Royal Enfield is an Indian motorcycle company with very British roots.
While the company began life in the UK, its legacy in South Asia stretches back to the 1950s and a partnership with Madras Motors that led to the formation of Enfield India and the design and build of the legendary Royal Enfield Bullet in what is now Chennai.
By the 1960s, all parts were being produced in India and, during that decade, UK facilities in Redditch and Burton on Avon were shuttered.
But today, the company once again has design and engineering teams in both India and the UK, having assembled a formidable array of talent and technology at its UK Technology Centre at Bruntingthorpe Proving Ground in Leicestershire.
This facility has played an important role in a remarkable turnaround, which has seen Royal Enfield transformed from a brand that was struggling at the turn of the millennium to a thriving concern, selling a thoroughly modernised product that hasn’t sacrificed any of the beloved styling and character that made it popular in the first place.
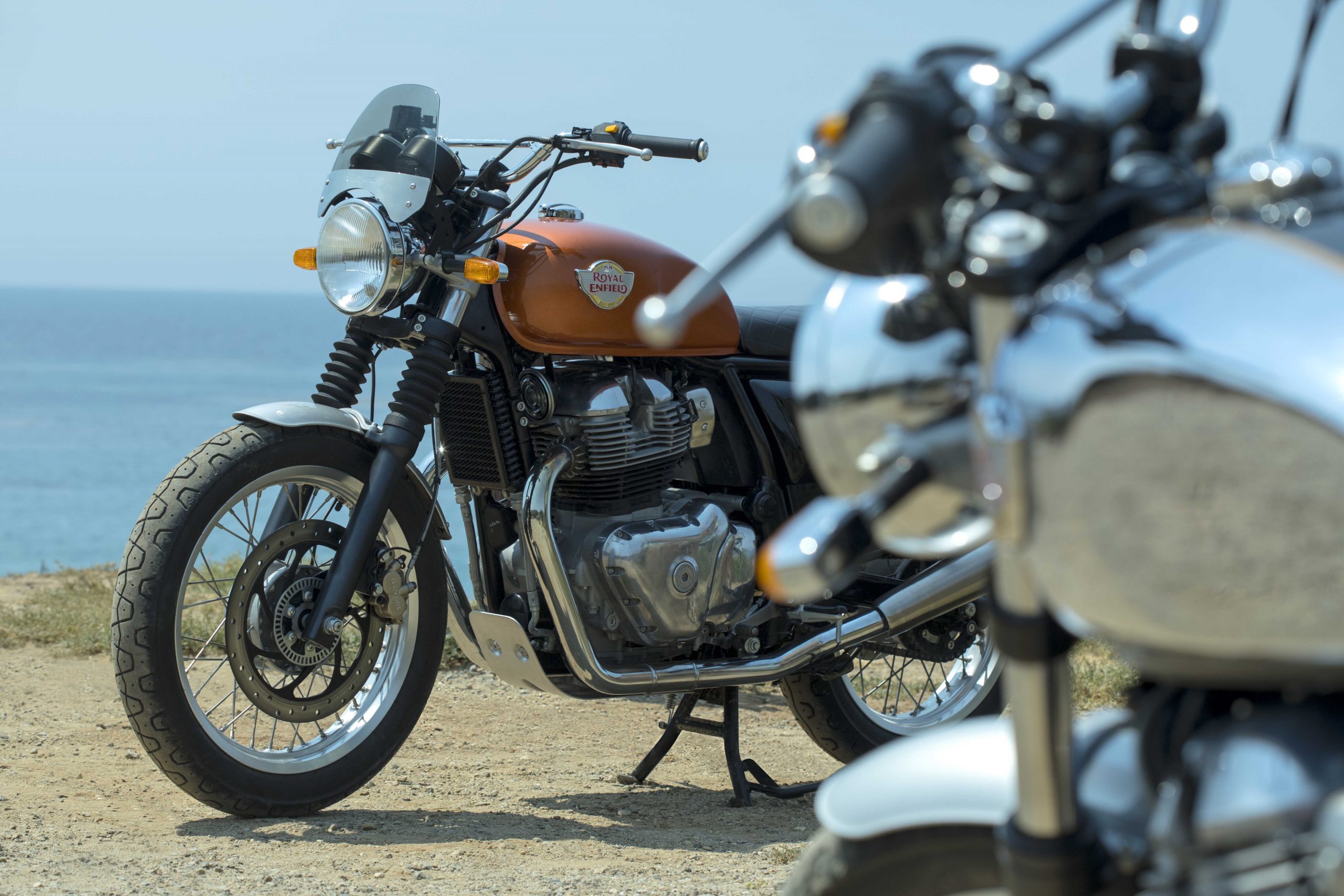
Royal Enfield – Power change
Royal Enfield enjoys a healthy presence in India, a market where some 20 million motorcycles and scooters were sold in 2019.
The company claims it built more motorcycles last year than all the European and North American motorcycle manufacturers put together.
It could still be vulnerable to an economic downturn in South Asia, however, which has recently led its leadership to shift focus on to European markets and the higher end of the Indian market.
It was as a result of this strategy that the P Platform was born – basically, a platform for its twin-cylinder 650cc engine models, or the ‘Twins’.
