Using SLA AM to meet automotive cost and sustainability goals:
Automotive designers are not only tasked with finding sustainable R&D and manufacturing processes, but also fast and cost-effective ones.
It’s a challenging balance of the bottom line vs the green line, but some large-format 3D printing processes can offer solutions that benefit both. We spoke with AME-3D managing director Rich Proctor about how additive processes are helping its automotive customers reap the benefits.
Q. What are automotive companies/suppliers coming and asking you for?
The adoption of 3D printing is constantly increasing, and a prime example of this is in aerodynamic testing. You can 3D print a scale version of the whole vehicle, or a small section, and put that in the wind tunnel to understand how the vehicle will perform.
When it comes to concept modelling of the full car, 3D printing is the go-to technology for a lot of the interior surfaces. You can generate the required textures, feel and colours too. If you want to create options where you have interchangeable features, 3D printing again, gives a perfect platform for that.
Automotive companies are currently approaching us for the larger parts built as a single piece in the new high-strength material we have on the large-scale SLA machine. This single piece build is the main attraction, yet the faster lead times and sustainability aspects are great additions once customers hear about these. We’re currently trying to raise awareness of the sustainability and faster lead times of the new machine and of using AM for automotive in general too.
We’ve had a few builds of motorcycle seats and car seating areas. We’ve also had a few grills, control panels, and show car features, while some SLA parts can be used for fit and function testing of drivetrain, suspension and chassis components.
For more functional test parts, we can use the prototypes as a baseline to then advise on alternative processes like SLS or casting (vacuum and RIM) and even offer low volume production to really test the functionality once the form and fit is established.
Complex jigs and fixtures can be produced in the same way that are robust and durable on the assembly line. We recently added a large frame UnionTech RSPro 800 SLA (800x800x550mm) to our fleet of machines to better serve this market.
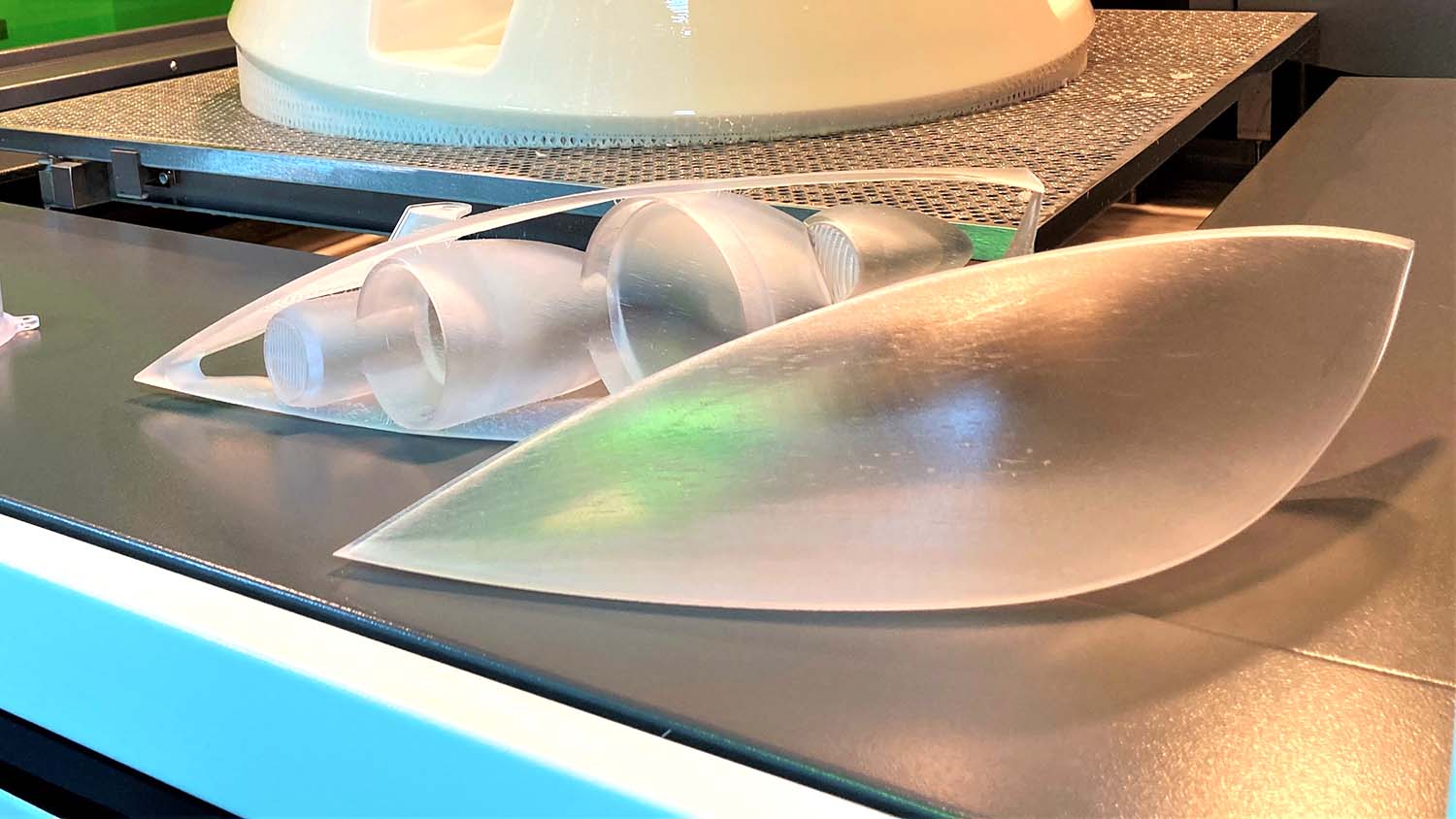
Q. Most automotive companies have their own in-house AM tech now – what benefits can a bureaux add, and what are you helping advise automotive companies about with additive – especially around sustainability?
