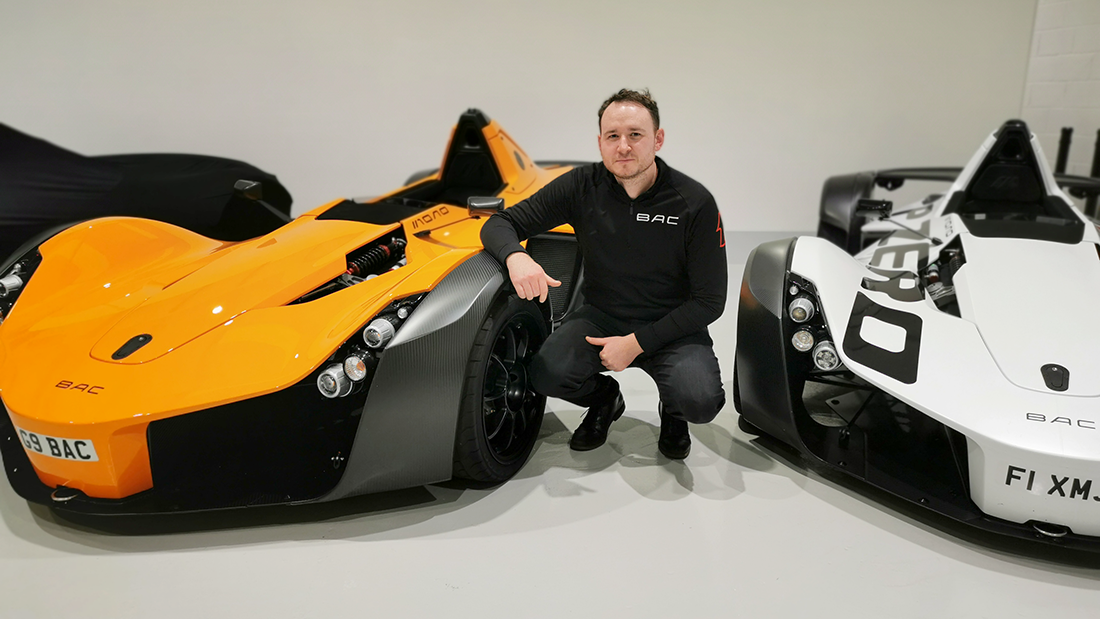
Great Britain has a long track record of producing lightweight, thrilling sports cars with a distinct motorsports edge. The BAC Mono R is the latest example to hit the asphalt.
An ultra-high-performance, single- seater, street-legal supercar, it’s a tribute
to its creators at Briggs Automotive Company (BAC) that the Mono R manages to combine everyday road manners with explosive track performance.
A 555kg kerb weight gives it a greater power-to-weight ratio than most hypercars, enabling it to sprint from 0-60mph in 2.5 seconds. Launched at the 2019 Goodwood Festival of Speed in July, the 30 models that BAC intended to produce were immediately snapped up by existing BAC Mono customers at £190,950 each, despite the car having no roof or windscreen.
This blazing success on the track and in business began life at a Stuttgart design agency back in 2007, where design director Ian Briggs and senior designers Guy Harvey and Murray Adams began with a clean sheet of paper to create the ultimate lightweight sports car.
The process for the original BAC Mono began with a benchmarking exercise to find out where their car would be positioned in the automotive market.
Its single-seat layout immediately gave it a unique selling point, but the goal was to find the sweet spot between enthusiast track-day cars, and being able to match the lap times of hypercars.
“Obviously there’s a big cost differential between what they were selling and your target lap time. We were able to find that pocket in the market,” says Murray Adams. “We were prepared to make the car cost more than [other track- day car manufacturers], but there was obviously this big gap between what the track-day car was worth, and what the supercar/hypercar was worth.”
Having found their starting position, the design for the Mono began with nearly eight months of sketching and concept work. “That’s just Bic Biro and pen sketching, just coming up with as many ideas as possible,” Adams explains, adding that initial forms were created around a Formula Ford race car chassis, but as time went on, the chassis took on its own bespoke design, too.
