BMW Group’s Lightweight Construction and Technology Centre in Landshut has given a peak at how it has been optimising its car production lines with 3D printed robot grippers and end effectors.
A particularly large gripper element weighing around 120 kilograms, was manufactured in just 22 hours and is then used on a press in the production of all Carbon Fiber-Reinforced plastic (CFRP) roofs for BMW M models.
The press is first loaded with the CFRP raw material, with the gripper rotating 180 degrees to remove the finished roofs. Compared to conventional grippers, BMW says that the version manufactured using 3D printing was roughly 20 per cent lighter, which in turn extend the operating life of the robots and also reduced wear and tear on the system, as well as cutting maintenance intervals.

This particular robot gripper is a combination of two different 3D printing processes – the vacuum grippers and the clamps for the needle gripper to lift the CFRP raw material are made using selective laser sintering (SLS), while the large roof shell and bearing structure are manufactured using a large format, pellet-fed FDM process (BMW calls it large scale printing – or LSP), which can also use recycled materials from the CFRP process.
Compared to the use of primary raw materials, CO2 emissions when manufacturing the gripper are apparently in the region of 60 per cent lower.
In summer 2023, an even lighter generation of gripper was introduced, applying topology optimisation to the original design and generating what BMW calls a ‘bionic’ form.
This combined the roof shell from the LSP printer with SLS vacuums and an optimised bearing structure. For this, a mould with printed cores is used in the sand casting. This mould is then cast with the intricate aluminium structure.
The new gripper is a further 25 per cent lighter than its predecessor, meaning the entire process of manufacturing a CFRP roof of the BMW M3 can now be performed with just one robot, rather than three as was previously the case.
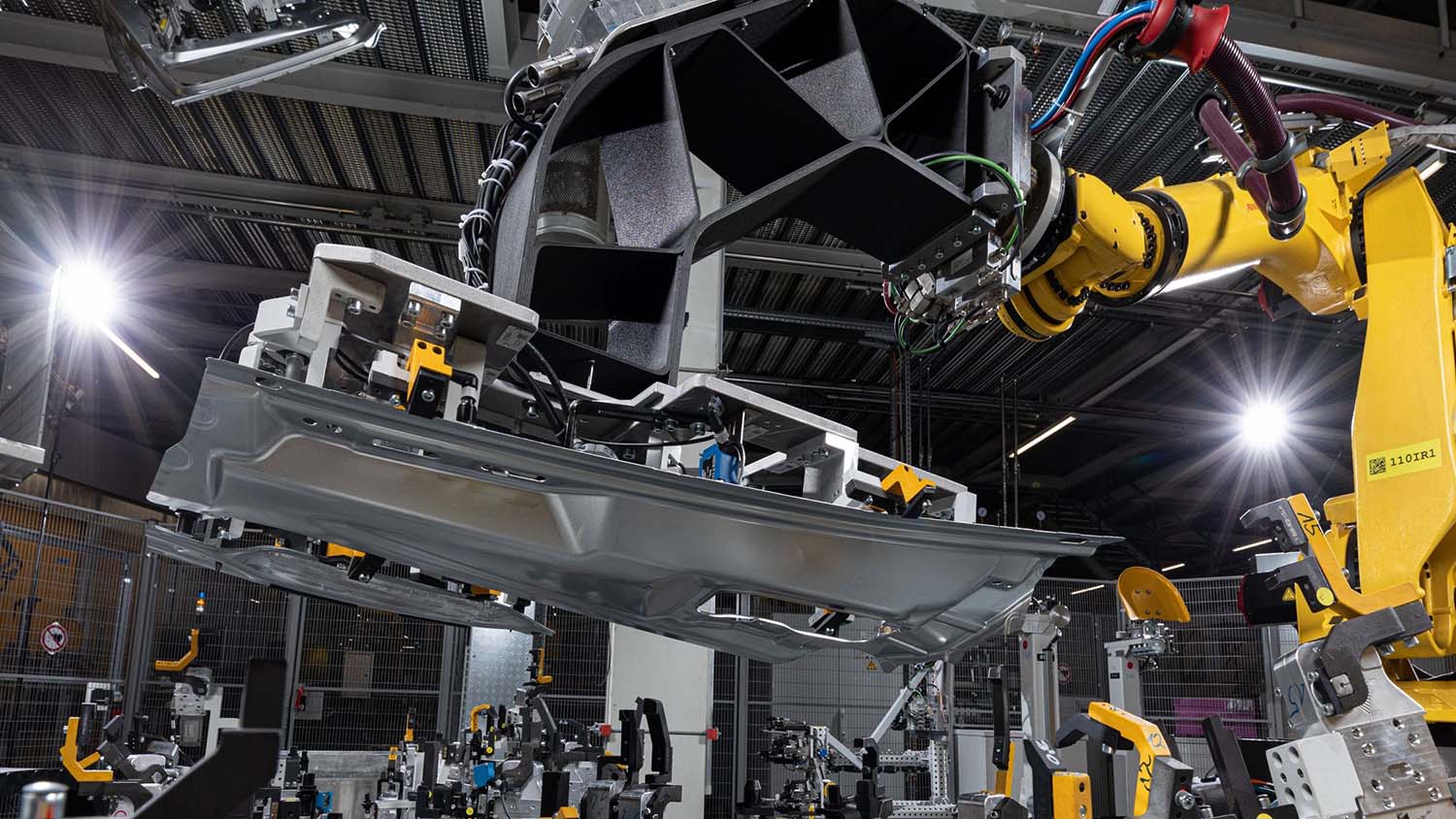
The BMW Group also employs grippers produced using the 3D printing process in chassis construction – for example, grippers printed with the LSP process for dealing with doors at BMW Group Plant Regensburg.
