From polymers for packaging to coatings for metals, here’s the DEVELOP3D round-up of nine materials that use innovative, eco-friendly thinking to get around some of product design’s most tricky challenges
Ecor by Noble
Eco particleboard
We all know that recycling is the first step towards a greener future, but what happens to our waste after we dispose of it?
Produced by San Diego-based Noble Environmental Technologies, Ecor is a recycled-content particleboard created from raw materials that might otherwise enter traditional waste disposal systems.
The raw materials are sorted, preprocessed and then processed using a mechanical pulping approach and a controlled chemical reaction that uses lignin as a natural binder.
The US-based company aims to provide a green alternative to materials such as medium-density fiberboard and chipboard by using as feedstock scrap paper, textiles and aseptic packaging.
Sustainable coatings can be applied for water and fire resistance. A new step in the process increases the stability of the panels, making them suitable for outdoor applications.
www.ecorglobal.com
Fibraese/Papira
Wood-foam packaging options
The wood foams Fibraese and Papira are cushioning materials that aim to enable brands to create greener packaging for fragile goods.
Fibraese is made from Nordic wood and features damping and insulation capacity while also being recyclable in existing paper/board streams.
Designed to replace polymer foams in packaging solutions, it is soft yet resilient, exhibiting memory foam-like behaviour. It suits different types of conversion methods, such as sawing, die-cutting, waterjet cutting and laminating.
Papira is also recyclable in regular paper and board flows, but it uses pulp fibres as feedstock and has shock-absorbent capabilities, making it ideal for protective packaging applications.
Producer Stora Enso claims that the wood-based raw materials are sourced from sustainably managed forests, and that the manufacturing process of foaming the material involves only air and water – no solvents, blowing agents or hazardous chemicals.
The environmental impact and carbon footprint of these materials have been tested in Stora Enso’s in-house ISTA-certified laboratory.
www.storaenso.com
Nas Eco & Luran Eco by Ineos Styrolution
Clear plastics
Produced by Ineos Styrolution, Nas Eco and Luran Eco are tough and shapeless copolymers, obtained from renewable feedstock including kitchen and wood waste. Their production does not divert resources that might otherwise be utilised in food production.
Ineos Styrolution claims that, depending on the amount of feedstock used to produce the material, the carbon footprint reduction for these products varies from 77% to 99%, when compared to respective fossilbased equivalents. These materials boast transparency, minimal haziness and resistance to both heat and chemicals.
Luran Eco is a styrene acrylonitrile copolymer (SAN) mainly used in household and cosmetics packaging applications. Nas Eco is a styrene methyl methacrylate (SMMA) copolymer that is stiff, amorphous and features high transparency, making it suitable for water tanks, displays, food containers or boxes.
Both materials have received the sustainability certification ISCC PLUS.
www.ultrapolymers.com
Amorim Cork Composites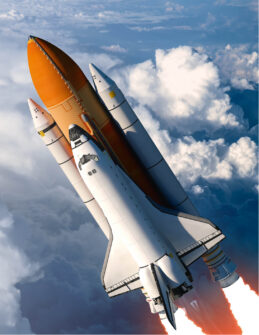
Aerospace-grade cork
It’s no secret that cork is one of the most sustainable materials in nature. Cork oak forests support a unique and fragile ecology, providing a habitat for rare and endangered species. They protect against erosion and desertification, act as a barrier against fire, regulate the hydrological cycle and also absorb carbon dioxide.
Amorim Cork Composite produces materials made from cork combined with surplus products from other industries. These materials are used in applications ranging from construction to mobility, and from footwear to furniture.
Thanks to their capacity to absorb a large amount of heat, products from Amorim Cork Composite are even employed in the aerospace industry.
Amorim Cork Composite states that lifecycle assessments show its materials and processes to have a negative carbon balance, when taking into consideration the carbon sequestration abilities of a cork oak forest and the emissions associated with the industrial process.
www.amorimcorkcomposites.com
AlgalFoam by Checkerspot
Marine foam
Checkerspot first demonstrated the potential of its sustainable materials as alternatives to conventional petroleumbased ones by collaborating with winter sports equipment specialist WNDR Alpine to produce ski layups.
Using AlgalTech technology, WNDR Alpine created skis that are both ecofriendly and high performing.