The distinctive styling took inspiration from outside the typical automotive influences. Adams explains that they wanted the Mono to be quite ‘superbike-esque’, with an enclosed front that gradually becomes more exposed to the rear, so you see more mechanical components as the eye travels along it.
“Inspiration for the car, in terms of just the design aesthetic, was very much both Ian [Briggs] and myself being inspired by a science fiction aesthetic,” says Adams.
“One of the key ones was a Björk video for the song All Is Full Of Love.”
“I think if you look at where mainstream cars have gone since then, Mono was certainly at the forefront of what they called ‘negative space’, which is kind of a fancy name for creating bodywork features that give you a much more open-looking form.”
The sketches were soon transferred from pen on paper into Autodesk Alias, with aesthetics and styling leading the car’s development. “I’d say we’re quite design-led. Primarily, it’ll start off in design and then we’ll see how we can achieve this; rather than it being the other way around: ‘This is what you’re working with, try and make it look good’,” Adams explains.
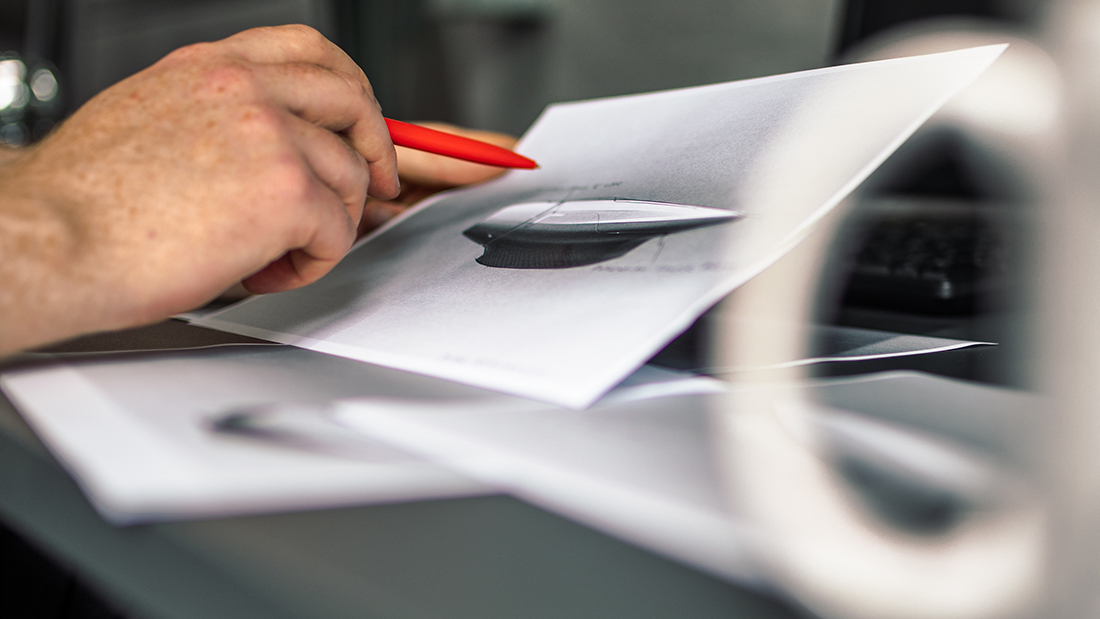
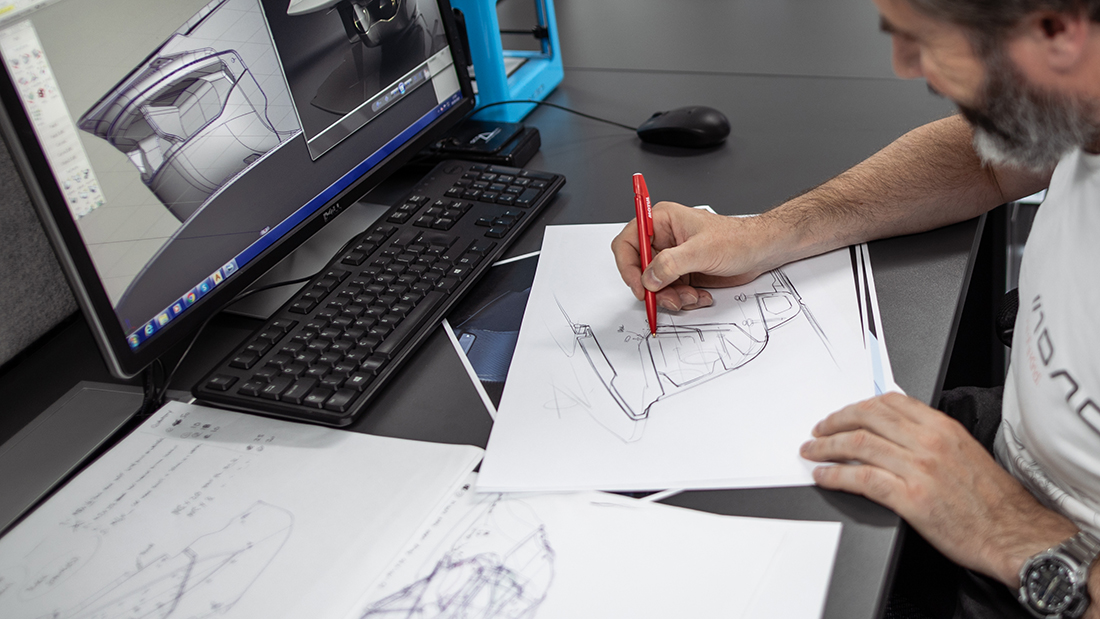
Quarter-Scale Model
Nearly a year into the project, the team built a quarter-scale clay model in the garage of the design consultancy.
It also worked a team from Stuttgart University, which operates one of the best wind-tunnel facilities in Germany and employs leading figures in the field, who were able to help benchmark the clay model and identify how the design could be advanced.
“We knew from the get-go it was going to be carbon fibre and we knew that we didn’t want to compromise too much on quality,” Adams explains, adding that the use of composite materials and over 200 machined billet aluminium parts meant that the starting point shifted slightly from the original benchmarking.
“The price of the car went up somewhat after the benchmarking, but we knew that we weren’t going to scrimp on using those kinds of materials, because that’s what the car demanded, and it’s exactly what the customer wanted,” he adds.
Work on the mechanical design began in Solidworks and quickly transitioned into Autodesk Inventor. Similarly, the BAC team moved from its German garage to a new facility in Speke, on the outskirts of Liverpool, UK, where it has continued to grow.
Having recently expanded, taking over a neighbouring building, the design and engineering set-up at BAC is a completely different animal now, in Adams’ own words.
The new location gives easy access to a number of facilities and suppliers in the North-West of England, with nearly 95% of the car’s components being manufactured or sourced from within the UK.
For example, Adams readily describes how all the machined billet parts come from up the road in Lancashire, and that the carbon fibre used in nearly two-thirds of the car is woven only a few minutes away in Runcorn, before being transported over to Derby, where it is layered up.
