The Astrobotic Peregrine lunar lander may not have succeeded in reaching the Moon, but the lessons learnt from this project will live on in an exciting new age of space exploration, powered by private companies and digital design tools. In the build-up to launch, Stephen Holmes spoke to mission director Sharad Bhaskaran about how simulation technologies from Ansys are critical and why designing for space is so hard.
Trouble can befall even the best-laid plans, and the plans made by Astrobotic for its Peregrine lunar lander may have been some of the most in-depth ever devised. Astrobotic’s goal was to become the first commercial company to successfully land a spacecraft on the lunar surface. Taking off on 8 January 2024 on a United Launch Alliance Vulcan Centaur rocket, Peregrine was due to touch down on the moon’s surface shortly after this article’s publication.
Sadly, some seven hours after the launch, Astrobotic reported that an issue with Peregrine’s propulsion system meant that it was going to run out of the fuel it needed to keep its solar panels oriented toward the sun, making a Moon landing impossible.
Despite the issue, the lander travelled onwards for 10 days and over 238,000 miles from Earth, putting it in line with the moon’s path, before the decision was made to return the vessel to Earth, rather than leave it floating around as an orbiting danger to future space missions.
A controlled re-entry took place on 18 January, when what survived of the craft dropped into the South Pacific ocean, somewhere near ‘spacecraft cemetery’, Point Nemo.
The disappointment is palpable. This was to be the first US craft to touch down on the moon’s surface in over 50 years, carrying 20 payloads, including five from NASA’s Commercial Lunar Payload Services (CLPS) initiative, as well as university and research institution equipment.
Failure is always an intrinsic risk of producing a spacecraft, as Astrobotic Mission Director Sharad Bhaskaran told DEVELOP3D shortly before Peregrine’s launch.
We have to test a lander while it’s still on the ground. It’s the inherent challenge of doing spaceflight. That’s why they say space is hard Sharad Bhaskaran, Astrobotic Mission Director
“The ultimate test is to get into space and see how it performs,” said the 25-year veteran of Lockheed Martin’s NASA activities, who now oversees Astrobotic’s plans for a new era of space missions. “Whereas a car or even a plane? Well, you’ve got to test it many times on the track or in flight, and then tweak it and make adjustments before you can finally commission that particular vehicle.”
