In light of the global focus on COP 26 and HP’s own Sustainable Impact Report, Guayente Sanmartin, global head & general manager, HP Multi Jet Fusion, HP Inc. gives her views on 3D Printing and its role in creating an era of sustainability in manufacturing
This this past year, we have seen consumers, brands and governments alike demand changes that will lead us into a future designed to have as little impact on the environment as possible.
The severity of the environmental situation in which we find ourselves has heightened so much, that today, any business or nation wishing to remain competitive and favourable in the consumer’s eyes must prioritise the health of our planet. This was even emphasised by Her Majesty, Queen Elizabeth II, who expressed her irritation with those nations choosing not to attend COP26 – the annual climate change conference hosted by the UN.
In this context, sustainability must underpin everything we do. Following the launch of this year’s HP Sustainable Impact report, I am proud to work for a company that puts sustainability at the forefront of its business operations. However, there is always more that can be done, and to enable true resiliency, companies must look beyond their initial operations and consider the entire ecosystem.
I believe that the world can be transformed by a refreshed approach to design and manufacturing, in addition to leveraging new and innovative technologies if we are to realise a net zero, fully regenerative economy.
When HP surveyed global digital manufacturing and 3D printing decision makers in late-2020, an overwhelming majority (89%) said they were changing their business models, and at least 9 out of 10 were investigating new and more sustainable supply chain models. This shift could be a conduit to widespread sustainable innovation, but only where companies are willing to redefine manufacturing for the world we live in today.
With 3D printing, developing, iterating, and manufacturing goods can be done by any company, small or large, efficiently and sustainably. Those qualities will increasingly win out in the marketplace. For example, French retailer Decathlon is reaping the benefits of HP’s 3D printing technology at ADDLAB, the company’s additive manufacturing laboratory.
The facility produces spare parts for Decathlon’s products, as well as other services including prototyping, design validation and the manufacturing of small tools.
Since installing two HP Multi Jet Fusion printers at the ADDLAB in 2016, Decathlon can produce functional parts with complex details at scale, increase efficiency, streamline workflow processes and target new applications. Yet, above all, the company has lowered its carbon footprint, thanks to the unmatched reusability of HP 3D materials.
Promoting More Resilient Production
As manufacturers sought greater supply diversification and more localized, on-demand production in the wake of the COVID-19 pandemic, 3D printing offered a solution. Look no further than the countless digital manufacturing sites that morphed into hubs for PPE production last spring. 3D printing allowed disrupted supply chains to be simplified and strengthened at the same time.
In fact, according to HP’s Additive Manufacturing Trends in EMEA report, 79% of respondents said that additive manufacturing helped them deal with production challenges related to COVID-19.
More than a year later, we must stop thinking of those shifts as quick fixes and instead focus on what they offer long-term. Expedited iteration, faster speed to market, less resource-intensive production, a smaller transportation footprint and the extension of product life with replacement parts on demand—these characteristics will not only define the future of manufacturing but will also chart a more sustainable course for generations to come.
3D printing enables both short- and long-term solutions capable of near-instant responses to market changes. In an increasingly globalised world, this is an unparalleled competitive advantage for companies, but also for customers.Again, according to HP’s report European industrial parts manufacturers agree on the urgent need for increased digitalisation, with 63% expecting to spend more than €100,000 on the digitalisation of their manufacturing workflows over the next 12-months.
Meeting Consumer Demand for Sustainability and Personalisation
As demand for sustainable products has multiplied, so has the pressure on businesses to break from the one-size-fits-all mould. According to Deloitte, more than a third of consumers have expressed interest in purchasing personalised products. Among them, one fifth are willing to pay a 20% premium for those goods.
Fortunately, conscientious and customisable goods can be one and the same. But first, current supply chain models that were not built for shorter runs or minimised inventory and warehousing needs must evolve.
This is where companies must embrace transformation in how they work and in how they think. The supply chain solutions that worked decades ago won’t work in a world where 3D printing has made the customisation of parts not only possible but also accessible. The automotive industry is a great example. GM, BMW, Volkswagen, Jaguar Land Rover and more have taken strides to put digital manufacturing to work in cutting-edge ways. They’ve simultaneously enabled less material waste and energy consumption while realizing more design options, all of which are critical to a more sustainable future.
For example, vehicle manufacturer Ford has been continuing to drive the future of automotive 3D printing by teaming up with HP to innovatively reuse spent 3D printed powders and parts, closing the loop and turning them into injection moulded vehicle parts – an industry first. The resulting parts are better for the environment and are produced without compromise in the durability and quality that Ford and its customers’ demand. Meanwhile, Nissan is using the technology for part repairs, giving new life to older car models.
These capabilities aren’t simply galvanising industries. They are actively changing the world—for the better.
Ensuring Lasting Change and Innovation
Of course, it is not just the realities of a vulnerable global economy or changing consumer demands driving the need for a new way forward. Our planet is in peril. According to research by IBM, 57% of consumers globally are willing to change their purchasing habits to help reduce negative environmental impact. Businesses must recognise this, and leverage consumers using their purchasing power to demand a more sustainable future by implementing processes and technology to transform their business model and operations proactively and sustainably.
3D printing and its intrinsically flexible nature empowers a more circular economy. And it could not be advancing at a better moment in time. Take, for instance, the ease of extending product lifecycles with on-demand replacement part libraries that 3D printing supports, or the inventive use of more environmentally friendly and recycled materials that new moulded fibre technology offers in place of single-use plastics.
People are ready to create big wins after a profoundly challenging time. We are on the cusp of an innovation boom, and companies require tools that will allow complex paradigm shifts to take shape.
While many leaders are driven by the economic growth 3D printing enables, the efficiencies and long-term resiliency it establishes have created a new era for sustainable manufacturing, which is second to none in today’s climate.
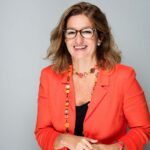
.