These are the Continental GT and the Interceptor. “In terms of the variance between them, one’s a classic bike and the other is a cafe racer,” explains Rod Giles, Royal Enfield’s head of CAD and CAE. “But actually, the difference is a handlebar tank and seat. That’s it.”
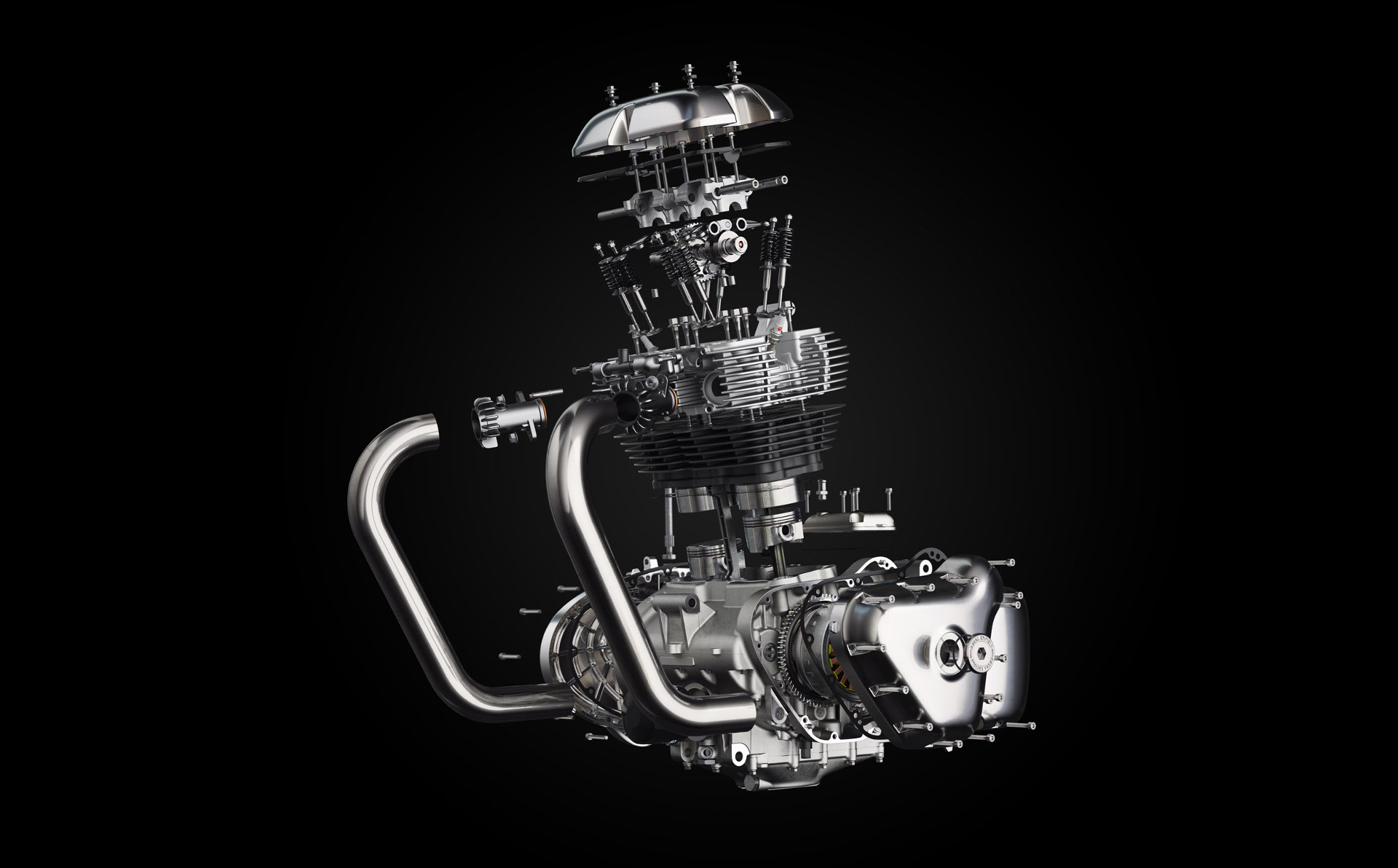
Riders are sometimes misled by appearances, and anticipate a very different experience of the two models.
In particular, it amuses him when journalists reviewing the bikes write about contrasts in how they feel and ride.
It makes him want to ask them, ‘Are you sure about that?!” Either way, the two machines both had to embody the Royal Enfield DNA, even down to the distinctive, ‘engine beat’ sound that is much-loved by Indian audiences.
Styling inspiration, meanwhile, was drawn from the original Continental model from 1962.
Royal Enfield uses a ‘stage gate’ system of product development, with initial phases carried out by the team’s industrial design and strategy heads.
Here, specifications are created for the motorcycles and vital decisions are made about how they will look.
This involves 3D concept modelling in Autodesk Alias, Rhino 3D, 3ds Max, Maya, VRED and V-Ray.
Once this stage is complete, the concept passes through ‘Gate Two’ and into the hands of product developers, where it is transformed into a solid engineering model.
This can be a ruthless process, says Giles. “Inevitably, what happens is that, by the time we get to the first prototype, there’s nothing left of what the original concept bike was,” he jokes.
