Star of its own Discovery Channel series, Kindig-It Design is a high-end ‘restomod’ auto shop that has seen hundreds of custom hot rods, muscle cars and classics roll off its ramps.
Along the way, the work of Kindig-It owner and chief stylist Dave Kindig, who has been designing cars by hand since he was a kid, has attracted a cult following.
The workshop where these often over-the-top creations come to life, meanwhile, boasts some seriously talented manual metal workers, fabricators and mechanics.
But with more new projects to tackle than ever before, and all the work performed on an entirely bespoke basis, the workshop has had to evolve and digitise to become more efficient.
Vintage cars, for example, feature masses of complex surfaces, including body lines with slight curves and very few flat areas or straight edges.
And that means that being able to capture, clean up and transfer accurate surface data in 3D has become key.
With Solidworks already established as the solution of choice for CAD modelling and manufacturing data, the next steps involved the addition of a Faro ScanArm to 3D scan cars and components, plus an implementation of 3D Systems’ Geomagic Design X scan-to-CAD software to process the data.
“Right now, we’re working on some fixtures – we are scanning a 1953 Corvette – and then designing our fixture pieces so we can start doing composite work and building bucks off of that car,” says Kindig-It Design’s digital fabrication specialist, Greg Hebard, speaking from the company’s garage headquarters in Salt Lake City, Utah.
“We’re really happy with that combination of tools,” he says. “The Faro scanner works great for the size of pieces we scan – from engine intakes to entire cars – and realigning the scans in Geomagics X works pretty effortlessly.”
While the company has always worked with Solidworks and modelling, adds Kindig-It engineer Will Lockwood, scanning is a newer, more unfamiliar step, “but being acclimated with the whole design aspect of it really helped move us into scanning and designing with the Geomagics software.”
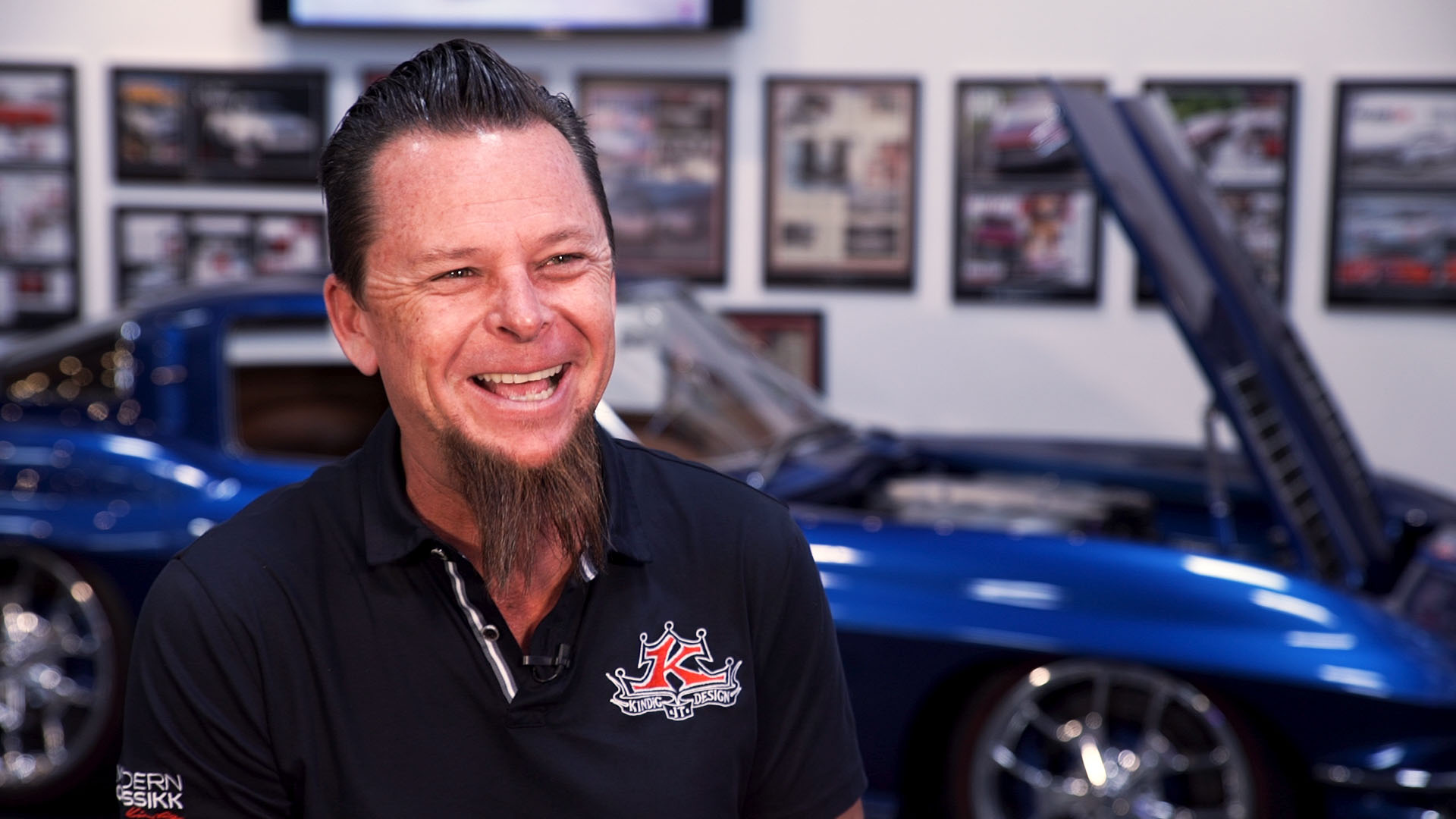
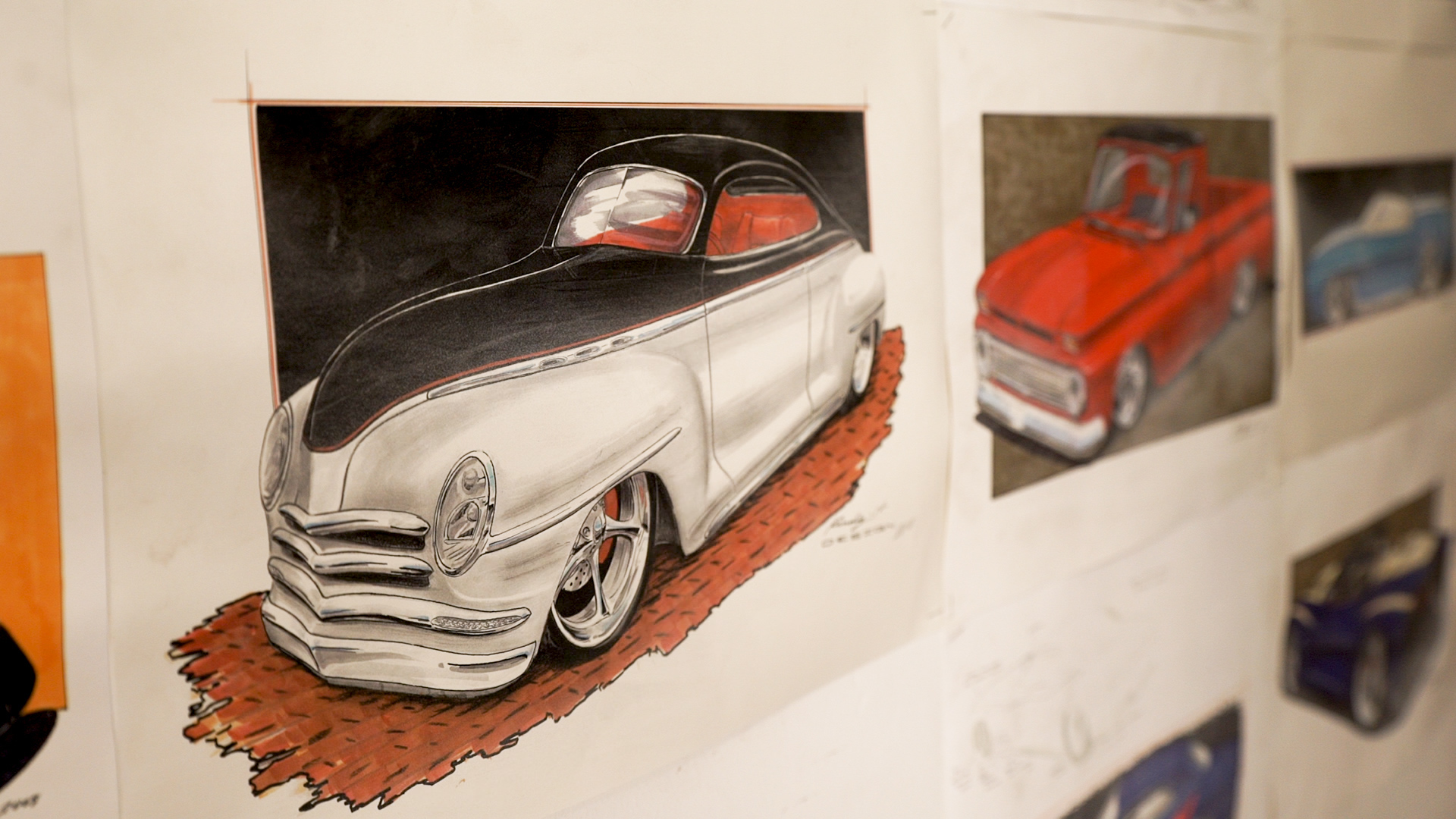
The use of the 3D scanner, combined with Geomagic’s Design X, has enabled a number of projects to complete first time and simplify traditional workflows – tasks like using dxf files to cut out templates, or using the scan data to help design brandnew tail lights for cars.
“We’re just shooting from the hip a lot of the time, figuring out ways that we can use the scanner – and I think a lot of it might be less conventional than what other people are doing,” says Hebard.