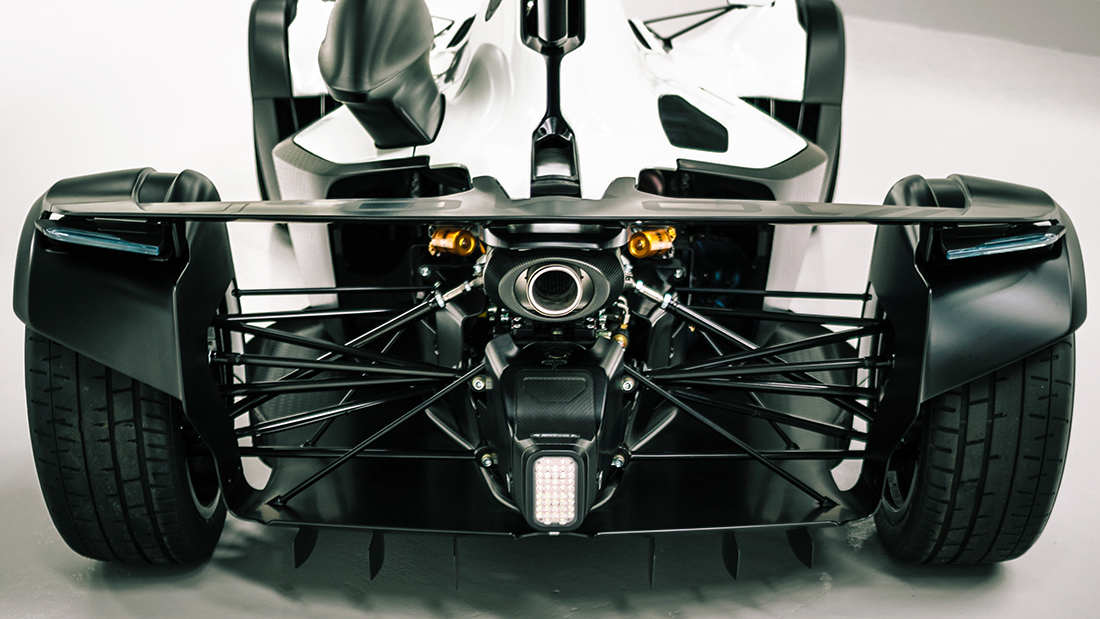
Local expertise also includes the Virtual Engineering Centre (VEC) near Daresbury, just 10 miles away.
The VEC developed an advanced, modularised workflow for assessing the bending and torsional stiffness of the Mono chassis, using the 3D CAD model taken from Inventor.
Different variants of the chassis were created and set up for structural analysis through single runs or design explorations, which took into account suggestions from Mono’s engineers, as well as material specifications from the chassis supplier.
FEA analysis was run on Dynamis from DTech, using the VEC’s remote virtual engineering testing service, which
in turn uses the powerful high-performance computing (HPC) facilities of the nearby Hartree Centre.
Given that the design of the Mono R has evolved from a physical car, as opposed to an original Mono’s development through a clay model, Adams explains that the simulation process is now as much about benchmarking the original car as it is looking at the next one.
“The thing about Mono is that, architecturally, it’s quite a unique car, so there were quite a lot of unknowns. But the good thing about Mono is it’s aerodynamically very stable, unlike some of your very high-downforce cars that are very extreme and need to be driven at 100% all the time.”
“Otherwise you get this an on/off type situation with engagement in terms of aero. So, from a driver’s point of view, it was very neutral in terms of the lift, downforce and the front and rear being rightly balanced. That was a conscious thing. That’s why it is so good to drive on the road and not just on the track!”
Agressive Posture
The Mono R looks incredible sat in the garage of BAC’s headquarters, with slightly more aggressive posture than its predecessor.
Also setting it apart visually is a new air intake, mounted at driver’s head height and shaped like a torpedo. This lends an eye-catching edge to the model, not dissimilar to a Jaguar D-Type’s classic asymmetrical fin.
The prototype for the airbox [see boxout at the end of the article], the full rear wing, rear arches and the spine of the bodywork have all been 3D printed, but while these will be swapped out for tooled carbon fibre in the end product, several additively manufactured parts will make it into the final car.
BAC worked with DSM to develop SLA 3D-printed grips for the Mono R’s steering wheel, which allow it to be fully customised to its driver, while more performance-based additions include new 3D-printed air inlets that are lighter, more durable and more cost-effective to produce than using traditional methods.
“There’s always a way of making something in the traditional sense, but obviously if you know that it’s going to be a 3D-printed part, then you know you haven’t got half the worries. It’s much more flexible to do exactly what you want,” says Adams.
It just becomes a cycle of losing weight. I think generative design is just the next step in that
The majority of the 3D printing work is carried out on BAC’s behalf by third-party bureaux. That has made sense, given the size of the parts, but there are now signs of it moving in-house, evidenced by a new Ultimaker S5 desktop 3D printer, which is currently sat in the back of the company’s garage.
“That’s our first soft introduction into doing in-house a bit!” laughs Adams. “We can use it for anything up to shoebox size. And that’s great for being able to road test some things, because we want to put 3D production parts on the car.”