There are several key benefits a bureaux brings to the table. For our recent motorcycle brand it was the overall part size which was the main benefit, as our machine had a much bigger platform and they could build the seat as a single piece for the first time. Previously they’d joined the two halves of the seat together but this weakened the part. They were very pleased to finally have the part strength they were hoping for.
We’ve also seen in-house AM team’s struggle with capacity and we can easily help them out with that. It’s mainly when they need a quick turnaround. Our machines are not only bigger but oftentimes much faster than theirs and with a full focus on AM from our team the project as a whole is completed quickly.
While the large-scale SLA machine is well-suited for automotive, we also have more specialised high-resolution machines and automotive companies don’t always have access to the same variety of machines that we have in our fleet.
However, the key benefit of partnering with a bureaux is the experience the team has. With over 25 years’ worth of AM experience, we know how to optimise a build and advise our customers on how to make the most of their design. This is also where sustainability support comes in: our in-house partner-brand is a design consultancy, and if automotive designers want advice on how to make their build lighter or to revamp it to build faster (thereby saving overall energy used per unit), we can support with this.
While some 3D print farms may only print what you send, we’re able to offer a more personal approach and so automotive companies benefit from our hard-earned experience when it comes to building automotive parts.
Q. You mention large parts: a lot of companies (auto or not) will remember how long it took to print a giant part – so how much faster is it to produce these parts?
Machines are much faster than they were 10 years ago, but even with the new large-scale machine speed very much depends on the part.
We’ve definitely seen a saving of several days (on average 2-3 days but it does depend on the part). When you’re in a tight spot suddenly having an extra 2 or 3 days can make all the difference. The speed comes from the new machines having more power and more advanced tech, but it’s also due to the fact that our team are very experienced in how to use them.
Prototyping at a larger scale enables designers to start thinking about reducing component count. By using a large-scale 3D printing process they can experiment with this. They can look at how using single large components might help in the production processes.
Reducing component count reduces the need for connectors or adhesives and decreases assembly time. Being able to test this at pre-production phase enable an organisation to better plan for mass production early and reduce the total carbon footprint of a vehicle.
