One question, eight thought leaders from the simulation technology space: Why has analysis and simulation technology not yet delivered on its promise and become a mainstream part of the design and engineering process?
Prith Banerjee, chief technology officer, Ansys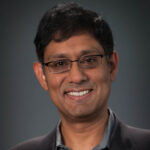
Integrating simulation throughout the design and engineering process requires both a broad spectrum of dedicated and embedded solutions, and companies that are willing to change their workflows to adopt those solutions. Momentum is building on both fronts.
Advances in compute power, ease of use and speed have been critical to enabling Ansys’s vision of pervasive simulation.
The cloud and GPUs are making compute power more affordable and accessible while reducing run times. AI and UX advances are making simulation dramatically more user-friendly. In fact, we’ve seen middleschoolers leverage simulation in the classroom.
Education is another important driver. At the undergraduate level, it’s increasingly common to see simulation baked into the core engineering curriculum, as opposed to being offered as an elective. That means the next generation of engineers will enter the workforce knowing how to use simulation, allowing companies to dedicate fewer resources to training.
On the customer side, ‘shift left’ or simulation democratisation initiatives are being discussed throughout organisations, from engineering teams to boards of directors. We’ve seen strong adoption rates for our solutions that help companies ‘shift left’, proving these initiatives are being acted upon as well.
Over the coming years, a broader spectrum of solutions will continue to mature. More engineers will join the workforce ready to simulate. And companies will either capitalise on these trends or be left behind by competitors that did.
Either way, simulation will be a ubiquitous part of the mainstream design and engineering process. It’s only a matter of time.
Dr Royston Jones, chief technology officer, Altair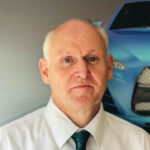
As someone who has spent a lifetime applying and championing simulation technologies (and it really has felt like a lifetime), do I agree with the premise that it has yet to go mainstream? Reluctantly, and setting aside some pockets of success, I agree.
The promise of simulation is built on design time reduction (speed!) and innovation (that is, performance targets). From my experience, speed trumps innovation, since it’s often assumed performance targets will eventually be achieved.
In aggressive design environments, speed is everything and simulation has historically been too slow. Other factors that haven’t helped simulation democratisation have been education and understanding, the siloing of simulation from the design function and the poor quality of embedded CAD simulation.
In my view, it’s always been clear that simulation will drive the design process, it’s just a question of when. In 2000, when Altair performed a weight optimisation simulation on the A380 Droop Nose Rib pack, these designs made it onto the aircraft.
If you asked me back then, ‘How long before this type of technology is standard?’, I’d have provided an overly optimistic answer. Great technology is not always rapidly adopted into an established design process.
However, adoption of simulation will accelerate with more powerfully integrated workflows and intelligence (for example optimisation, machine learning), supported by the key enabler of inexpensive computing power.
Large pockets of simulation success are emerging, which will drive others to follow.
Due to the complexity of next-generation products (for example, electrification, connected, mechatronic) and the requirement to cost-effectively homologate, simulation will become a ubiquitous part of mainstream design processes.
Carlo Polini, president, Esteco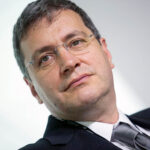
Nowadays simulation and analysis are part of any industry and the variety of applications is diverse. However, a measurable impact in the product design process is still difficult to make, since in order to be valuable, a simulation study must be accurate and therefore performed by an expert.
Democratisation, in the sense of simplifying models and/or GUI to sophisticated simulation tools, has somewhat failed to increase the number of people in a company able to perform simulations.
The lesson learned is that it is not access to a software simulation that needs to be democratised. Instead, it is access to ‘certified’ parametric models that can and must be made available to a broader audience, amplifying the impact of the ‘expert+simulation package’.
Effective democratisation shouldn’t be a watered-down compromise. Rather, it means making the most of everyone’s competencies and propagating simulation knowledge and insights throughout the entire organisation.
