Oxsight is creating eyewear that uses mixed reality to help those with visual impairment. We spoke to design agency Oxford Product Design on how it helped develop the technology into a daily wearable device.
It’s estimated that over a billion people across the globe experience some form of visual impairment that is significant enough to affect their daily lives.
Low vision can have an enormous impact on an individual’s ability to perform a variety of everyday tasks from driving and shopping to travel, resulting in reduced independence and quality of life.
In 2010, researchers at the University of Oxford began work to gain a deeper understanding of how the brain manages visual information, and to explore ways that this capability could be amplified in the low vision community.
The team’s work gained international recognition, and in 2016 it founded Oxsight with the goal of developing this technology into aids that would help visually impaired people to live more independent lives.
One of its products is a pair of ‘smart glasses’ named Prism, which expand the user’s field of vision by up to 68 degrees.
Oxsight Prism captures live video of the real world via a small HD camera on the front of the headset, which relays to two HD displays that are then projected in front of the user’s usable area of vision.
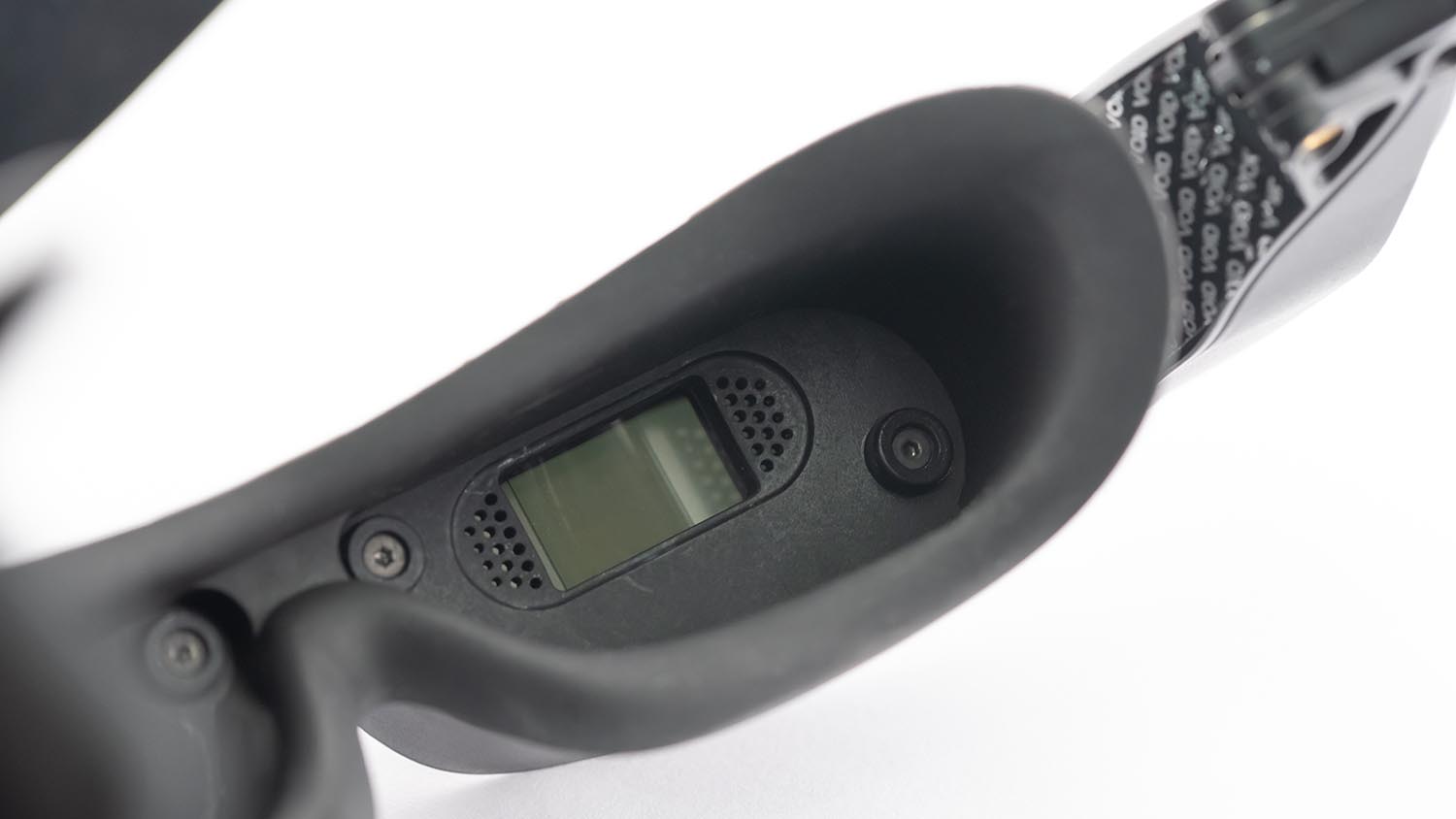
Through the use of Mixed Reality, Prism can display in a variety of modes to help the user in various scenarios – for example to enable them to pick out specific details such as faces, to make writing more legible, or to highlight approaching objects and obstacles.
