CogniCAD 3.0 – There’s a groundswell of interest in topology optimisation and generative design, but as these solutions get more complex, many of their benefits could get missed. We take a look at a system that aims to bring back simplicity
If there’s a type of technology that’s currently getting some time in the limelight, it’s topology optimisation – along with its cousin, generative design. In truth, the terms are used interchangeably to describe the same concept: getting a computational device to solve an engineering geometry problem.
The thinking behind it goes something like this: Give the computer a set-up – in other words, a design domain in which to play, information on what to avoid, some boundary conditions it has to solve – and let it do its thing. The focus could be a structural problem. It could be a thermal or fluid-flow problem. It could be something else entirely.
It’s into this field that ParaMatters has stepped with its CogniCAD offering. The company was founded by simulation industry veteran Michael Bogomolny and is backed by XponentialWorks, the venture investment outfit set up by former 3D Systems CEO Avi Reichenthal. Its product, meanwhile, is a cloud-based system, which works on a token-per-use basis. So shall we see what it can do?
CogniCAD 3.0 – user experience
CogniCAD is browser-based, which means no install to perform. It’s just a case of registering for the service and away you go. As previously mentioned, usage is based on credits. In other words, you only pay for what you compute and use. You’ll get 30 credits for free and then pay for additional credits – but more on this later.
Once logged in, you’ll find a relatively simple interface showing existing projects and a menu of studies you can perform. On the generative design front, the system currently supports both structural/ mechanical problems and thermal studies.
Alongside these two core functions, there are supplementary tools to help with aspects of design for additive manufacturing, such as supports design and data repair. But since we’re here to talk about optimisation, I’d like to focus on the mechanical tools.
CogniCAD – getting started
To begin, you’ll need a set of geometry to define your optimisation study. CogniCAD uses STEP as its format of choice. There are a few caveats and requirements for this import process.
Above all, you should have all of your geometry contained in a single file. And by all your data, I mean your design domain volume, as well as your required and/ or non-design features, which should be represented as an exported assembly rather than a multibody part file.
Once that’s uploaded, you enter the Mechanical/Structural workspace. If you’ve used simulation tools before, this will be pretty self-explanatory.
First, you work through the process of defining materials (either from scratch or using the built-in library), then you identify which geometry defines the design space and which represents the design features that need to be retained.
Defining the load case
The next step is to define the load cases. Here, you have two options. If you have a clear understanding of your project, you can progress through a familiar workflow, defining static loads (force, moments, pressure, acceleration and so on) as well as vibrations (frequency). The system can also handle thermal design.
You then define your goal. This might be to minimise mass, increase stiffness, or some more complex combination, such as mass minimisation under stress constraints while maximising fundamental frequency.
There are symmetry controls as well as manufacturing controls (to optimise for either additive manufacturing or investment casting). Then it’s time to set the system running. Only at the point of computation are your credits/tokens consumed. The system works its magic and presents you with your result.
Another option is to instead use the CogniCAD AI engine, getting it to put its artificial intelligence magic to work on defining your loading conditions for you.