Class A and styled surfaces – typically parts like the engine covers, fuel tank, headlight surround and seat – are owned by ID and remain fixed throughout development.
PTC Creo is the primary CAD tool used for product development, with Royal Enfield having 266 PTC Creo users spread between its Indian and UK offices.
Around 180 of them are “hardcore users”, he says. “The exterior surface is the starting surface. We don’t try and copy that in Creo, or anything else,” he explains, describing how the team transforms those surfaces into a solid model before working on the chassis and powertrain.
Following the announcement of the design team’s concept models for the 650cc Continental GT and Interceptor, such was the general interest and excitement generated that the P Platform needed to shift into accelerated development.
Time was of the essence. “We had to make sure that we got a lot smarter,” says Giles.
“With assemblers, particularly when you’ve got two variants of bikes that look different but share the same platform, you’ve got to handle that much more elegantly than had been done before.”
This included taking the gamble on an early release of PTC Creo 4 and integrating Windchill as its PLM system.
“There were challenges with that, because there were bugs – but because we could identify them and get them fixed by PTC, by the time we got to [a later version of] Creo 4, a lot of that was fixed,” explains Royal Enfield CAD manager Adrian Marshall.
“So, we had a plan in place to deal with that, and it’s what allowed us to go to that early release, because then you get all those benefits, rather than have to go to [Creo] 3 and do another upgrade later on that year.”
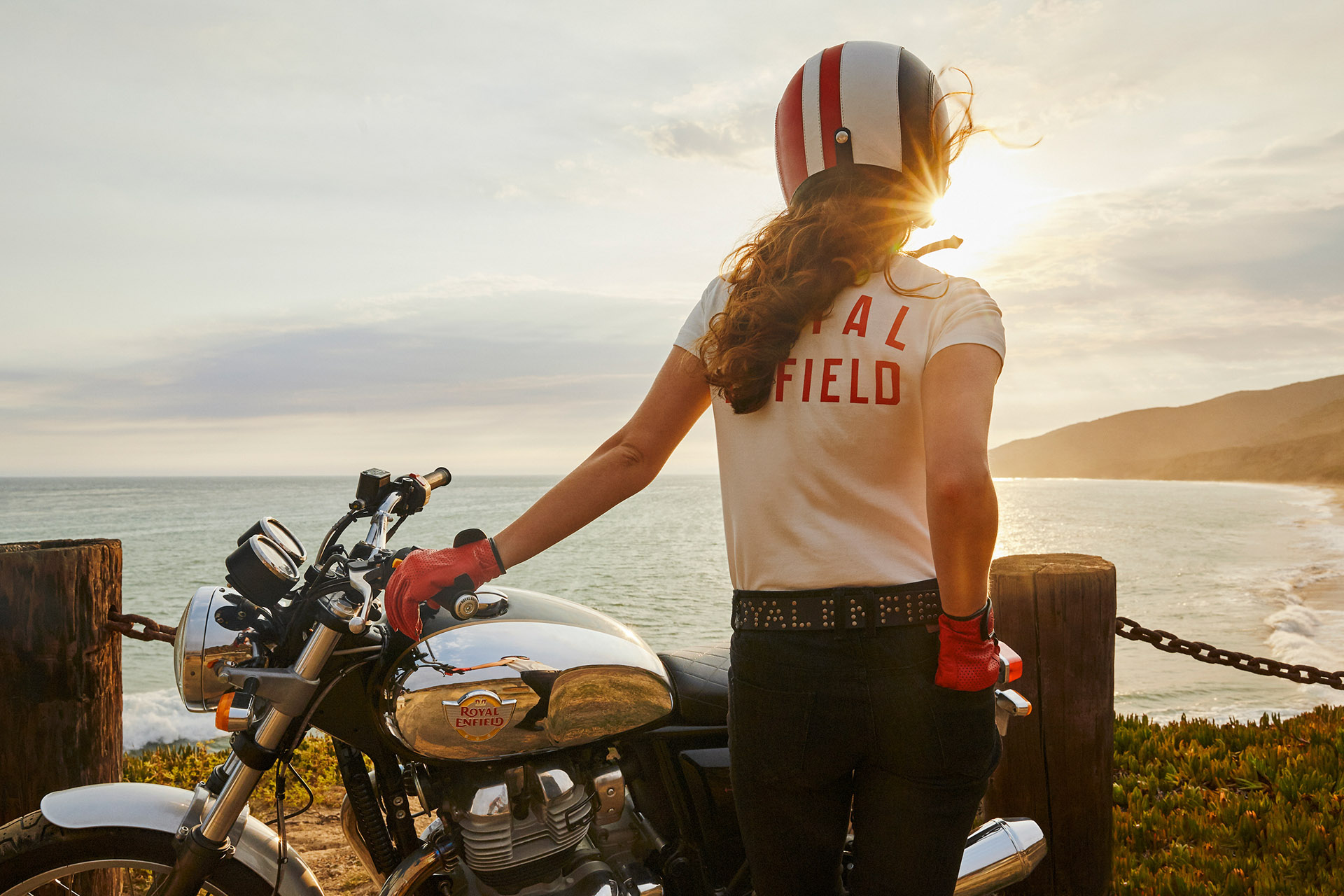
Full throttle
The engine was the first consideration. The development team jokes that this is ‘Gate One-and-a-half’, since the powertrain takes the longest time in terms of development and testing.
