Boxer software has launched its latest simulation software Boxergeom for through-life performance for prediction of components from erosion, particulate build-up and potential blockage, allowing users to optimise designs or model damage.
The software looks to predict in-service component performance, lifespan, and determine optimal operating conditions, all in an entirely topology-independent and unconstrained manner, helping judge potential damage to impeller designs or valves.
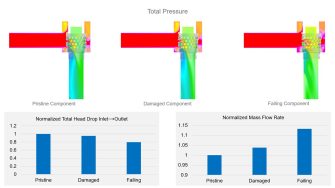
Developed by Cambridge Flow Solutions, Boxer software allows users to quickly mesh geometry before applying simulation data to deform and generate new geometry.
This creates a digital twin of a part, with analysis helping to understand the performance of a component or system during service and not simply in its pristine, manufactured condition.
Boxergeom can alter a geometric surface in response to an arbitrary surface scalar value such as temperature, pressure, x-location, particle impact frequency and erosion rate.
The surface can be made to move outward (add material) or inward (remove material) to model particle build-up, icing, erosion or burn-out in response to the local scalar value.
“With Boxergeom, we now can allow users to get a better idea of what is happening to components during service and how this affects their performance,” said Cambridge Flow Solutions CEO Bill Dawes.