“With an optimised bearing structure produced using 3D printing, we were able to increase the rigidity of the gripper when handling door elements at the plant in Regensburg, while at the same time reducing weight. In subsequent projects, it is then possible to use robots with a low bearing capacity, which helps to cut costs,” says Florian Riebel, head of door and flap production in Regensburg.
At BMW Group Plant Munich things are being taken to another level with the assembly of the BMW i4, with a new optimised gripper design being used to move an entire i4 floor assembly. Built from cast aluminium using a 3D printed sand core, even with all the other elements attached it weighs 110Kg, 30 per cent lighter than previous models.
This shift is making it possible to use smaller and lighter heavy-duty lifting robots to perform the same task, boosting savings in equipment outlay, energy requirements and reducing CO2 emissions.
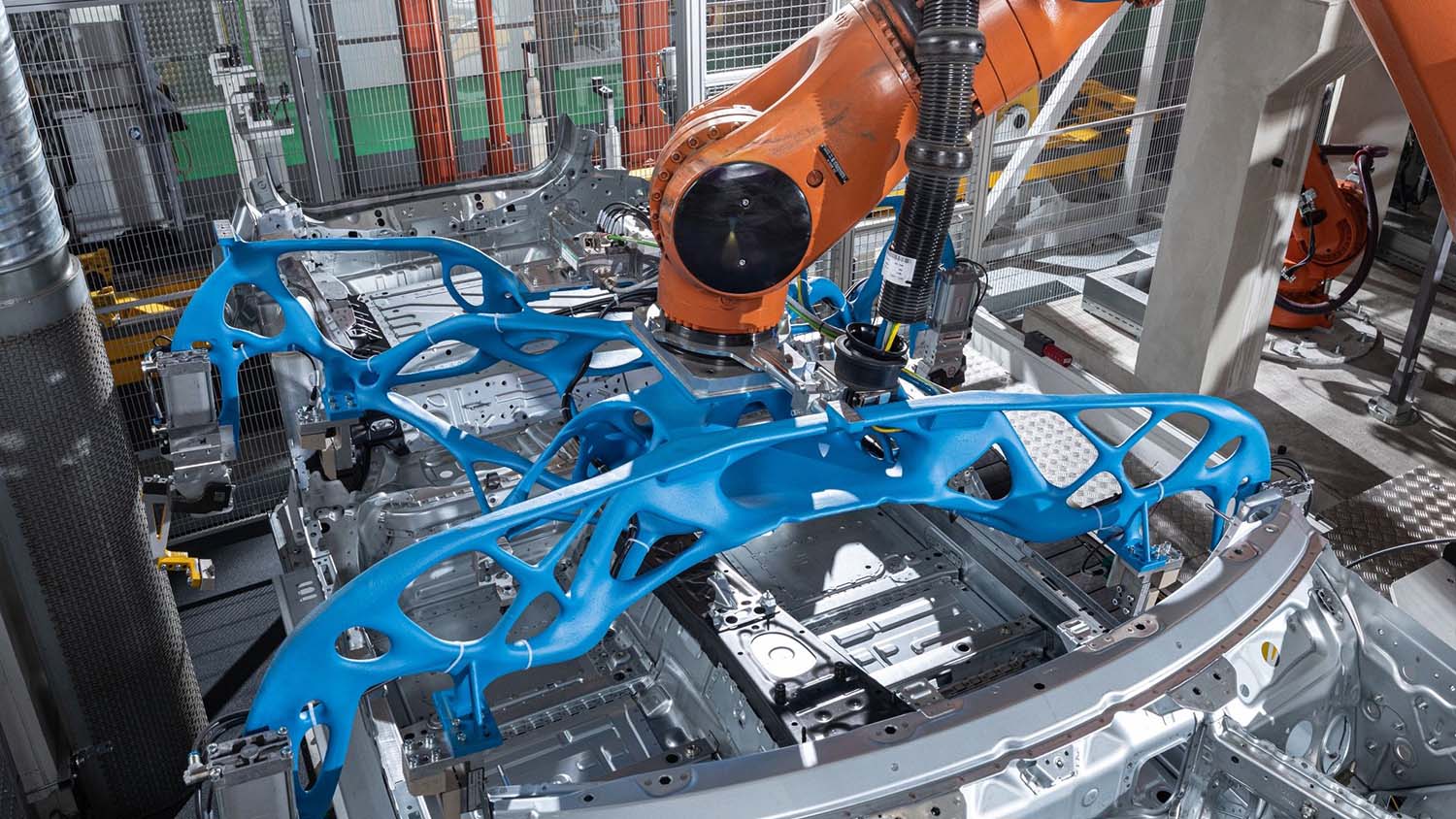
“We use 3D printing to equip our established grippers with individual, printed attachments and are already replacing complete gripper systems with highly-integrated and weight-optimised bearing structures,” said Markus Lehmann, head of plant engineering and robotics at BMW Group Plant Munich.
“When handling the full BMW i4 floor assembly, this allowed us to reduce the weight of the complete gripper by 30 per cent – 50 kg – and thus to extend the service life of our facilities.”
BMW says that the structures are “designed and calculated using special generic software tools, such as Synera” which it uses for ‘algorithm-based’ automated optimisation. BMW’s investment arm, iVentures, has invested in Synera in the past (previously known as Elise).
BMW Group’s Additive Manufacturing Campus in Oberschleißheim, a suburb just north of Munich, is home to a team specialists whose knowledge is then passed on throughout the company. In the case of gripper design, much of the calculation and construction of the bearing structure to be largely automated, and thus fast and efficient, was developed here.