eNovates is rapidly growing its range of electric car charge terminals, expanding its presence across Europe as more drivers adopt battery-powered transport.
With about 80,000 charging stations installed in early 2021, the company is extending its reach into smart energy management and recently added a vehicle-to-grid (V2G) charger to its portfolio.
Its customers are Charge Point Operators (CPOs) – companies who sell charge points, connect them to networks and provide maintenance.
“Some of our customers approach us with no more than an idea for the final product. In this case we can base ourselves on a set of generic platform components and products to realise the best-fit custom product for the customer,” explains eNovates R&D manager Stijn Vispoel.
“Others come to us with an enclosure and ask us to develop a charger for it. We do full projects for them, and all solutions include mechanical, electrical, electronic and software components.”
Technologies, regulations, standards and customer requirements are evolving quickly in the electric mobility ecosystem. “The biggest challenge is the constantly and rapidly changing guidelines in the market,” Vispoel says.
“We have to be on top of all the new developments and we really need a new product every year. It’s important to have enough R&D capacity to keep up with the changing requirements for charge points.
“Another factor is the different regulations in different countries in Europe. For example, customers in the Netherlands have different requirements than customers in France.”
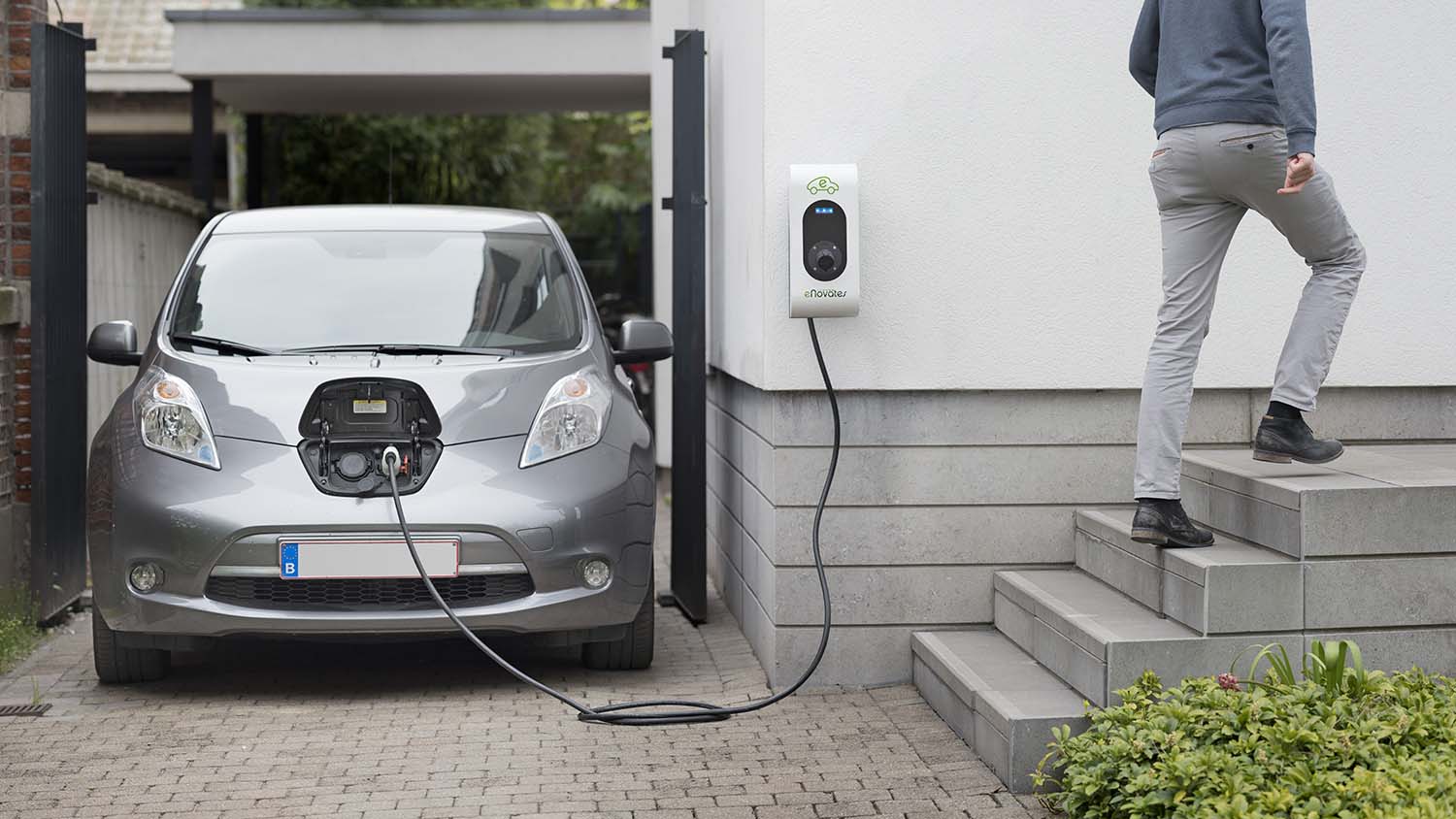
The eNovates product development team has varying backgrounds in mechanical, electrical and electronic engineering. “We begin each project with a prototyping phase where we develop the printed circuit boards we need, the electrical wiring and mechanical components,” Vispoel explains.
