For automotive brands such as Groupe PSA’s Peugeot, Citroen and Opel to achieve complete electrification by 2025, thermal impact on vehicle battery life needs to be optimised. DEVELOP3D speaks to Groupe PSA’s engineers about using multiphysics simulation to tackle cooling conundrums
With the announcement in late 2020 that the UK government is to bring forward to 2030 rules banning the sale of new fossil fuel vehicles, the electric vehicle (EV) race is now running at full speed.
Groupe PSA, the second largest car manufacturer in Europe, has already committed to a future of sustainable mobility for its brands, which include Peugeot, Citroen, Opel and Vauxhall. The company’s full range of vehicles is set to be completely electrified by 2025.
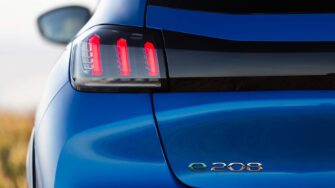
But ‘range anxiety’ remains an important barrier to uptake, so for EVs to meet customer expectations, battery issues must be tackled. And since most EV batteries today come with an 8-year warranty or 160,000km (100,000 miles) drive limit, battery aging is high on the agenda.
Temperature variation is one of the most important factors in battery aging.
High temperatures may allow larger battery capacity, but they drastically shorten battery life. That makes thermal management critical in achieving the perfect balance between capacity and longevity.
In this context, it is crucial for the battery cooling system to be designed in a way that balances other vehicle performance attributes.
That system can’t be too big, as this would impact overall vehicle performance, due to being too heavy, complex, expensive and bad for aerodynamics.
It can’t be too small, as this would put at risk vehicle performance and safety. And this is just one of the huge range of considerations involved in designing cars that successfully combine comfort, driving pleasure, performance and durability.
With all this complexity in mind, leading OEMs have to adapt to new development priorities – and adopt technologies that help them do so. At Groupe PSA, team leader of battery system modelling and design Angelo Greco has been leading the company’s work in the fields of functional design analysis and multiphysics modelling.
“The main challenge is that we can’t make proper battery design analysis and evaluation without integrating it in the complete vehicle architecture,” he says.
“It is very complex, because you have to take into account its multiphysics nature, including electrical, thermal, cooling and control parts in the same model. It is not an easy task and that’s why we chose Simcenter Amesim to work on that engineering challenge.”
