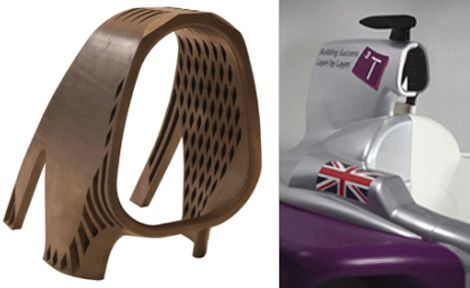
A F1 car safety hoop/air intake produced in titanium using 3D printing – saving 2kg of weight
As the highest point on an F1 car the roll-hoop/air intake is an often under appreciated piece of technology, needing to be as strong and as light as possible.
Its primary function is to protect the driver’s head in the cockpit but other key roles are to act as a critical air intake for the car; as a camera mount for the TV viewers at home, and as a pick up points for the car should it spin off into a gravel trap.
In order to show the type of work it is capable of producing for F1 teams (without giving away any secrets or receiving any pesky legal notices from the teams) 3T RPD has produced a ‘concept’ part of its own, fully demonstrating its skills and the benefits of 3D printing in metal strengthened using custom lattice design technology from Within Technologies.
3T approached Within Technologies since they offer a new approach to design that frees designers from constraints imposed by traditional manufacturing technologies. Its Within Enhance software, has a unique optimisation process coupled to an internal FEA package, and is used to create an original lightweight design, incorporating thin walls with an internal lattice build to create structural strength.
The software was also optimises the geometry of the design in order to minimise the amount of support structures commonly associated with producing metal parts, helping to reduce costs.
The resulting design contains internal features that would be exceedingly difficult and costly if built using any other manufacturing method.
By reducing the part’s weight by nearly 2kg at the car’s highest point, the weight can be redeployed in lower and more aerodynamic positions to help increase performance.
The part has maintained its aerodynamic line and features an area to allow for the addition of a camera mount or other component.
By selecting the Ti6Al4V titanium alloy, 3T has ensured the part would be lightweight whilst having maximum strength and thus the greatest potential for performance enhancements.
The very nature of the metal additive manufacturing process requires a support structure to be used during the build of any downward facing surfaces, since the powder bed alone is not sufficient to hold the liquid phase created when the laser has melted the powder.
3T’s roll hoop was printed vertically to demonstrate the capabilities of building tall components (the part stands 22.5 cm high). Only one small region under the front face of the hoop required support structures to be added for the build phase, while the rest of the roll hoop design was self-supporting, thereby minimising the need for support structures; resulting in faster build times, less waste material, and less post-process finishing.
The roll hoop has received positive feedback from the F1 sector, helping to further the understanding of the capabilities of additive manufacturing and increase confidence in the performance of the materials produced by this technology.
The future should see even more parts being produced faster in this way, with progress being made in design and analysis software it would be possible to model the part to almost exact FIA test criteria and even being produced at trackside.