Astrobotic doesn’t get that opportunity, he pointed out. “We have to test it on the ground. We just simulate it and that’s part of the process. It’s the inherent challenge of doing spaceflight. That’s why they say space is hard.”
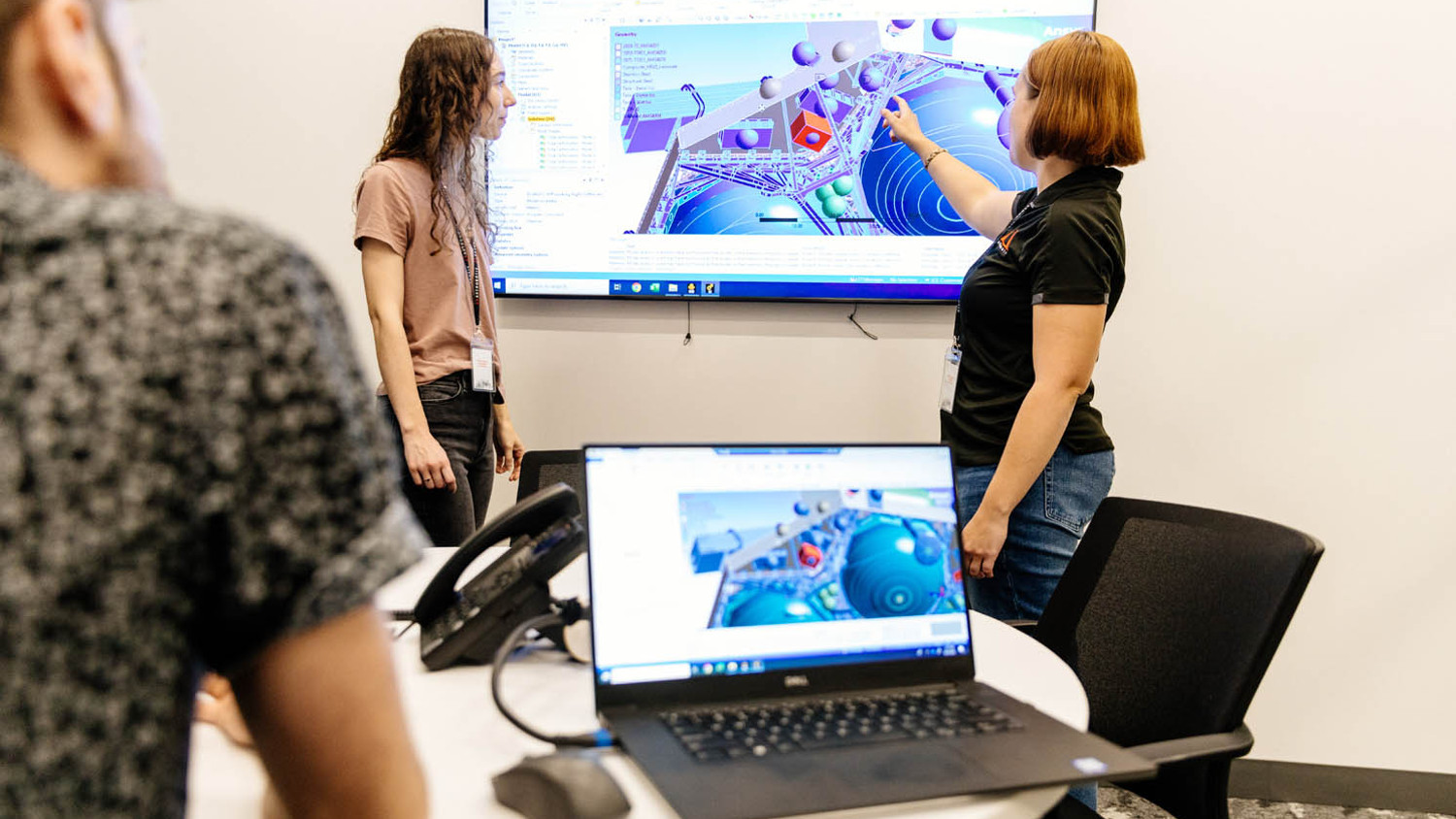
Intense loads
Designing a craft capable of withstanding the intense loadcase scenarios of space flight and landing, while remaining light enough to carry enough fuel for the journey and the cargo onboard places comes with a huge reliance on virtual testing and mission planning software.
Standing 1.9m high and roughly 2.5m across, the boxshaped main body of Peregrine stood on four landing legs. The main structure was composed of aluminium isogrid shear panels and aluminium honeycomb mounting surfaces that divided its insides into four bays.
Its propulsion from five TALOS-150 667-N thrusters got added control from four sets of three 45-N attitude control thrusters to maintain orientation, designed to keep it on the right course and set it up for a gentle moon landing.
The design began to take shape in 2015, but it wasn’t until the NASA CLPS program issued funding for its first ‘lunar delivery service’ in 2019 that Peregrine moved into serious development. A team was built, a launch vehicle sourced, and the process of procuring all the necessary equipment began.
This included Ansys’ suite of multiphysics simulation and mission planning software, which was needed to enhance the spacecraft design and predict performance across all phases of the complex mission from Astrobotic’s headquarters in Pittsburgh, Pennsylvania.
With support from SimuTech Group, an Ansys Elite Channel Partner, engineers used Ansys Mechanical to help evaluate the lander’s performance under extreme structural loads during the launch and transit, and the impact of shock, vibration and fluid transients during powered descent. Ansys Discovery played a part in helping to mature the design to tolerate stress, reduce mass and optimise Peregrine for assembly.
Topology optimisation of the structure to finetune the many lattice parts, helped attain mass savings of nearly 20%, while allowing the team to meet structural durability criteria.
To handle the extreme temperature swings in space, Ansys Thermal Desktop allowed the complex cislunar orbit and trajectory options to be analysed across diverse thermal environments and spacecraft altitudes. This helped the mission to also determine the most suitable launch and landing opportunities.
