Having returned to his design for the Aston Martin Vanquish, Ian Callum has reworked the model for today’s GT driver. DEVELOP3D spoke to the team at the Callum Designs studio about the role played by desktop 3D printing in the Aston Martin Callum Vanquish 25
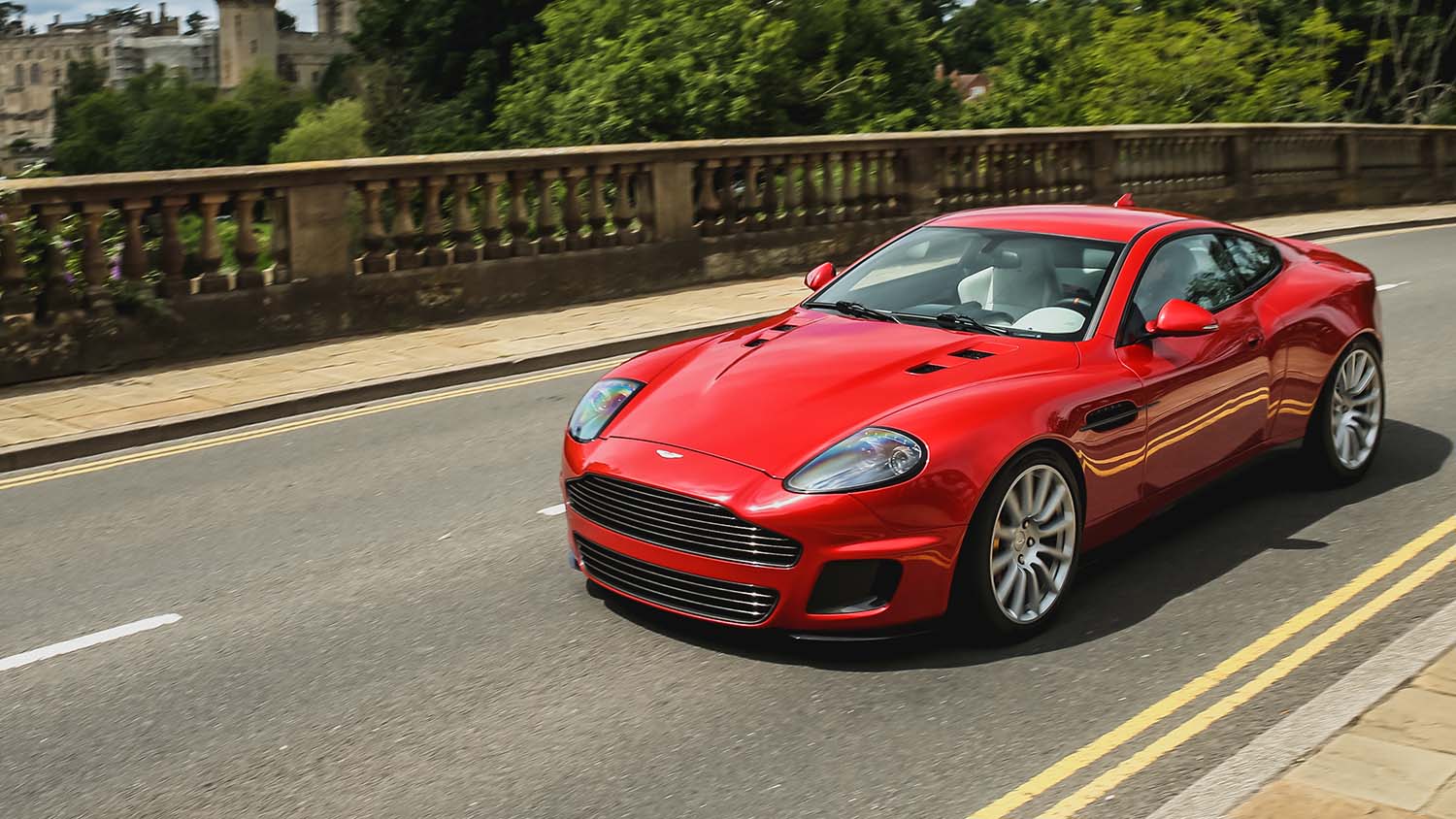
Two decades after he first sketched the iconic lines of the Aston Martin Vanquish, legendary automotive designer Ian Callum CBE has recently produced a contemporary version of his creation: the Aston Martin Callum Vanquish 25.