He adds: “I mean, it makes sense for us, volume-wise: Mono R is going to be 30 cars, and so in terms of tooling costs, then it becomes beneficial for us and gives us the flexibility as well.”
This lends itself to Adams’ clear enthusiasm for what optimisation software can offer to BAC’s designs, noting that the team is about to start a new project to design an alloy wheel design using generative design.
Setting the boundaries between the organic structures and being able to manufacture them, along with not having something that dominates the aesthetic, is currently the balance that the team strives to achieve.
“This is much about setting the parameters that you want it to work from: we want it to look pretty broadly like this, what can you do to save weight? I think that the relationship between the designer and the generative will be really interesting,” says Adams.
As the senior designer explains, reducing weight is a huge focus: “As soon as you save weight on the brakes, then you know your suspension, perhaps, or your wheel hub, doesn’t have to be as big and you can save weight on there and save weight on the chassis. It just becomes a cycle of losing weight. I think generative design is just the next step in that.”
With its four-cylinder, naturally aspirated 2.5-litre engine, maximising the power-to-weight ratio is always going to be a key part of the Mono’s development.
Parts on the Mono R reflect this consideration, with some of the machined parts topology-optimised in Inventor’s Shape Generator tool in order to achieve lightweighting, yet still manufacturable using 3-axis machining.
“The further you go on, obviously there’s always ways in which you can make the form a bit more efficient in terms of packaging things; maybe one part can do two jobs and so on,” says Adams. “I think the cool thing about Mono is that the concept is really strong, so it’s just about how can you continue that development cycle.”
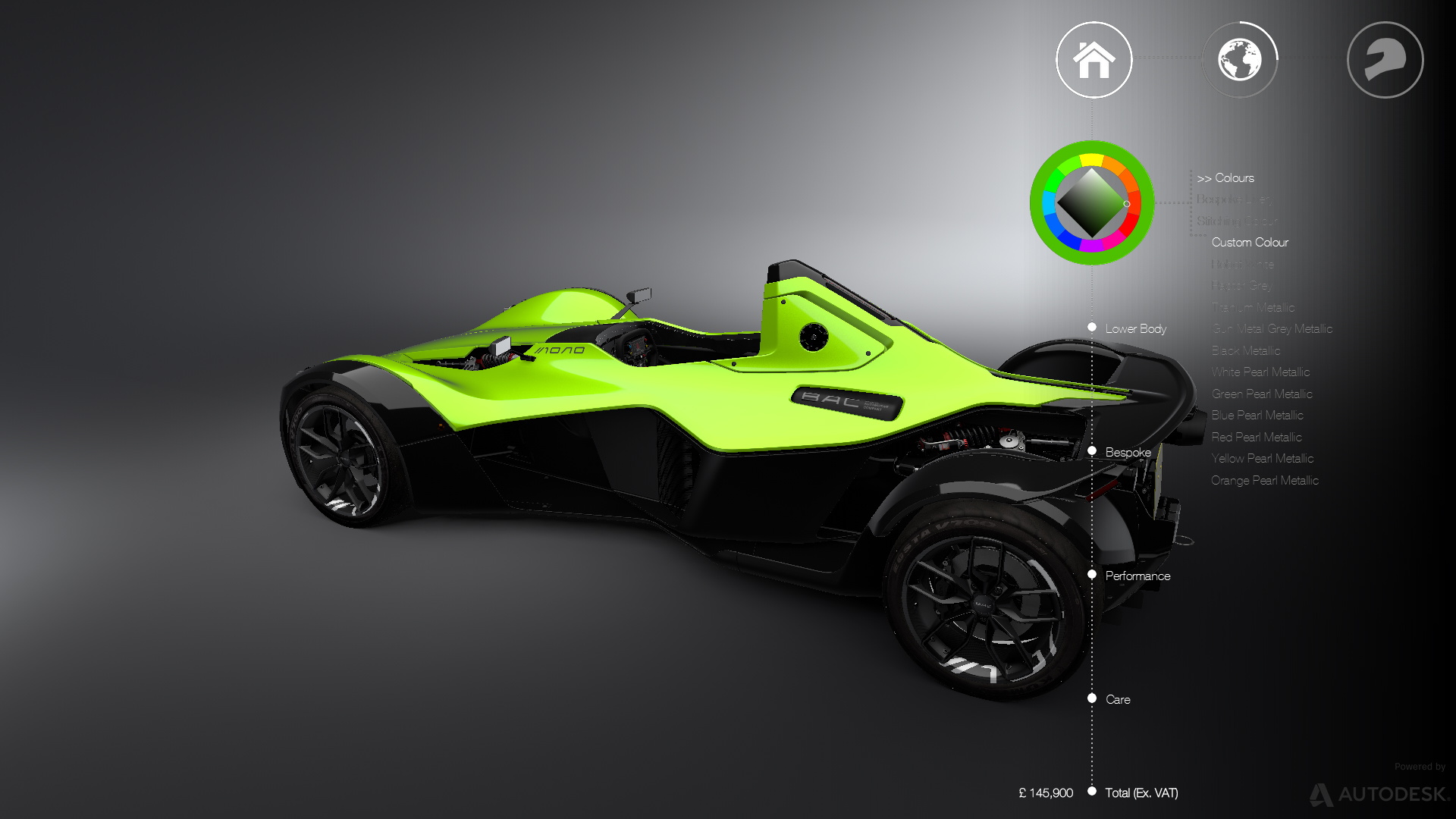
Implementing this as quickly as BAC’s design and engineering team does relies on each of its members being as nimble and agile as the cars they produce.
As Adams puts it: “We’ve not got thousands of engineers. We’ve not got hundreds of design staff. So you’ve got to use [size] to your advantage. If you can do something better, then it doesn’t have to go through this ridiculous process in order for it to happen. This is what we want, so how can we go about achieving it?”
Being part of a small team inevitably means that Adams For example, BAC recently needed to create marketing is frequently pulled in to solve other design challenges that the company encounters.
