Additive manufacturing at an industrial scale, despite the hype, is still in its infancy. We asked six industry experts for their thoughts on what’s holding back uptake, and what needs to happen to put additive manufacturing on a par with other manufacturing methods
Bart Van Der Schueren, Chief Technology Officer – Materialise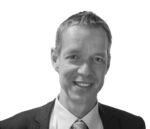
Should the STL file format continue to be the standard for additive?
It is indeed interesting to note that STL files are still used a lot in our industry. This is most probably because of the solid format, where few things can go wrong. As long as one wants to exchange geometrical information for printing, STL suffices.
Still, we believe that it makes a lot of sense to enrich the STL mesh information. This is why Materialise has been playing a leading role in recent years in the definition and development of the 3MF file format.
While still being a mesh representation of the parts, 3MF stands for a seriously enriched format that contains much more information on the actual part than just the geometrical part description.
Also, parametric CAD formats are gaining importance. Not just as more and more CAD designs are used as basis for volume AM production, but also to maintain a link to CAM post-processing steps, following the print process.
That is why Magics not only accepts a multitude of CAD formats as input, but also enables a STEP workflow to always show the differences between nominal design and additive manufacturing (AM) specific alterations, and track any rotations or translations performed when preparing the AM build, conveying these to the CAM engineer; for example, for post-print CNC or CMM steps.
There are over 50 metal 3D printing OEMs active in the market today. Which technology do you see as being the leader in that sector over the next decade, and what will drive that?
There are many metal 3D printing OEMs active, using several different technologies: binder jetting, laser powder bed fusion, electron beam powder bed fusion, direct energy deposition, to name a few.
We believe that each of these technologies has its own merits and will have its own market position. So, we don’t want to put one or the other technology forward as the leader.
We’d rather believe that the current drive by the OEMs to make metal 3D printers better performing; to increase the size and complexity of components that can be printed; to expand the choice of metals; and to improve the repeatability and predictability of the output, will mean that metal 3D printing will thrive in the next decade and will be used on a much larger scale in the industry.
materialise.com
Christoph Erhardt, Metal 3DP Manufacturing Manager – Protolabs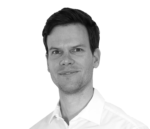
Repeatability – between machines and even between batches – is a huge problem, especially in metals additive manufacturing. What might be done to solve this?
Firstly, at Protolabs, we are qualifying parts on a dedicated system, so we don’t switch parts between, for example, an EOS and a Concept Laser System.
Once we’ve defined a system, we qualify a certain material with our printing parameters to be as robust as possible. This means we can achieve the same mechanical properties and accuracy over the complete build.
The last stage would be a defined build orientation, which leads to optimum part quality and covers surface roughness and detail resolution, for instance.
With these three topics in mind – qualified machine, qualified printing parameter and locked build orientation – we are able to offer customers from every manufacturing sector imaginable a high repeatability that is at least comparable to a classic CNC machine.
What does the additive industry really need in order to step up to production-grade levels?
We know that we can deliver parts that meet all production requirements when it comes to mechanical properties and accuracy.
However, where we have traditionally struggled is when we talk to customers about higher quantities (in multiples of thousands) and being able to meet their pricing requirements.
It works in different fields when we have extremely complex parts or we’re talking about a high variety of components – medical being a prime example.
For simple standard parts, it is often too expensive, compared to traditional manufacturing methods, and we need to explore new technologies and ways in which we can reduce the cost.
With this in mind, we are focusing on speeding up the process with machines (multi-laser/automatisation) or enhancing the complete process to encompass automated finishing and improved build preparation.
protolabs.com
Ben Schrauwen, Chief Technology Officer – Oqton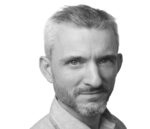
There are over 50 metal 3D printing OEMs active in the market – which technology do you see as being the leader over the next decade, and what will drive that?
Laser melting will probably still remain the workhorse whenever high-precision, bio-compatibility or superior surface finish is required.
For parts with less stringent tolerance constraints, or ones that will be post-machined, a binder-based process with postsintering will probably become the dominant technology.
What does the additive industry really need to step up to production-grade levels?
On the hardware front, prices of machines and materials need to keep coming down, and precise control of the complete process is key to improving reliability and reproducibility – the main drivers in a production set-up.
Furthermore, a software platform focused on production, such as Oqton FactoryOS, can significantly improve the utilisation of equipment and reduce engineering costs and mistakes, thanks to its AI-assisted workflow automation.
