While electrospindles and related tools must operate with incredible levels of precision, they are also subject to extremely demanding conditions, including high-speed mechanical rotation and high thermal loads.
These machine tools with rotating shafts are designed for cutting, grinding, milling, and other processes, tackling a wide range of tough materials.
Based in Grader, Italy, HSD Mechatronics is one of the world’s leading manufacturers of electrospindles, many of which are highly customised, as well as two- and five-axis heads, boring heads, rotating tables, smart motors, and other machine components.
Throughout the development, the holy grail is a product that can combine precision and durability, with thermal effects and deformation the serious concerns.
“Many of our customers are original equipment manufacturers who must meet strict quality standards and tight production deadlines,” says HSD tests and experiences manager Manuel Camperchioli. “That means we must engineer our solutions, including electrospindles, for maximum performance, power density, durability, and consistency over time.
“We need to understand and minimise materials degradation, vibration, thermal buildup, and other physical issues that impact long-term, reliable performance in our customers’ applications.”
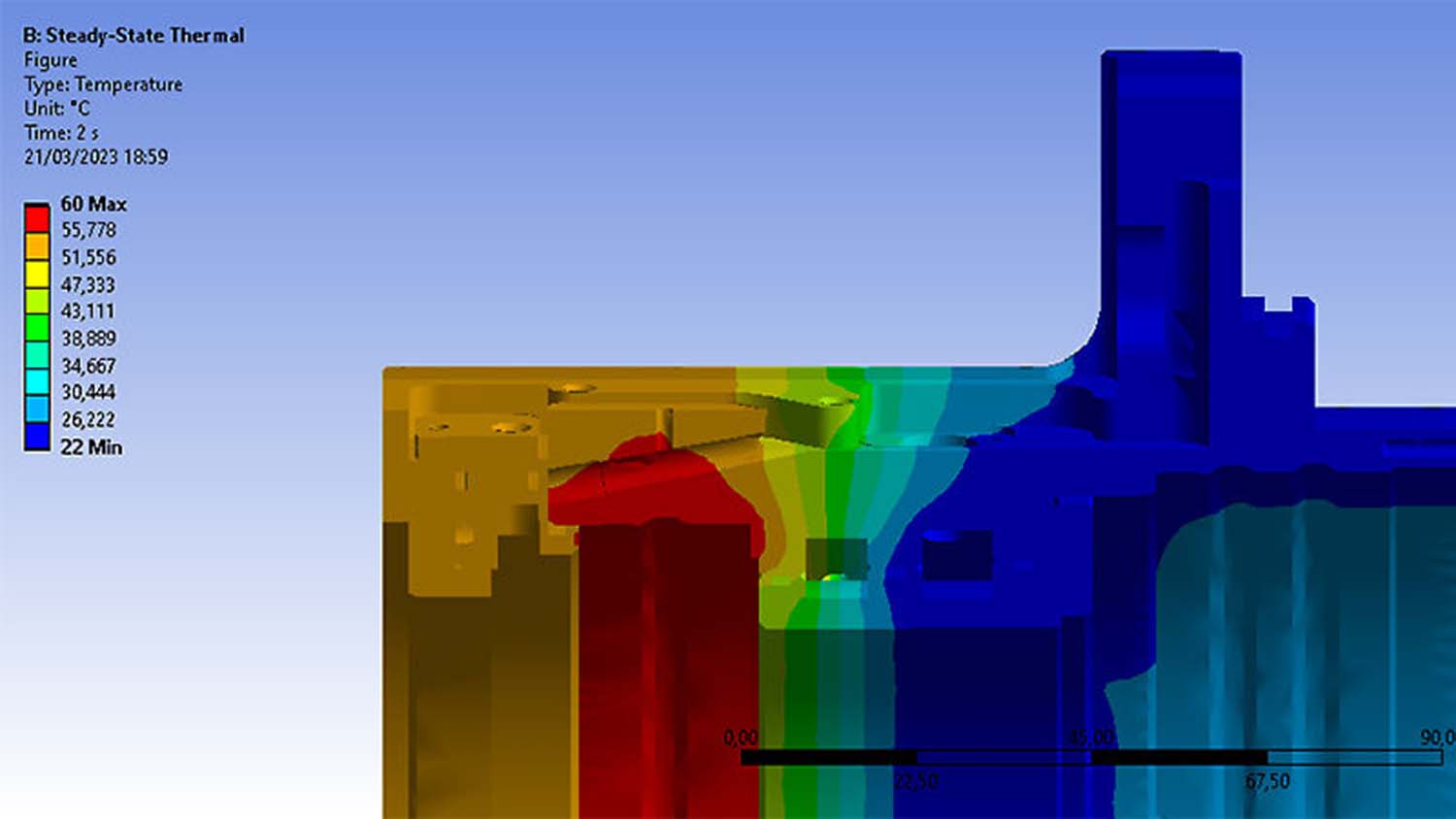
Since 2019, HSD has relied on a suite of Ansys solutions, including Ansys Mechanical and Ansys Fluent, to simulate the real-world performance of its electrospindles in customer applications and investigate improvements such as new materials. HSD has chosen an Ansys Cloud delivery model that Lorenzo Ciccarone, Electrical Machines Designer at HSD, notes has been critical in managing the large numeric problem sizes required to replicate rotating machinery.
“Large multiphysics problems like vibration can be distributed and solved much faster. In fact, we’ve achieved a 40-times acceleration in solution times since we transitioned from using an internal cluster to the Ansys Cloud delivery model. That enables us to run many more simulations and investigate more complex performance issues.”
But this is only the beginning. In December 2020, HSD was named a partner in Italy’s prestigious Intelligent Factory Cluster, a public-private partnership aimed at establishing Italian leadership in zero-defect manufacturing.
