Vorteq has set its sights on creating the fastest custom cycling skinsuit to help riders compete at their absolute best. We report on how a handheld 3D scanner is helping to shave vital seconds off medal-winning performances
With up to 90% of a cyclist’s energy output spent on overcoming air resistance, reducing the rider’s drag is paramount in a sport where every second counts. Vorteq has already created some of the fastest cycling skinsuits for professional track and road riders. It’s now building on its reputation with the launch of a custom skinsuit service for serious riders of all levels of experience.
Whether they’re professional riders or serious hobbyists, the reality is that money spent lightweighting a bike and its components might be better invested in more efficient apparel. After all, the most aerodynamic clothing can actually reduce their level of drag to below what they might experience riding naked.
In its bid to take skinsuits to a whole new level, the British company has invested in excess of $500,000 in R&D facilities at its headquarters at the Silverstone Sports Engineering Hub (SSEH) in Northamptonshire. This location enables it to test more than 45,000 different material, tension, and speed combinations in specialised onsite wind tunnels.
Created in custom patterns and fabrics, each custom skinsuit is designed to reduce the drag of the individual rider, helping them to achieve their own personal bests.
A 3D scanner is a crucial element in capturing the rider’s exact anatomy. In the hours that follow just a few minutes of scanning, data relating to size, patterns and fabric types are meticulously processed by a computational draping system and then assembled by Vorteq’s skinsuit team.
In the past, Vorteq used an arm-based scanner for 3D scanning race cars, bicycles and other machines. But when it came to using the scanner for capturing humans, the team ran into significant difficulties. In short, older 3D scanning technology wasn’t up to the job.
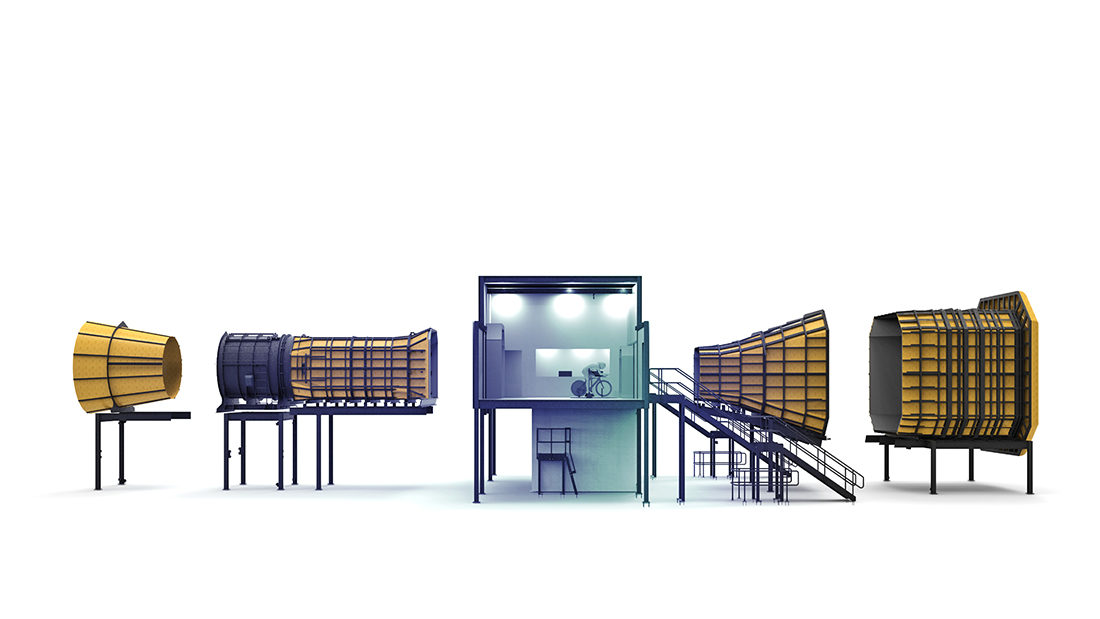
Freedom of movement
Following a consultation with Central Scanning, a 3D scanning specialist, the team at Vorteq was recommended the Artec Leo, a cable-free, handheld 3D scanner with a built-in touchscreen and an up to 80fps capture rate.
