Fastlane Turnstiles are building entrance control experts, designing and manufacturing solutions for security – 70 per cent of which feature a bespoke element.
By managing the entire process from its HQ in Feltham, UK, the company is able to tailor each end product for its customers – which range from banking financial centres, to Facebook – that rely on its access and anti- tailgating products to maintain secure buildings.
While the core components cover the full range of entrance systems, there is a huge requirement to integrate different card readers, tokens or biometric systems into the end product to generate a personalised aesthetic and function.
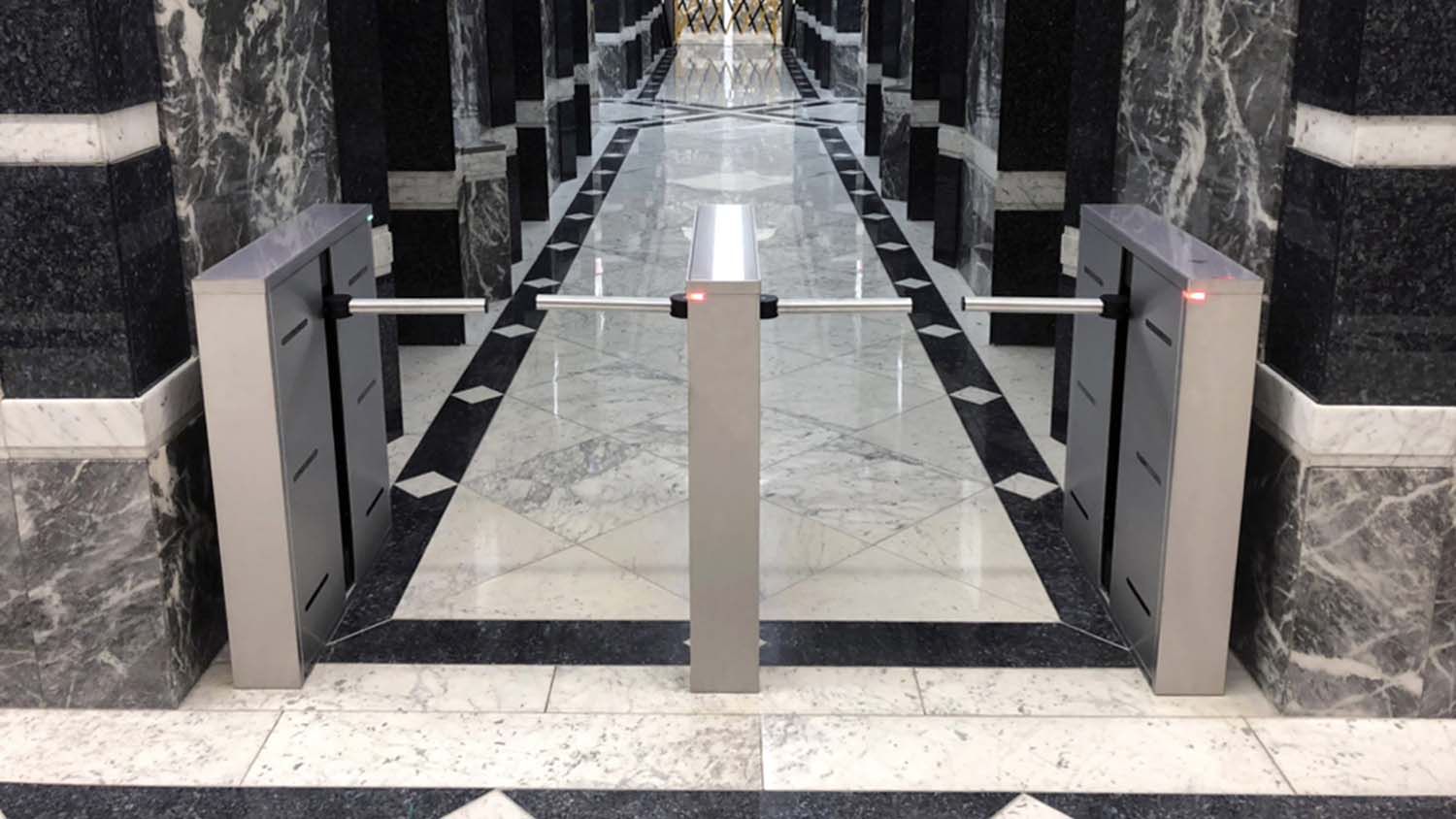
As a client’s identity becomes even more unique and important, so does the need to have branded and unique access control systems designed to match.
