As more goods get shipped around the world, Loadhog is redesigning transit packaging for sustainability. Emilie Eisenberg learns more about the company’s focus on greener, more ergonomic alternatives
In goods transportation, the pressure is on for manufacturers to ship in as environmentally friendly way as possible, while delivering products free from damage in easy to handle containers.
Experts in goods handling Loadhog has been making specialist transit packaging since 2023, moving stock for brands like Sky, the NHS and Pets at Home. Investing in a 3D printer from SYS Systems has allowed Loadhog to significantly shorten their manufacturing process, improving the speed at which products can go from on-screen to their customers’ doors.
Its latest solution, the Dolly Max, is a reusable rolling container system created to carry segregated or loose bulk goods. It was designed after multiple enquiries from customers wanting an alternative solution to traditional roll cage pallet shippers.
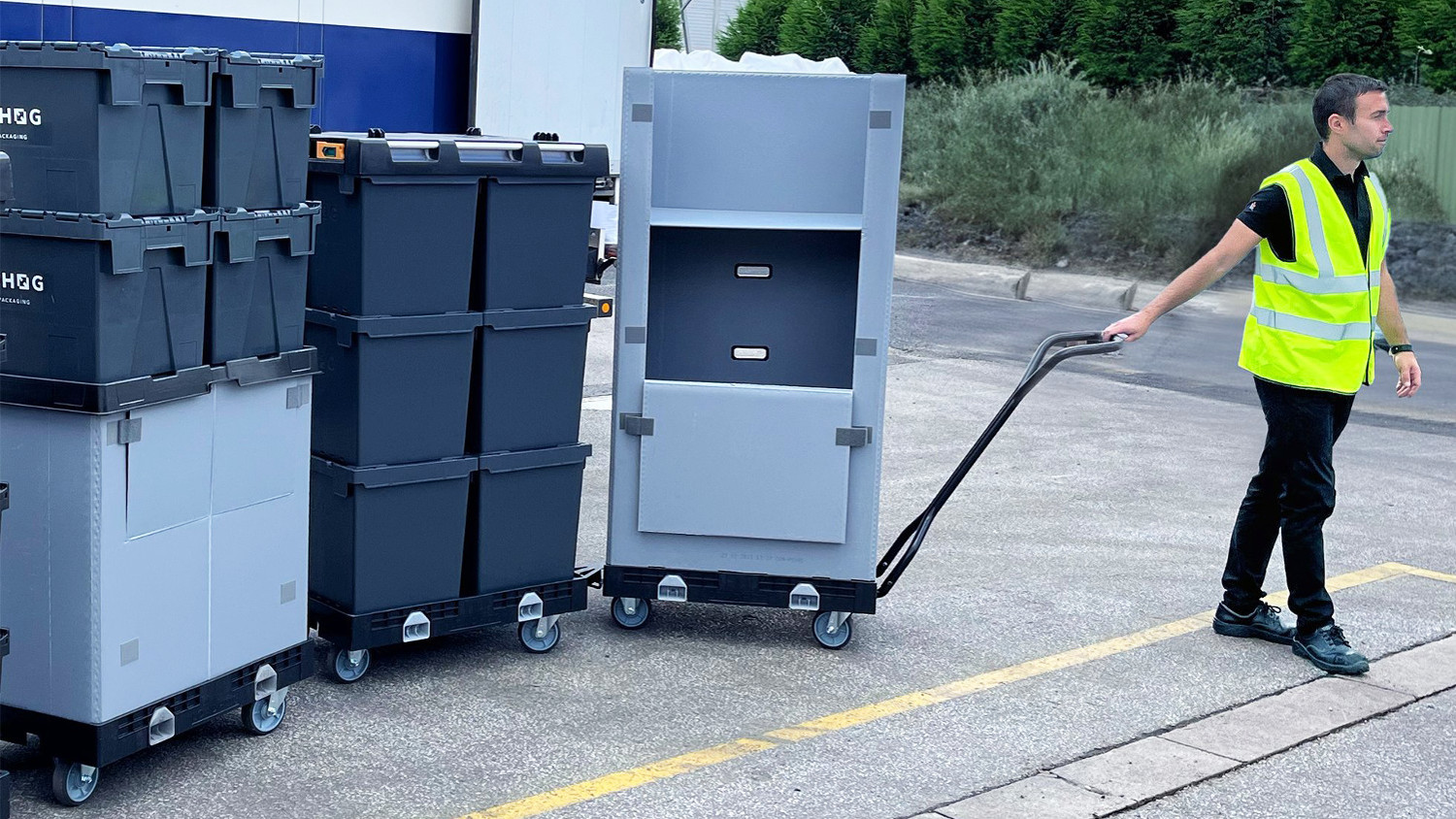
This traditional method can be difficult to use, typically requiring a cellophane wrapping to be applied to keep the load together – adding waste through single-use plastic.