This can be achieved by means of a properly customised, server-based and secure SPDM platform where simulation experts can build, version and share parametric models.
At the same time, design engineers can perform their simulation and optimisation studies, without dealing with the model complexity.
Finally, all the generated knowledge is captured and reused to run further simulations and drive more informed design decisions.
This is where embedded artificial intelligence can make the job easier for everyone, regardless of their level of expertise.
Strange as it sounds, the more invisible simulation (and its complexity) becomes in the design process, the bigger its impact will be in enabling a true, game-changing digital engineering approach.
S. Ravi Shankar, Siemens Digital Industries Software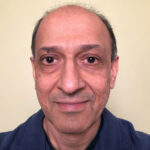
Broad adoption of commercial solutions for mechanical computeraided design (CAD) and computer-aided engineering (CAE) really began in the 1990s. During those early years, CAD was meant for creating the design and CAE, which often lagged design, was primarily aimed at reducing reliance on physical testing. With some exceptions, they mostly evolved as disconnected processes which used different software tools.
Today, simulation’s role is broader, it is used to explore options and inform decisions not just validate designs.
Simulation also addresses a much wider range of physics and applications and complements physical testing.
The market size for CAD and CAE are roughly equivalent, with higher growth rates for CAE over the last decade. And in some industries, such as the automotive and aerospace sectors, for example, analysis and simulation have become standard parts of the engineering process.
As product complexity continues to increase, there is a growing need to connect all development activities. As a result, companies see more value in front-loading simulation within design.
Strategies for simulation driven design might include deploying easy-to-use simulation applications within CAD; using templates that allow specialists to guide designers; and providing dedicated apps that assist designers with specific evaluations.
Data management, already widely used in connection to design, is gaining acceptance in the simulation domain, so that stakeholders can easily access performance results and use them as the basis for their design decisions.
Looking ahead, we see accelerated adoption of CAE into mainstream design. Approaches based on artificial intelligence, generative engineering and fast simulations are further increasing accessibility of CAE.
Ongoing advances in multiphysics modeling, material engineering and digital twins ensure that simulation will be ubiquitous and critical across all phases of engineering.
Dr Naghman Khan, technical manager, SimScale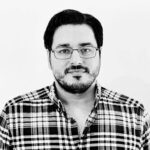
The world as we know it has been shaped by feats of engineering innovation. Nearly everything we see, touch and use depends on a designer or engineer having done their job well.
This includes the cities and buildings we live in, the air we breathe, the food and water we consume, the healthcare and mobility options we have, the devices we use and the energy we need to power them.
Despite our society’s dependence upon engineering, today’s engineers aren’t as empowered by their tool stack as software engineers. Every engineer globally should have the technical and economic means to access simulation technology. It should be as common as engineers using a spreadsheet to perform basic calculations.
The tool stack, the range of design and analysis software tools available to an engineer, is fragmented. A central cloud simulation platform, which can integrate into existing workflows, must be widely adopted to facilitate this democratisation of simulation.
Analysis and simulation technology still requires a high level of expertise, investment (software and hardware) and training. Its value proposition has not changed in the last 30 years.
The potential for improving products early in the design process requires broader accessibility beyond expert users. Entire teams must be able to access simulation – with collaboration and ease of use considered central features.
The cloud can enable both, although many well-known software products are not fully cloud-enabled.
This is why SimScale has developed the world’s first fully deployed cloud engineering simulation platform that allows engineers to test their designs against real-world physics using a powerful CFD engine, accessed through a web browser.
Delphine Genouvrier, portfolio director, Simulia R&D Dassault Systèmes
I would add nuances to your statement that simulation has not fulfilled its promise of becoming a core design and engineering process.
We can agree that the adoption of simulation tools by the entire designer community is not there yet and we are a far way from saturation.
However, the adoption of this technology is rapidly increasing across companies in a number of sectors. Today, simulation is perceived as essential to design and engineering by a growing number of our customers and prospects.
