In need of an awe-inspiring showcase of its expertise that would leave a lasting impression, submersibles specialist JFD Global turned to Malcolm Nicholls Limited to produce a scale exhibition model with big impact
An established provider to 35 of the world’s navies, JFD produces equipment that improves safety and preserves life in the event of submarines running into trouble. Heading to DSEI London, one of the world’s biggest trade shows for its industry, the team at JFD planned to launch the company’s latest subsea product, the fourth generation of its submarine rescue system, Agile.
JFD entrusted UK modelmakers and 3D printing bureau Malcolm Nicholls Limited (MNL) to create of a 1:10 scale model of the new Agile, with a brief not merely to showcase the product, but also immerse the audience in the world of the submersible, and in particular, the rescue craft’s ability to lock onto a submarine escape hatch, deep underwater, in order to extract stricken crew.
The first stages of this project involved safe data handling and exchange of CAD, with JFD providing MNL with a mesh exterior model of the craft.
The CAD data allowed MNL to produce detailed renders of its proposal to ensure it fitted the customer’s vision, including an intricate stand and lighting features that would help bring the static display to life.
After careful consideration, the team chose stereolithography (SLA) as the method of manufacturing the parts. Accuracy, superior surface finish and the ability to create the necessary four sections simultaneously made SLA a good fit with the project’s demands.
“JFD wanted to be able to use this scale model for years to come, so as part of the build, we used internal carbon fibre patches to help prevent any long-term sagging to the model, while vacuum casting was utilised to ensure the end portal’s UV stability,” says MNL technical director Ross Nicholls. In this way, MNL was able to avoid a common problem associated with SLA models of this size: distortion.
While alternative technologies, such as selective laser sintering (SLS), were an option, Nicholls says they were ruled out due to rougher surface finishes.
“Opting for SLS would have necessitated extensive post-processing and, crucially, would have extended the project timeline beyond what JFD’s exhibition schedule allowed,” he explains.
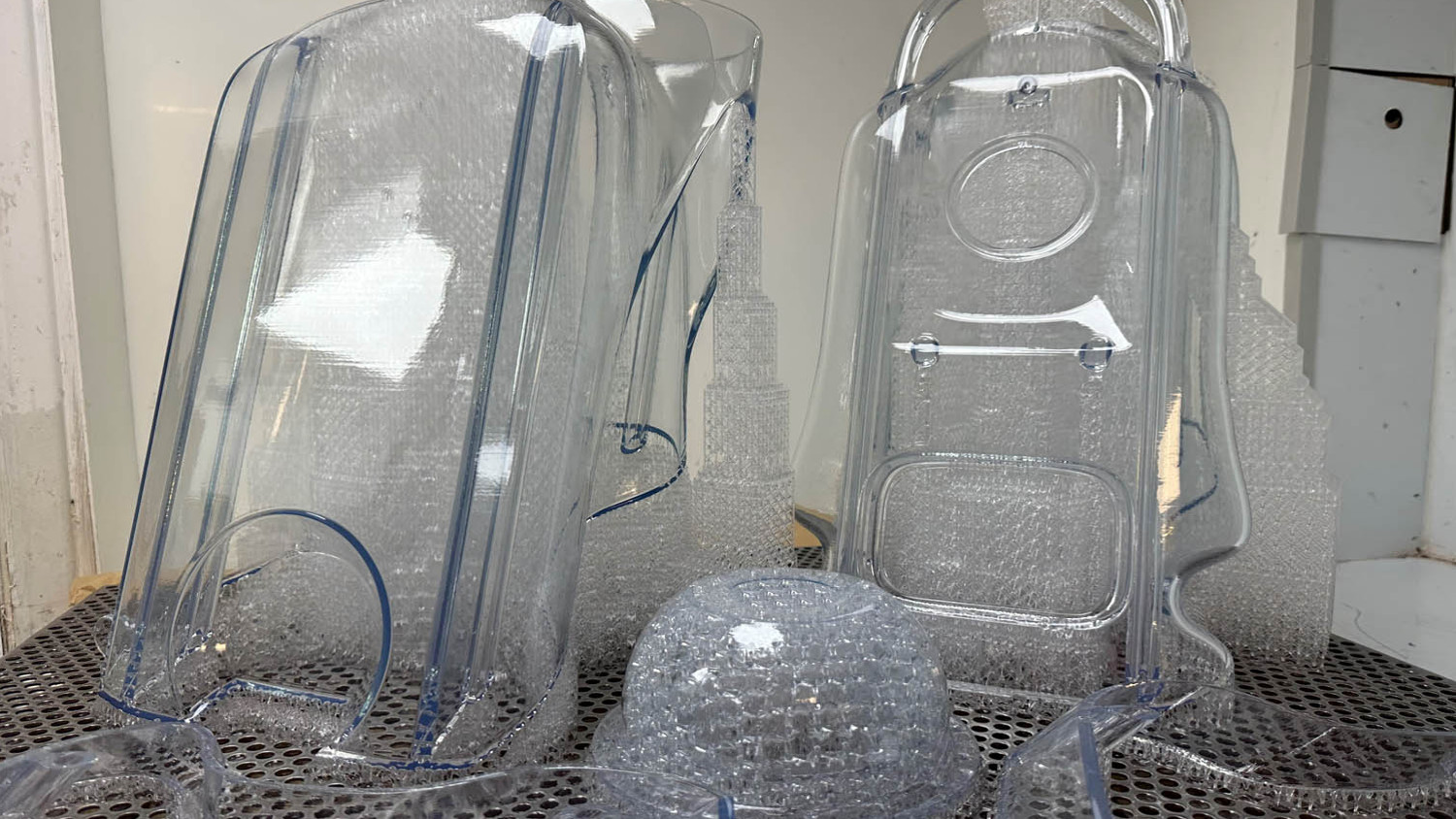
Modifying the 3D CAD model was key to ensuring the model’s accuracy and integrity. The team added strategically placed steel tubes for support, reinforcing the structure and ensuring it could withstand the rigours of being transported to exhibitions around the world.
Lattice supports were added to the CAD to help with the stability of the model, while internal ribs and injecting epoxy resin following post-processing also contributed to the overall strength and longevity of the model.
Additionally, the clear domed viewing portal, a critical component, was carefully vacuum-casted to ensure UV stability, guaranteeing its clarity and durability.
To achieve the required precision and aesthetics, the MNL team opted to use Somos Watershed materials on the company’s largest 3D printer, a Stratasys Neo 800 SLA machine with a 800 x 800 x 600mm build platform. “The choice wasn’t arbitrary; it was driven by the Neo’s remarkable precision, generous build capacity and the material’s exceptional surface-finishing properties,” says Nicholls.
The MNL team painted, assembled and finished the model to an immaculate showroom finish, all within a tight six-week timeframe, providing JFD with a stunning showcase for its new lifesaving vessel.
This article first appeared in DEVELOP3D Magazine
DEVELOP3D is a publication dedicated to product design + development, from concept to manufacture and the technologies behind it all.
To receive the physical publication or digital issue free, as well as exclusive news and offers, subscribe to DEVELOP3D Magazine here