The first 3D-printed airless prototype basketball is the result of the union between Wilson’s centenary experience in sporting goods, EOS’s innovative AM solutions, General Lattice’s advanced computational design tools, and DyeMansion’s cutting-edge post-processing technologies
For sports that require little to no equipment, every little detail is crucial. While for sports like skiing, ice hockey, lacrosse or golf, the overall quality of a player’s gear is determined by a combination of many elements, for basketball it all comes down to the quality of the ball and Wilson Sporting Goods Co. knows that no aspect of its design can be overlooked.
This is why the Chicago-based sporting goods company has recently partnered with General Lattice, EOS, and DyeMansion to elevate the game, unveiling the industry’s first 3D-printed airless prototype basketball, achieved through Additive Manufacturing.
Wilson says that Additive Manufacturing provided its team with unparalleled design freedom compared to traditional manufacturing methods, and is transforming the sports industry through digital innovation.
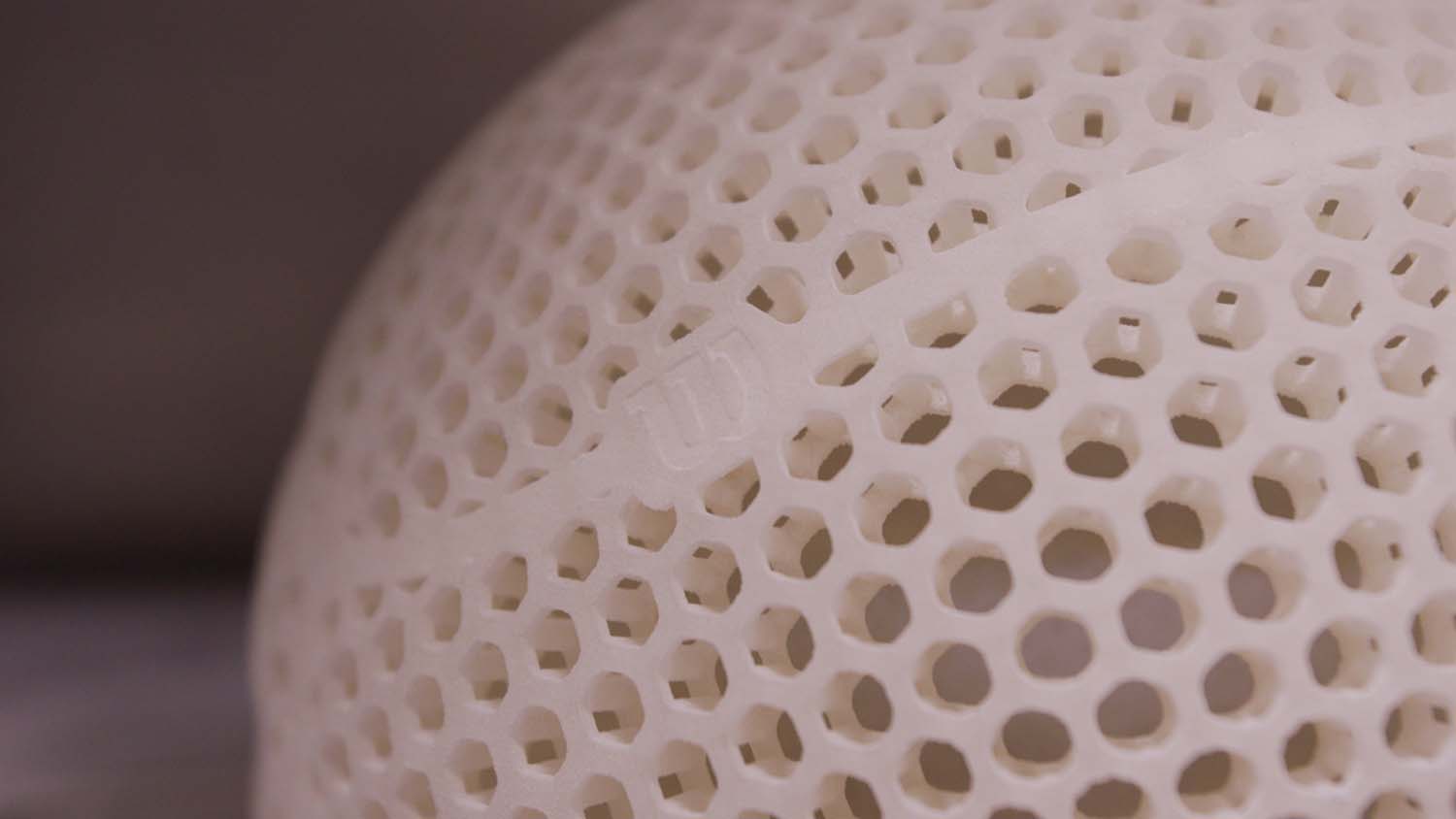
The three companies worked closely together, with General Lattice providing computational design services, EOS providing the 3D printing at its technical centre, and DyeMansion providing post-processing with their surfacing and colouring solutions.
GL Labs, General Lattice’s enterprise solutions team, worked with Wilson to bring to life their concept by streamlining the design and iteration process through the use of its computational design tools and workflows.
“The flexibility GL Labs and its tools enable customers to integrate data throughout the design process to reach optimal solutions faster,” says General Lattice CEO Nick Florek.