With most of our customers, we are working on a unified modeling and simulation approach. This is what is challenging the status quo and breaking down barriers to simulation adoption by all. So while simulation is not used by everyone, it is certainly leveraged by many.
There are two fundamental hurdles in adopting simulation. First, a siloed approach to design and simulation still exists in the sector. Different and sometimes conflicting tools are used by the simulation and design functions, and this has proved to be an inefficient way of working.
The speed and ease of use needed to match the increasingly competitive and efficient pace of modern design simply isn’t there when different toolsets with different user interfaces and disconnected workflows are deployed.
But when an integrated, connected set of design and simulation technologies is put in front of a product designer and an engineer, we have found they are receptive to the unified approach.
The second hurdle is that most ‘simulation for designer’ software is not powerful enough to answer the real questions important to designers. They need to know more than just the linear stress in the fillet of a product. They need to know how long their product will last, how well will it perform, what the user experience be like, whether it can be made from a different material and even how its weight might be reduced without sacrificing end-user performance.
These are the questions of real value that historical approaches to simulation-for-designers cannot answer.
A unified, integrated approach, using powerful state-of-the-art simulation technology with a design-oriented user experience, can provide the answers needed.
With that, users and customers are successfully bringing simulation into their core design processes.
Philip Kinnane, PHD senior VP of sales, Comsol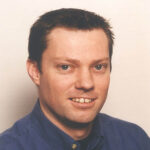
Since the advent of computers made it possible to crunch numbers, analysis and simulation technology has revolutionised design and process engineering.
As computational power and accessibility have increased over time, from vacuum tubes and punch tape to modern-day cluster computing and schedulers, simulation has become a necessary part of the development and optimisation of engineering designs and processes.
This increased capability has also required those engineers who harness such power to become more sophisticated, which includes the comprehension of multiple and coupled physics being simulated.
Moreover, these engineers are required to develop a superior expertise of the simulation tools and hardware operability used to perform such simulations. The number of people who master these facets, in concert with the increasing power of simulation, is limited.
To alleviate this roadblock, simulation engineers need to share their expertise with colleagues who have not mastered simulation techniques, but do hold acute knowledge and experience within the application field itself.
Subsequently, modern-day simulation software needs to work as a platform for building targeted simulation applications relevant to the engineering experts in their specific application domain, as well as present their work in a way that is intuitive to those engineers.
Instead of mastering the underlying physics, the numerical methods used to simulate them and the algorithms used to harness the hardware to ‘crunch the numbers’, these engineers can instead concentrate on the inputs to a simulation that they can actually control and understand, relating the resulting data back to their initial designs and processes.
John Janevic, chief operating officer, MSC Software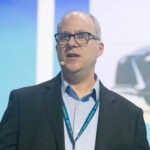
If you look across industries and applications, simulation is everywhere – but it’s under-exploited, because it’s used by isolated teams to replace physical tests.
I believe we still need to build trust in results and change this mentality by demonstrating that simulation isn’t simply cheaper than physical tests, but can provide more insights than a physical test alone.
Looking across product development, each user needs the right tools so that they can classify problems correctly and we need to ensure that an issue is sent to the person with the right level of expertise to solve it.
The challenge is to build a workflow that presents a relevant level of information and context to each user.
We need pervasive simulation to meet escalating productivity and sustainability demands, but it must be time- and cost-efficient.
For example, a multiphysics simulation may offer a faster route to optimise an electric vehicle’s drive efficiency and durability, but if it takes two days to run, its use is confined to R&D.
AI fundamentally changes that equation. Automotive crash analyses that previously took hours now complete in seconds, enabling more thorough safety testing. Reduced Order Modelling (ROM) with supervised learning made that possible.
Physics-based simulation alone cannot assimilate historical data, and unless the computational efficiency of simulation is improved by several orders of magnitude, the potential of digital twins will remain underexploited throughout product development.
The application of AI enables digital twins to greatly enhance end-to-end product development processes; for example, by analysing how material properties transform through manufacturing, in order to reduce material use and avoid redesign.