Oxsight challenged design consultancy Oxford Product Design to incorporate their technology into a wearable that would be both stylish and comfortable enough for the user to wear for extended periods.
Oxford Product Design boasts some extensive expertise in applied ergonomics and human factors engineering – and with weight, size, position and fit key to the design of any wearable device, it made them expertly positioned for the task.
Initial concept work involved exploration into attachment methods to the head as well as product construction and assembly methods.
Sketches were created digitally in Autodesk Sketchbook and Adobe Illustrator to run through proposals to enable the right fit, where the bridge narrows back to meet the wearer’s ears.
Aesthetics were also critical, particularly with devices to be worn on the head; with research showing users were quickly put off by a product that makes them ‘feel like a cyborg’.
The design quickly moved into Solidworks, where once a 3D CAD model had been built, initial prototypes could be produced, and pain points could begin to be identified.
Initial testing proved that while a lightweight headset was important to users, the quality of the received image was even more so, making one of the most integral parts of the device the occluder surrounding the users’ eyes.
This element ensures that no light or distraction entered the Prism headset from the outside world, in order to enhance contrast and quality of the received image.
Because of its placement, the occluder would also support the weight of the headset against the user’s nose.
Creating components that fit tightly to the face requires a great deal of input data and testing to validate: Human heads have some of the largest variation in contour and shape of any part of the body – from fullness of cheeks, to length and width of nose, to the depth of eye sockets.
While Prism was created for the European market in the first instance, the design needed to be easily adaptable for other global markets in the future.
With this in mind, the team at Oxford Product Design employed anthropometric data that captured a range of multiethnic head sizes across genders from fifth to the ninety-fifth percentile adults.
As a result, the occluder’s seal is able to fit a large proportion of the target market and its design is such that it can be easily and cost effectively adapted to suit specific markets.
The Oxford Product Design team applied knowledge from previous work with respiratory face masks, opting to build the occluder from a soft touch biocompatible rubber designed for low force but high interference against the face upon contact, making it cooler and more comfortable to wear over long periods.
The seal was designed to roll and flare away from the face upon contact, resulting in a consistent contact path thickness around the face which evens out pressure and reduces the overall contact area.