Much like the ‘director’s cut’ of a classic movie, this reworking of the V12-engined grand tourer retains many of the designer’s original flourishes, while also benefiting from advances in materials and technologies.
As a result, the Vanquish 25 features over 350 design and engineering updates developed at Callum Designs, the designer’s own design, engineering and production company.
The svelte form of the Vanquish has been refined to give the new car a more purposeful look, reflecting the increase in power from its 5.9-litre V12 engine. Lower and wider, its revised suspension delivers a sharper ride, while stopping power is similarly enhanced by new carbon ceramic brakes.
The interior, meanwhile, has been heavily reworked, with exclusive interior trims created by in-house craftsmen. Fully endorsed by Aston Martin Lagonda, customers can choose to upgrade their own existing car or have one sourced, and are encouraged to play an active role in working with Callum to create their unique Vanquish.
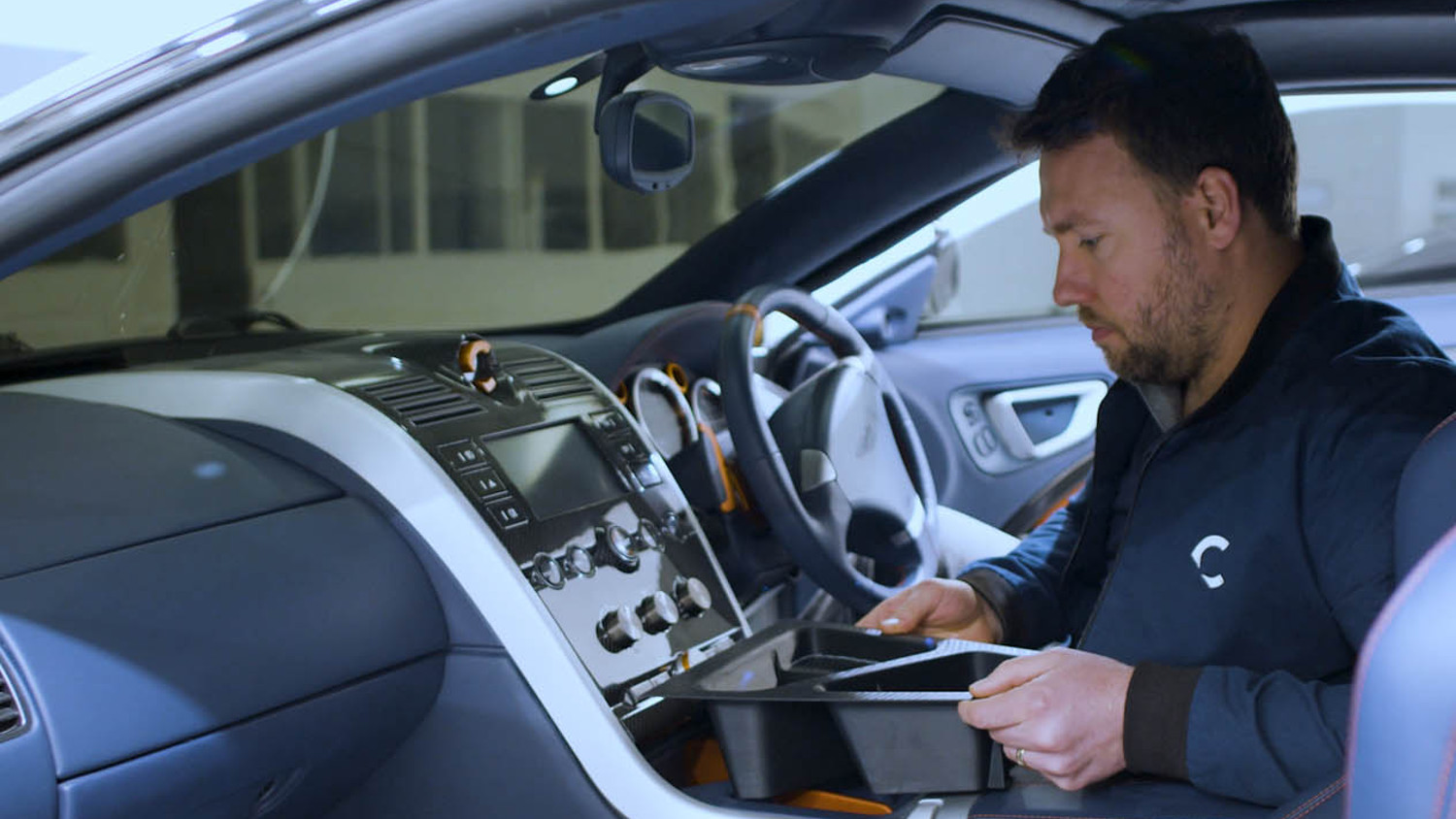
Room for additive
Based in Warwick, UK, the Callum Designs headquarters boasts full design and engineering capabilities, along with 9 build bays to produce the Vanquish 25. As well as a full trim shop and 3D metrology capabilities, space is also set aside in the design and production workspaces for additive manufacturing.