The Dolly Max boasts reusability as well as an improved design on their previous models. It is intended to be deconstructed and returned to Loadhog quickly and efficiently. The bulk system has a 3/1 return ratio and ergonomic sleeve locks, with large safety shoe access to speed up system deconstruction.
The Dolly Max’s one-touch break mechanism is ergonomic and ensures that the brake is always applied. The vehicle fill has a 20% increase compared to standard roll cages, resulting in maximum efficiency and a decreased carbon footprint for the customer.
The system is designed as a safer alternative to substitute systems due to the brake’s coefficient of friction ensuring the unit remains still even on a sloped tail lift. It has no sharp metal touch points, unlike traditional roll cages, and doesn’t require material handling equipment unlike pallet shippers.
Based in Sheffield, UK, the design team’s goals were to create a product that had increased versatility, improved vehicle fill and handling efficiency while reducing plastic waste. Loadhog’s Ideas and Innovation department work to ensure that designs are as sustainable as possible, including designing products that can be made from 100% recycled plastics.
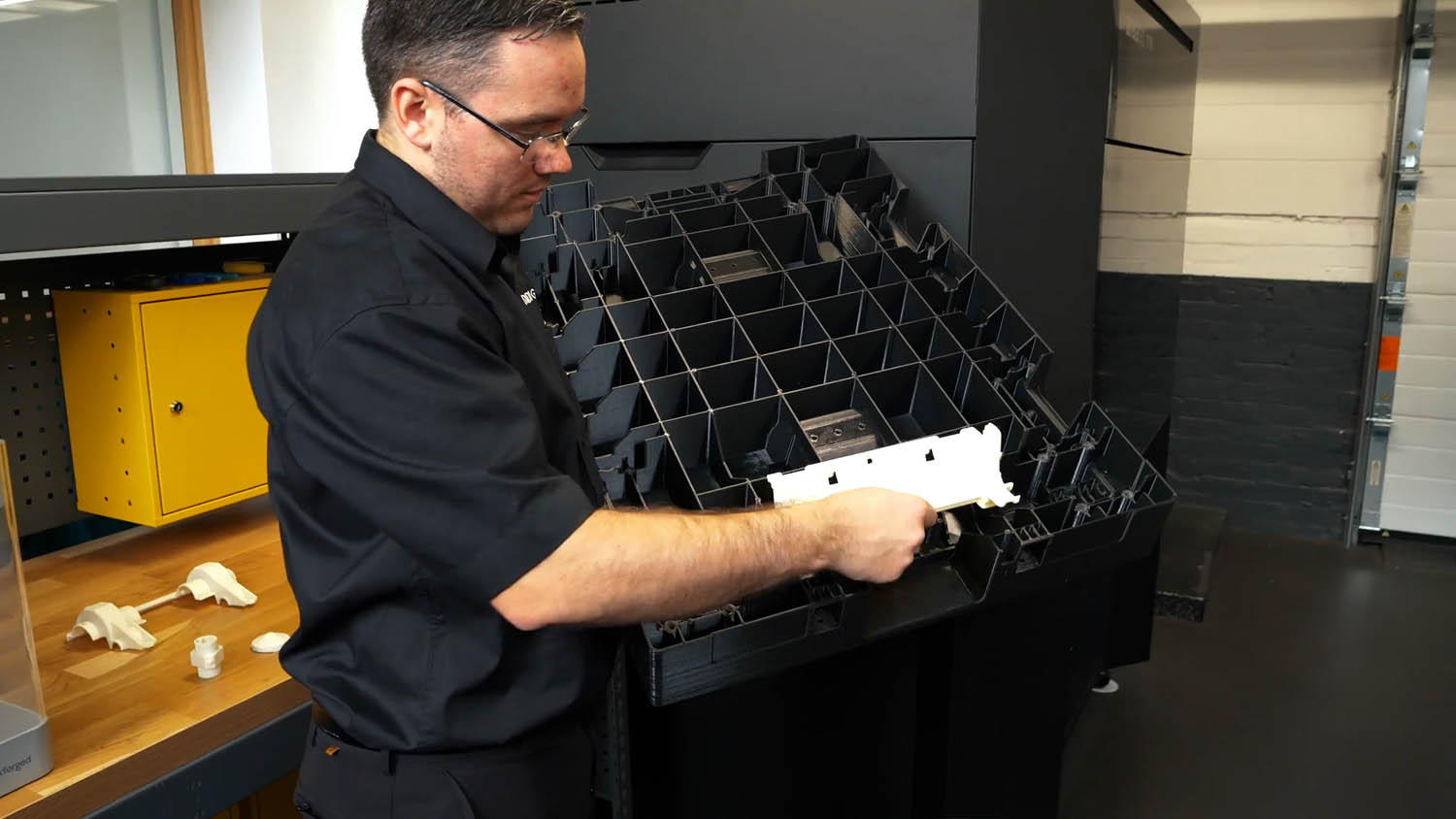