For example, these have included helping to design a show stand for Goodwood Festival of Speed, as well as bespoke liveries for individual customers’ cars.
Visualisation software Autodesk Vred is used regularly in these ad hoc projects, for tasks that vary from in-house design reviews and presentations, to helping customers configure their dream Mono.
An interesting development here is how the team pair Vred with Autodesk’s ReCap Pro 3D scanning software, which imports photographs and can then output a point cloud or mesh ready for CAD.
For example, BAC recently needed to create marketing material for a driver’s jacket designed by the team. “We used ReCap Pro to get someone in position, as if they were sat in the car’s carbon seat, then took all the photos and uploaded them. That model was then put into Vred and we created visuals based on that,” says Adams.
It’s a highly creative solution, but then nothing less would be expected from the team behind a brand that has emerged from the starting gate at a blistering pace, and which has shown itself more than ready to utilise the very latest technologies in order to continue evolving at terrific speed.
Boxing Clever
One of the design challenges for the BAC Mono R was the design and testing of its unique air intake pod.
Essential for the car’s cooling and on-road performance, the airbox has a complex and unique geometry, with the final part needing to be produced entirely in carbon fibre.
These demands meant that the production of a prototype using traditional methods presented a huge hurdle for the team.
Naturally, the aim was to avoid lead times and costs from spiralling, while ensuring there was no compromise on the performance and functionality of the prototype itself.
With temperatures expected to surpass 100°C, any prototype produced needed to be able to withstand intense conditions during test drives.
BAC turned local 3D printing expert Tri-Tech 3D and, with its know-how and Stratasys F900 production 3D printer, the company managed to produce a prototype that was as close as possible to the real part – meaning that, in testing, the Mono R could be pushed right to the limit.
The part was built from Stratasys’ Nylon 12CF material, a carbon-fibre reinforced thermoplastic, which is able to endure temperatures over 140°C.
“It withstood the tests on the track with ease,” explains BAC design director Ian Briggs. “We were able to tweak the design and not worry that the final 3D-printed version wouldn’t match the exact size or geometry we needed.”