Looking to break into a new industry sector, Reach Surgical aimed to enhance their new product’s ergonomics to beat the competition, turning to design studio IDC to perform the procedure
Ultrasonic shears are a popular choice for surgeons performing minimally invasive surgery, allowing them to cut and seal blood vessels with a single action. But when used over long periods, ergonomics, comfort and fine motor interactions become increasingly important.
Entering the ultrasonic shears market for the first time, Chinese clinical equipment company Reach Surgical turned to London design studio IDC to enhance the usability of its technology.
An initial challenge for the IDC team was to overcome strong market acceptance of a competitor’s product by introducing a genuinely better alternative. The main objective was to optimise the ergonomics of the new ultrasonic shears, since Reach Surgical had already applied its own extensive medical knowhow to developing the technology itself, which can cut through and seal closed a 7mm blood vessel.
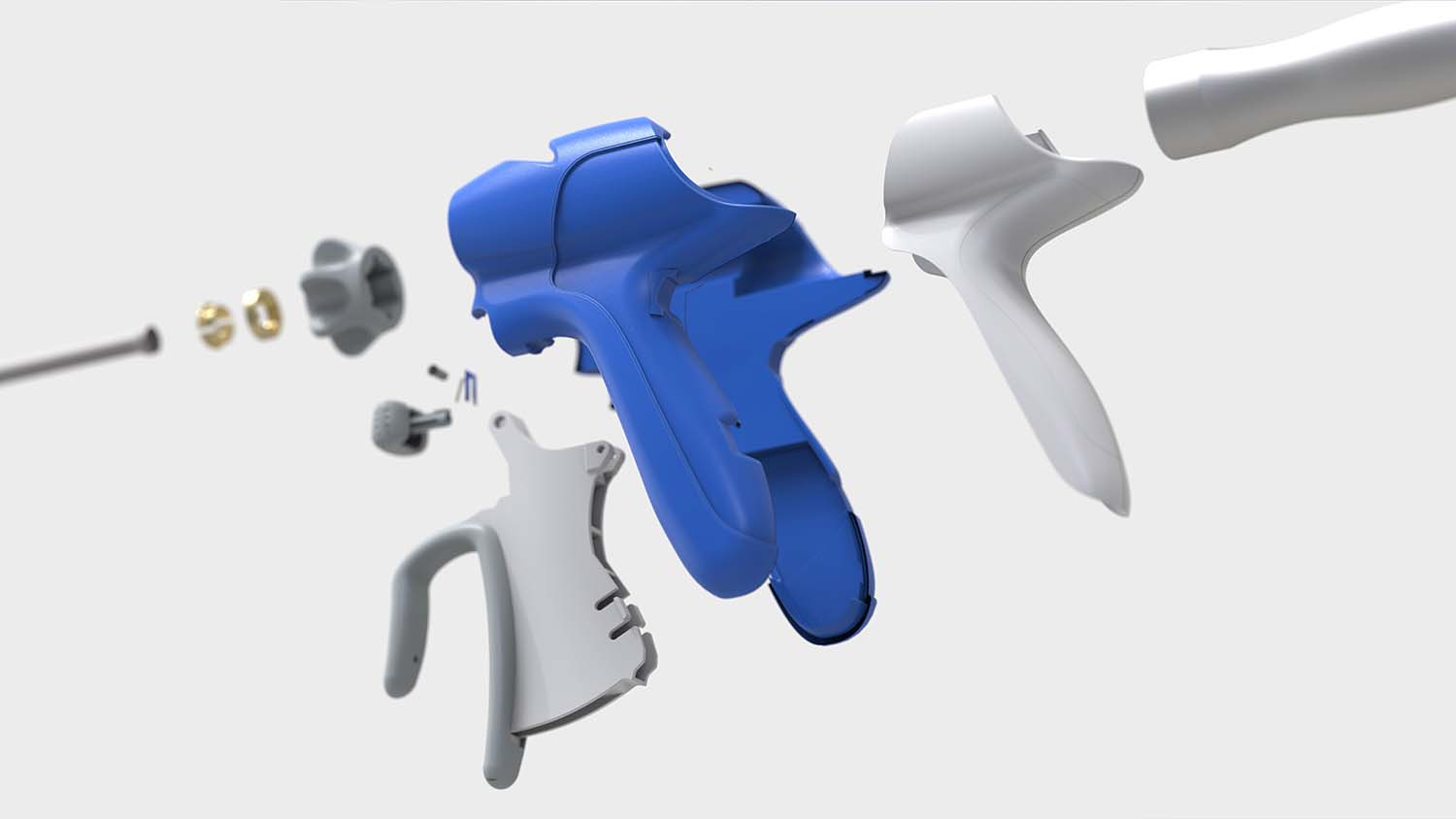
The team at IDC immediately set to work, breaking down the user interaction characteristics and processes involved in working with competing shears and highlighting nine elements as candidates for improvement, including the trigger, handle, buttons and knobs.
“This project was very much co-developed alongside surgeons,” says IDC design director Nick Chubb. “We used a mix of analogue and digital sketching techniques to generate ideas and blue foam modelling for early physical testing.”
Chubb explains that the team used Sketchbook Pro on iPads, along with Adobe Photoshop, to generate and explore form and different initial CMF directions, before Luxion Keyshot was brought in to create more polished visuals.
As the concepts were further refined, the design work moved into Solidworks to create modifiable and trackable changes and enable more high-resolution prototype models to be printed using IDC’s in-house FDM 3D printers.
These prototypes could then be tested by surgeons and any suitable modifications or new ideas added to future builds. One key design change derived from this research was the shortening of the trigger’s range. This would reduce fatigue during continuous surgery and enable the design to cater for a large range of hand sizes and preferences.
As progress was made on the design, these models switched to SLA 3D-printed models, allowing for greater detail to be considered. Enhanced usability, in the end, came down to the form of the handle with overmoulded grip detail; the form and material of the trigger; the distance from palm to index controls; and detailed engineering to dictate resistance forces and travel distances of controls.
“The ergonomic development was rigorous and timeconsuming,” says Chubb. “There are some nuances to the surfaces of this handheld instrument that were achieved in Solidworks, which is an interesting challenge, as there’s always more than one way to approach it.”
Combining increased comfort with heightened usability all within the space parameters of a handheld device, the end product can truly be considered cutting-edge.
This article first appeared in DEVELOP3D Magazine
DEVELOP3D is a publication dedicated to product design + development, from concept to manufacture and the technologies behind it all.
To receive the physical publication or digital issue free, as well as exclusive news and offers, subscribe to DEVELOP3D Magazine here