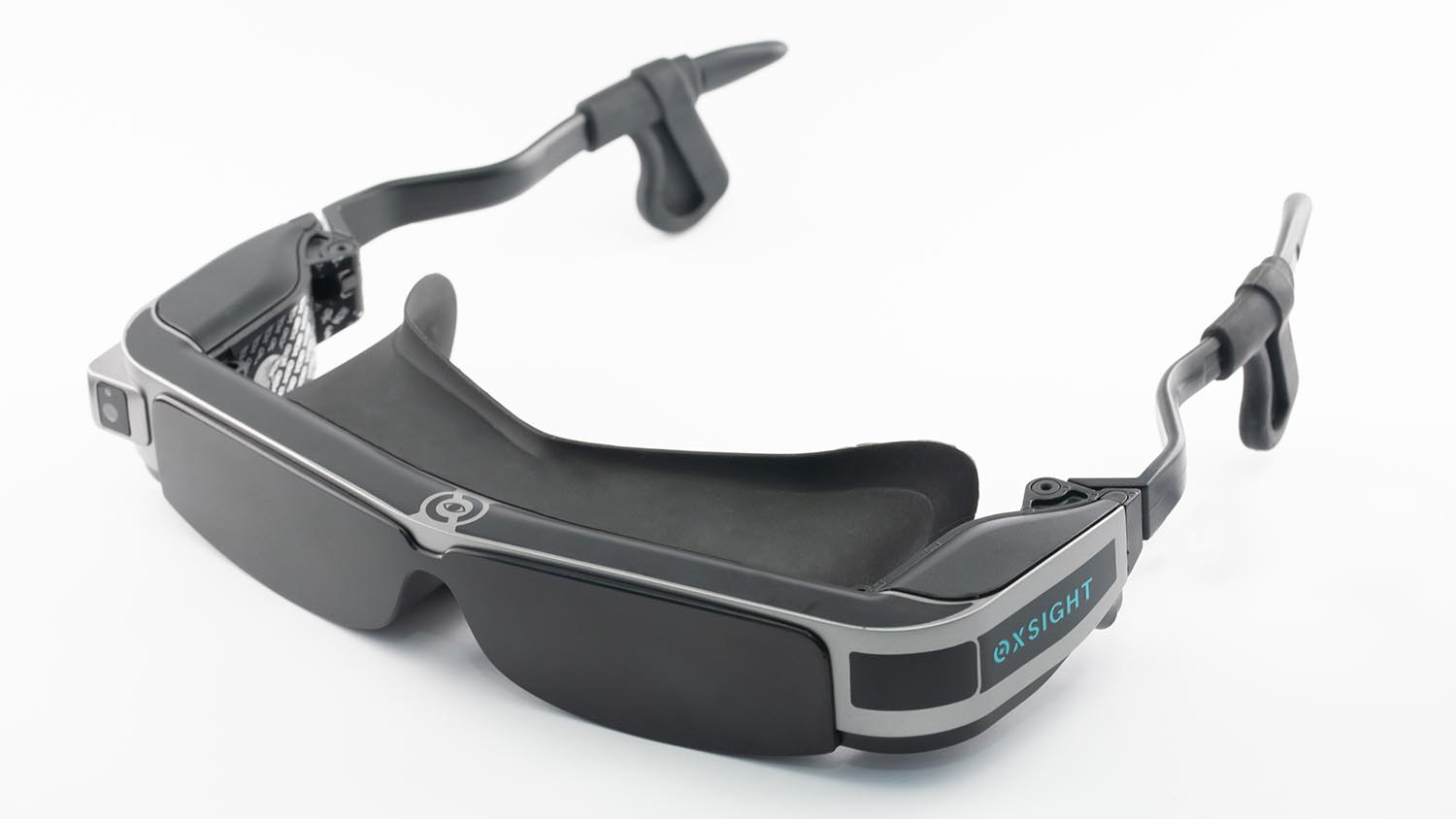
Multiple prototypes of the occluder were created to ensure that the seal would roll evenly and dynamically across a range of face types. A variety of production techniques were employed, from Stratasys Polyjet 3D printing for rapid design iteration, to vacuum-casting the stable design in polyurethane when a more realistic elastomer was required.
Prototypes were tested on a wide range of real-world users during user trial phases, and feedback was incorporated back into the design by the team to ensure that size and shape of the contact area were optimised for the comfort.
The product’s original arm design didn’t account for the level of force that the occluder was applying, and through initial user testing it became clear that the force pressing the device to the user’s face was in some cases pushing the headset up and away from the user’s head.
Many VR/AR headsets solve this issue with a ratchet wheel that holds the device on to the head securely, although this can make the headset cumbersome to put on and skew the aesthetics to look like a piece of sports or tech equipment rather than eyewear.
The team investigated and tested a variety of solutions to secure the headset to the user’s head, with the low compression force of the Occluder helping in this regard to keep stability with a lighter weight solution.
In the final stages, the design was readied for manufacture and even certification through the Solidworks CAD model.
Oxford Product Design used the model to create split lines, material marks, injection gate specifications, and 2D drawings, as well as creating assembly instructions, with the model used helping to lease with the manufacturers.
The final design for Oxsight featured hooks that rest behind the ear, maintaining the familiar glasses design and reducing the visual weight of the product, while a thin membrane was also added to mould to the shape of the wearer’s ear, adding comfort.
By integrating human factors engineering throughout the design process, Oxford Product Design was able to design a truly adaptable product, which pays more than a passing glance at future markets for the product.