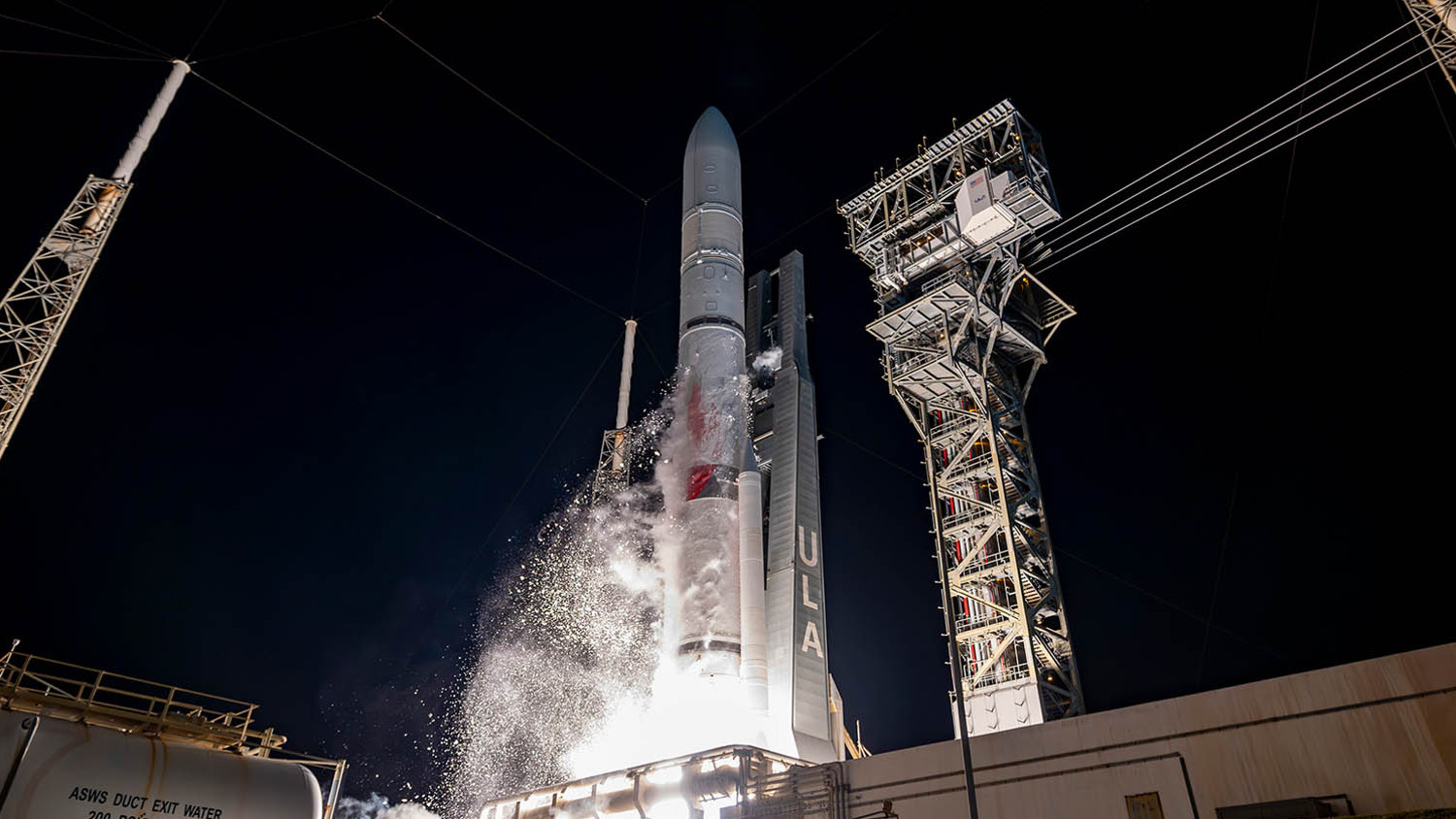
Simulating space
Specific to the space industry, Ansys Systems Tool Kit (STK) was used by engineers working on the project to model complex systems inside a time-dynamic threedimensional simulation. This allowed for Peregrine’s entire system-of-systems to be tested in scenarios the closest they could be to space.
Astrobotic’s flight dynamics team worked alongside experts in this field from Space Exploration Engineering (SEE), an aerospace firm specialising in planning space missions and mission analysis, in order to leverage Ansys’ Digital Mission Engineering software to plan and support the mission.
Peregrine’s mission, trajectory and manoeuvres could all be set out in STK’s sandbox environment, pulling in CAD models and other 3D assets to simulate the entire system-of-systems in action.
“Flying to the Moon is no easy undertaking, because there are innumerable variables and scenarios that must be tested,” says John Carrico Jr, chief technology officer, astrogator and technical advisor at SEE. “Our collaboration with Ansys helps customers like Astrobotic account for cislunar environments through predictively accurate, reliable simulations and real-time guidance from experts with a track record of success.”
Simulation and analysis tools are critical to the development of modern spacecraft, given the cost and timescales required for physical prototyping. At the start of his career, Bhaskaran was an engineer performing finite element analysis for space shuttle payloads.
“The tools were very different back then. And not nearly as evolved, not as capable,” he says. Optimisation wasn’t even an option back then, he adds. “And the integration of different tools across platforms, that’s also something that’s newer.”
The time required to run those models took an age, let alone post-processing the data and tweaking the model to run again.
