Boatbuilder Daniel Lee blends traditional methods with the latest technologies to bring beautiful vessels to life. He speaks to Claudia Schergna about how digital tools help his dreams take to the water
As long as he can remember, Daniel Lee has always been around wooden boats. As a little kid, his dad would take him fishing. His grandad always had boats parked in his driveway and had a passion for carpentry.
Unlike his father and grandfather, building and repairing boats in his spare evenings and weekends was not enough for Lee. “It was always just a hobby for them, an interest,” he says. “I’m the first generation to actually make that jump.”
Although his business is relatively young, Lee is hardly a novice in the field. As a former electronics engineer and an experienced woodworker, he has brought a great deal of manufacturing experience to the venture. And by combining handcrafting and high-tech equipment, he has been able to create an innovative workflow that is taking that business to the next level.
By watching countless YouTube tutorials, he taught himself how to use 3D CAD programmes, starting with SketchUp but soon moving on to Autodesk Fusion 360. “To begin with, I started just modernising old plans and I realised I could sell them digitally. It’s a bit of an additional income; there’s a bit less pressure on the daily work to pay all the bills,” he explains.
“I really like old plans from the 1930s and 40s, so the first thing I did was modernise those with modern manufacturing methods using CNC machining and designing the whole boat in CAD,” he says.
Fusion 360 has provided Lee with a key tool for both restoration works and boatbuilding. When his new digital designs caught the attention of American naval architect Michel Berryer, the two started working together.
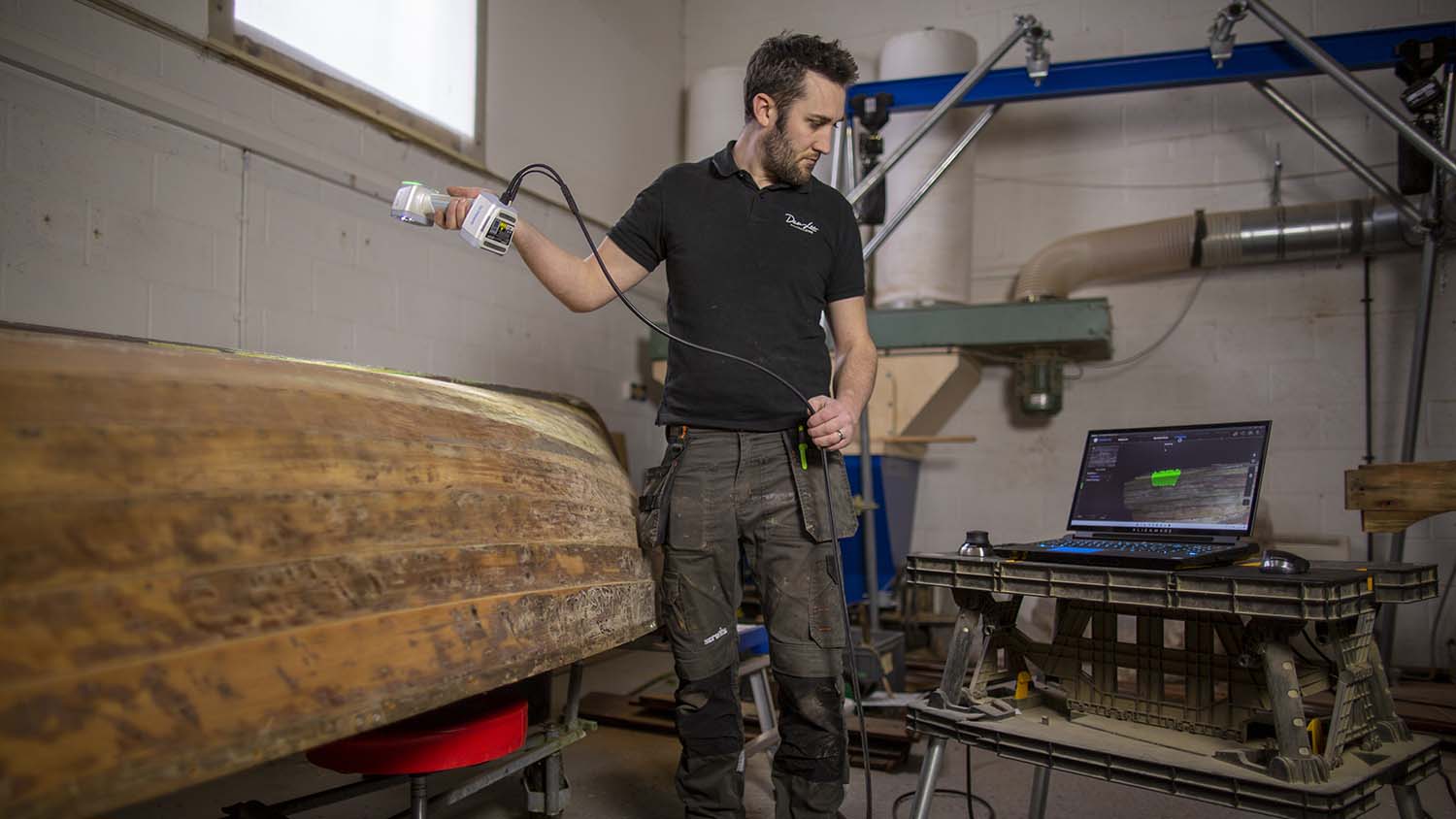
Classic collaborations
One of the first projects Daniel Lee and Michel Berryer worked on together, the Temptress, was a classic boat model first designed by Berryer over 20 years ago. Lee quickly fell in love with it.