Everything from the original concept engine design had to be overhauled, leaving little more than the 650cc twincylinder capacity and the 270-degree crank that struck a chord with the concept-launch audience.
The engine size was kept reasonably small to make the bike light and ensure it handled well, keeping it within the medium-sized A2 category of bikes for Europe, but still a comparably ‘big bike’ in India.
Air cooling decisions were driven by the need for simplicity and reliability in adverse climates, but primarily by the desire to remain faithful to the classic styline of the motorcycles.
This gave the design team a challenge to over come, given the stringent regulations around emissions in both India and Europe, “but we were able to obtain a good cooling solution by carrying out a full vehicle CFD/CHT analysis,” says Giles.
Elsewhere in the engine, internal cooling jets were designed especially for the new model, spraying oil on the cylinder heads to help better control engine temperature.
Given its extra power compared to other Royal Enfield models, it was decided that riders would benefit from more stability, something achieved by lengthening the chassis.
Although pushing the front wheel forward to extend the bike’s length was seen as a major engineering challenge, it didn’t take that long to design, due to the way the Royal Enfield team marshals its data flow.
Sub-modules for logical groupings of bike sub-assemblies (wheels, brakes, handlebar, fuel tank, fuel system and so on) are controlled by their own General Arrangement (GA), which then references a top-level GA.
“Because we could quickly update the model with a new dimension, the whole frame went with it, effectively,” Giles explains. “It’s not completely automatic. There’s still a bit of work to do, but it saves a lot of time.”
However, not everything is purely performance-driven. Brand styling plays an important part, too.
The engine’s shape has been stylised to give it a vintage aesthetic. Giles notes that, in days gone by, when none of the “computer simulation stuff” even existed, size and shape was a matter of trial and error.
If the engine for a bike this size was being designed for performance today, it would likely be half the size, he says, but the P Platform maintained the oversized body, not just to respect the brand’s heritage, but also because visually, it makes it look good.
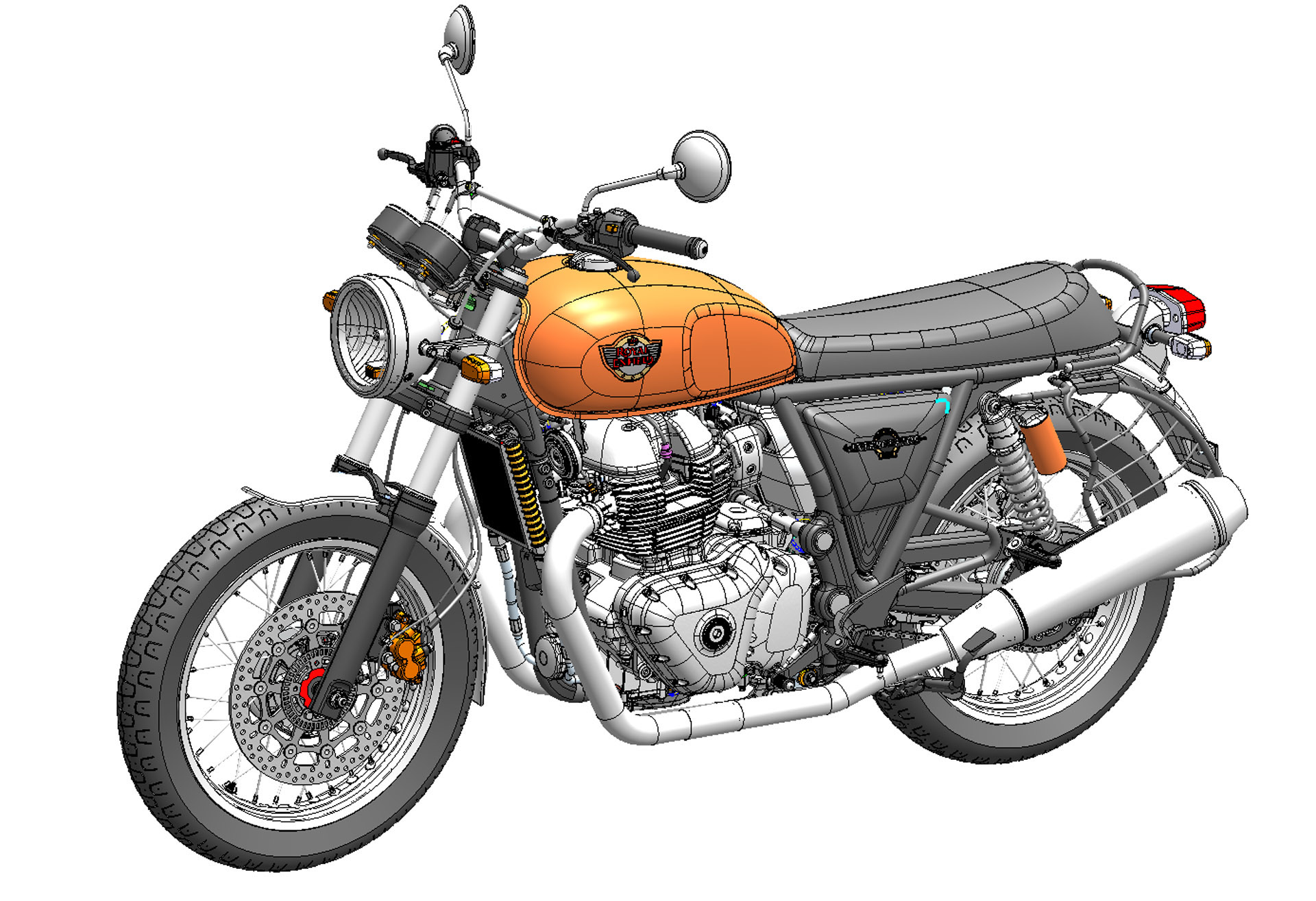
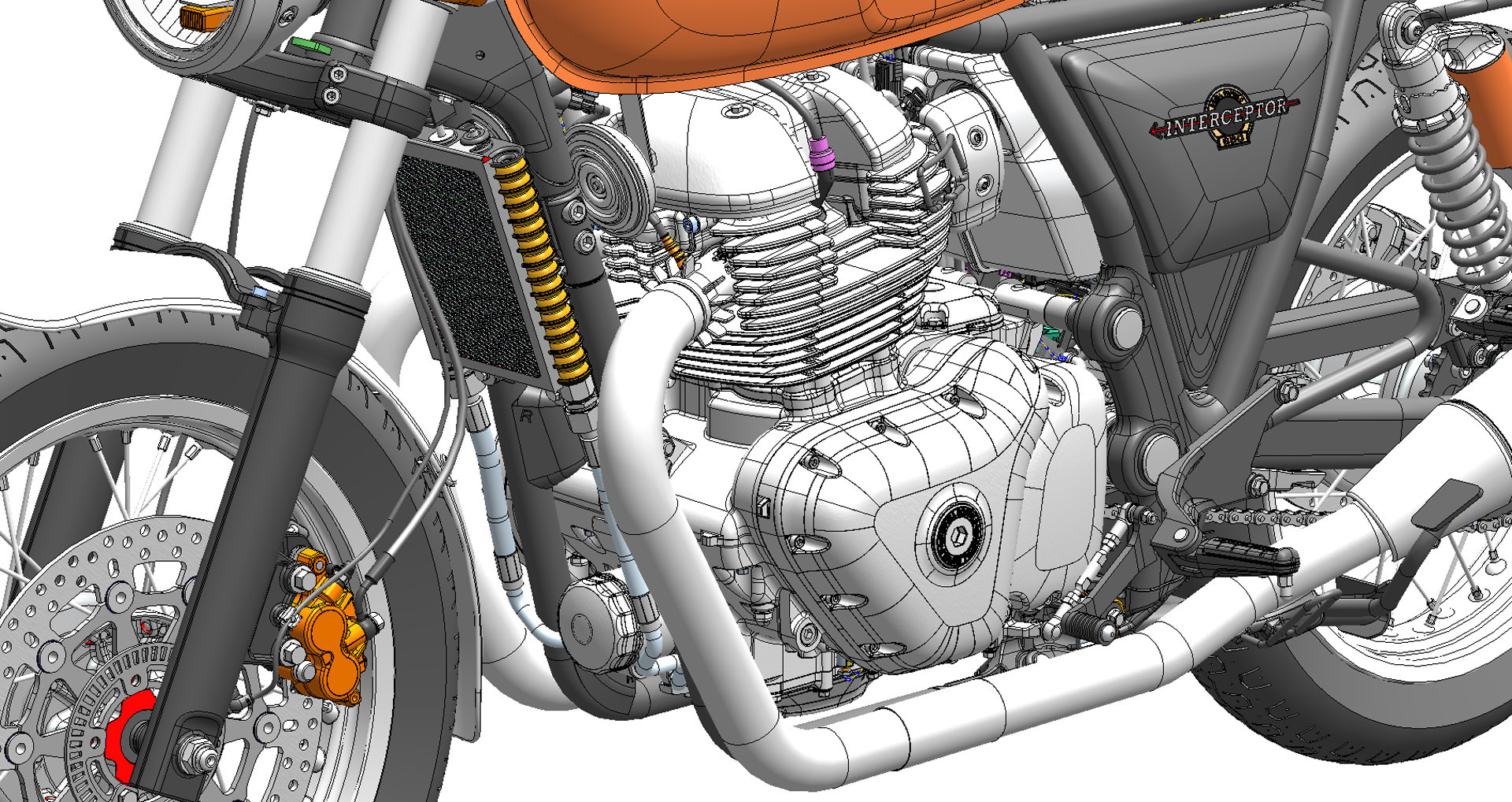
Royal Enfield – Living for simulation
A shortened design cycle meant more simulation was moved upfront in the process to help speed up engineering.
A wide range of software was used, including Abaqus for engine durability analysis; Altair HyperWorks for chassis build strength; and Siemens Star-CCM+ for the CFD side of things.
But there were many others, he says, adding, “I can’t think of anything we don’t simulate.”