“Just the output of the team, and the iteration cycles that we can do are far quicker than when I was doing this kind of stuff. It’s tremendous. And in the capability of the tools to model more accurately the physical system that you’re building? I think that’s also huge,” he says.
“The more the mathematical model matches the physical model, the better your analysis results are going to be. And the better your simulation is going to turn out.”
Ultimately, the spacecraft is tested physically on a vibration table, but this is also in part to verify all the digital models that were built and their analysis. Bhaskaran emphasises that it’s imperative to have what’s known as a test-verified model.
“During the design and analysis stages, it gives us confidence that what we’re designing is actually going to work in space and then can be tested. It’s only once we start flying and we’re in space that we find out if all those were accurate.”
We try to carry a very diverse set of payloads with all sorts of mission objectives and these need to be taken into consideration during our pre-flight analyses and simulations Sharad Bhaskaran, Astrobotic Mission Director
Balancing the load
Mass margins are always critical in any spacecraft development, Bhaskaran says. Teams strive to minimise that as much as possible, while still maintaining the strength and the stability necessary to withstand the launch environment and the landing scenario.
Balancing the centre of gravity and mass properties is a tricky business, especially when your craft is essentially a cargo vessel for 20 different loads.
Using analysis tools for this is essential, Bhaskaran explains, as assembling the physical craft is so timeconsuming. “When those specialists map mass properties, when we have the right centre gravity located where we want it to be, and the mass properties are aligned to the launch vehicles requirements, then, if we did our analysis wrong, once we integrate spacecraft – well, it’s kind of too late to start moving things around.”
“We try to carry a very diverse set of payloads that have all sorts of mission objectives,” explains the Mission Chief. “And that could include on-surface-deploy rovers, it could include deploying booms and other sensors that need some sort of field of view. So, all that has to be taken into consideration, because we want to make all our customers successful.”
Nor does he want to see one customer payload adversely impact another customer’s payload, or even the spacecraft itself. One payload, for example, might create a vibration, adversely affecting those next to it.
The Peregrine lander was designed to handle a payload mass capacity of 90kg, filled with the 20 payloads from seven nations and 16 commercial customers.
The cargo came from space agencies, universities, companies and individuals across the world, including the first lunar payload from the UK. Much of it comprised scientific instruments designed to study the lunar exosphere, its thermal properties, hydrogen abundance, magnetic fields and the radiation environment. In addition, the DHL MoonBox contained mementos and messages from over 100,000 individuals around the world, captivated by the pioneering nature of the mission.
With the huge number of considerations involved, including the package sizes, weights and structural robustness, all the payload analysis needed to be finalised well before assembly in order to maintain that centre of gravity and the right mass proportions.
“It’s not just structural. It’s thermal as well,” adds Bhaskaran. “Everything has a thermal tolerance limit. The temperature ranges vary significantly in space, whether you’re in sun or shadow, and so there’s so many considerations on where to put payloads and where to put instruments so that they all survive and ultimately get to the Moon.”
Pittsburgh’s pathfinder
Peregrine was not only the first commercial lander under the CLPS programme to head into space, but also the first to be built in Pittsburgh – a city better known for its bluecollar steel industry.
The lander included parts manufactured by hundreds of suppliers from across the US, including 184 companies in Pennsylvania alone.
Astrobotics’ headquarters include the next-door Moonshot museum, the only museum in the world to focus exclusively on career and community readiness for the 21st century space industry.
From inside the museum space, visitors can look through large windows and watch activity in the clean room as the landers are built. “People are now looking at our second mission, Griffin, being assembled. It’s getting a lot more people connected with the process, which normally isn’t that visible to the public,” says Bhaskaran.
“A lot of people have never seen this happen before. They’ve never seen a spacecraft, even. Here they are able to see close-up how it’s done, and hopefully that will motivate and excite kids to pursue careers in these types of fields.”
Regardless of the setback with Peregrine, Astrobotic’s lunar exploration efforts will continue with the launch of Griffin Mission One later this year. Griffin, the largest lunar lander since the Apollo lunar module, will carry NASA’s Volatiles Investigating Polar Exploration Rover (VIPER) to the south pole of the Moon, in order to search for frozen water.
Peregrine may not have made it to the Moon’s surface, but in more ways than one, it was a marvel of engineering that will act as a pathfinder for the next age of space exploration.
This article first appeared in DEVELOP3D Magazine
DEVELOP3D is a publication dedicated to product design + development, from concept to manufacture and the technologies behind it all.
To receive the physical publication or digital issue free, as well as exclusive news and offers, subscribe to DEVELOP3D Magazine here