registered patents and a Queen’s Award under its belt, Liniar has big ambitions when it comes to product design – and 3D printing is operating at the heart of its current success.
“It’s not only product development and design that we use it for. We also print jigs and fixtures for our fabrication divisions,” explains Liniar product design manager Tom Roberts.
3D printing reduces the time and expense of machining components for saw blocks or drill jigs on the manufacturing and assembly front, but for Liniar, its biggest cost saving is time.
With faster development of new products key, and the ability to iterate on a design or idea is truly valuable.
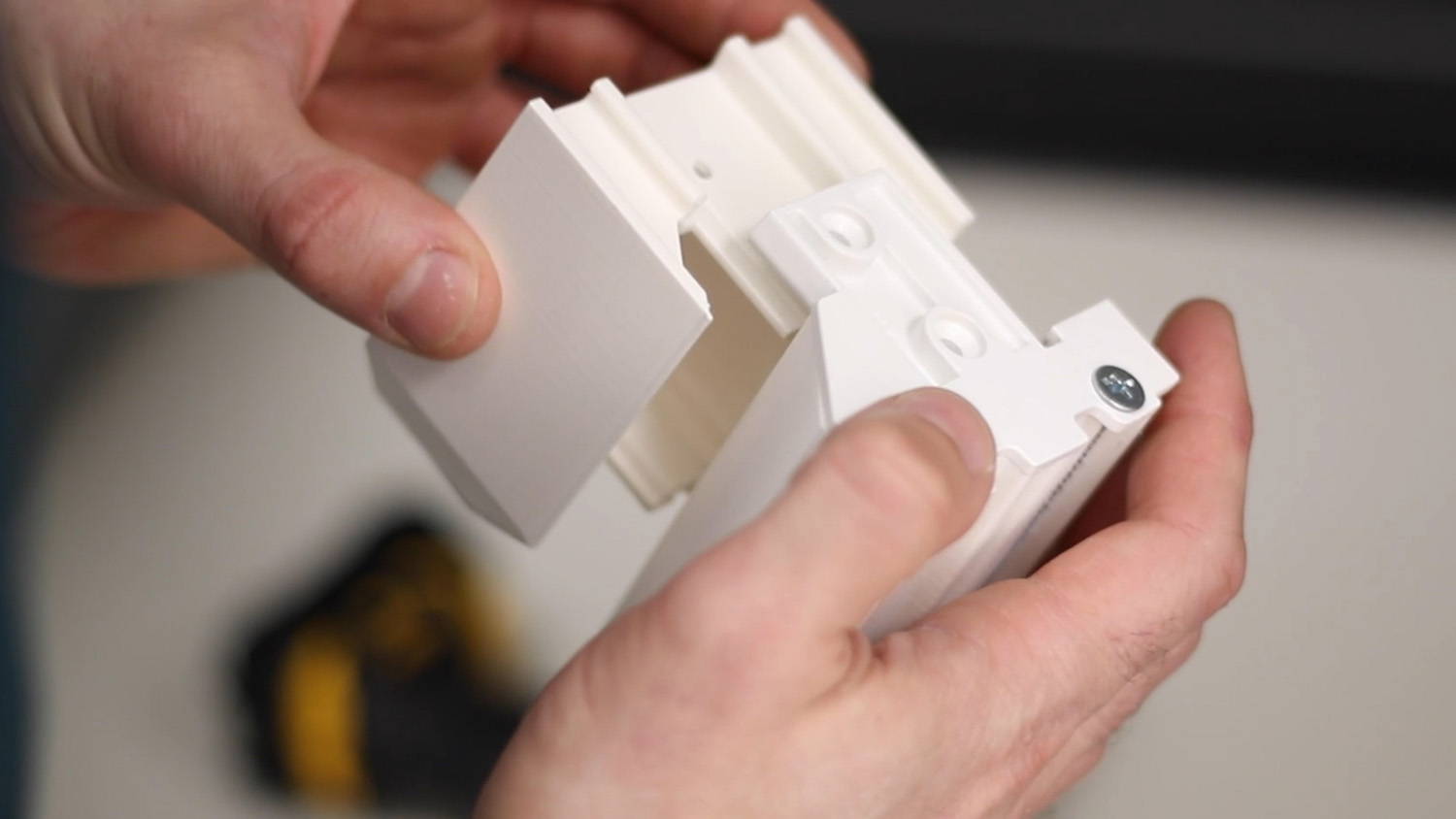
Liniar has used a Stratasys Objet260 Connex3 for nearly six years but has more recently installed a Stratasys F370, with both machines supplied by experts SYS Systems.
Where the Connex offers precision multi-material printing in a spectrum of colours, enabling design freedom and the ability to overmould rubber-like materials, the F370 produced tougher FDM thermoplastics, used to produce functional parts that can withstand vigorous testing.
Roberts is positive about having the abilities of both technologies in-house: “With the two printers we have the best of both worlds: We can print rigid material, which is useful for a lot of the extruder profiles we produce, but we also have a co-extruder gasket on our profiles.
“We can design products, assemble them, make some changes, re-print it and try it again, all in the space of a day.”
Given that the team design a lot of products with gaskets and sealing, being able to print with multi-materials and produce realistic components has meant a big bonus for the development cycle, without having to produce tooling to extrude profiles.
Liniar’s products can be big and heavy, and need features like screw ports and clipping features. With the 3D printed parts, Roberts and his team can screw together full assemblies as they would end use products, and know that it works.
“As great as 3D CAD is it’s always nice to have a physical part in your hands to be able to test it out and see if it performs as you think it will,” concludes Roberts.