Once the design was finalised, EOS 3D printed the Airless Prototype using its EOS P 396. “What Wilson is doing with its airless prototype is such a great technology showcase, demonstrating yet again how to achieve entirely new ideas with mature applications,” says David Krzeminski, senior consultant with Additive Minds at EOS.
“We regularly see AM innovation in the business-to-business space, but lately, innovative organizations, like Wilson, are getting creative and exploring how to leverage AM for prototyping and production, and mass customisation products that give consumers exactly what they want in the products they purchase,” he goes on.
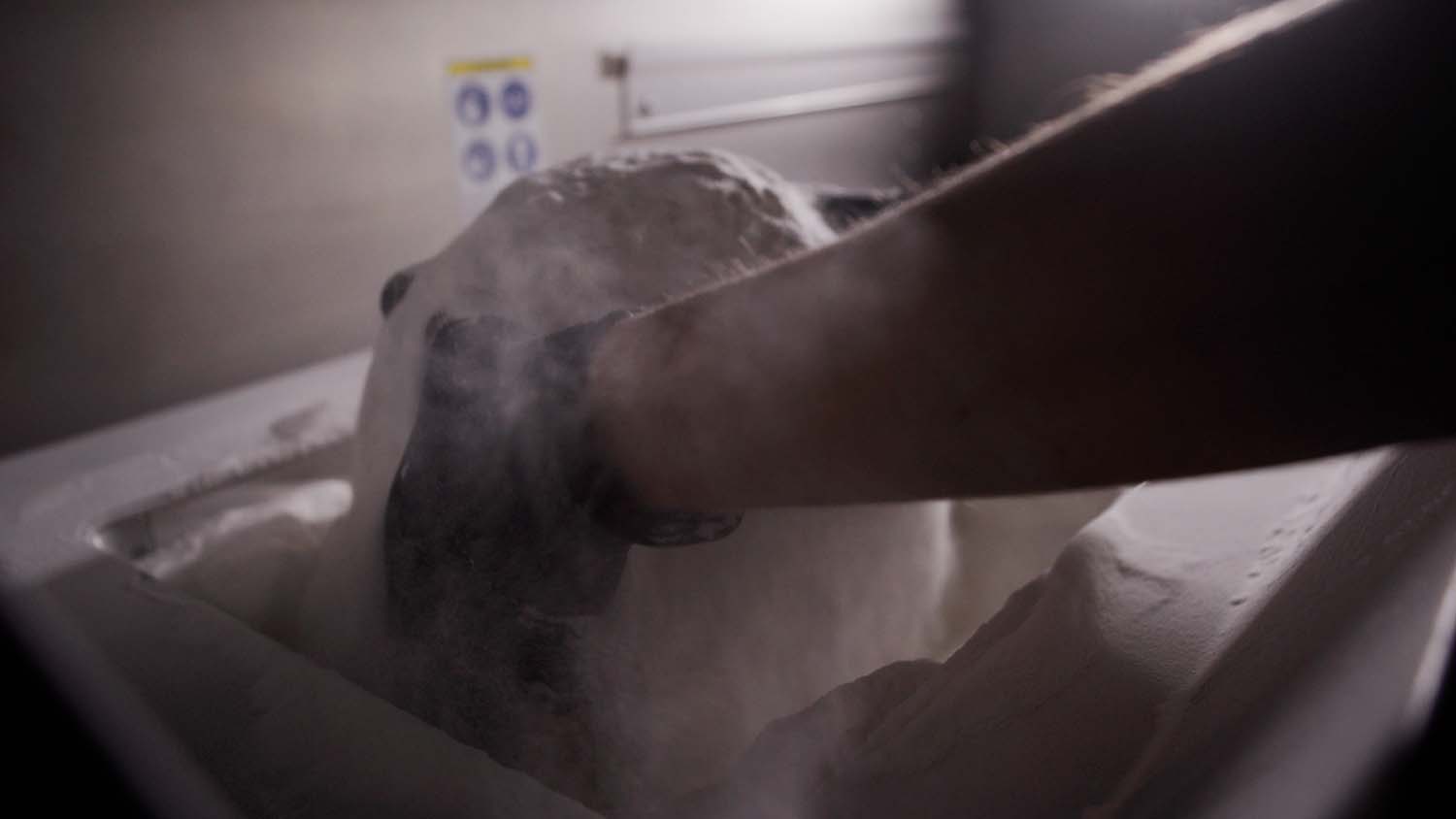
DyeMansion added the finishing touches to create a smoothed finished surface and colourful outer skin by employing their VapourFuse Surfacing and DeepDye colouring technology.
“With basketball being a ‘low equipment’ sport, changing the most critical element, the basketball, is no small venture,” said Lester Hitch, application consultant at DyeMansion North America.
“It was the focus of our team in North America to fine-tune the vapour smoothing treatment creating a consistent finish that matched Wilson team’s expectations based on experience making basketballs.”
The three companies unanimously agree in saying that the first 3D printed airless basketball does not only show how employing additive manufacturing and computational design can help produce lighter, stronger and more durable equipment, while also allowing greater design freedom, it is also an example of how collaborations between industry specialists can lead to significant design innovations.