“The rider comes into the wind tunnel with their bike, mounts it in place on the platform, hops on, and in just five to six minutes with the Leo, I capture the rider in two positions in precise, high-resolution colour 3D,” says Vorteq metrology engineer Sam Quilter. “Then I need just another minute to capture their shoe, on all sides.”
This means he can be totally done with that rider in just 10 minutes, he continues. “I’ve got everything I need to design an anatomically accurate, fast-as-a-bullet Vorteq cycling skinsuit. No chance of a rescan needed – not once.”
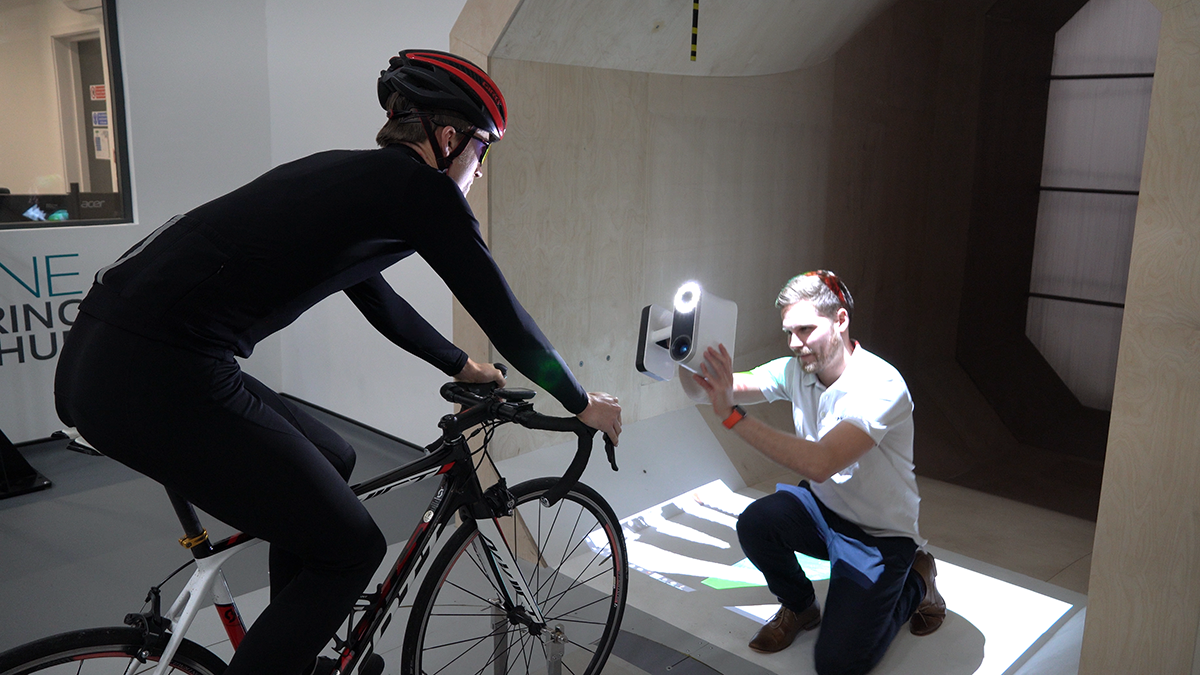
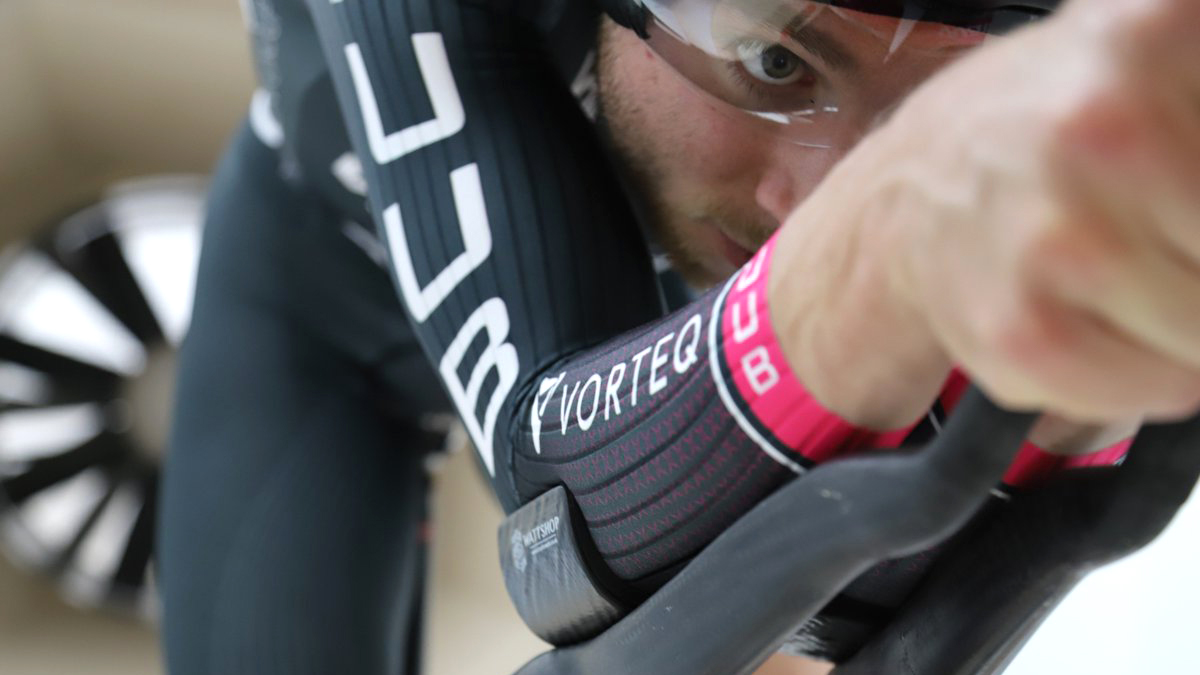
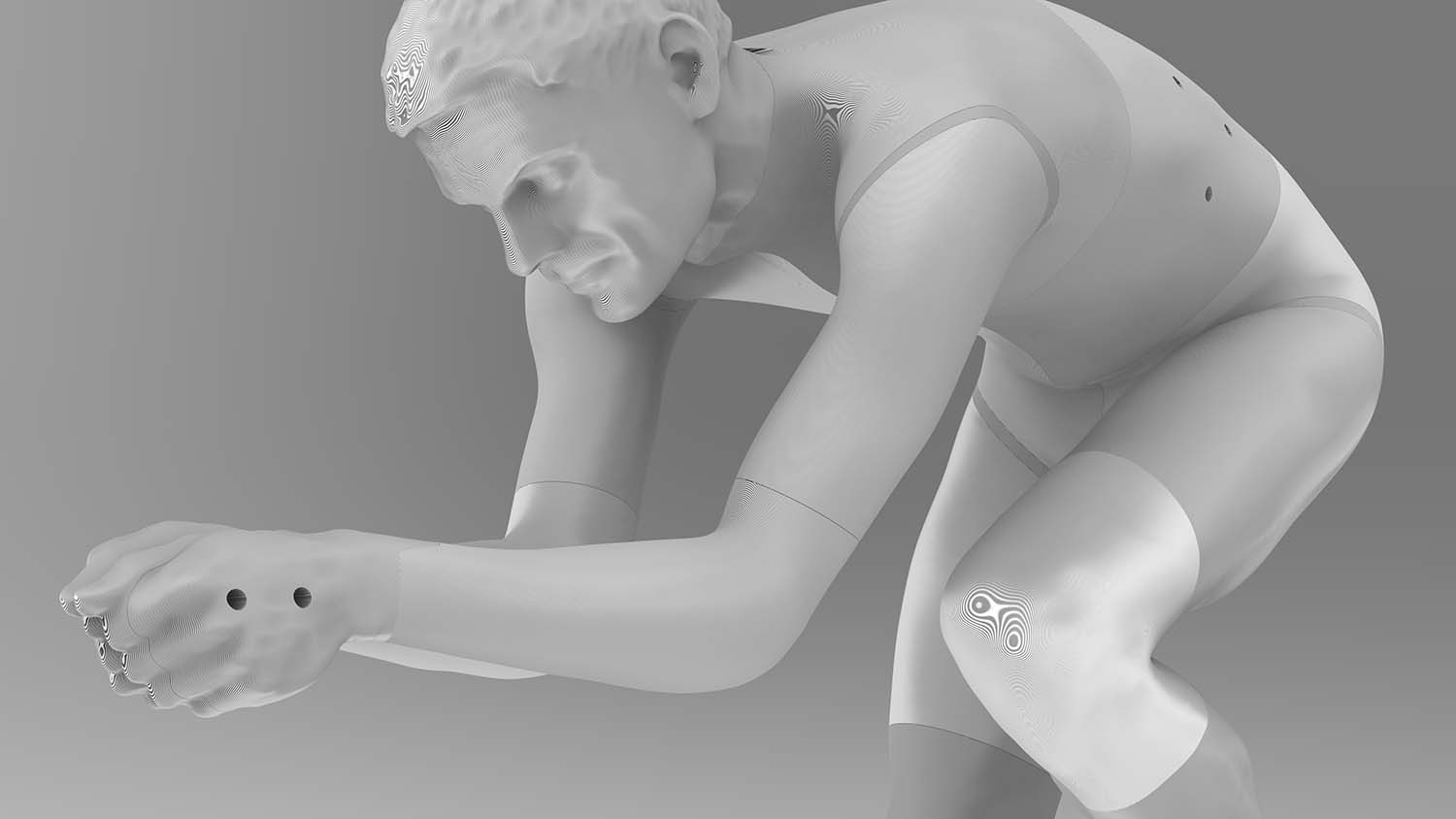
Cyclists are typically scanned in their underwear to capture as much detail of their anatomy as possible, meaning that the end product lays perfectly over the cyclist’s body – just like a second skin, in fact.