We have seen up to 50% reductions in part cost, purely from using an integrated production software platform.
oqton.com
Shai Terem, Chief Executive Officer – Markforged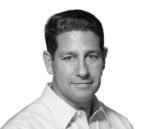
Covid-19 has shown how fragile global supply chains can be. Is additive making inroads into reshoring manufacturing? What will it take to make this happen?
The pandemic has proved that additive manufacturing must play an important role for manufacturers that hope to thrive during periods of uncertainty.
As we saw manufacturing activity plunge, 3D printing levels recovered much faster than other means.
In the beginning, there were big drops as we saw Europe and Asia go into full lockdown, but then we saw a quick bounce-back, with stories of customers bringing printers home and figuring out how to return to essential work.
By using additive manufacturing, manufacturers were able to rapidly engineer solutions that shortened their response time to problems.
As international supply chains continue to strain while we battle the virus, we’re seeing manufacturers want more control over their supply chains. They’re not necessarily reshoring their entire supply chains, but they are looking for ways to make those supply chains more resilient.
Whether they’re sourcing parts from China or the CNC shop a few states over, it’s clear that additive is part of the strategy for the most successful manufacturers.
Repeatability – between machines and even batches – is a huge problem, especially in metals. How might this be solved?
To me, this comes down to three steps:
Step 1: Regardless of what kind of printer you are using, you need to design for the process. Learning how to design is such an important first step.
Step 2: Test, test and test again. AM manufacturers need to sweat the printing details, so our customers can focus on running their operations. We obsess over reliability to make sure our machines run the same way every time under the rigorous challenges of a factory floor.
Step 3: Bring in the power of smart technology. Sensors and software can help to make printers smarter and capable of self-correction.
For example, at Markforged we’ve baked automatic calibration into our printers by combining software with scanners, allowing users to quickly and easily check if a part is within tolerance without the need for additional clunky and expensive equipment.
markforged.com
Yann Rageul Emea, Head of Manufacturing – Stratasys
Should the STL file format continue to be the standard for additive?
The STL file is an increasingly dated file format that costs you colour, resolution and especially, time.
Increasingly sophisticated 3D printers can take advantage of a lot more information than that. The right solution is 3MF.
This XML-based open-standard data format is kind of like next-gen STL. It holds all the information – not just surfaces, but also textures, materials, colours and mesh.
Plus, it is increasingly supported by leading applications like Luxion Keyshot and Solidworks.
It makes it much faster and easier to get the most out of multi-colour, multi-material 3D printers.
How long until AM rises out of Gartner’s Trough of Disillusionment on the Hype Cycle – and what will it take?
Momentum for additive manufacturing was accelerating even before COVID-19 arrived, but the disruption caused by the pandemic has made the technology’s benefits even clearer.
This was evidenced in the way Paris hospitals invested in 60 Stratasys 3D printers to create spare parts in-house; automakers were using 3D printing to re-tool production lines quickly to assemble ventilators; and scores of organisations around the world were helping meet urgent needs for things like PPE by putting spare 3D printing capacity to work.
Manufacturers recognise that the next disruption – be it from climate change, competition, or trade war – is inevitable, and they want to be able to better manage uncertainty.
The agility and efficiency of additive manufacturing, when combined with continued technological innovation, is already helping move it out of the lab and onto the factory floor.
In fact, our estimates are that the manufacturing segment of the 3D printing market will exceed $25 billion by 2025, up from less than $3 billion in 2015.
To achieve this growth, a combination of highperformance hardware that offers repeatability, accuracy and reliability and connectivity for a fully digitalised inventory will be key.
stratasys.com
Duann Scott, VP of Marketing – nTopology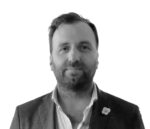
Should the STL file format continue to be the standard for additive?
At nTopology, we are very much advocates of using the best data communication for a given situation. We do not believe there is one file format that covers every requirement, especially not STL.
We are focusing on using the 3MF file format and adoption of extensions like the Beam Lattice and are very interested in the Volumetric extension to get more information than just geometry to machines.
We also have a lot of customers that export slice stacks direct from nTop to their build preparation software. So it really is a case of finding the best format for the situation.
Unfortunately, we do still have some customers whose machines only accept STL, so of course we support the format, but we would really like to use another format wherever possible.
There are over 50 metal 3D printing OEMs active in the market – which technology do you see as being the leader over the next decade, and what will drive that?
We expect to see some level of consolidation with mergers and acquisitions in the metal additive manufacturing market in the coming years.
I also expect there to be more specialisation of machines optimised for serial production for specific products, like a medical device unit with low Z-height and faster build plate changeover, and more hybrid DED systems with adaptive toolpathing and secondary machining functions on very large parts for aerospace.
ntopology.com