It has no doors. No roof. No windscreen. No creature comforts like a heater, carpets, a stereo system or air conditioning. But what it does have in abundance is astounding performance. Zero to 60 mph in 2.7 seconds. Zero to 100 mph in 6.8 seconds.
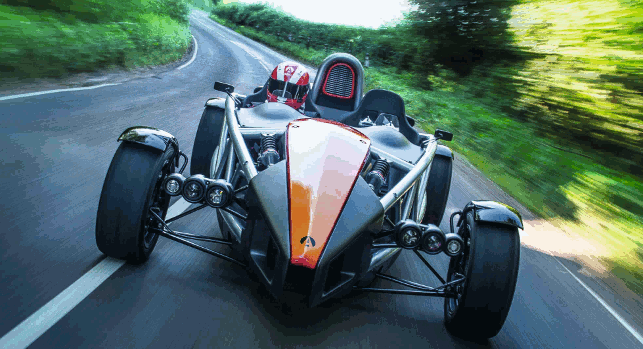
Top Gear describes the Atom 3.5 as “the most visceral espresso shot of pure acceleration this side of a superbike
It’s the unique and British designed and manufactured Ariel Atom 3.5. Powered by a 2 litre Honda i-VTEC engine, with the option of a 310 bhp supercharged version, the two-seater Atom is equally at home as a serious track racer and as the ultimate fun
sports car for the road.
But exhilarating performance both on and off the race track isn’t the only thing that stands out with the Ariel Atom. So too does the build quality.
The person at Ariel Motor Company with ultimate responsibility for ensuring this high level of build quality is the company’s managing director, Simon Saunders. And one of the technologies that he has at his disposal is a Solutionix Rexcan CS+ 3D scanning and inspection solution.
“As a small design and manufacturing company producing a technically advanced, low volume product, it’s a real bonus to have access to the sort of accurate 3D measurement capabilities that the Solutionix Rexcan CS+ provides,” says Saunders.
“This type of inspection and measurement system wasn’t readily available to small companies like us when we started making the Atom back in 2000,” he adds.
Complete solution
The Rexcan CS+ provides a complete, integrated hardware/software 3D scanning solution that can sit on a desk.
Using Solutionix’ Blue LED Technology to provide high resolution, high accuracy structured light scanning, rather than the laser technology found in most other scanners, the scanner in the Rexcan CS+ system features interchangeable dual lens sets to provide different degrees of resolution and accuracy – up to 0.035 mm point spacing (resolution) with better than 10-15 microns accuracy – depending on what is required.
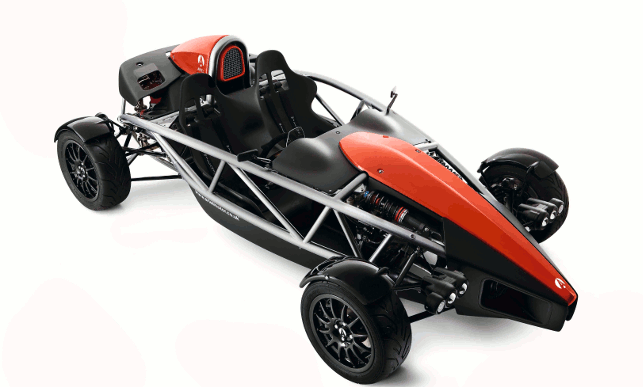
The supercharged 310bhp version costs around £38,000
It also comes with a dedicated, portable stand, a fully integrated and automated 2-axis tilt turntable to hold the object to be scanned and Solutionix’ ezScan software for scan data capture and processing.
The system used at Ariel Motor Company also includes automated 3D measurement and inspection software in the hardware/software bundle.
Ensuring accuracy
One of the first components to be inspected at Ariel using the Solutionix system was a fabricated sheet metal part, known as an upright. This forms part of the Atom’s front suspension system.
The upright was positioned on the turntable and the scanner was set to look down on it at 45 degrees. With Solutionix ezScan software controlling and coordinating the turntable’s motion and the scanner’s data capture processes, scans of the upper surface of the part were then taken automatically at increments of 10 degrees as the turntable rotated through 360 degrees.
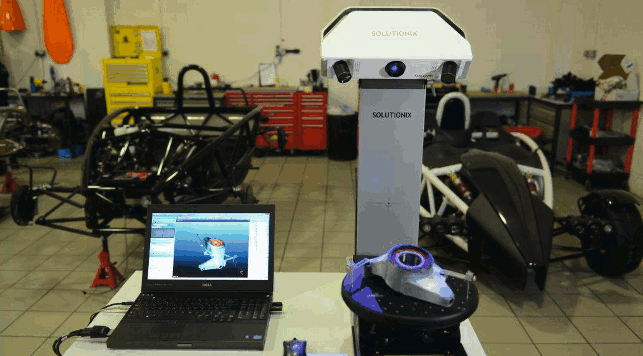
Solutionix Rexcan CS+ provides a 3D scanning desktop solution
The part was then turned over and the process was repeated in order to capture the opposite surface.
The raw scan data was converted, on the fly as it was captured, to a polygon mesh using Solutionix’ ezScan software, which also merged the individual mesh models together to create one complete polygon mesh model of the part.
In order to speed up subsequent processing of the data, curvature-based sampling of the mesh model was performed with the ezScan software to reduce the polygon count in areas of low curvature while retaining it in high curvature areas. This reduced the overall polygon count without losing any of the fine detail.
The whole scan to final mesh model process was completed in less than half an hour and the model was then ready to be taken forward into the automated inspection process.
Fast inspection
During the inspection process, the 3D scan data model is automatically analysed against the CAD model to identify and measure any deviations between the physical part and its counterpart CAD model.
The entire inspection process takes just a few hours. Additionally, inspection reports can be saved or output as PDFs automatically and if design changes, or analysis such as CFD and/or FEA, or design optimisation is required, the scan data can also easily be used to reverse engineer the as-produced part.
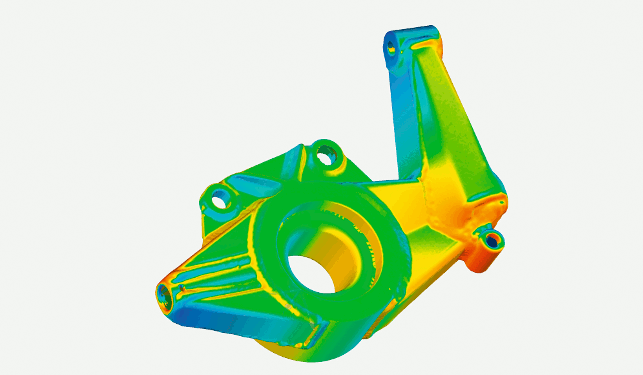
The output from the inspection process, with call-outs
“The accuracy and speed with which parts can be inspected with the Solutionix system, plus the fact that it’s portable so we can take it to where the job needs to be done rather than needing a dedicated inspection area, is of great benefit to a small manufacturing company like Ariel,” says Saunders.
“Not only does it give us the capabilities that until recently have only really been available to large corporations, but it helps us to attain and maintain the high build quality we strive for in a car that’s a world beater – not just in pure performance but in affordable driving fun that’s built to last”.
Using Solutionix in development of the Ariel Atom 3.5 sports car
Default