“When we’re making our skinsuits, we’re working directly from the Leo scans, so it’s not measurements we’re taking, it’s the exact physical data that’s being used, and the difference is crucial,” explains Quilter. “If you’re taking physical measurements and then entering them into a CAD system, or a computational draping system like ours, something is going to be lost in the transition. And that something can easily result in imprecise dimensions being used to create a skinsuit, which is entirely unacceptable to us.”
Even one tiny mismeasurement could result in a wrinkle here or there, he says, or fabric being overstretched in areas. Quilter then uses Artec Studio to post-process the 3D scans. Any 3D modelling work needed is carried out in Geomagic Wrap. Finally, the garment is exported as a 3D model that can be used to make the skinsuit.
“Not many steps are needed in Artec Studio at all. I basically read the Leo data in, double-check everything visually, then use the Eraser tool for a few clicks to remove any occasional, unwanted bits,” says Quilter.
“I normally keep the bike in the scan, since it’s a great reference point to get XYZ positioning as well as the angle, and then I go into Global Registration, where I just use the default settings, because they work brilliantly as is.”
Outlier Removal isn’t usually necessary, he adds, because the data is already clean enough. “Then I do a Smooth Fusion and, after a few other minor changes, I export it as an STL file for use in Geomagic Wrap.”
Geomagic Wrap’s Decimate tool is used to reduce the triangle count further. “If I’m getting rid of any wrinkles, which shouldn’t be in the scan, but on a very rare occasion might be, I use the Relax command, and then I move on to the Smooth commands, which let me cut out any imperfections, because sometimes athletes twitch their fingers during the scanning, and we need to fix that.”
This is exported as an OBJ file for use in Vorteq’s computational draping software. This final part of the process takes around two hours, and a ready-to-race skinsuit is typically produced in just under two days – but Quilter is looking to narrow that down to just 24 hours in the future.