Multilevel modelling and multiphysics simulations have become pivotal in evaluating the impact of architecture design on key performance attributes and anticipating control strategies validation, he says.
“On top of those engineering constraints, we have strict development time requirements to maintain a competitive time-to-market,” says Greco. “We have to be very agile.”
Sometimes a component or model needs to be changed quickly to adapt to new requirements from the supplier It’s the versatility of multiphysics models that is key to assessing the impact of changes in performance levels.
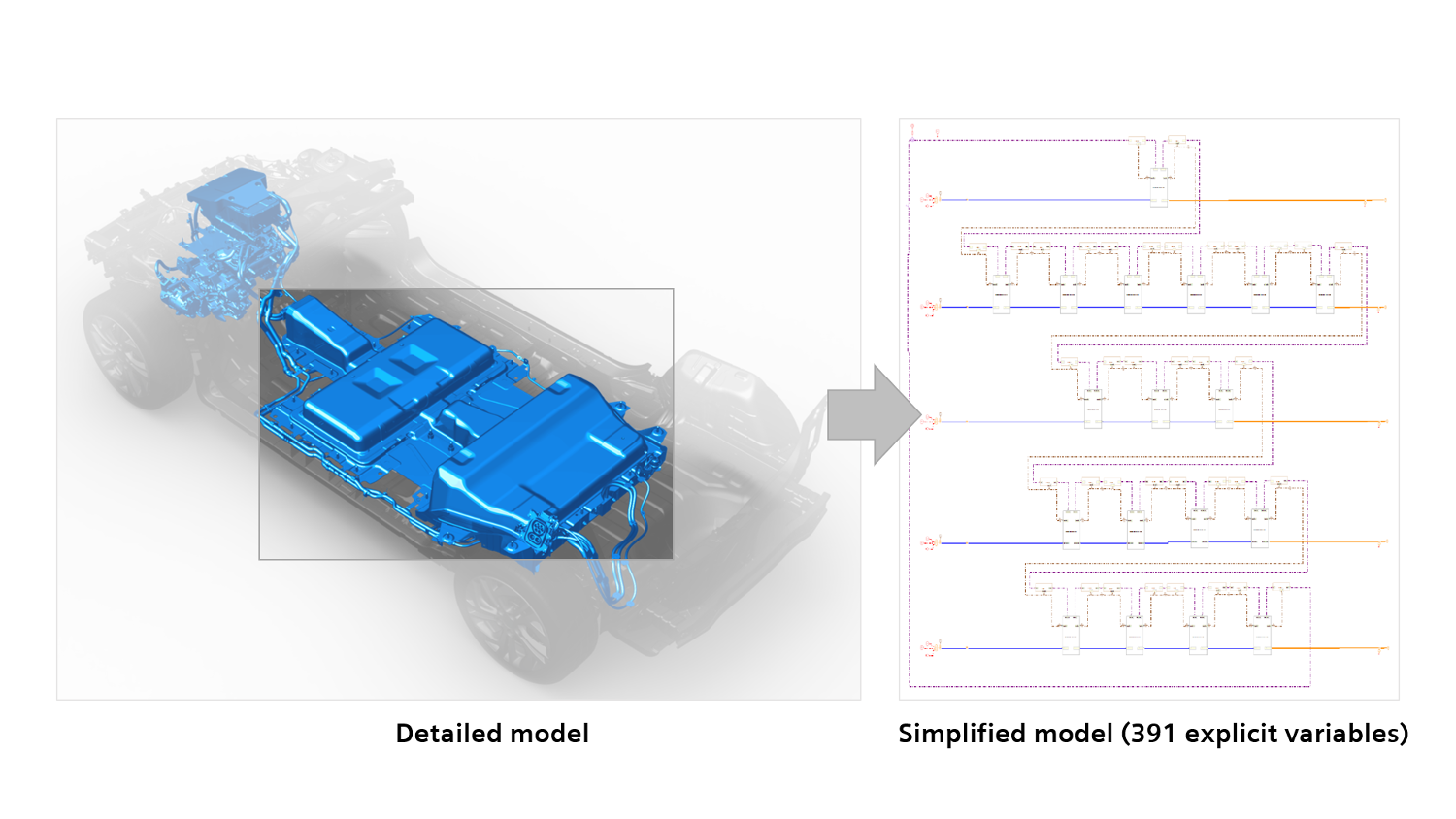
Hot stuff
To analyse battery thermal management, Greco has to understand how a battery is designed by Groupe PSA Peugeot Citroen suppliers. Tier suppliers usually size and develop the battery module by considering the worst use-case conditions to ensure that the EV works under any conditions and that the battery life range aligns with the 8-year warranty and meets regulation requirements.
Nevertheless, the battery is often oversized and so is the cooling system. Consequently, it requires more development time, but also reduces overall vehicle performance. This can definitely be optimised, says Greco.
“Having access to simulation enables PSA Peugeot Citroen to rapidly analyse battery performance and its thermal management. Further, it enables the firm to investigate alternative battery designs, validate them virtually and to make sure they meet the required levels of performance without compromising safety.”
Greco explains that the only way to reach desired optimisation levels is to use multiphysics and dynamic models with the accuracy of 3D computation and the flexibility of 1D simulation.
“It has been fundamental to find a way to transcribe a 3D thermal and hydraulic model into a 1D model with the addition of the electrical part, in order to evaluate the battery thermal management in a reliable way early in the development cycle.”
To succeed, Greco developed a methodology to develop a 1D model of the battery from a 3D thermal model using a nodes network. He reached similar results to the 3D thermal-hydraulic modelling, but in shorter runtimes.
“We used Simcenter Amesim to develop this approach that helped us not only save simulation run times, but also assess the dynamic thermal management of the battery versus a static assessment that we usually achieved using 3D thermal model for the battery coupled to a 3D CFD (cooling plate) model.”