Clients often want to integrate new technologies, such as Hitachi’s USB Finger Vein Biometric Authentication Unit into their entrance control systems.
The device takes a biometric scan of the user’s finger print to grant access, but as such products are newly developed, there are no existing ways to mount the scan unit into Fastlane’s turnstiles.
The solution for Fastlane’s design team was to integrate 3D printing further into its workflow, which has allowed them to create truly bespoke products for its clients that won’t accept compromises.
3D printing is involved from the beginning of design process through to end use components.
Upon receiving the initial design specification, Fastlane is able to produce a number of concept designs that are then sent to the client for approval.
As part of the iteration process, the design is sent to Fastlane’s production team to manage any requirements for components, mountings or jigs that will need to be 3D printed in advance.
“Before we used to estimate a product and do an outline drawing for customer approval,” explains Fastlane marketing manager Tony Smith.
“Now we do the full design brief, so we know the design we are going to make and how we are going to make it before we offer it to the client for approval.”
For its entire 3D printing process, Fastlane has invested in Markforged’s Mark Two 3D printers, which can add a continuous carbon fibre reinforcement to either a Nylon or Onyx base filament.
“The good thing is because we have completed the full design up-front, with all the componentry, parts for assembly and have assembled a test part, we understand what is required to produce the part,” says Fastlane technical manager Mike Lau.
This means that when it comes to end production there are a fewer issues needing to be fixed, he says. “In the past, we would have seen more problems in production, time lost with shipping delays or component fitting which would have compounded, but now this is all addressed beforehand.”
For the Hitachi fingerprint scanner, the design team built a bespoke housing for the new product, which was then 3D printed to order for each gate in Markforged’s Onyx material.
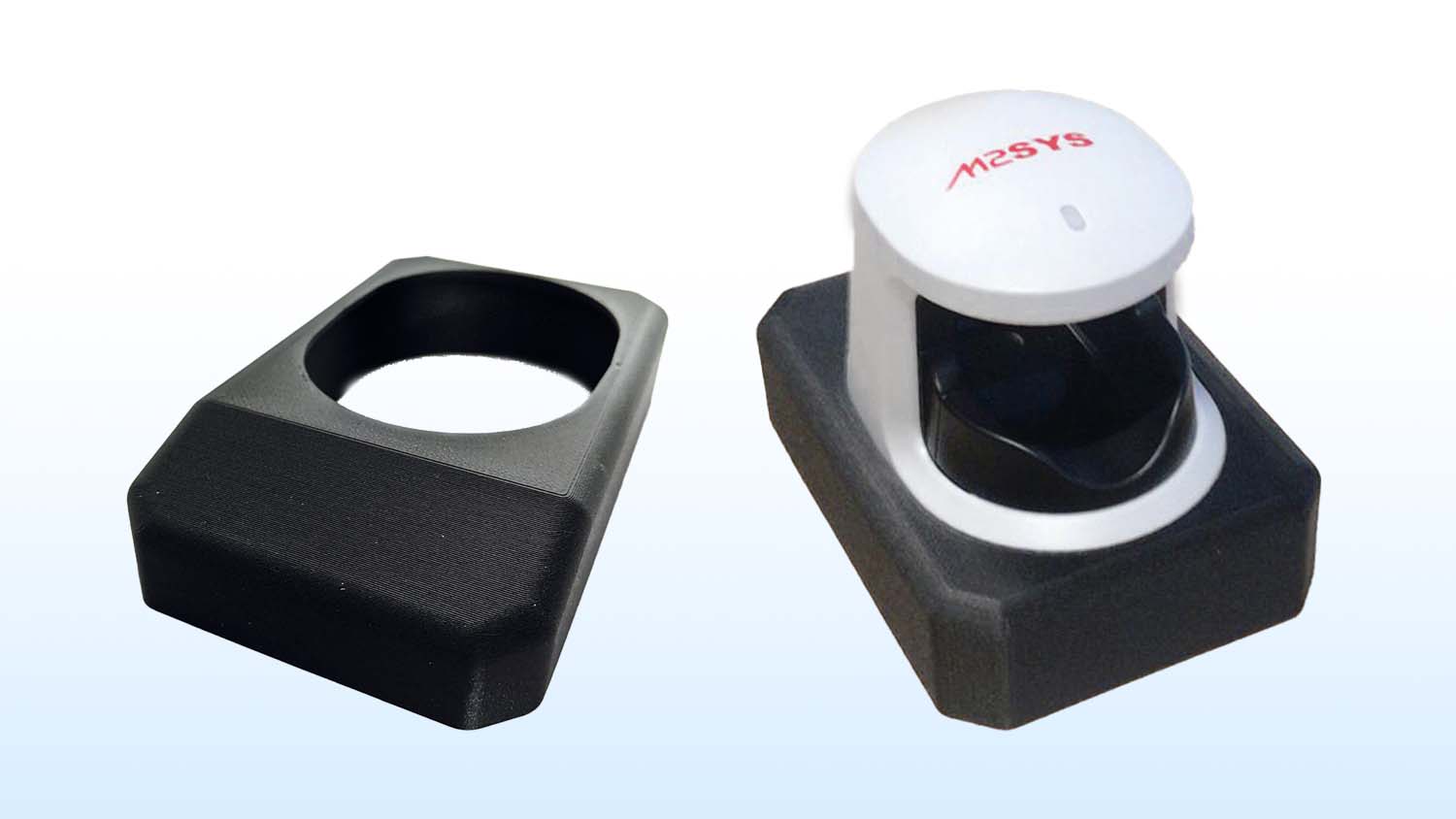
The parts could be fitted to the end turnstile like any standard part, with no additional finishing required.