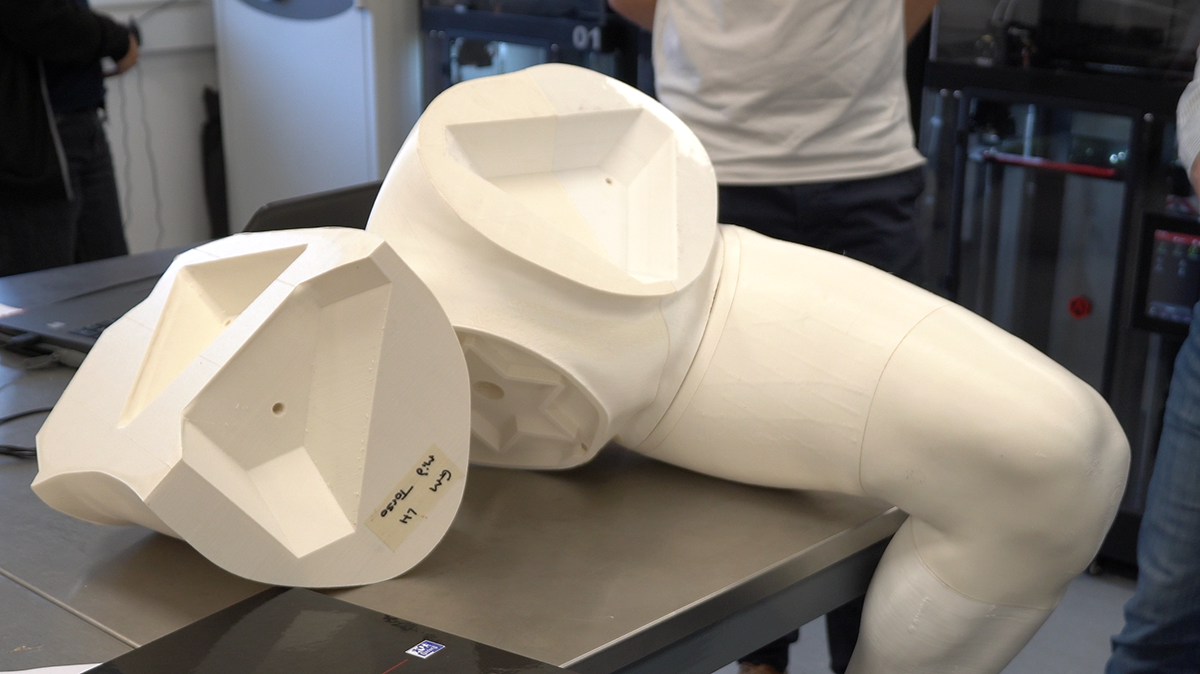
Dummy run
For regular customers, typically professional athletes, there’s now a way for them to order new skinsuits without having to visit the Vorteq offices.
Based on the 3D scan data, Vorteq produces a 3D-printed, anatomically precise mannequin of them. This means that if a cyclist is training on the other side of the world, but urgently needs a cycling skinsuit for an upcoming long-distance time trial, it can be produced in hours and express-delivered to them. What’s more, it will be entirely customised to the specific terrain they will be covering, whether that’s flat roads or long downhills.
“That’s where the marginal gains really add up,” says Quilter. “With a live rider in the wind tunnel, there’s going to be the wiggle factor to deal with, where the rider is moving around, even ever so slightly, and that’s going to affect results.”
With a mannequin, those problems disappear. The only factor that changes is the fabric, and this can be tested on the mannequin in the wind tunnel.
Says Quilter: “Mannequins don’t get tired, and they’re always perfectly still, which allows us to know exactly what kinds of changes our fabrics and designs are causing in terms of drag and performance.” At present, the Vorteq custom mannequin process takes just under two days, but that time is steadily decreasing with each passing week, he says.
And, thanks to the portability of the new Leo 3D scanner, Vorteq can really go where the action is, meeting athletes face-to-face at training camps and even during a Tour, something which potentially makes for a far more streamlined approach all round.