In fact, Royal Enfield would do more simulation if it could, he says, but many component suppliers keep data to themselves.
In particular, PTC Creo Simulation Live enables engineers to perform simulation on parametric models in near-real time.
“Like most analysis, it’s about making inferences from the information you’re given. That’s the really difficult bit,” he says.
“It’s mega-amplified with Creo Simulation Live, because you can only do very simple things. It’s a direction-indicating factor – like a compass, not a GPS system.”
The software has already proved itself an “absolute lifesaver”, in terms of saving the team countless days waiting on traditional simulation results, but he is keeping it out of the hands of the designers – for now – until he’s finished testing it and making some decisions around how it should be deployed and how many people should use it.
That said, the technology keeps proving its value in new ways.
“At five o’clock last night, our head of powertrain said: ‘I need to make a decision on the way we’re going on the structure of the cylinder head.
I need to have a result by 11 o’clock tomorrow morning’,” he recalls.
That led Giles to immediately run an evaluation in Creo Simulation Live of three possible cylinder head assemblies.
He was able to dismiss one assembly while still sat in the meeting and ran the analysis of the other two models that evening.
A decision was successfully made the next day. As Giles puts it: “That kind of gives you an idea of how powerful it can be, but also that you have to be really careful about how you use it.”
While Creo Simulation Live is a relatively new addition, Creo Behavioural Modelling Extension (BMX) has been used by most of the Royal Enfield team for over a decade and forms part of its everyday workflow.
Coupled with Creo Simulate for FEA analysis, the credibility of the results stand up well to real-world tests, helping to accelerate the product development cycle even more.
If a designer has used Creo Simulate on a wheel design, for example, Giles says, he knows it will pass analysis first time when it comes to him in the CAE department.
“And once it has passed all those tests, we go straight into tooling.”
Simulation even extends to the noise the twin 650cc engine and its exhaust produce, allowing the team to simulate the required pass-by noise test before even building a bike.
This extends to optimising rib structures on the bike engine covers, which can be optimised for rigidity, helping reduce engine vibration noise.
Recent bikes have passed the pass-by noise test quite easily, allowing the team to increase and tune the noise of the exhaust to give them that extra character that fans love.
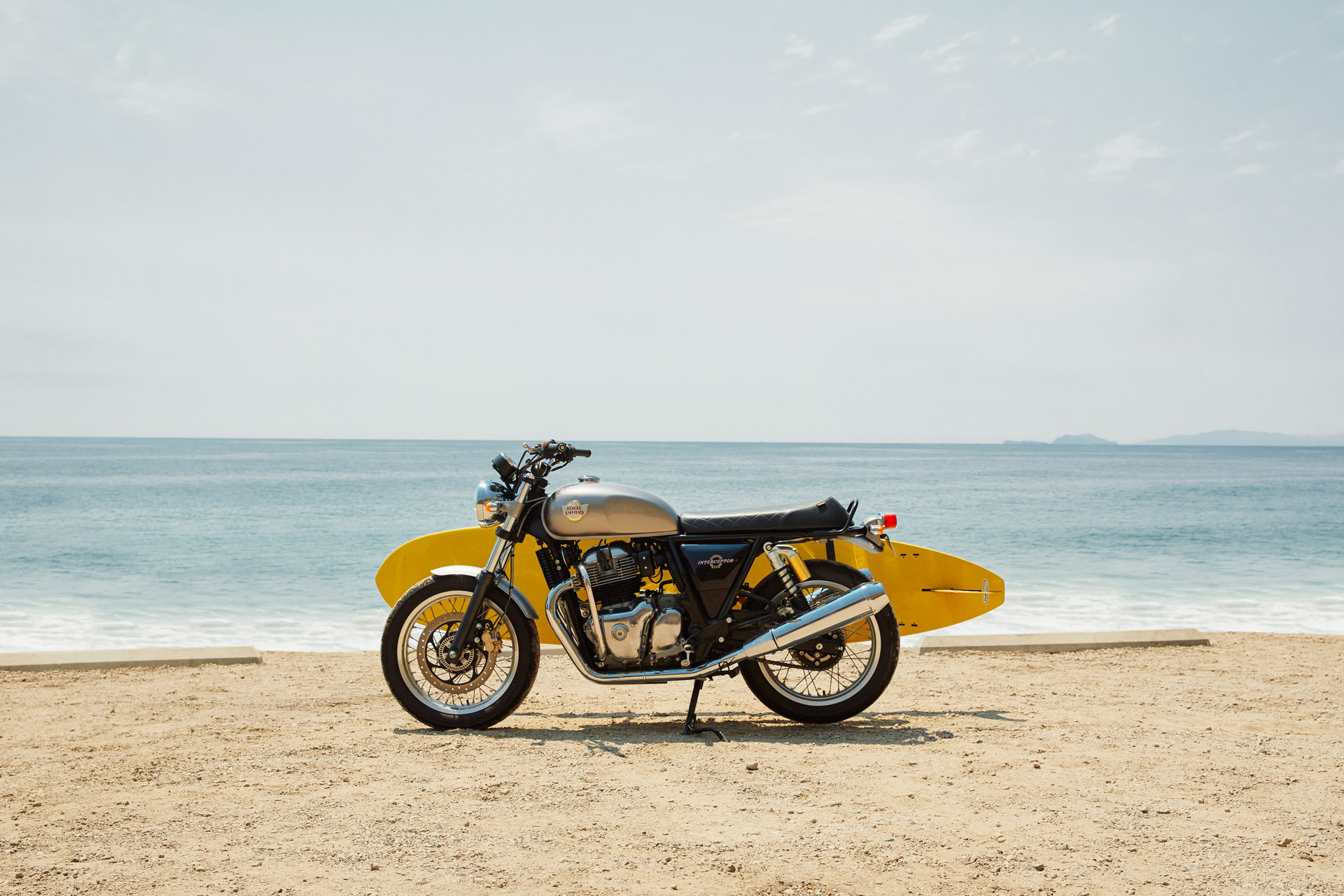
Royal Enfield – Augmented additions
Royal Enfield is now working with PTC Creo 5 and Vuforia Studio is growing in importance as part of its toolset, as the company looks to utilise its existing CAD data as the basis for augmented reality (AR) experiences.