Throughout the design and development of the Vanquish 25, Callum Designs has used desktop 3D printers to produce functional prototypes for testing proof of concepts. “
Additive manufacturing has come a long way in the past ten, even five years. The resolution of such machines is much better, allowing us to create intricate products with a high standard of finish that wouldn’t have been possible before,” explains Callum Designs engineering director Adam Donfrancesco. “Traditionally, these parts would have been machined from billet aluminium, or created via injection moulding. These methods are expensive, time intensive and often reliant on third-party suppliers.”
Waiting around for some small, low-volume part to be produced isn’t an option – or worse still, finding out it doesn’t meet Callum’s exacting requirements when it does arrive. “When you’re working on such a prestige vehicle as an Aston Martin, and at the level of refinement [that] we are, everything has to be absolutely precise,” he says.
The complexity of the parts involved means that the design process often has to be iterative. Air ducts for cooling the new brake discs and callipers, for example, had to integrate with the bumper and pick up the wheel arch lining. This required tweaking to achieve the perfect fit and airflow.
Low-cost 3D printing meant that the design team could experiment with new ideas right up until they were ready to create the final parts.
This was the point at which the desktop 3D printer that Callum Designs had chosen came into its own. Having opted for the MakerBot Method X, the path from quick concept models to Nylon 12 Carbon Fibre for the final production parts to be fitted to the vehicle was seamless.
“Due to its strength, stiffness and heat resistance, Nylon 12 Carbon Fibre is an ideal lightweight solution for parts such as brake ducts,” explains Donfrancesco.
“At the front end of the car, you have impact considerations, and these materials enable us to meet the stringent requirements of these environments. The ability to produce parts in such strong materials is one of the most impressive attributes of the Method X desktop machine. For its size, it really is remarkable – something that’s been hugely beneficial to Callum.”
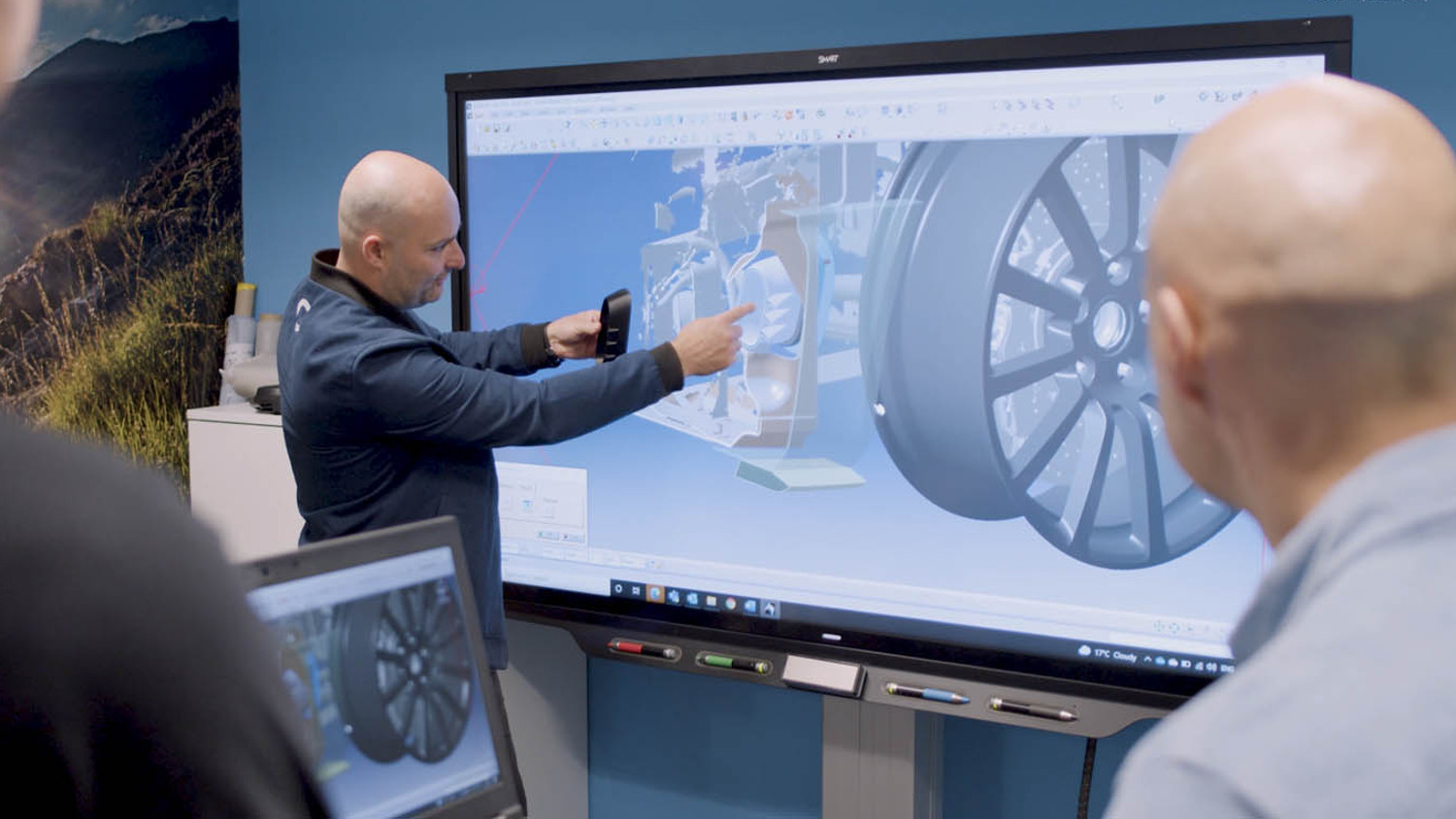
Timeless design