This might be useful if you’re just experimenting or exploring ideas. As its developers explain: “Based on ParaMatters’ experience and data collection under the hood, we define typical load cases per application in order to get a very robust model, even if the user doesn’t know the load scenario.”
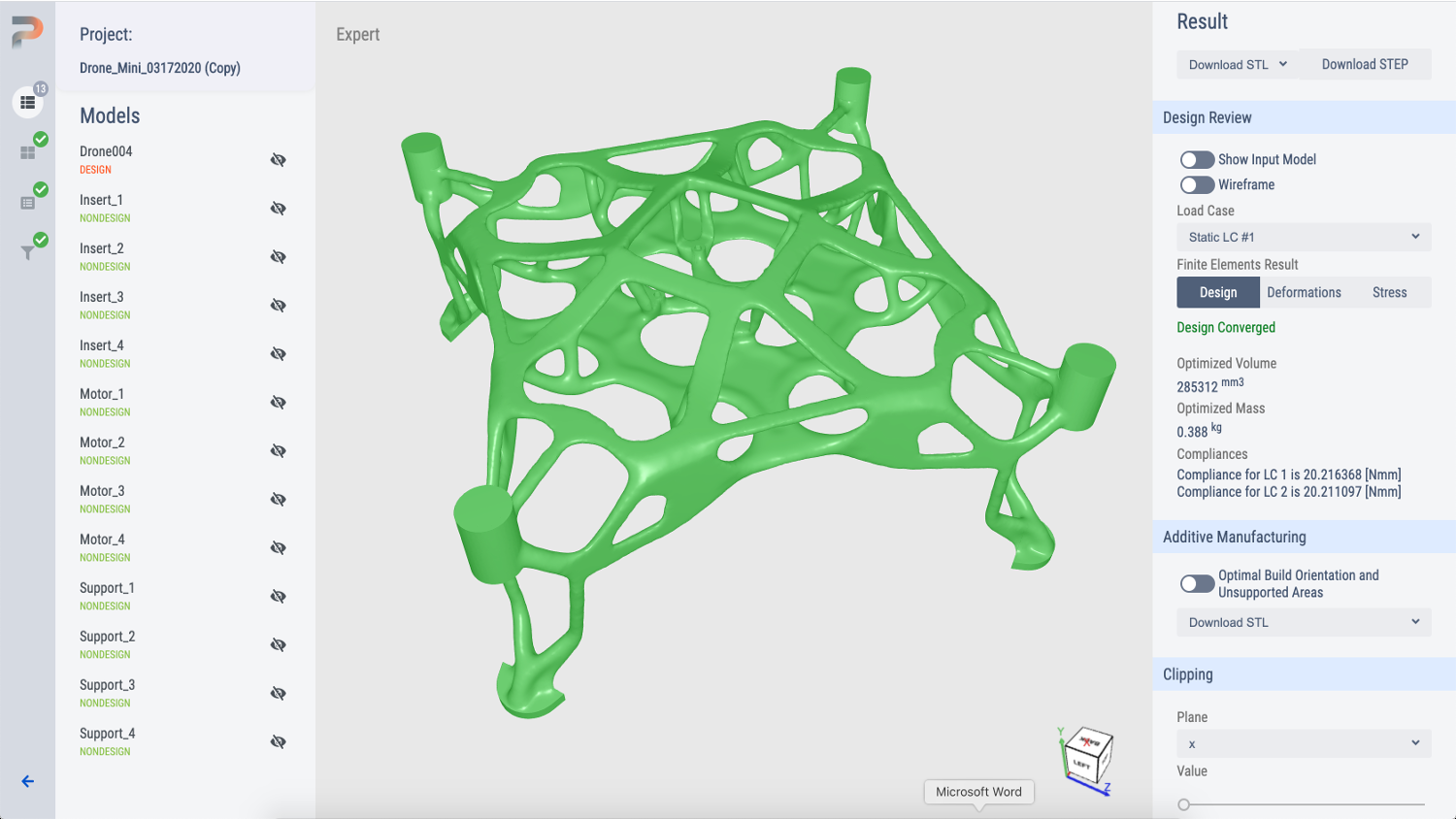
CogniCAD 3.0 – inspecting results
Whichever route you take, you’ll end up with an optimised form. The results inspection workspace brings up the 3D model, showing it in the context of your defined geometry. This is dynamic and can be panned, zoomed and rotated as per usual. A useful sectioning tool is also provided.
Your model can be shaded (along with the more useful numerical data), in order to show how the part deforms and where stress concentrations lie. Both of these can be filtered to a specified axis.
In many cases, this is where a topology optimisation workflow ends. The user downloads an STL of the results and perhaps passes it back into the CAD system.
CogniCAD, however, has a few extra tricks up its sleeve. While many optimisation systems will give you a mesh-based result, in CogniCAD, the team has developed its own method of taking the voxel data from the results and providing you with a smooth, surfaced part file that can more readily be imported in your CAD system of choice for further work and/or validation.
There are also a number of additional tools that allow you to export your results in the most appropriate orientation. Here, you’ve got a few options. First, you could send out those results using the coordinate position of the original file, so it will import back into your CAD system in the same position as the set-up geometry with which you started.
Your second and third options, meanwhile, pertain to additive manufacturing, allowing you to automatically orientate the part either for minimum supported surface or for minimum volume of supports.
What happens then is that the system makes its calculations according to the target and builds a dummy set of support structures, typically based on powder bed metals processes.
In conclusion
Whether you consider a system like CogniCAD to be generative design, topology optimisation or something else entirely, it’s probably fair to say that this offering is playing in a pretty crowded market.
There are a number of tools available here from a wide range of vendors. Some of them are decades old, others are much newer.
The goal, for the majority of them, is the same: take a set of inputs and boundary constraints and use them to arrive at an optimised form, which can then be pushed into the engineering validation process.
Where these systems tend to differ is in the steps that they make the user navigate and the quality of the results they achieve at the end.
Where CogniCAD stands out from the crowd is by offering features that make the software genuinely more usable than many rival systems. For a start, it’s CAD-agnostic. Some might see this as a benefit, others as a hindrance.
Personally speaking, I think that having a system like this uncoupled from your CAD could be a real plus, especially when you’re working with larger teams and/or multiple CAD systems.
Another big differentiator for CogniCAD is the simplicity of its set-up process. To get good results from any optimisation process, you need to understand how best to set up your study, ensuring you include all the loads, constraints, boundary conditions and materials correctly.
You also need a good knowledge of how your product operates and the ability to define performance in a simulation-based system.
That said, a system like this could equally be used to explore a design space quickly and roughly. The AI load definition tools do this for you. You give it the geometry of the design space, tell it where it’s fixed and let it do its thing.
That could be incredibly powerful in the right hands. It’s a valuable way not just of exploring a design space, but also getting a great view of the power of optimisation to fuel experimentation, before you decide to embark on a more intense, all encompassing workflow.