After a two years delay due to Covid restrictions, Additive Industries has opened its first UK-based process and application development centre in Filton, Gloucestershire. At the opening event representatives and experts gathered to see its new facilities and to share views on the future of the aerospace industry
Famous for having hosted the development and production of the Concorde aeroplane in the 1960s and 70s, Filton is today home to a growing additive manufacturing hub, featuring aerospace and engineering industry leaders such as Airbus, Rolls-Royce, and GKN. And it’s in Filton that Additive Industries has decided to open its first UK process and development centre.
Mark Beard, Additive Industries’ global director of process and application development and general manager of the centre, cut the opening ribbon accompanied by Raymond Clinton, associate director of the science and technology office at NASA, who joined remotely from the US, and Thoms Rohr, head of materials and processes section at the European Space Agency.
To inaugurate the brand new development centre, which was delayed for two years due to Covid restrictions, Additive Industries invited representatives from the space and AM industry to showcase the facility and its new MetalFABG2 3D printer, which the company claims offers twice the productivity compared to previous models thanks to an optimised gas flow and heat management, updated process parameters and automated beam quality measurements.
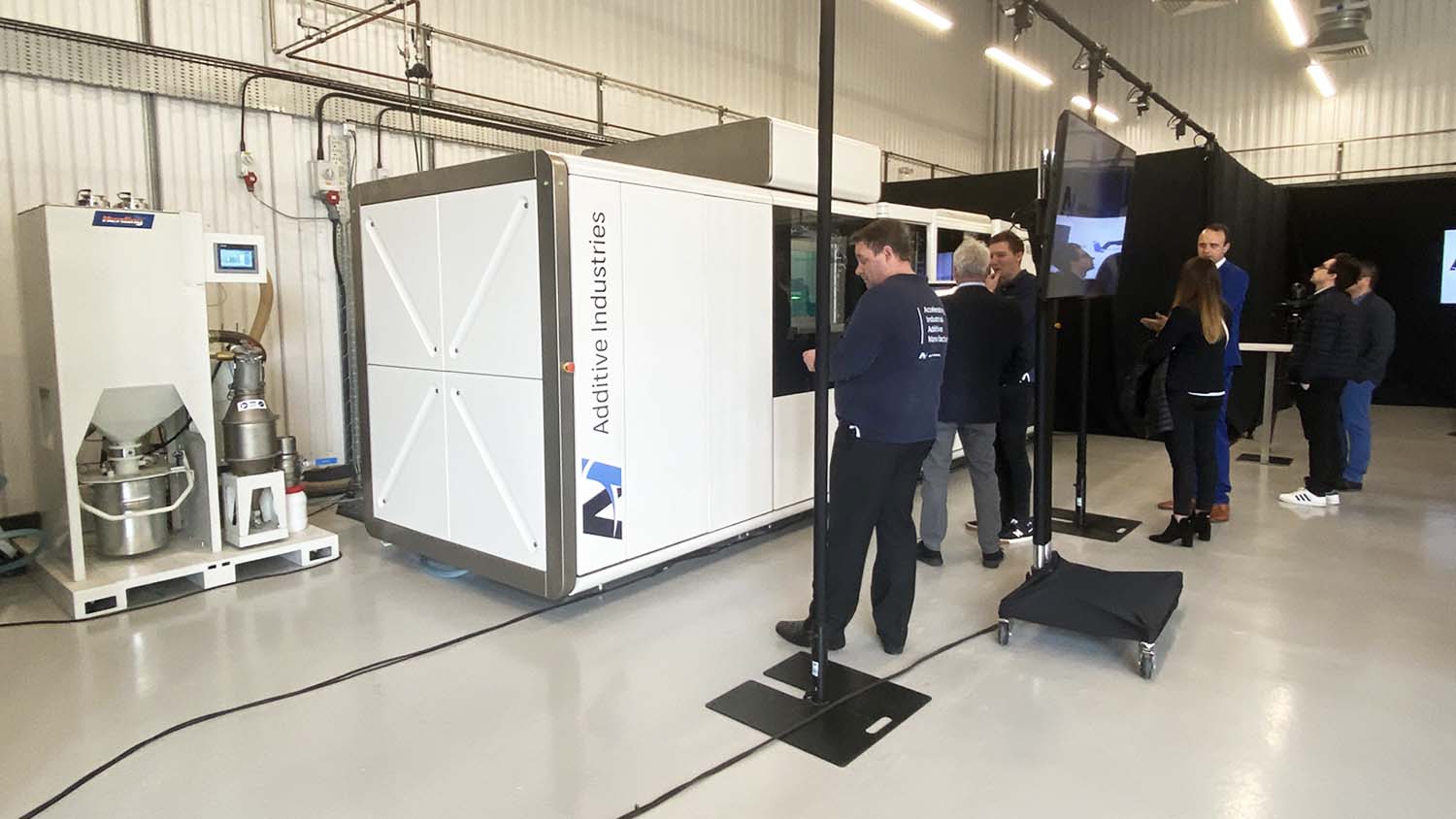
The new centre is part of a global network, with locations in Eindhoven, Los Angeles and Singapore, where Additive Industries says it is focused on enabling customers and partners to realise the full potential of metal AM solutions, provide professional services, and guide customers through the development process, including design for AM, process development, materials development and post-processing.