Product development begins
The product development process begins with initial concept sketches that are then turned into 3D CAD files using PTC Creo. Mouldflow analysis is also carried out on designs by a third-party tooling supplier.
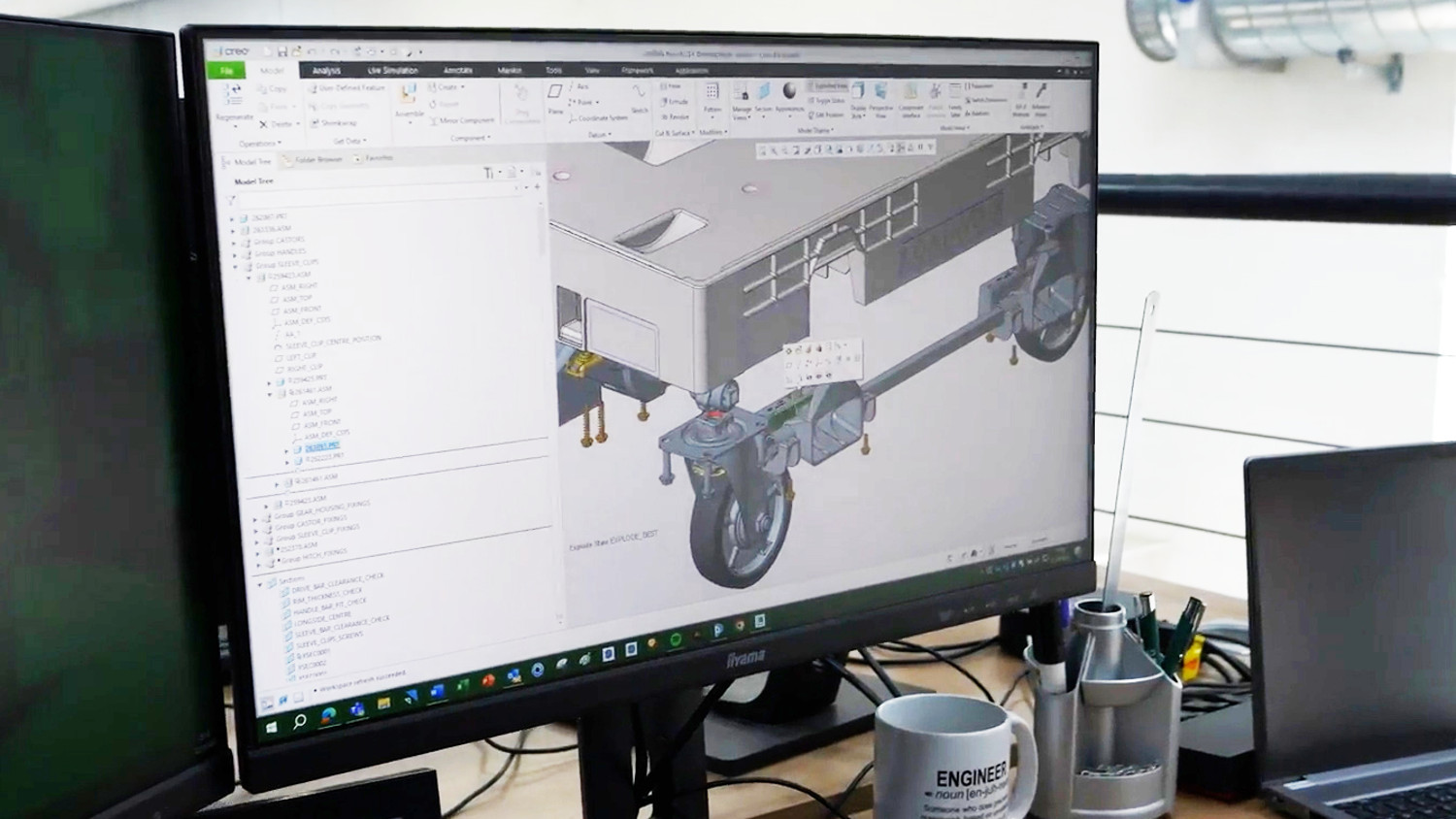
The Stratasys F770 3D printer is used to print functional prototypes of the design which can be showed to customers and re-designed until a final version is approved. GrabCAD is used for integration with the F770.
The F770 was supplied by SYS Systems, a Platinum Partner of Stratasys, which supplies Stratasys additive manufacturing solutions to companies across the UK.
The end products are then manufactured onsite at Loadhog’s manufacturing facility, which runs 16 injection moulding machines 24 hours a day.
The Stratasys F770’s large format capability means prototypes can be completed in a single print, even for the largest Loadhog products
Since introducing additive manufacturing into the process, the timeframe on creating new products has shortened from months to weeks. The F770’s large format means prototypes can be completed in a single print, even for the largest Loadhog products.
Prior to using the F770, Loadhog used hobbyist 3D printers to print parts which had to then be bonded together and tested. They also outsourced prototyping, which added weeks onto the development time due to delivery time and the time necessary for communicating with third parties.
The decision to use the Stratasys 3D printer was made due to its size and large capacity.
In addition to shipping equipment, Loadhog also uses additive manufacturing for printing bespoke jigs and fixtures for machinery and product assembly, as well as parts for robotic arms.
The Dolly Max proves that sustainable alternatives are by no means a world away, and Loadhog’s success in eliminating the single-use plastic without compensating on quality will no doubt encourage other manufacturers to follow in their footsteps. With an initial order of 10,000 units placed for manufacture, and a distributor set to deliver the units to independent garages, retailers, and home delivery services, the Dolly Max is set to be a success.
This article first appeared in DEVELOP3D Magazine
DEVELOP3D is a publication dedicated to product design + development, from concept to manufacture and the technologies behind it all.
To receive the physical publication or digital issue free, as well as exclusive news and offers, subscribe to DEVELOP3D Magazine here