“Michel designs on a software called Key Creator,” explains Lee. “He models the whole boat, and he does all the calculations for hydrostatics weight and strength calculations. Then he sends me a model, which I put into Fusion 360 and do all the kitting stuff to turn it into something buildable.”
The final product is a 3D model that can either be built by Lee or by the customers themselves, in the form of a kit.
The combination of Fusion 360 and 3D scanning has also been life-changing – but when Lee first purchased an EinScan H scanner from Shining 3D, he wasn’t actually thinking about its application in boatbuilding.
“The reason for getting the scanner was that I was doing some van floors for a campervan conversion company,” he explains. “They wanted van floors that looked like a boat, to have that ‘marine’ feel to them. I started off making floors for them and very quickly found that trying to measure the shape of a van floor is really difficult, because nothing is square on it. So that sent me down the route of looking for a 3D scanner.”
He then experimented with scanning a boat in his workshop that had originally been built back in the 1970s. “A few people were interested in potentially buying a new production version of it. So, I scanned that and reverse engineered all the moulds and everything that you need to make it.”
Hull capture
To start, Lee used the 3D scanner to digitally capture the entire hull. He realised that the Shining 3D EinScan H was the right tool for him, as it is easy to manoeuvre around big objects and does not require the application of targets.
Transferring data from EinScan software to Fusion 360 is pretty straightforward, as he explains: “I get a mesh file from the 3D scanner, which I put into Fusion 360. Then I take a series of cross-sections – or ‘stations’ as they would be called for a boat – which are basically slices at 90 degrees through the boat, at maybe ten different points. Then I create a new whole skin, which comes out smooth, because it takes out any deviations that might be in the old boat, or that the scanner might pick up. From that, you’ve got a whole new skin.”
The final step is to create the framework and structure for the boat: “That is cut on the CNC machine. So, I end up with a crisscross, egg-box shape in the middle, which forms the shape of the boat, and then I build the skin over the outside of that.”
EinScan H has turned out to be very convenient for scanning wood, says Daniel Lee: “I like it because it captures the colour and the texture of the surface, as well as the physical shape.” Originally designed for scanning people and skin textures, he explains, it also tracks well on wood surfaces.
Use of a 3D scanner brings several advantages in his daily work. For a start, it saves time, enabling Lee to plan ahead effectively.
“Of course, the first question people ask me is, ‘How much is it going to cost me?’,” he says. “I can very quickly mock-up the moulds in CAD enough that I can get the material quantities. That was the main exercise for scanning and drawing up the moulds – just to very quickly get a rough price, and then see if there’s any actual feasibility in it. Because if it came out ridiculously high, and no one was prepared to pay that much, I just wouldn’t bother doing any of the rest of the work on it.”
This process can now be done in a fraction of the time previously required. “It probably took me an hour to scan it, and maybe two to three hours to draw up all the moulds and everything in CAD. If I was to loft that traditionally, I think it would be two or three days, probably. And if it’s just for the purpose of trying to get a price to build one, that’s a lot of time invested.”