“Filton has a long and successful history in advanced engineering, aerospace and defence, driven by knowledge, innovation, enterprise, and excellence,” said Beard. “Therefore, it is the perfect location for our new centre.
“We are strongly convinced that additive manufacturing is increasingly important for the aerospace and defence industry. Working here in the heart of this industry, we can collaborate firsthand with all parties and by doing so advance our technology on a daily basis.”
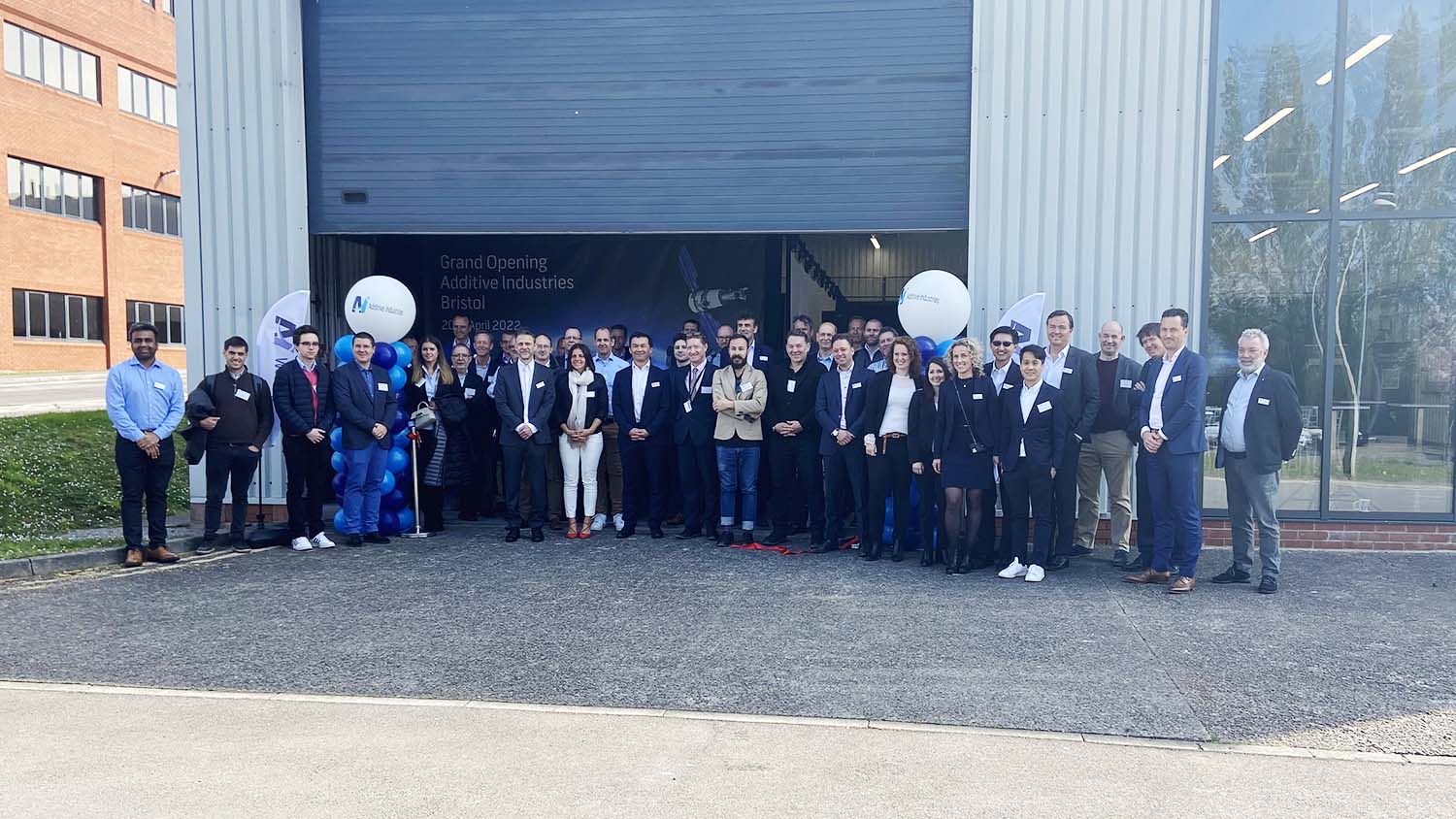
“In the aerospace and defence industry, metal additive manufacturing is key enabler and is now competing with traditional manufacturing processes, for example, high-value assemblies of machined and cast components,” added Additive Industries CEO Ian Howe.
