The development of Great Britain’s track cycle for the Tokyo Olympic Games was a race to achieve the most minute of margins. We speak to Renishaw about the company’s role in creating the medal-winning Lotus x Hope HB.T
Seven medals at the Tokyo Olympic Games – three gold, three silver and one bronze – is an outstanding track record. The Great Britain cycling team was helped to that victory by the Lotus x Hope HB.T track bike, the design for which saw valuable grams shaved from its weight and drag reduced to a minimum.
That design, too, was a heroic team effort. The HB.T was built by Lotus Engineering, which also designed the iconic 108 and 110 bikes ridden by Olympic gold medallist Chris Boardman in the 1990s, in collaboration with cycling component manufacturer Hope Technology.
British engineering company Renishaw joined the bike development team in 2019 and, as an official team supplier, it contributed additive manufacturing (AM) expertise in order to develop lighter, more complex components than would have been possible using traditional manufacturing methods.
“The UCI [Union Cycliste Internationale] rules for international competitions around forks and seat stays allowed this innovative bicycle, but this presented a huge challenge to make the bike light enough to be fit for Olympic competition, so optimising strength to weight was key to success,” explains Ben Collins, a design and development engineer for Renishaw’s Additive Manufacturing Group, who was involved throughout the project.
“It was exciting to see Renishaw’s additive manufacturing expertise play a pivotal part in Great Britain’s push for Olympic gold medals at Tokyo,” continues Collins. “This was a brilliant achievement for the cyclists and a great showcase for the benefits of additive manufacturing.” Each rider had a bespoke bike set-up, custom-built to maximise their aerodynamic performance and power output from their ergonomics.
Renishaw initially used its AM expertise to rapidly produce polymer and metal prototype parts to undertake aerodynamic testing of the new designs and ensure that parts were light, geometrically correct and strong enough to endure the strain from riders.
Two versions of the handlebars were developed, with Renishaw playing a key role in both. The Lotus Sprint drop-bar handlebar was used in group-start events like the Omnium and Madison. The Lotus Pursuit, meanwhile, is for time-trial events like the Team Pursuit, where minimum drag is key.
After proving the concepts, the handlebars were manufactured in titanium on a Renishaw RenAM 500Q AM system, with each detail customised for the individual athlete.
While the frame was built using pre-preg carbon fibre, 3D-printed titanium was used to manufacture further elements around the bike that combined the various elements – from the fork crown to the lug used to join the seat stay to the tube.
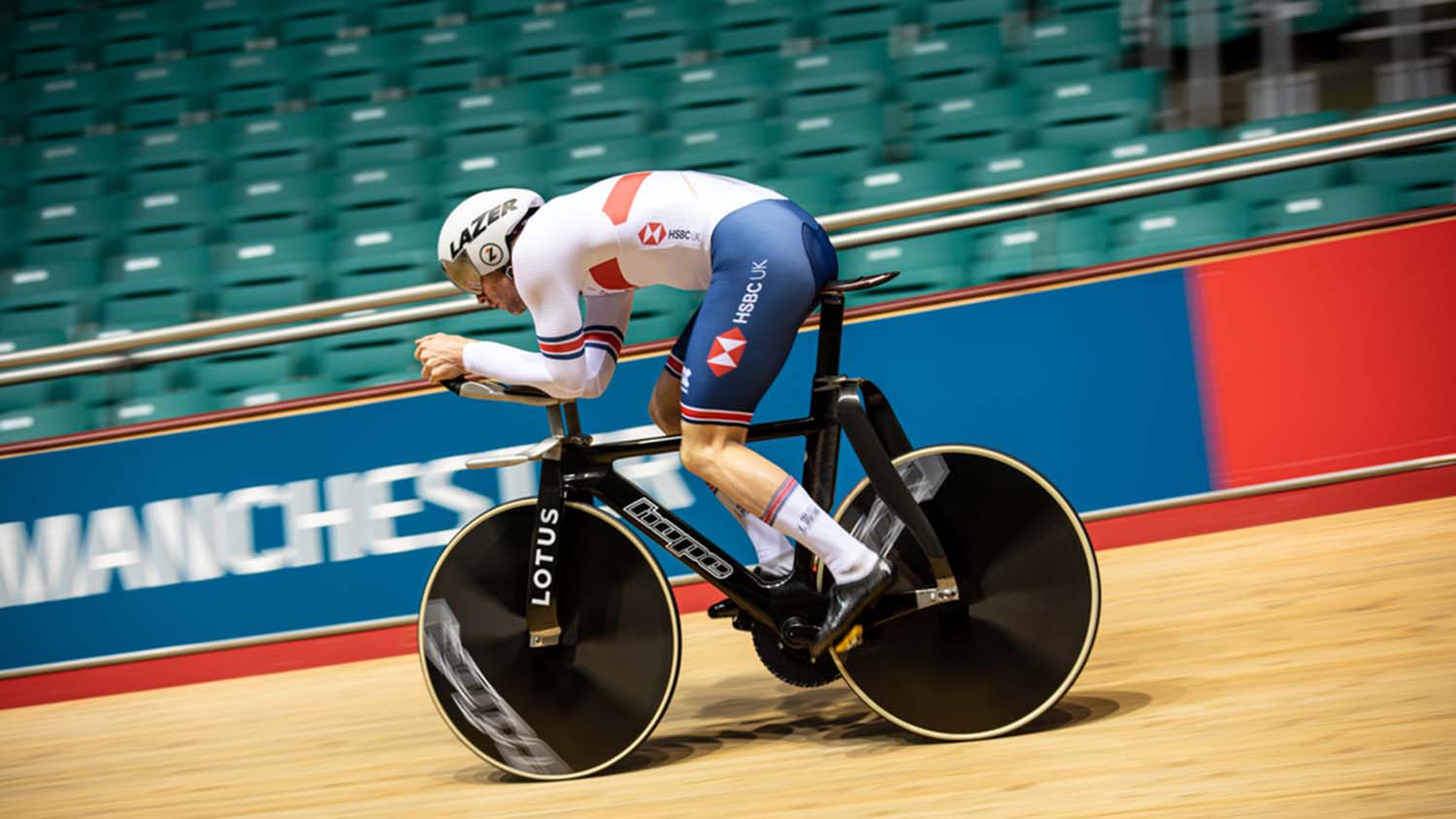
British Cycling head of technology Tony Purnell says that the design was new and brave, a move that threw up lots of challenges, to which Renishaw rose with aplomb.
“The Renishaw team has worked with the engineers to do the refinement at breakneck speed,” says Purnell. “In the past it would take months to go from the drawing board to a piece that you could try in the test rig or in the velodrome – and now we can do it in weeks.”
As cutting edge as the HB.T is, UCI regulations state that any Olympic Games track race equipment must be commercially available. And that means that you, too, could be the proud owner of a full spec model for somewhere in the region of a cool £30,000. Handlebar choices alone reportedly cost between £1,550 and £4,050 – but it’s pretty much impossible to put a price on what victory means to the team behind the bike.