There are well over 300,000 different spare parts for Daimler buses and trucks – a staggering itinerary to keep tabs on, let alone store multiples of physically in warehouses around the world.
Even more so, it means that parts for long since discontinued models must be maintained, even when suppliers might have closed decades ago, taking CAD data and tooling to their graves.
While additive manufacturing is often heralded as a solution to all this, the materials, finishes and colours often leave a lot to be desired.
Daimler jumped headlong into tackling this issue in 2016, setting up the subsidiary department: the Centre of Competence 3D-printing.
The key aim was to see whether Selective Laser Sintering (SLS) could stand up to daily production for visible spare parts. The offshoot pulled in expertise from Additive Minds, EOS and DyeMansion, with the entire supply chain defined and evaluated.
Daimler – Big Numbers, Small Runs
It was here that Daimler realised a need for reinvention – for a decentral, on-demand production that allows small volumes.
High quality final products were a must, and the surface quality and colour of the parts had to be in no way inferior to the spare parts produced with injection moulding.
The first attempts had great functional ability, but the parts printed on EOS 3D printers were white, matte, with a rougher surface finish.
It was clear that the 3D printed parts would work, but would need some innovative post-processing to make them applicable for use.
Step-up Dyemansion, with its print-to-production workflow.
Consisting of the blasting systems Powershot C and Powershot S, and delivering colour to white polyamide parts with its DM60 system.
Through the treatment with the PolyShot Surfacing in the Powershot S the SLS parts get their injection moulded-like surface, without effecting the part structure or geometry, saving the faux-leather surface of the parts.
Colour posed the greatest predicament – matching three special Daimler Buses shades of grey already in use throughout the brand.
Using the original injection moulded parts as colour samples for the DM Colour Matching, three colour shades of grey were developed that achieve the same colour values on EOS PA2200 as on the original parts.
Dyemansion’s technology allowed for its proprietary DeepDye colouring, applied via the DM60 using colour cartridges.
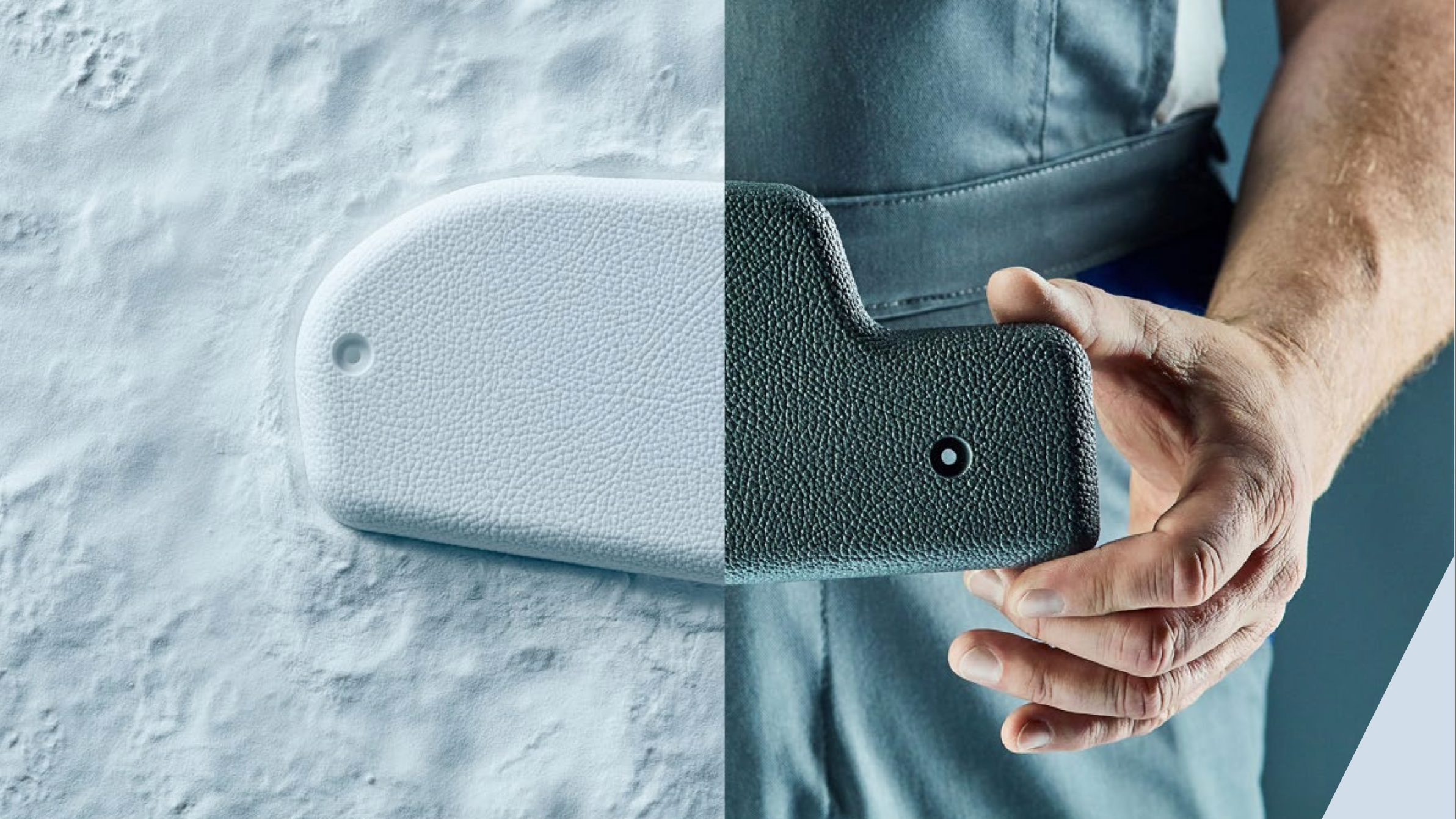
In contrast to spray painting, the paint is absorbed into the component, so does not form another layer on the part, which also contributes to preserving the textures.
After the development, all process parameters are traceable. All defined parameters, such as batch size, colour recipe or surface finish), are stored on the colour cartridge using RFID chips.
The individual recipes are stored and can be retrieved and ordered again and again – a possibility for every colour and every physical colour sample.
Through the successful implementation of industrial 3D-printing, Daimler Buses’ spare parts can now be produced on-demand when and where they are needed – keeping vehicles on the road with fewer delays.