Markforged has launched its Blacksmith 3D printing software for Markforged X7 3D printers, claiming that its AI learns from the user and streamlines the workflow to produce accurate parts, right from the print bed.
Blacksmith connects part design, production and inspection with the ability to learn through artificial intelligence (AI). As Blacksmith learns from across the users fleet of 3D printers, manufacturers should be able to print the right part every time.
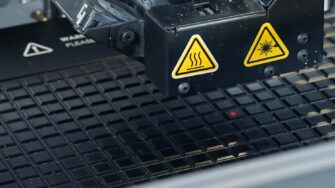
Markforged Blacksmith allows users to print and scan their part simultaneously to assess how close the printed part is to the intended design, using the X7’s existing integrated laser micrometer and smart scanning process to measure parts as they are being 3D printed.
The laser micrometer enables the calibration of the machine, by scanning a Markforged-approved part to set-up the X7, before capturing a point-cloud during the 3D printing process.
The part’s dimensional data is automatically evaluated against the CAD file, including the inner part structure and critical features that would otherwise be impossible in a single step after fabrication.
“We knew that it would only be possible to reinvent manufacturing with a software-first approach to building hardware,” said Markforged CTO David Benhaim.
“Blacksmith fundamentally changes the way engineers think about additive manufacturing. For the first time, they will have confidence that their parts will perform as expected without a time-consuming process.
“Blacksmith makes our platform smarter and is the next step on our roadmap to bring the agility of software to the world of manufacturing.”
Blacksmith is available today as a software subscription on all cloud-connected Markforged X7 printers.