This process on average would take just 12 hours per part, costing £10 for each completed unit – for which no mass produced housing would be available for months to come.
“The Markforged has changed the way we design,” Lau continues. “There are now no limitations.
“In the past we have been constrained by the traditional methods of manufacturing of machining, turning and sheet metal, but with Additive Manufacturing, it’s really changed the way we think about design and what is achievable.”
By fitting a 3D printed housing, Fastlane were able to manufacture a complete set of entrance systems using the unique access control, that previously could not have been manufactured.
When considering which 3D printing technology to choose, surface finish and part strength were the most important criteria. Fastlane worked closely with experts Creat3D to determine which additive process and materials would work best.
Having been recommended Markforged’s technology, the range of applications has since snowballed, and Fastlane has seen huge time and cost savings.
The design team to are able to use the Markforged 3D printers to experiment with design ideas, with its carbon fibre material strong enough to replace metal parts for some prototyping applications, allowing for iterations to be worked on before proceeding to traditional tooling.
By removing the need to manage external suppliers, Fastlane also has the peace of mind that its knowledge and proprietary information for its security products is kept in-house.
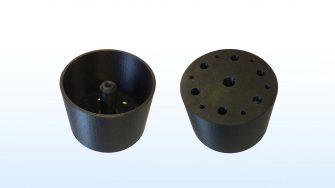
A rotary part developed in-house allowed for a part to be 3D printed and ready for testing in less than four hours, at a cost of £10. The traditional alternative was for it to be outsourced and machined out of steel at a cost of £300, taking two weeks.
This efficient and comprehensive workflow allows Fastlane to build new designs to order within 8 to 10 weeks.
The installation teams have also benefitted – thanks to 3D printed mounting guides, jigs and assembly components. By removing the need for an experienced fitter to install parts by eye, right-first-time installation can be achieved with 100% accuracy.
Fastlane has completely re-defined their business processes, from sales quoting to installation, through 3D printing, with the direct result of it opening more doors for their business.