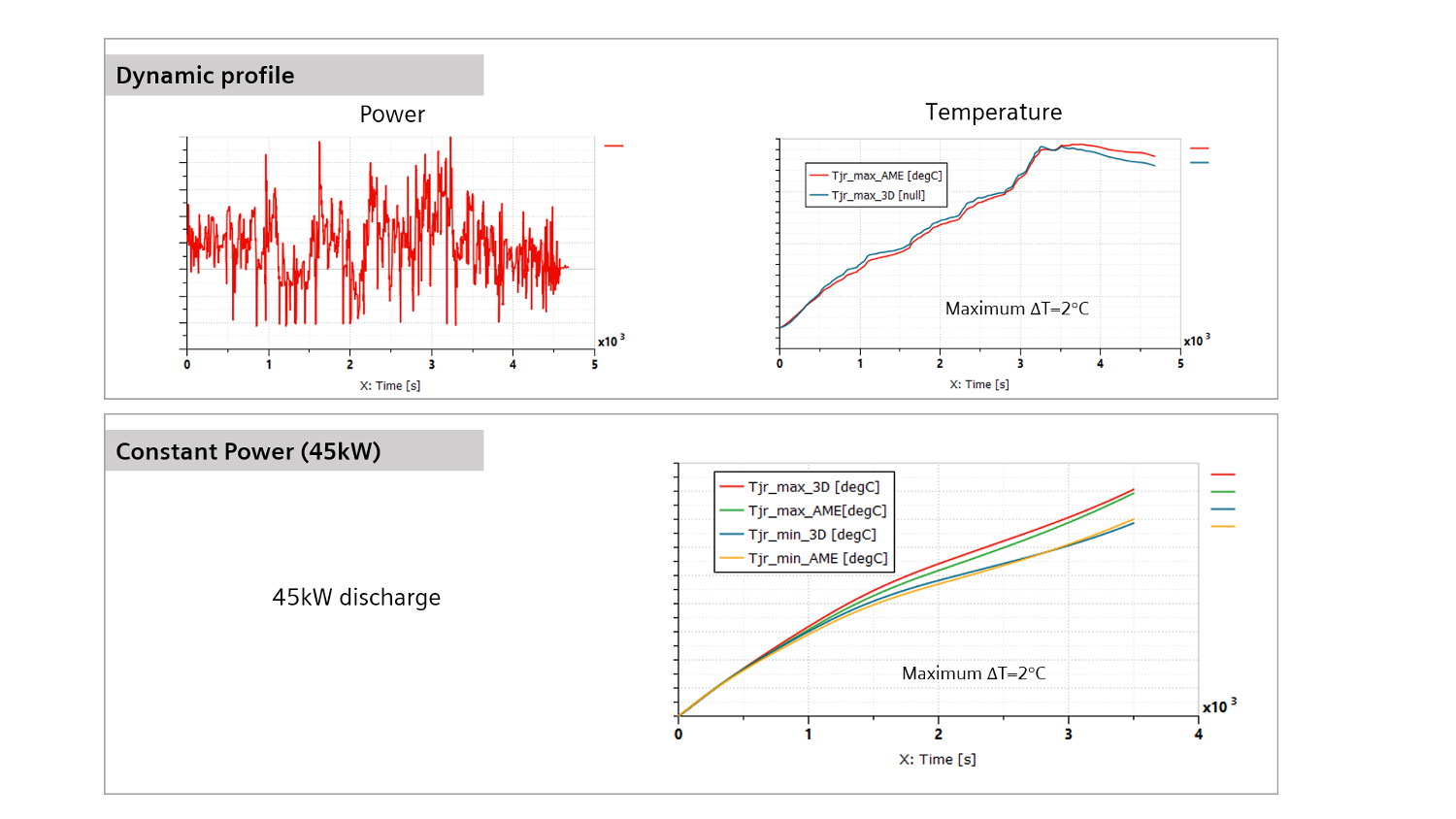
By using the models built with Simcenter Amesim, Greco claims that his team has been able to run simulations twice as fast, on average, compared to the standard procedure.
“From the battery model provided by the supplier using the 3D-to-1D simulation approach, I’ve been able to show the battery could have an overall thermal resistance of 0.9K/W (worst case), instead of the 1.8K/W proposed by the supplier.”
This improved methodology enables the team to make decisions earlier in the development cycle, defining a battery architecture that will enable Groupe PSA to power forward in the race for electrification.