Already, Royal Enfield is piloting AR for training at Royal Enfield’s service centres and for new workers joining production lines in India.
The fact that the company can work with technologies from a single vendor, rather than using a bundle of unaffiliated software and third-party add-ons, gives CAD manager Adrian Marshall a lot of confidence, he says:
“Because it’s a PTC product from end to end, you get the integration consideration between each product.”
Rolling out such new technology to a huge customer base might be seen as a daunting task, but with little to lose by capitalising on its existing 3D CAD data, it in fact provides a way for Royal Enfield to bring the brand closer to its fanatical customers.
The company’s marketing proudly boasts that it’s the oldest motorcycle brand in the world still in production. With a new digital backbone, it looks on track to maintain that status for years to come.
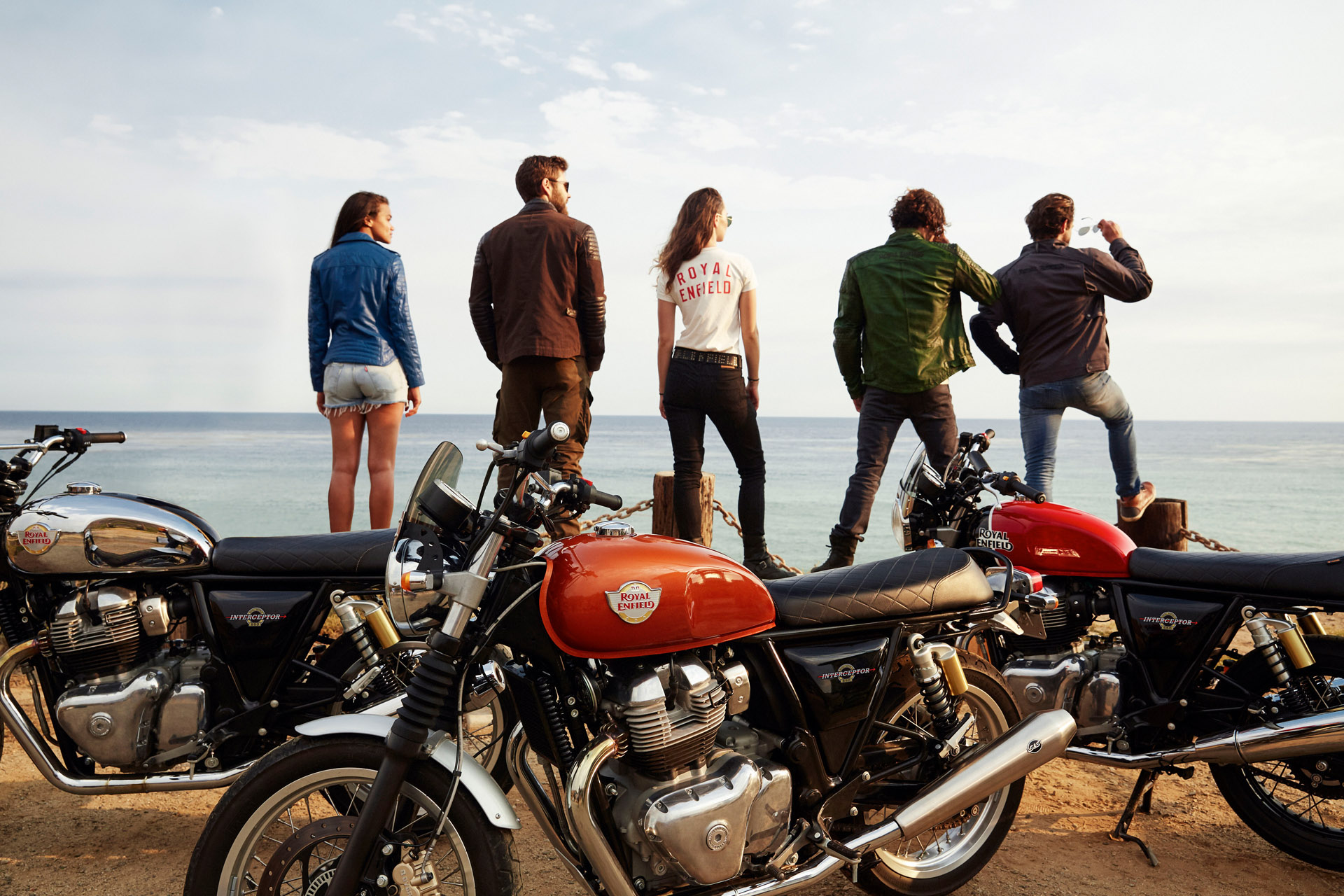
Royal Enfield’s push for automation
Boosting the amount of simulation work conducted at Royal Enfield may have helped speed up the development process, but it also brought with it new challenges to overcome.