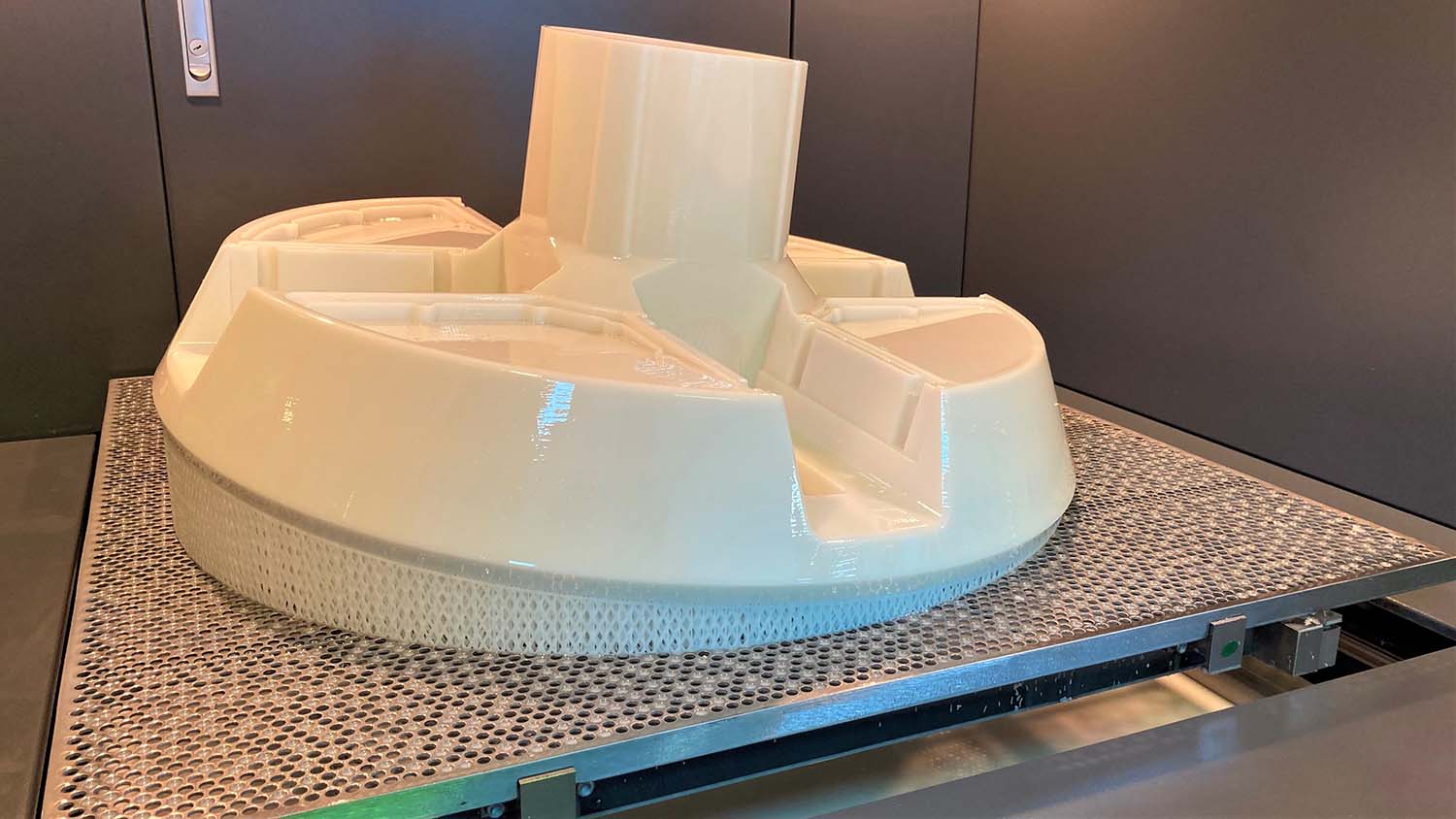