HSD has set its sights on developing a next-generation electrospindle that is digitally connected to the rest of its customers’ production environments. The Polytechnic University of Marche, Sapienza University of Rome, and startup company EN4 are partners in the ambitious development project, titled Electrospindle 4.0.
HSD believes that the electrospindle of the future will be digitally connected in real time with the rest of the factory to create a true zero-defect environment. With all assets connected, including machine tools, manufacturers will be able to create a centralised digital ‘control tower’ that can detect defects at any stage of fabrication and assembly.
To accomplish the ambitious goals of Electrospindle 4.0, HSD partnered with Ansys to add Ansys Twin Builder to its solutions portfolio in order to create a a digital twin that’s directly connected to a working machine tool.
By increasing the interconnectivity of its machine tools with the larger production environment, sensors need to be placed on each electrospindle. Some of these are real-time physical sensors that warn of an event or the need for servicing, however, it’s impossible to place physical sensors everywhere they’re needed due to the complexities of electrospindle operation. So, an equally important component of Electrospindle 4.0 is creating an accurate digital twin of the working tool that’s equipped with a series of virtual sensors.
“We can replicate a specific tool’s operating conditions in Twin Builder based on live inputs from the digitally connected, working electrospindle — then the virtual model provides even more data points,” explains Ciccarone. “By gathering data from both physical and virtual sensors, we can predict repair and maintenance needs before an event happens.
“We can gather an enormous amount of real-time insights to continuously optimise the product and its performance. Ansys Twin Builder is the perfect solution for building that working model of the electrospindle and connecting it to the live, working tool in a customer’s facility.”
HSD is seeing that the complementing of physical sensors with virtual sensors helps reduce the overall costs of digitalisation and enables the team to explore very complex performance parameters — such as the internal workings of the tool — that would not otherwise be possible.
While creating real-time connectivity across the factory is still a complex undertaking, the use of Twin Builder is helping to simplify it, accelerate the overall development process, and drive down the costs of the Electrospindle 4.0 initiative.
Cut to fit: How Guhring use 3D printing for custom cutting tools