“We’re always just trying to experiment with it.”
Fresh classics
The biggest challenge that the Kindig-It Design team faces is creating more interesting and intricate parts that are by their nature harder to mock up or are impossible to do by hand.
The custom ’53 Chevrolet Corvette project is the biggest they’ve worked on to date. It involves constructing four units from Dave Kindig’s handsketched designs, with a view to building more going forward.
“We’re investing a little bit more time into each aspect of this project,” says Hebard.
“When Dave comes up with a design, he’ll just let us loose to figure out how we’re going to do these different processes, working within an entire car at once on the computer and implementing every component into a design, verifying all of our fitments and everything like that.”
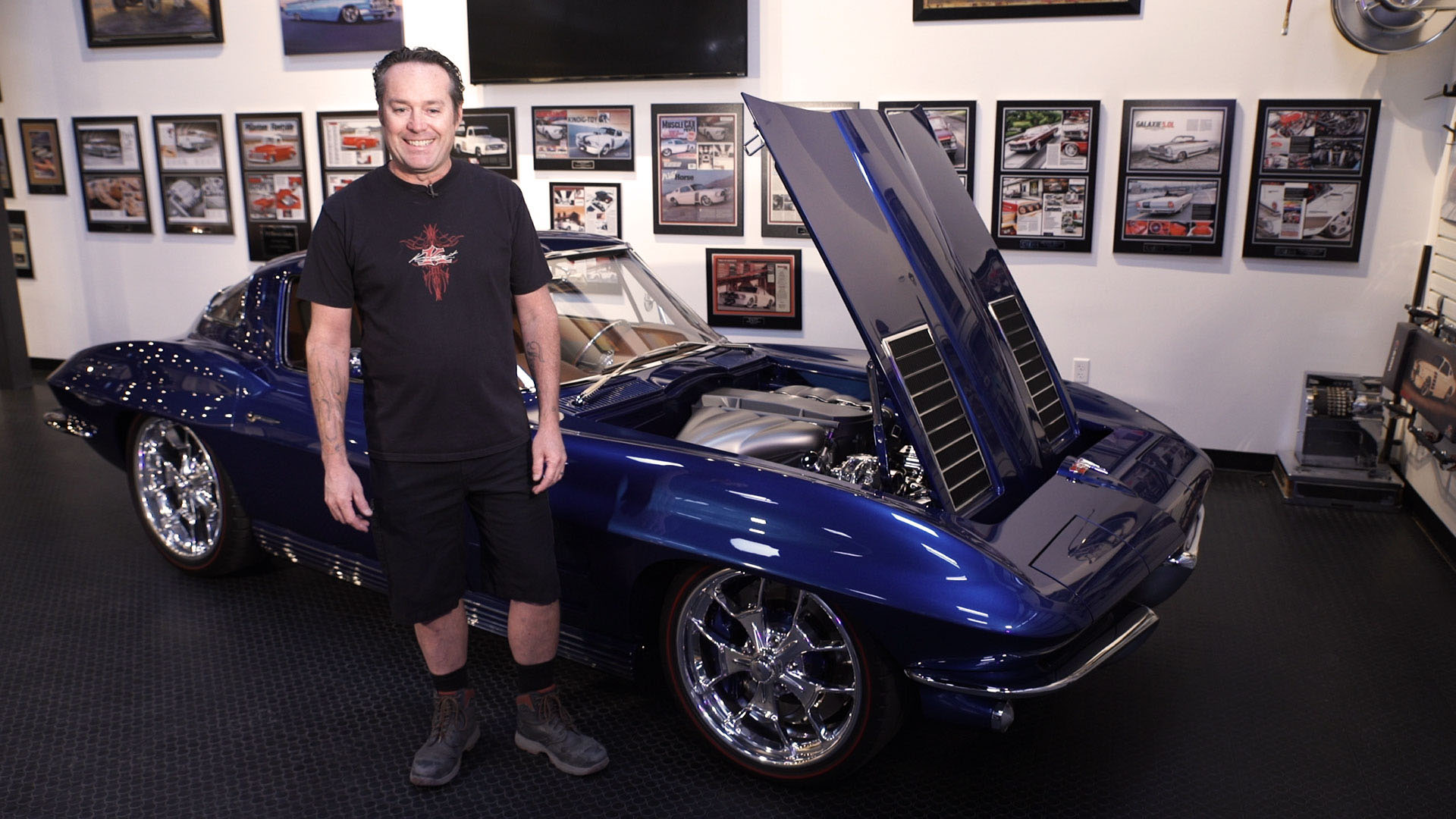
Key to the Kindig-It style is taking original cars and making them bigger and better, adding bigger power plants and fortifying the rest of the mechanics to handle new extremes in horsepower in the great hotrodding tradition, as well as adding greater levels of reliability and finesse to these old motors.
“The clearances are so tight, because these old cars had much smaller engines,” explains Hebard. “We put these massive engines in them and everything is a tight fit.
“The alternator’s close to the inside of the side of the engine bay; our [air] intake’s almost always within a quarter-inch off the hood itself.
“So, that’s always something you have to fight on basically every car.”
Designing all that in a computer, where the hood can become transparent in order to get a good view on those space limitations is “definitely important”, he adds.
“It’s been super-cool to be able to basically get the scan and then ‘see through’ to what you need to be able to,” confirms Lockwood.
“Now we have the scanners and we can see through where we need to, we can zoom in on where we need to be and build stuff that fits the first time. It’s been ultra-cool.”
Next on the to-do list is adding the integrated Geomagics For Solidworks solution to the equation for extra accuracy.
For now, however, the team’s pretty happy manually exporting parts out of Geomagics and into CAD.
It’s just another workaround, says Hebard, who’s been compiling the scanned parts for the Corvette project into Solidworks.
“Luckily, they seem to work pretty well,” he says.
There’s plenty of things changing at the Kindig-It Design workshop all the time, with the team looking to refine its design processes and make them more streamlined, so that the cars that emerge continue to reflect the company’s own unique style.