Philadelphia Racing Products, a high-performance aftermarket automotive parts manufacturer, is continuously evolving to meet the rigorous standards of racing enthusiasts.
Established in 1991, feeding the demand for street and performance racing, company founder Julius John Schonberger III saw an opportunity to shift the company’s focus from selling ready-made parts to designing and manufacturing automotive components for sale.
Three decades later, Philadelphia Racing Products has grown to include a thriving performance engine division alongside its comprehensive racing parts manufacturing facility.
Yet with increasing demand for custom projects, the company recognised the necessity for improving the efficiency of its product design workflow, which is split between reverse engineering existing parts and designing products from mating parts, such as a valve cover, where getting a precise fit is essential.
Reverse engineering projects were undertaken with handtools then verified by printing out paper templates, a method both time-consuming and tedious to process.
Moving to a 3D scan-to-CAD workflow, to better shift the process into Philadelphia Racing Products’ Solidworks pipeline, required a reverse engineering software to translate the scan data into a workable Solidworks model. Working with its 3D scanning technology supplier GoMeasure3D, the team opted for Mesh2Surface for Solidworks
“Now, for instance, when we design a custom valve cover for a head, all we have to do is capture the surface measurements of the head with a 3D scanner to obtain measurements such as the bolt-hole locations, valve train geometry, and rail locations,” said lead engineer Chase Evans. “By referencing the 3D mesh of the physical component, we can dedicate all our time to designing the custom valve cover and significantly simplify the process.”
Evans explains that the combination of Solidworks-native tools with the Mesh2Surface Scan to CAD toolsets helped to simplify the process through its synergy. “Some designers and engineers prefer standalone reverse engineering software. However, as an experienced Solidworks user, I found it more practical to perform reverse engineering all within one CAD software package,” he said.
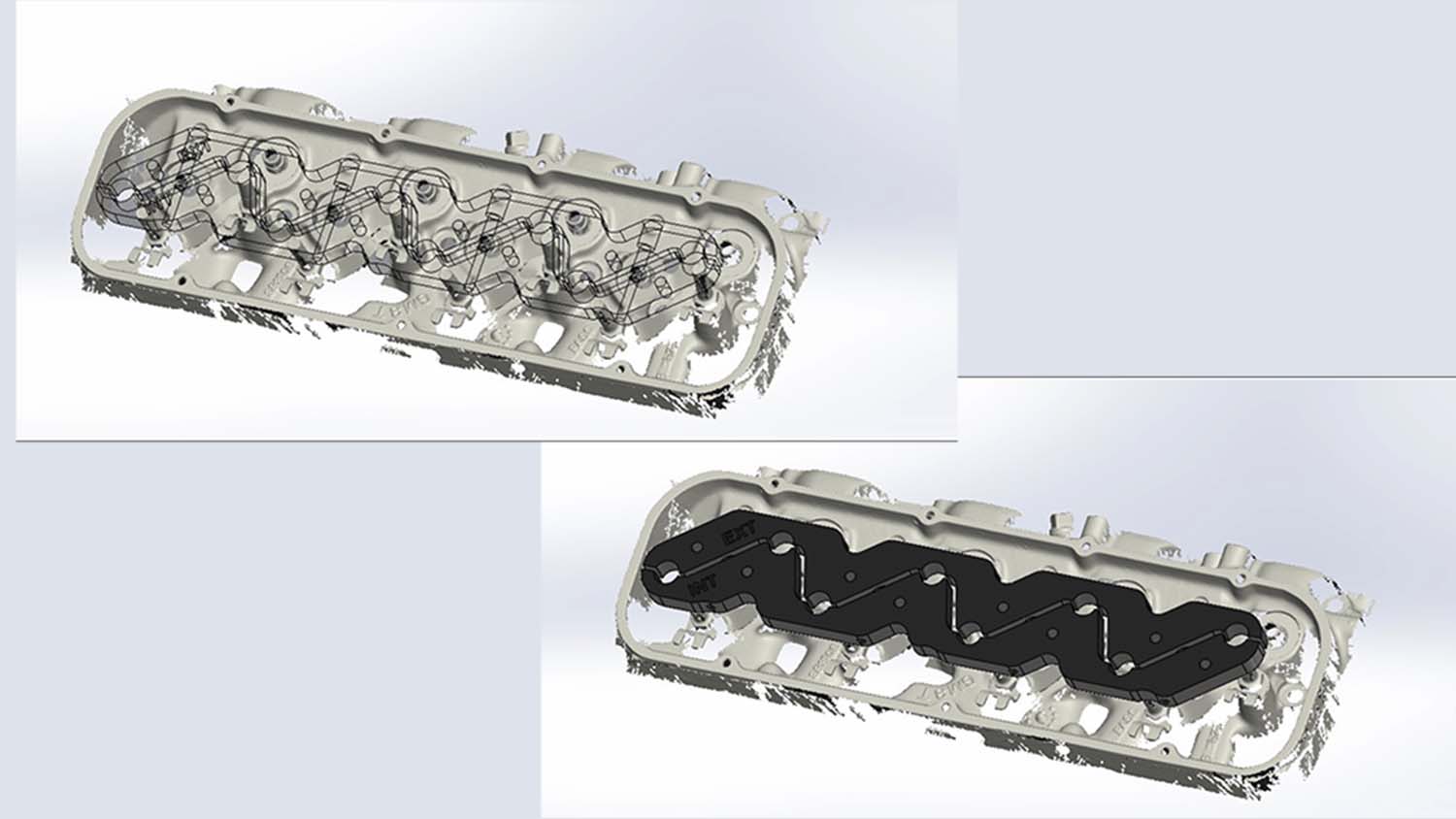
“Mesh2Surface as a plugin works perfectly well with Solidworks by allowing me to access a comprehensive set of advanced reverse engineering tools. With this seamless integration, I can fully harness the potential of both platforms, significantly enhancing my product design and development workflow in multiple ways.”
Evans gives the example of a project to develop big block Chevy stud girdles, a set of bars that bolt together to clamp onto a valve train’s poly locks. This part helps increase the rigidity of the valve train and provides more support in cases of an aggressive camshaft. Mesh2Surface for Solidworks, he says, was instrumental in finding the precise angles of the poly locks. Each piece sat at a compound angle, which would be practically impossible to accurately design without this Scan to CAD plugin.
“It’s fantastic that we achieved our goals by using Mesh2Surface for Solidworks,” says Philadelphia Racing Products Richard Schonberger. “We’ve successfully transformed our product design process through 3D digitisation, allowing us to streamline our workflow instead of relying on conventional manual methods as we did before.
“We’re excited to further expand our operations with this overhaul of our reverse engineering design workflow. Now, we can handle more projects, serve new clients, and tackle extremely complex design tasks.
“We’re also designing better products using this new approach because we can fully trust the reference measurements captured by our 3D scanner for designing our parts, compared to the hand tools we used previously,” Schonberger explained. “Using the 3D mesh data to determine clearances and ensure the proper fit of mating parts becomes significantly easier and faster. As an extra advantage, the parts our team is designing are extremely accurate.”