San Francisco Bay-based Checkerspot is now exploring other uses for its algae-based materials. One such material is AlgalFoam, a rigid, high-density polyurethane foam made from algae. It features a closed-cell structure and can be used to manufacture products that contain up to 41% USDA Certified Biobased content.
www.checkerspot.com
NAFILean X Forvia Faurecia
For lighter car parts
Faurecia is focusing on developing sustainable solutions for vehicle interiors with the goal of reducing the CO2 footprint of materials by 87% by 2030. This includes incorporating recyclable and recycled materials and creating alternatives to petrol solutions with no impact on cost.
To achieve this goal, Faurecia has selected NAFILean, a 20% hemp fibre-reinforced polypropylene compound specifically designed for automotive structural parts. In addition to being a renewable and green material, the company chose hemp because it met required performance and safety standards while enabling a weight reduction of 5kg per vehicle, resulting in lower fuel consumption.
Faurecia claims that the NAFILean products are, on average, 25% lighter than their conventional counterparts and save around 28% in CO2 emissions.
Moreover, the benefits of using hemp extend beyond the automotive industry, as this plant requires no pesticides, fungicides or irrigation, and creates healthier soil for future crops.
Faurecia’s materials have been used in 17 vehicle models to date, including the Renault Clio, Alfa Romeo Giulia, Peugeot 508 and Land Rover Velar. That’s some 13 million cars in total.
www.faurecia.com
Henkel Palumbina
Aluminium for automotive
Awarded by the Suppliers Partnership for the Environment, Henkel’s innovative thin-film metal pre-treatment process reduces the manufacturing steps involved in a conventional metal pretreatment process from seven steps to four.
Environmental benefits include the elimination of heavy metal phosphates like zinc, nickel and manganese phosphates; the reduction of sludge generation by up to 90%; and a significant decrease in water usage.
One major change is the use of a metal oxide conversion coating in place of a zinc phosphate-based coating. This new process decreases the amount of sludge generated by reducing the need for metal etching and fluoride additives. As a result, tank cleanings are required less regularly and annual chemical cleanings are eliminated. This reduces both sludge removal and labour costs.
The Pallumina thin-film process can process up to 100% aluminium and is effective across all major metals. The process is recognised for its significant environmental and economic impact, as it allows for the use of aluminium in the automotive industry. www.henkel.com
Econiq by Nucor
Net-zero steel
Steel company Nucor claims that Econiq is the world’s first net-zero steel. It is obtained by using electricity from 100% renewable sources, which eliminates Scope 2 emissions, and then purchasing carbon offsets to eliminate Scope 1 emissions.
According to Nucor, the emissions from its EAF steel mill are less than 25% of the global average. The company has committed to an additional 35% reduction in steel mill Scope 1 and Scope 2 GHG intensity by 2030, using 2015 baseline goals.
Nucor uses recycled scrap-based electric arc furnace technology and is a significant purchaser of renewable energy. It has a virtual agreement in place to receive wind and solar power.
Several automakers, including General Motors and Mercedes-Benz, have announced that they will incorporate Econiq into their workflows. Nucor has also stated that Econiq could be used in the construction, renewable energy and infrastructure sectors. www.nucor.com
Nemalloy by Nemak
Lightweight alloy
Novel automotive aluminium alloy Nemalloy from Nemak has won the Altair Enlighten Award 2022 in the Future of Lightweighting category. This alloy offers several environmental benefits. Its composition eliminates the need for strengthening via heat costs, for example, and it can be easily cast into large thinwalled components. It can also be fully recycled.
Nemak’s melting centre focuses on producing aluminium-silicon alloys specifically used in the automotive industry.
The company recycles approximately 2.5 billion aluminium cans every year, resulting in an eco-friendlier manufacturing process.
The company claims that its recycling capacity of over 400,000 tonnes per annum can significantly reduce the energy required to extract primary aluminium by 95%, thereby reducing carbon dioxide emissions by 4.8 million tons annually.
www.nemak.com
This article first appeared in DEVELOP3D Magazine
DEVELOP3D is a publication dedicated to product design + development, from concept to manufacture and the technologies behind it all.
To receive the physical publication or digital issue free, as well as exclusive news and offers, subscribe to DEVELOP3D Magazine here