“Once we do all the checks on the digital design files, we make some prototypes and do test runs to confirm that they comply with the customer requirements and regulations.
“Then we enter what we call the alpha phase, redesigning any components that need modifications. We make another batch of the product, around 30 to 50 chargers, and do another validation run, performing temperature and high-voltage tests. We also have customers who use them to charge cars and run additional tests.”
In the next stage of development, the beta phase, eNovates makes necessary design modifications and orders a new batch of the product. “We go directly to certification labs with the beta chargers, and place about 100 chargers in the field with our customers, so we are certain that the product is mature enough and it’s fully certified to go into the market,” explains Vispoel.
“At that stage we typically don’t develop the hardware further – the focus is on finishing the software. Finally we go into production for our customers.”
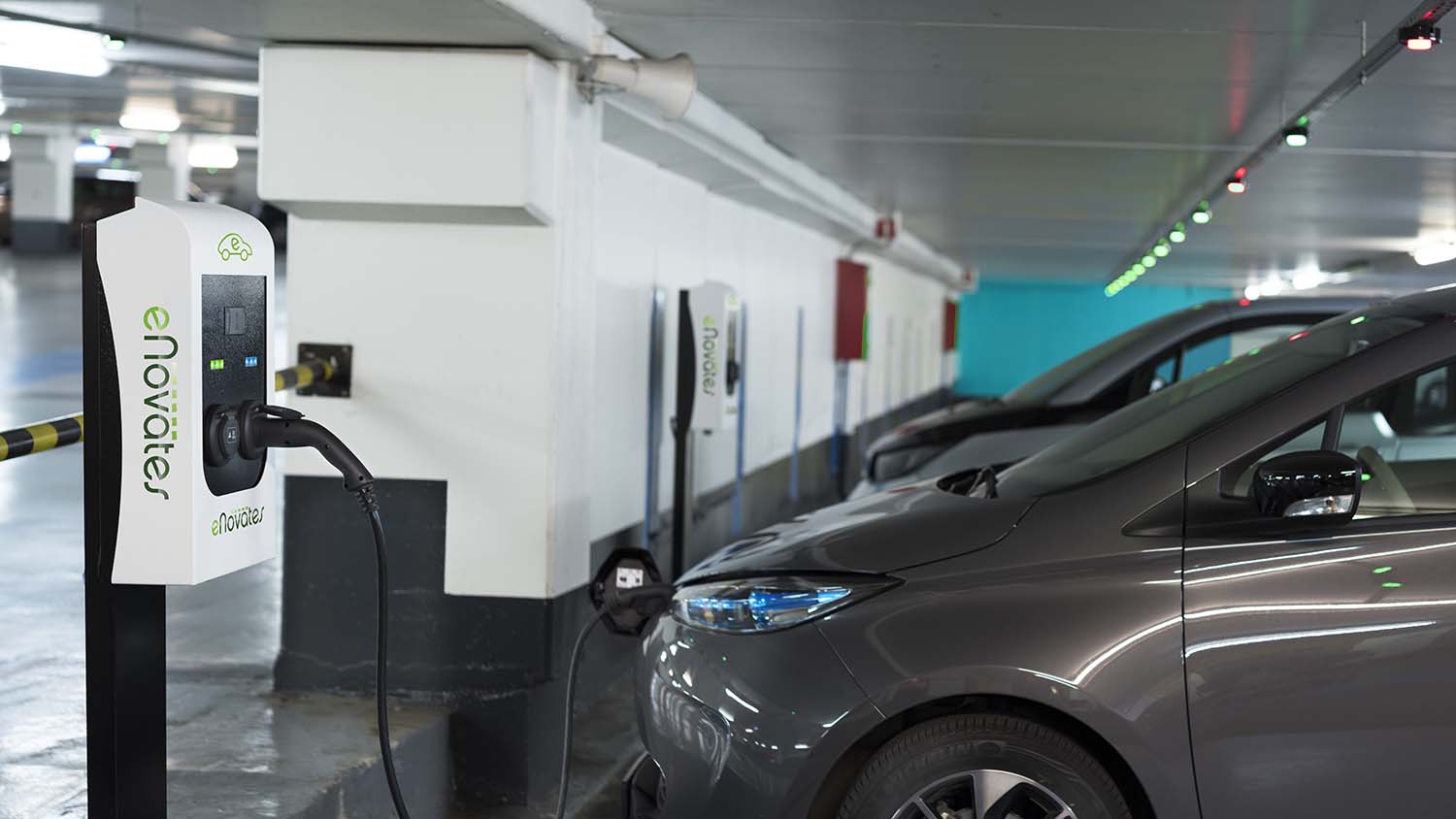
Over its history, eNovates had acquired engineering software systems for CAD, two different printed circuit board (PCB) design solutions, and a system for electrical wiring and harness design.
The systems had been selected based on engineers’ prior experience and partners’ and customers’ use of the solutions
This software landscape had some limitations: The CAD system lacked electrical design functionality, the wire harness design system had no 3D capabilities and neither system easily exchanged data with the PCB design tools.
The four separate and disconnected software solutions created information silos that hampered interdisciplinary collaboration.
Each software package used different data formats that impeded transfer of information between disciplines. Because the software was purchased from different vendors, the new versions of each software solution were not synchronised with the others and eNovates had four different sources of support.
Using this approach, the mechanical design team sent their design models to the electrical team, which amended the designs and returned them to the mechanical team.