Callum partnered with luxury British watch manufacturer Bremont on the design of the driver’s instrument cluster, and has even placed a removable mechanical Bremont pocket watch centrally in the dashboard of the Vanquish 25.
The team wanted to make this timepiece removeable, so that the vehicle owner can wear it when not using the vehicle. As such, it developed a bespoke mounting mechanism to keep the expensive feature of the interior secure during transit, but easy to access.
“A lot of development was required for the clock housing. We needed to create something that worked ergonomically; many iterations were developed on the Method X and validated in the vehicle, which we were able to progress quickly,” says Donfrancesco.
“We needed to ensure that when you were sat in the driver’s seat that it was easy to remove – that it wasn’t uncomfortable or forced your wrist into an unusual action to remove or insert the clock. There is also a high degree of tactility to consider, too.”
By producing iterations of each concept, the team were able to experiment with the mechanism, which also led to them introducing customisation cost-effectively.
The dimensional accuracy of the 3D printer, combined with the soluble support material has meant that it has been used to create further mounting and fixture devices within the interior.
Fixtures, like those used to position and secure the infotainment screen in the dash, would typically require aluminium injection moulding. However, for such low volume requirements, Callum saved cost and time by using reinforced parts straight from the MakerBot.
Says Donfrancesco. “Instead of the time and cost of developing tooling, we were able to create these intricate parts ourselves.”
He goes on to explain that the methodology fits well with the firm’s design process, while the low costs for both prototypes and end-use parts is a huge win for the team.
“With the filament and usage costs so low, it feels like it’s ‘free’ to try these different things,” he says.
For this comparatively small design and engineering company, the speed and flexibility of the new workflow it has established has helped it not only to refine its design, but also control its own destiny in terms of the supply of parts for its creations.
The end product is a prestige vehicle with all the luxury, exclusivity and detailing its badge demands, with a little extra magic added by the man who first brought the car to life.