Gozney Dome, Gozney’s latest wood-fired oven, is designed for making restaurant class pizzas at home. Stephen Holmes talks to IDC about how it developed the initial concept and ensured the product was oven-ready for manufacture
Perfect pizza is the ultimate goal of all Gozney products, whether the company is supplying commercial ovens to restaurants like Pizza Pilgrims and Franco Manca, or outdoor ovens for domestic use by consumers.
Based in Christchurch, UK, the company was launched after founder Tom Gozney built himself a pizza oven in his own back garden, attracting the interest of local restaurants.
This early experiment quickly evolved into The Stone Bake Oven Company. Launched in 2010, the firm offers precast stone ovens, and has inspired celebrity chefs to use stone cooking at home. Initial products were snapped up for installation in luxury kitchens and were such a success that the company grew quickly, adding Gozney Professional Ovens to the mix.
Today, Gozney products are found in a number of world leading commercial kitchens and its consumer products have proved popular, too. The crowd funded Roccbox, for example, shrank the pizza oven to a portable format.
For its latest product, the Dome, Gozney wanted to make wood-fired cooking easy for home cooks, in the form of a versatile outdoor oven.
A dual-fuel approach retains the wood-fired approach – which gives the best taste and experience – but also means the user can switch to the convenience of a built-in gas burner.
That’s more flexible for customers and enables the oven to reach temperatures of 500-degrees Celsius, simply at the turn of a dial.
Design and engineering ingredients
During the Dome’s development, Gozney called on product development agency IDC’s engineering team to review its initial plans. “The overall challenge was to engineer how this product would be manufactured and put together,” explains IDC project manager Michał Uhman.
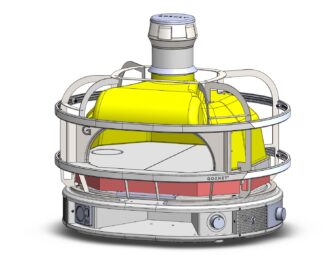
In a series of brainstorming sessions, Gozney and IDC came up with several innovative ideas to improve the design, including scalable engineering for size changes to the product in future and simplification of components for easier assembly.
While Gozney already had the look and feel of the product firmly in mind, IDC developed the internal engineering.
The Dome’s compact form houses both gas and electrical elements, as well as materials that react differently under high temperatures.
Based on its wide experience of manufacturing and sheet metal forming, IDC proposed a new approach to the outer metal pressings, taking into account the depth and angles that would best suit the smooth, domed geometries of the product.
The optimisation of the design for manufacture and assembly was carefully balanced with the need to retain the core functions of the internal geometry, in order to control the flames and retain the outstanding cooking performance of the oven’s original design.
“There was very little space for error,” says Uhman, explaining that there was also no time for a full prototype to be built to test out the design.
In fact, the only elements that were physically tested before heading to manufacture were a couple of 3D-printed models to test the fit of some small sections and a 1:10 scale model. “Other than that, we relied on all the internal expertise [at IDC],” says Uhman.
Gozney Dome – Ready to serve
Once the first packaged design was complete, it was a case of ironing out some small features and tolerances to ensure that all the parts came together with the neat fit that Gozney demanded.
IDC kept in close touch with the factory producing the parts in China, receiving feedback throughout and making any necessary amendments, ensuring they completed Gozney’s brief for a high-quality product.
The design and engineering work was all carried out in Solidworks, importing Gozney’s initial designs and building them out. This included the client’s ideas for a comprehensive range of accessories.
Several add-on fitments, for example, enable the Dome to transform into a Neapolitan pizza over, a bread oven, or a smoker – so it was up to IDC to flesh out these ideas, ensure they worked with the design, were manufacturable, and took into account issues like heat breaks between all the elements that the user would handle.
This was made easier by good lines of communication with Gozney, enabling the project to be completed in under six months, from first engineering plans to samples.
“On the outside, it looks very simple,” concludes Uhman. “But then it was about making sure that all the elements came together, including the sturdiness and the reliability, so that it fulfills the quality required by Gozney.”