These iterative design exchanges continued over weeks and months, resulting in huge design and prototyping costs and product launch delays.
The information silos and barriers between systems made it difficult for eNovates to fit electrical designs into mechanical spaces. They also created problems in communicating design information to contract manufacturers.
eNovates says the details of the design for manufacturing could become disconnected and even confusing, which resulted in issues with quality requirements and regulations.
To eliminate the workflow inefficiencies, eNovates searched for an integrated software toolset that better suited the fast pace of development.
With aid from Ghent University and Belgian Siemens solutions partner ADOPT id PLM, eNovates adopted Solid Edge and its integrated electrical design and technical publishing tools.
“The Siemens software offered us a better match to help us make fewer errors in our design iterations,” Vispoel says. “We didn’t find this level of integration anywhere else in the engineering software market.”
Solid Edge mechanical design, electrical wire routing and harness design, and technical publishing applications were fully integrated and used the same data format and user interface conventions. ADOPT id also proposed Siemens EDA (formerly Mentor) PADS Professional software, also integrated with Solid Edge, for PCB design and verification.
Vispoel adds that it has aided its ability to outsource manufacturing. “We deliver the contract manufacturer a full package of information on how the product has to be made, how to test it, how to package it. And then they translate what we do in engineering into making the product.
“They source every component, make every PCB and test everything based on the instructions we provide.”
By using Solid Edge Technical Publishing software, eNovates has mastered the creation of information for manufacturing – including a unified BOM for the entire product, which is especially useful for pricing.
The improved accuracy and completeness of manufacturing now means eNovates can roll out the next stage of its plans, powering more people take to the roads in electric vehicles with confidence.