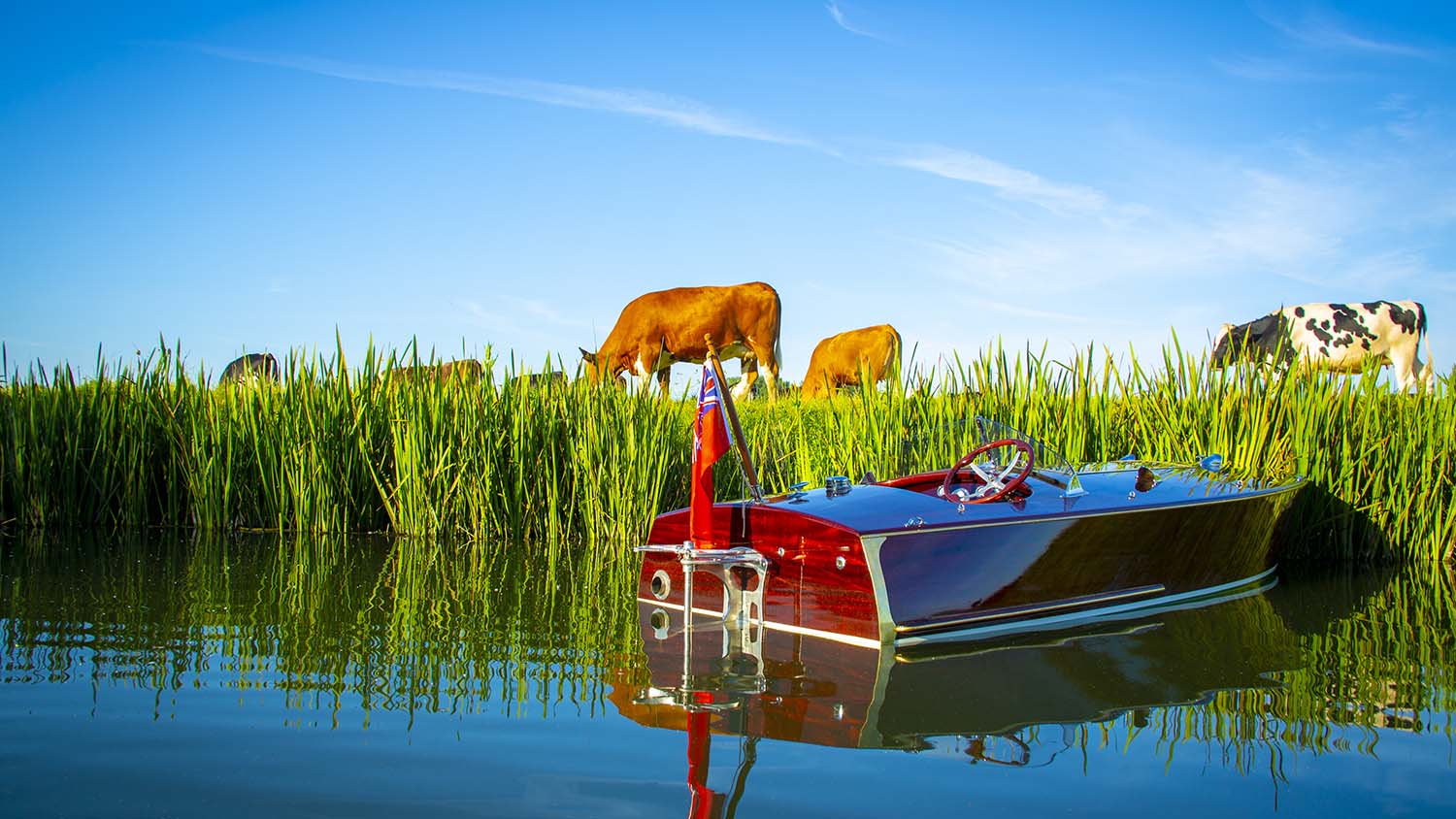
Restoration magic
Using 3D scanning is also great for restoration as it allows Lee to reverse-engineer the damaged parts of a boat and replace them with nearly identical pieces.
“I’ve got a ‘30s Chris Craft that I’m restoring, which is a really old, rotten boat. It’s probably going to be 90% new wood, I would think,” he says.
“So, because I’m replacing probably 90% of the wood on this, when it comes to putting cleats back on, you often lose your reference and where they should be. Now, I can refer to the 3D scan. And I can measure how far a cleat was from the transom. I can locate things like the waterline and position that vein in the same place that it was originally.”
Once completed, the vessel will be yet another in a whole fleet that Lee has brought back to life, taking to the water as his dream career cruises in the right direction.