About three years ago, the company’s head of CAD and CAE Rod Giles realised that, with the volume of work coming in, he couldn’t recruit enough people.
Even if he did, he adds, the associated software costs would have been “ginormous”. That set him on a mission to automate as many of the company’s CAE workflows as possible.
“Royal Enfield made an investment of quite a few rupees in developing automation tools with our software partners,” he says, describing how the company began to build up a whole library of tools to improve the workflow for its engine and chassis durability simulations.
Prior to automation, the process of setting up and running a standard engine durability simulation took 10 weeks.
If it had to be run again, it took nearly as long again. With this in mind, the CAE team worked with simulation and analysis expert Technia to help identify bottlenecks in the process.
As Giles explains: “We’ve got all sorts of tools which work together, so we actually portioned the task up into various areas where there was a real bottleneck in terms of time taken to do things.”
A classic example is an engine model that features over 100 bolts.
Royal Enfield will typically perform the analysis with it pre-loaded, “so we’ve got to make all the bolts, attach them all together, and then apply the pre-load to get the engine to bolt up… That just took weeks and weeks, particularly when you’ve got thermal expansion effects to take into account as well.”
Since a motorcycle’s engine tends to take up the longest development and testing time, this was a massive issue – but it is also one that got solved.
Now, with a tool that was developed in conjunction with Technia, Royal Enfield just brings the engine in, a member of the CAE team hits the button, and the tool creates all the bolts in the engine, says Giles.
“You don’t have to tell it anything. It can find all the holes that are bolt holes and create a bolt on every single one in the correct, approved manner.”
The automation sets up the default pre-load for a given size bolt, something it computes from the model, the size of the hole and the choice of standard bolts available.
It’s cut down a job that used to take up to two weeks to perform to a task that takes two or three minutes.
Royal Enfield has also created a similar automated add-on for chassis analysis with the help of Altair, which allows it to import a 3D CAD frame and create a mid-surface.
From this, the user identifies all the edges that are welded, and the system applies welds automatically and meshes the model in the prescribed manner, meeting all internal standards.
It applies loads, boundary conditions, and, at the press of a button, can automatically generate a full report.
“Our wheel models have got 648 load cases on them,” says Giles.
“That’s just a single wheel. Run the wheel add-on, run the report generator, out pops a report 200 pages long, with everything on it.”
Automation has also been added to use cases for CFD models, helping solve issues around heat transfer and thermal expansion, where there are lots of factors that can prove timeconsuming for a human running the simulation and hamper its ability to work properly.
“We do all that automatically,” says Giles. “So now you just say, ‘Can you apply this CFD output file to this model?.
Bang – job done! Again, that’s probably saved about a week.”
“I think there’s over 100 surfaces that you have to load correctly with the correct loading profile, different profiles for different bearings, and different things they have to do.
That was incredibly labour intensive,” he says. “Now we drive that all from our Google spreadsheet: take the data from the MBD model, dumped into a spreadsheet, take that data from the spreadsheet, and then apply the loads in the correct manner, and build the load cases and so on.”
While Royal Enfield has dedicated time to working with third parties in order to achieve this automation, it has involved a great deal of in-house work too.
New tools are being created all the time, based on how regularly a particular calculation needs to be performed.
In fact, the team has gone as far as building its own handy calculator, regularly used by Royal Enfield engineers and designers. It’s written in Python, he says:
“The only reason we’re using a spreadsheet is to dump information out so that designers can look at it.”
He concludes: “It’s a massive time saver for the designers, it’s more consistent and it’s approved with this validated engineering tool.”
“Automation of simulation workflows is rapidly becoming the main offering from the Technia Simulation Centre of Excellence,” says Technia technical director of simulation Laurence Marks.
We undertook our first real automation project about four years ago – streamlining the building of pressure vessel models – and since then we’ve been involved in a number of projects aimed at reducing the time, and therefore cost overhead of making finite element models.
“The great thing about these projects is that we don’t take 5% here and 3% there away from the model build time. We’ve been reducing it to 10% of the original timescales. That has a major impact on how engineering organisations view the whole simulation process: It’s the key to so many new views and insights.
Automation isn’t any form of free lunch though, explains Marks. “It doesn’t just happen. You can only really achieve the huge speed ups if you’ve got a real grip on the process, and that has to include every aspect of it: basic simulation technology, quality and relevance of the data fed into the process, who is going to do it and who is going to use the results.
“With this knowledge/framework and a view on the art of the possible automation projects can be successful.
“Where they fail is when people try to make them 100% automatic in every scenario, rather than 90% in some. It really is about choosing the project and aims appropriately.”