“In particular, in rocket and aviation engine development 3D printing is now being used to manufacture certified, high tolerance parts in these demanding applications while reducing costs. We are looking forward to working with our customers and partners at Filton and around the world to further advance our technology and their applications, in order to provide component solutions with the optimum performance at the right price points to boost efficiency and effectiveness.”
Lift Off
AM experts, engineers and representatives of the space industry presented at the launch event, started by Mike Curtis Rouse, head of access to space at Satellite Application Catapult, who took to the stage with a session titled ‘Connecting parts without screws and joints’.
Curtis-Rouse called for a member of the audience on stage for a demonstration, asking them to assemble a LEGO man while wearing thick gloves. The point was that astronauts work in very complicated circumstances, and something that might seem easy on the earth, such as the assembly and disassembly of LEGO, is not as easy in space. Additionally, they often wear very thick gloves that prevent them from having the same dexterity they would have on earth. “Imagine doing this upside down, and maybe while holding your breath!” he said.
This is just one of the many reasons Curtis-Rouse believes that 3D Printing is the ideal technology to be employed for manufacturing aircraft and rockets. Curtis-Rouse went on to explain various advantages of employing AM in aerospace and asked the audience to talk about the application of this technology in their fields, which varied from automotive to nuclear.
The initial workshop was followed by a solid lineup of presentations in which engineering, representative of the aerospace industry and academics working in the aerospace field, had a chance to illustrate to the audience the projects they are developing.
The CEO of LIA Aerospace Dan Etenberg took the stage with a presentation titled ‘Additive manufacturing as leveraging technology for space propulsion systems.’ The start-up, based between the UK and Argentina, aims to produce eco-friendly and reusable rockets to tackle the issue of space debris. Etenberg said, LIA Aerospace is currently developing propulsion systems for spacecraft, launch vehicles, and landers for future interplanetary missions, keeping in mind the need for storable, green, and non-toxic propulsion systems. Etenberg said that cost-effective technologies with short lead times such as AM, will play a central part in building future space infrastructure.
Aaron Knoll, head of the Imperial Plasma Propulsion Laboratory, part of the Department of Aeronautics at the Imperial College, presented a novel innovative approach to spacecraft micro propulsion his Ph.D. team is developing.
“One of the particular challenges when it comes to space propulsion is the growing number of spacecraft and the use of propulsion for those spacecraft in earth orbit,” said Knoll. “So for right now we have about 4000 satellites in earth orbit and this is expected to grow to over 10,000 in the next 10 years. What this means is that in the next 10 years, we’re going to have more spacecraft launch into space than in the entirety of human history.”
As Knoll explained, the major driver of these satellites are propulsion systems themselves. Producing propellents is extremely energy-intensive and expensive, so it won’t be sustainable in future years.
“So the role that I see for the research involving space or culture is to continue to allow sustainable access to space without causing adverse environmental impacts to our lives,” continued Knoll. “Ideally, we want to find means of propelling our spacecraft that aren’t reliant on materials that we’re taking from our planet.”
The research group led by Knoll is developing an architecture that uses water as a propellant for electric propulsion and chemical propulsion. “This aims at changing the way people construct new satellite architectures, which we consider to be much more future proof,” said Knoll.
The group is currently developing two different chemical propulsion technologies – an Iridium Catalysed Electrolysis (ICE) thruster, and a small CubeSat variant of the same technology called the ICE-Cube thruster. In each case, several manufacturing methods have been employed such as MEMS, magnetron sputtering, EDM cutting, and diffusion bonding processes.
Contrarily to other presenters, Knoll explained that he and his team came to the conclusion that AM was not the right technology to employ: “The thruster is very, very, very small. We can’t use something like a conventional additive manufacturing method, because we can never achieve that sort of feature.”
Next speaker on stage was Nigel Robinson, COO at the Digital Manufacturing Centre, who brought his experience in automotive to make a parallelism between his industry and aerospace with a session titled ‘From the race track into space’.
He was followed by Andy Bushby, CTO of Ultima Forma and professor of materials science at Queen Mary University, presenting his work in building metallic engineering components using a novel additive manufacturing electrodeposition process called electroforming.
To finish the round of presentations were Thomas Rohr presenting the ESA advanced manufacturing initiative, and Raymond Clinton, who talked about manufacturing, construction and outfitting on the lunar surface.
The opening event of the new Filton centre was concluded by a panel discussion where all the representatives from the aerospace industry that had presented during the event, shared views and predictions about the future of aerospace, what this expansion might mean for humankind, and the part can AM can play in this development.