Until engineers could finally return to digitally record its form, the Groussgasmachinn has lain dormant for years. We speak to Artec 3D’s engineering team about the mammoth task of scanning this huge gas turbine
The Groussgasmaschinn is the largest blast furnace gas engine ever built – so when the Luxembourg Science Center set out to preserve it, it made sense to record its form digitally for the benefit of future generations. Also known as Gas Engine Number 11 (GGM11), it’s listed as a national monument in Luxembourg. And it’s so large, it could contain an entire tennis court, and then some: 26 meters long, 10.5 meters wide, 6.5 meters high and weighing in at over 1,100 tonnes. Its four cylinders, each with a capacity of 3,000 litres, were built with the capability to produce 11,000 bhp, or up to 7,000 kilowatts of power.
Built in 1938 by German manufacturing company, Ehrhardt & Sehmer, it finally shut down in 1979, still the largest ever built and one of the last of its kind, due to the emergence of more efficient steam turbines. After lying dormant for almost three decades, the Ministry of Culture in Luxembourg ordered its preservation and restoration in 2007.
As part of this project, the Luxembourg Science Center reached out to Artec 3D in 2016, with plans to digitally capture the engine. At that time, however, even the best of the scanning technology available was no match for a task of this scale. Today, however, this mammoth job is underway.
“We’ve been meaning to scan this engine for a very long time, and we’re glad that the technology is finally here to help us do it,” says Nicolas Didier, president of the Luxembourg Science Center. “There is no other gas engine like this one, and it’s crucial to capture it in its current state.”
Artec 3D – Capture challenge
The Artec 3D Ray was chosen as the primary scanner for capturing the Groussgasmaschinn in its entirety, due to its ability to laser-scan large objects from a distance with accuracy.
An Artec 3D Leo wireless handheld 3D scanner was chosen as a secondary device, specifically for capturing high detail from smaller elements and harder-to-access sections of the engine.
“GGM11 is not only the largest object we ever scanned, but it’s also a very complex one,” says Vadim Zaremba, an Artec 3D deployment and technical support engineer who undertook much of the scanning.
To save time, the team split up. The first team positioned the Artec 3D Ray at various locations, at one particular angle, 5 to 15 meters away from the engine.
The second team followed along behind, scanning smaller sections with the Leo, staying out of the Ray’s field of view.
One of the most challenging tasks was to scan the engine from above, using a rickety old cabin positioned some 10 metres above GGM11. This required the team inside that cabin to remain frozen in place for several minutes, in order to avoid disturbing the scanner while it did its job.
Overall, it took the team four days of shifts lasting up to four hours to complete the project. The engine required 18 different angles with the laser scanner, and these were later combined in Artec 3D Studio software with 67 additional detail scans made using the Leo. The final size of the project came to 186 GB in total – 170 GB of Leo scans and 16 GB of Ray scans.
Awaken the giant
Following data capture, all the Ray scans were processed with Global Registration by Artec 3D engineer Dmitry Potoskuev. Then, each of 18 scans were processed into triangulated meshes using Artec Studio’s Ray Scan Triangulation algorithm to clean up the scan surface. All the meshes were processed using Artec Studio’s Sharp Fusion algorithm to create a single mesh of the engine.
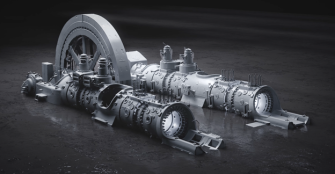
Adding the details captured with Leo had to be broken down into several steps, given the amount of data with which the team was working.
A duplicate of the huge single mesh was created and simplified to under 10 million polygons. Next, the Leo scans were added and registered with the simplified mesh to achieve a higher quality alignment of data.
After all the Leo scans had been registered, the team selected the original Ray mesh and four to five raw registered Leo scans and applied the Sharp Fusion algorithm to create a new mesh, repeating the process until all the Leo scans were processed.
This created a final mesh consisting of a staggering 350 million polygons, which was then reduced to 10 million polygons for further post-processing, using such features as hole filling tools, the smooth brush and bridges. The total processing time for the project was just 80 hours.
Finest details
Speaking about some of the issues faced when working on the model, Potoskuev says that time was the greatest challenge. “This project was so big, not only did scanning and processing take a long time, but transferring the data from the scanners to the computer and then into Artec Studio, could take up to as much as five to six hours – just for transferring!”
“We’re talking about almost 200 gigabytes of data. It’s the largest and most time-consuming object we’ve processed.” But the team’s patience paid off. “It’s amazing that with the 3D scanning technology we have today, something so vast and inaccessible has been digitised right down to its finest details,” concludes Potoskuev.
This massive task may now be complete, but the Groussgasmaschinn story is far from over. Plans are in place to use the scan data to restore missing parts and preserve the giant engine in its current state, “so even if it loses its shape with time, we can still go back to this 3D model and show it to our future visitors, and use it for restoration purposes,” says Didier.
The renovation of the engine is due to be completed by 2027/28, when it will become an integral part of the Science Center, as an interactive exhibit that visitors can not only see, but also interact with. And for the future, the museum has invested in two handheld Leo scanners for its Future Skills programme, in its work to inspire and educate the next generation of engineers.